Thanks for joining us again, David. We're excited to hear about your latest project with SMS group – Hybar has some breathtaking goals that will be industry-firsts in many ways. But before we get to that, let's look at what you accomplished at Big River Steel because it is very impressive.
David Stickler: Thank you, and thank you to the entire SMS team here at Metec. It is an impressive group. Last time I was here, we indeed made some bold announcements about Big River Steel. It was to be a LEED-certified (Leadership in Environmental and Energy Design) facility, and I said that it would have the lowest carbon footprint in America, if not the world. Thankfully, it all worked out that way. The numbers tell the whole story: The world average emissions is 1.85 t of carbon per ton of steel produced. At Big River Steel we made it happen with only 0.123 t of carbon. That's 15 times lower – and frankly, it is because of the technology supplied by SMS group and the hard work by the Big River Steel employees.
That's incredible. I understand that word about your accomplishments quickly spread around the world, too, right?
David Stickler: Absolutely. After two years of operation, I got a call from Germany. It was the CEO of Mercedes-Benz saying that he wanted to come over to our small town in Arkansas to present us with their sustainability award. Mind you, not just in the steel category, but the overall Mercedes-Benz Sustainability of the Year Award, which includes all suppliers for everything the Mercedes-Benz buys worldwide.
That's quite an environmental track record. But what about the economic side of the equation?
David Stickler: We have a great story to tell there as well. You know, in the US, it is shocking to me how cumbersome and bloated the legacy steel producers are. It is not uncommon for a legacy mill to struggle to produce only 900 tons of steel per year per worker. At Big River Steel we were producing 5,000 tons of steel per year per worker! That enables us to pay our workers more. When I was running Big River Steel, we likely had the highest-paid steel workers in the world on average, yet our labor costs per ton of steel produced were probably the lowest.
I understand that caught the attention of one of your competitors, a company founded over 125 years ago and famous for producing the steel for the Ford Model T.
David Stickler: That's right. None other than steel giant U.S. Steel approached us for a partnership because they saw an opportunity to take a leap forward with the SMS technology that had us producing record results in terms of quality, sustainability, efficiency, and productivity - which is what today's customers like Tesla are looking for. After being our partner for fourteen months, U. S. Steel was so impressed by what we were accomplishing that they went beyond the initial partnership and purchased all of Big River Steel.
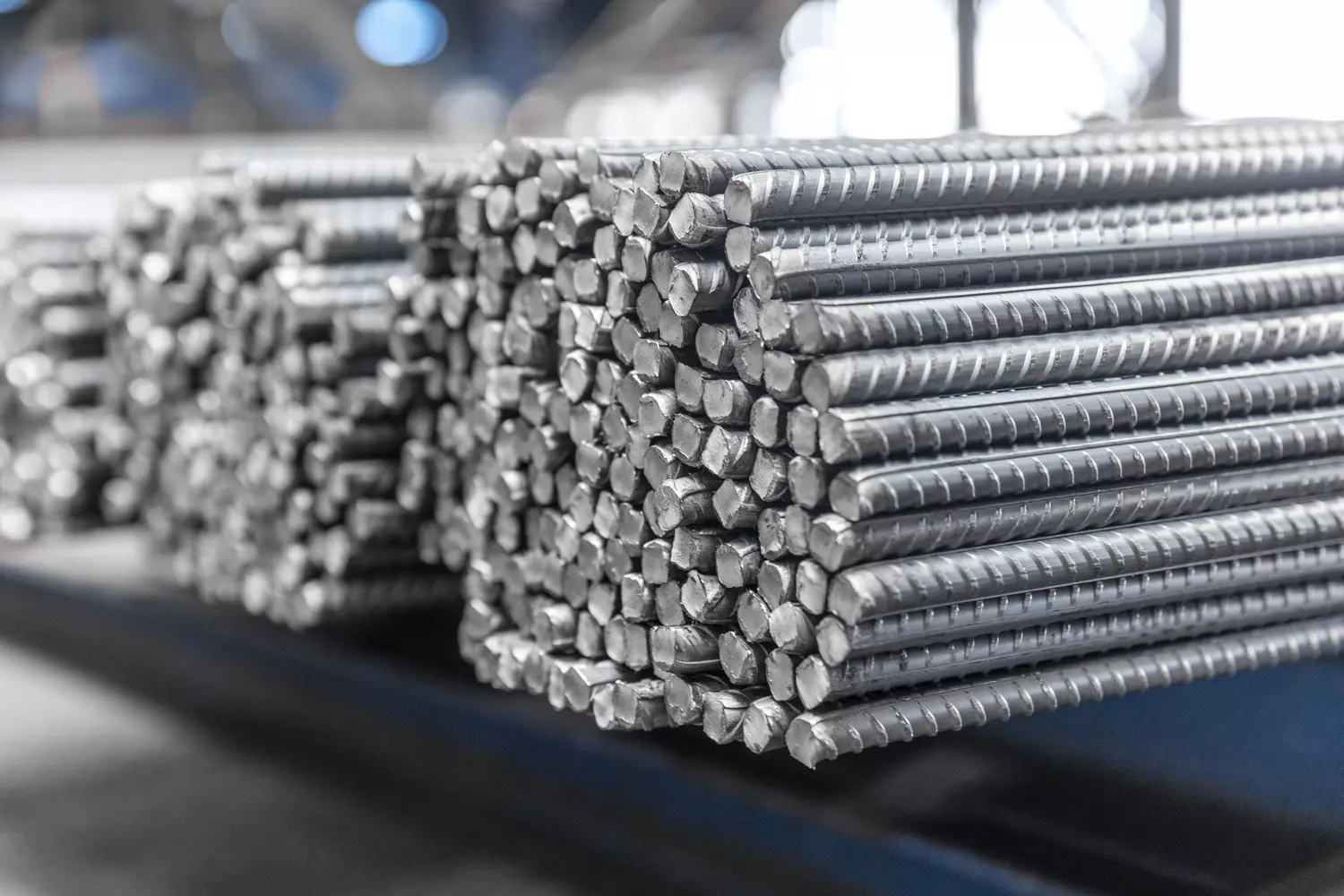
That's certainly a momentous development. Thanks for the update on the partnership success, David. But from what I understand, you two have a whole new and exciting chapter planned for your collaboration.
David Stickler: Indeed we do. There's a new company which I am CEO of, called Hybar, where we focus on a different product category. We are going to produce long products at Hybar, using high-yield, low-emission, and energy-efficient CMT® technology from SMS group. And just as with Big River, we see the opportunity to set worldwide standards once again: in terms of carbon emissions and labor efficiency. We bought the technology from SMS to make that happen. And before you ask about the economic dimension of the mill – we will again break world records there, by producing 630,000 short tons of rebar annually and be able to spool up to size 8 rebar in eight ton spools – which will be world leading.
