Zekelman and SMS group write record history: with a continuous 28-inch ERW tube welding line with a wall thickness of up to 25.4 millimeters. In addition to SMS group's know-how, proven plant technology and the necessary new developments, the scope of supply also includes the PERFECT arc® cross welding process developed by SMS group – for a continuous production process.
Zekelman meets the market
As part of the project, the family-owned company Zekelman Industries is investing over 150 million US dollars in its site in Blytheville, USA. With a capacity of more than 400,000 tons per year, the new 28-inch plant within Zekelman Industries will complement its Atlas Tube division.
In our company, we will continue with our long-standing goal of creating and not waiting for the future.
In future, structural and piling tubes can be manufactured with diameters ranging from 10 3/4 inches to 28 inches (273 to 710 millimeters) and wall thicknesses of up to 1 inch (25.4 millimeters). In addition to that, it is possible to produce square and rectangular hollow sections with dimensions of 8 inches x 8 inches up to 22 inches x 22 inches or 34 inches x 10 inches. The highly automated ERW tube welding line has been ordered in April 2019 and is scheduled to go on stream already in mid-2021. It will create a total of 75 new jobs at Zekelman Industries.

For the North American market it means not only a more diverse product range for HSS products (Hollow Structural Sections): the new line enables Zekelman Industries for the first time to domestically manufacture products larger than 20 inches on an ERW tube welding line.
How Zekelman customers benefit from the new system
Design and configuration of the new welding line meet the strictest requirements regarding product quality and throughput. The intelligent X-Pact® Quicksetting system from SMS group provides for an automatic adjustment of the rolls to their new working position after a size change. Thanks to a data-based approach for system adjustments, changeover and setting times in the line are minimized, productivity is increased and a continuous improvement of product quality is guaranteed.
Besides a production speed of up to 35 m/min the line offers a very wide size/wall thickness ratio providing excellent flexibility together with very short changeover times when different products are manufactured.