Now, there's another innovative sustainability twist you're adding to this project that you are very excited about – I heard you have plans to incorporate solar power.
David Stickler: That is true and another testament to our innovation-driven business model. We are putting a solar field right next to the Hybar mill that will be capable of running the entire operation. That's never been done anywhere else in the world. So when the sun shines, we will make steel with 100% renewable energy that is directly fed into the mill, not from an electrical energy grid or network. Even without that, the advanced CMT® technology from SMS group will facilitate a 35% lower carbon footprint compared to a conventional steel minimill. The Hybar mill will be the world's showcase for efficiently producing green rebar.
The rebar minimill of Hybar will be the world's showcase for producing green rebar.
Another element that will be vital for achieving your aggressive production and environmental goals also comes from SMS – tell us about the role digitalization plays at Hybar.
David Stickler: Going back four, or even eight years, our partnership with SMS group has always had a significant digitalization component. The digitalization advancements we jointly made for flat products in the learning steel plant at Big River will serve as our starting point at Hybar. And again, there is a sustainability dimension and significant productivity and safety benefits to the comprehensive suite of digitalization solutions SMS brings to the project. We're going to capture many thousands of data points for analysis, looking for predictive patterns we can use for risk analysis – we'll know about every event or trend that adversely affects mill productivity and safety so that we can take appropriate measures. It's that type of digital automation efficiency that makes it possible for us to produce, as at Big River, 5,000 tons of steel per year per worker. Ultimately, with the technology SMS is developing for us, I can even see taking the pulpit out of the mill and moving it to an administrative facility – but that's a little further out in the future; maybe for the one of the next mills we'll build together.
When we speak again, maybe in another four years, what do you think we will be talking about? What will the steel market look like in the U.S., in your opinion?
David Stickler: That's a hotly debated question with many different answers. But it will undoubtedly still be a very price-competitive market. If you look at the last twenty years of steel consumption, it has remained pretty constant averaging around 107 million tons of steel per year, with maybe a six or seven percent variation between years. So our upcoming plants will have to take market share away from other producers, as we have done for over two decades. I am confident that the trend we have helped foster in the US of newer more modern steel making technology replacing older less environmentally sustainable steel facilities will continue. So, whatever else may happen, I am confident that the US will have cleaner steel to work with. And I expect a lot of that steel to be produced using SMS technology.