For the first time ever, automated horizontal roll changing is also being carried out for a plant larger than 16 inches by means of change carriages. This not only results in a shortened change-over time, but also increases the operating time and thus the production capacity. In addition, a short change-over time ensures greater production flexibility – a significant success factor in the production of structural tubes.
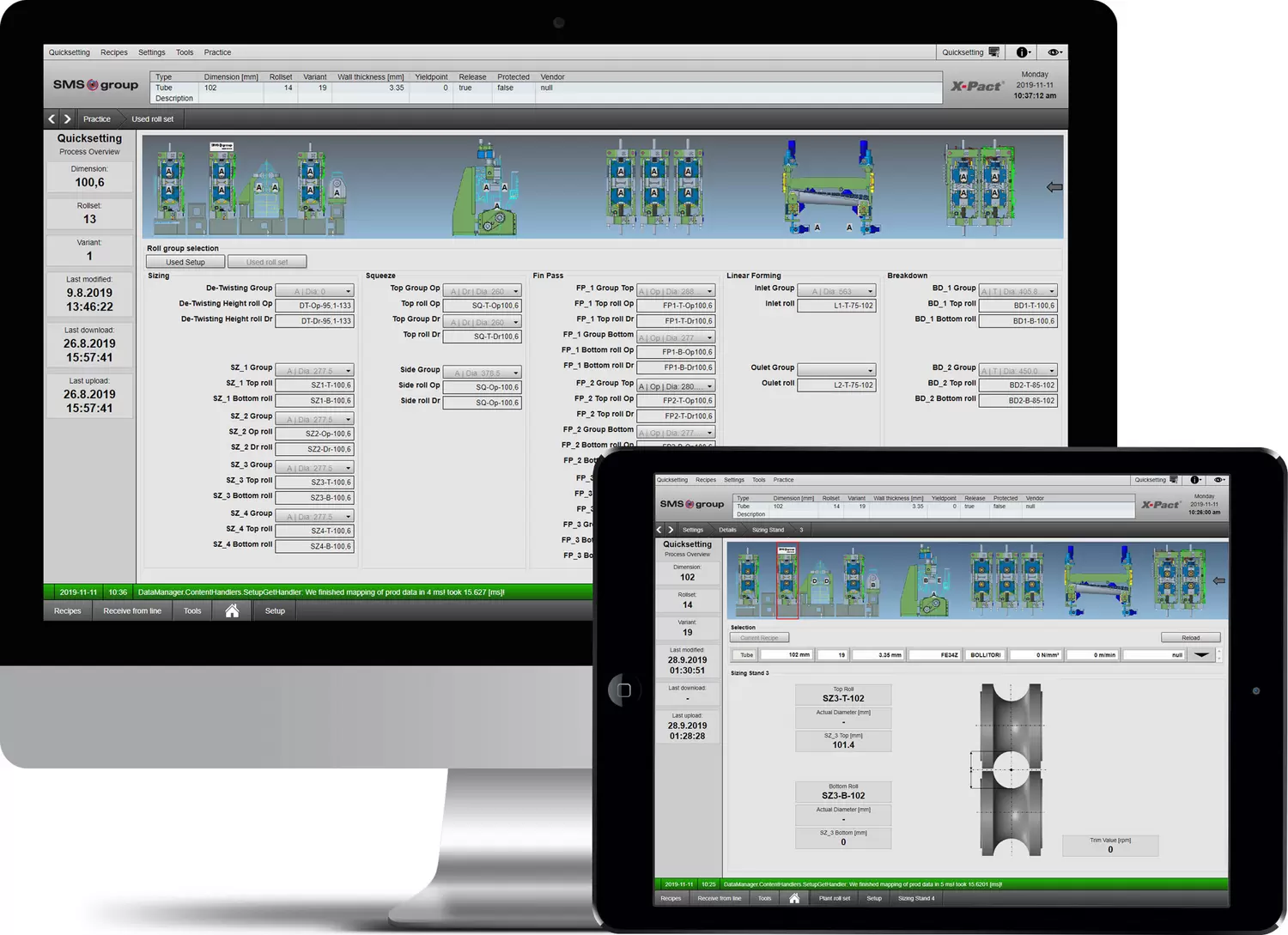
The plant is designed to enable roll changes in less than 2.5 hours. Our long-term goal is to optimize this time towards 90 minutes.
“Over the past few years, we have seen the increasing need for larger, domestically produced HSS in the bridge, transportation and building markets,” said Tom Muth, president of Atlas Tube. “Also, HSS with thicker walls that meet the more stringent width-to-thickness ratio requirements of the AISC Seismic Provisions are in greater demand for lateral bracing systems.”
Reliable cross welding up to 25.4 millimeters wall thickness
This 28-inch ERW tube welding line uses the PERFECT arc® welding technology for the cross joining of strip up 25.4 millimeters thick. The PERFECT arc® welding system which was developed and patented by SMS group, is an GMA (Gas Metal Arc) tandem welding process: a set of tandem torches applying single-wire gas metal arc welding. Able to cross-weld the 25.4 millimeter thick coil ends in only one welding pass with reliable fusion, it significantly saves cycle time in the cross welding station and thus, increases the productivity of the entire plant. Welding is performed at up to 800A per wire.
The PERFECT arc® inverter welding power sources feature digital technology, which can deliver efficiency exceeding 90 percent. Depending on the operating point, energy savings of up to 30 percent can be achieved compared to welding power sources still using conventional thyristor technology.
In the development of its unique cross welding technology, SMS group cooperates with the Technical University of Berlin and the Fraunhofer Institute in Berlin. Together, the cross welding process was tested on a selected range of products and the welding parameters were fully optimized. The process data obtained from these developments are included in the process software and can be retrieved at any time via pre-programmed synergy curves. This significantly increases the reliability, reproducibility and quality of the PERFECT arc® cross welding technology to users such as Zekelman.
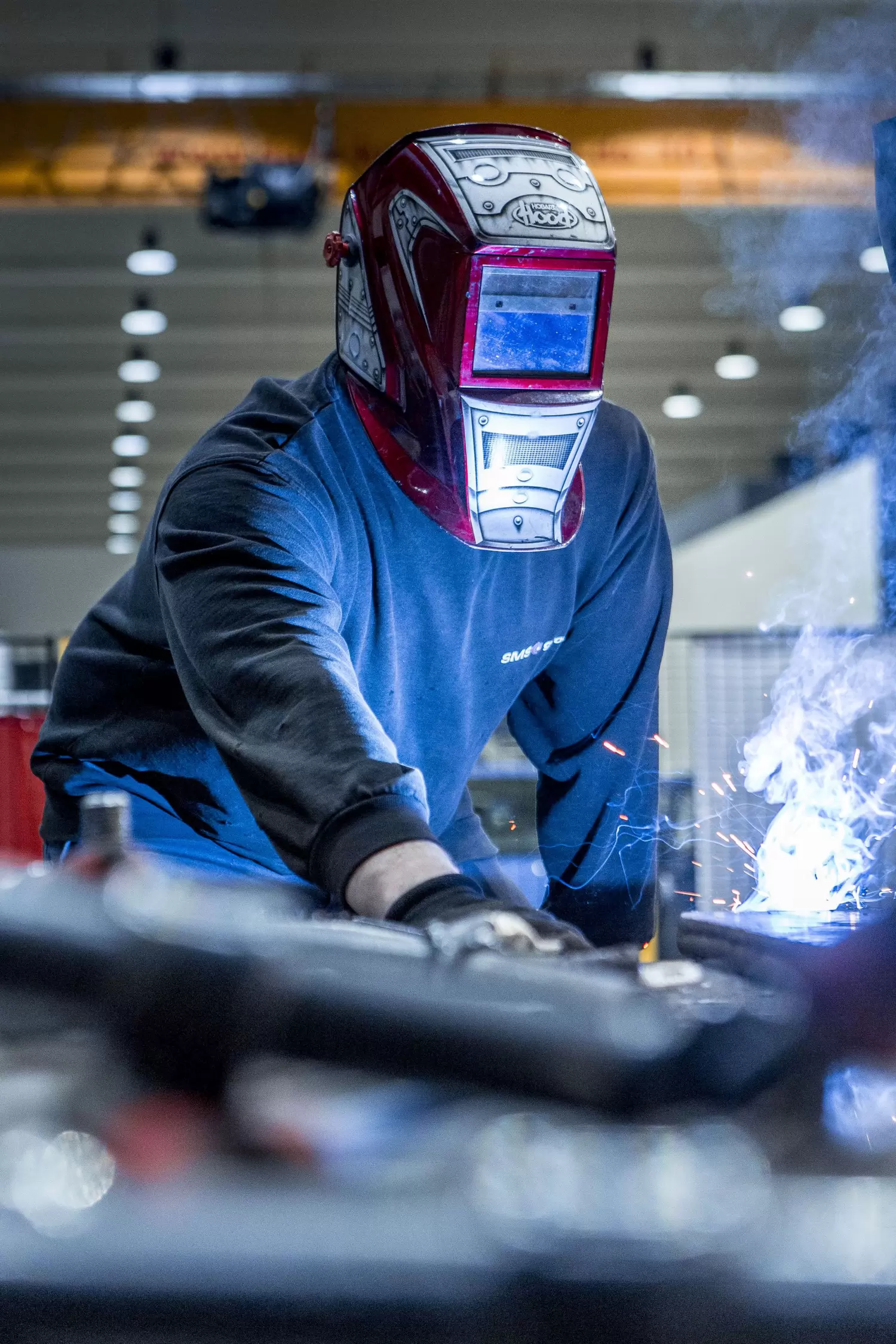
Cooperation with tradition
For several years already, Zekelman Industries and its Structural Atlas Tube Division have been relying on the tube welding technology of SMS group. The success story and rise of Atlas Tube – today the tube division of Zekelman Industries, under the leadership of Barry Zekelman – began with the first two ERW tube welding machines from the SMS group, which were delivered to the site in Harrow, Canada, in 1994 and 2000.
For the 16-inch tube welding line transferred to Blytheville, Arkansas, in 2006, which had already been largely upgraded and expanded by SMS by the relocation, SMS group received several follow-up orders in 2017. To extend the product range and to improve product quality, the welding line has most recently been equipped with a complete new sizing section. By using URD® (Uniform Rigidity Design) stands in the sizing section the changeover times could be greatly reduced for size changes.
Owing to these modernization measures, Zekelman Industries further expanded its North American position in manufacturing structural tubes. In the meantime, this has led to a long-term partnership between Zekelman Industries and SMS group. The most recent order for the world‘s largest continuous ERW tube welding line is the next step in the successful cooperation between the two companies.
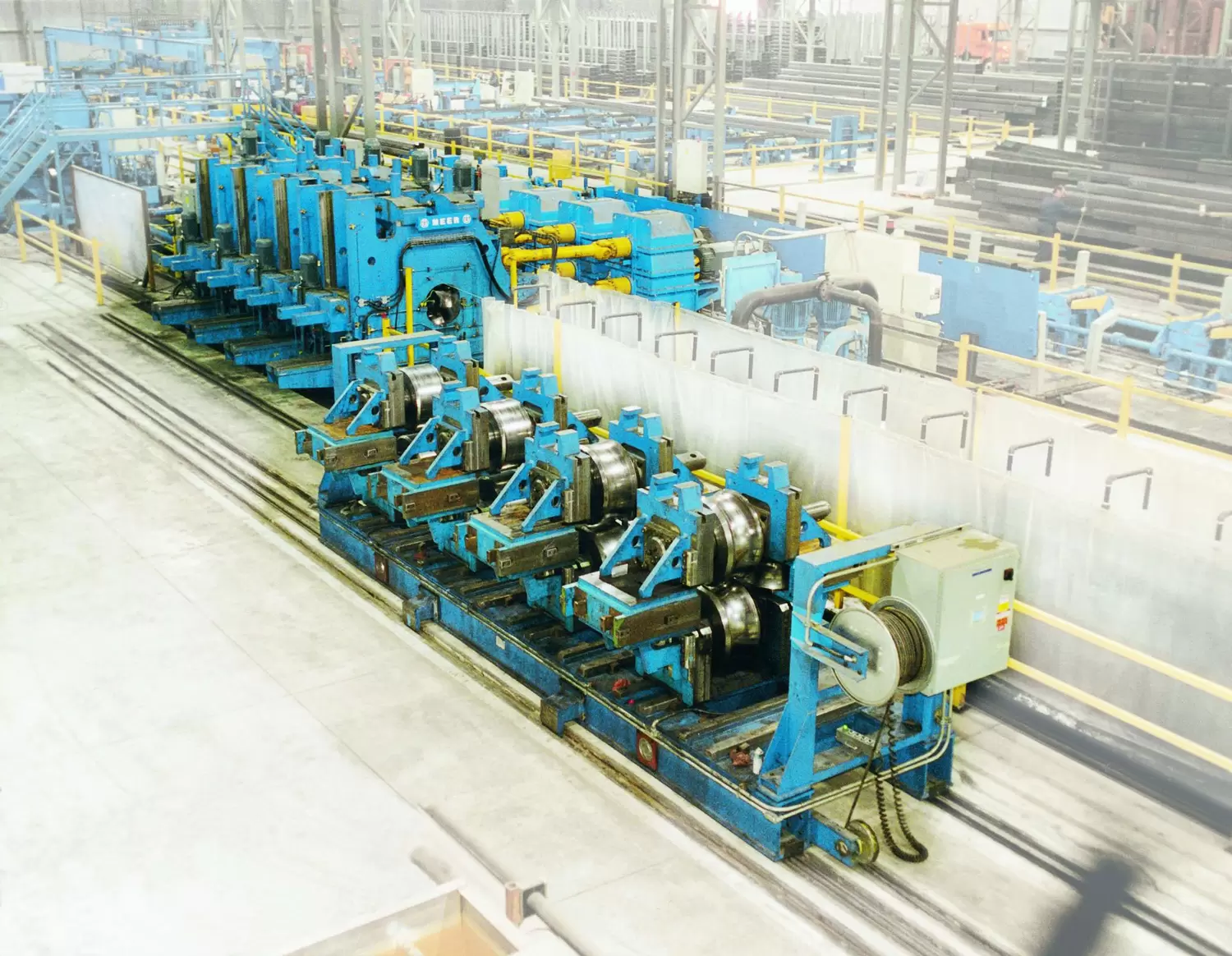