Through the past years, we had very good cooperation with SMS, and we were very satisfied about the mill’s excellent performance and the level of technical support from SMS group. Also, SMS group was the only supplier capable to offer us an integrated project covering electrical and mechanical extents.
Resume of production after a short ramp-up phase
Within a shutdown of merely twenty days, SMS group managed to complete the modernization of the CSP® plant at the Alexandria production site of Al Ezz Dekheila Steel Company (EZDK). The customer could resume production after a short ramp-up phase. SMS group talked with Mohamed Fouad Emam, General Manager for Technical Affairs at EZDK about the project.
Mr. Emam, what kind of products is EZDK producing and what is the annual capacity?
Before the upgrade, we produced one million tons of flat steel per year. We used to produce several steel grades from low- to medium-carbon and HSLA grades and limited quantities of API and dual-phase steel. But our point of excellence is the production of thin gauges which requires highly skilled operators and perfect mill condition.
After the modernization we are looking for more added-value products such as API-X70 thicker material 12.7 millimeters in thickness, silicon steel, dual and multi-phase steel. Moreover, we are planning to produce gauges with 1.0 millimeter thickness as part of commercial production. Currently, the minimum gage is 1.2 millimeters.
What was the reason for the modernization project?
The main reason was the obsolescence of automation system hardware, but we found it wise to upgrade the models in order to make use of the development in the past 20 years. In addition, we included some mechanical upgrades like liquid core reduction and super-reinforced cooling to fully utilize the new models’ capabilities.
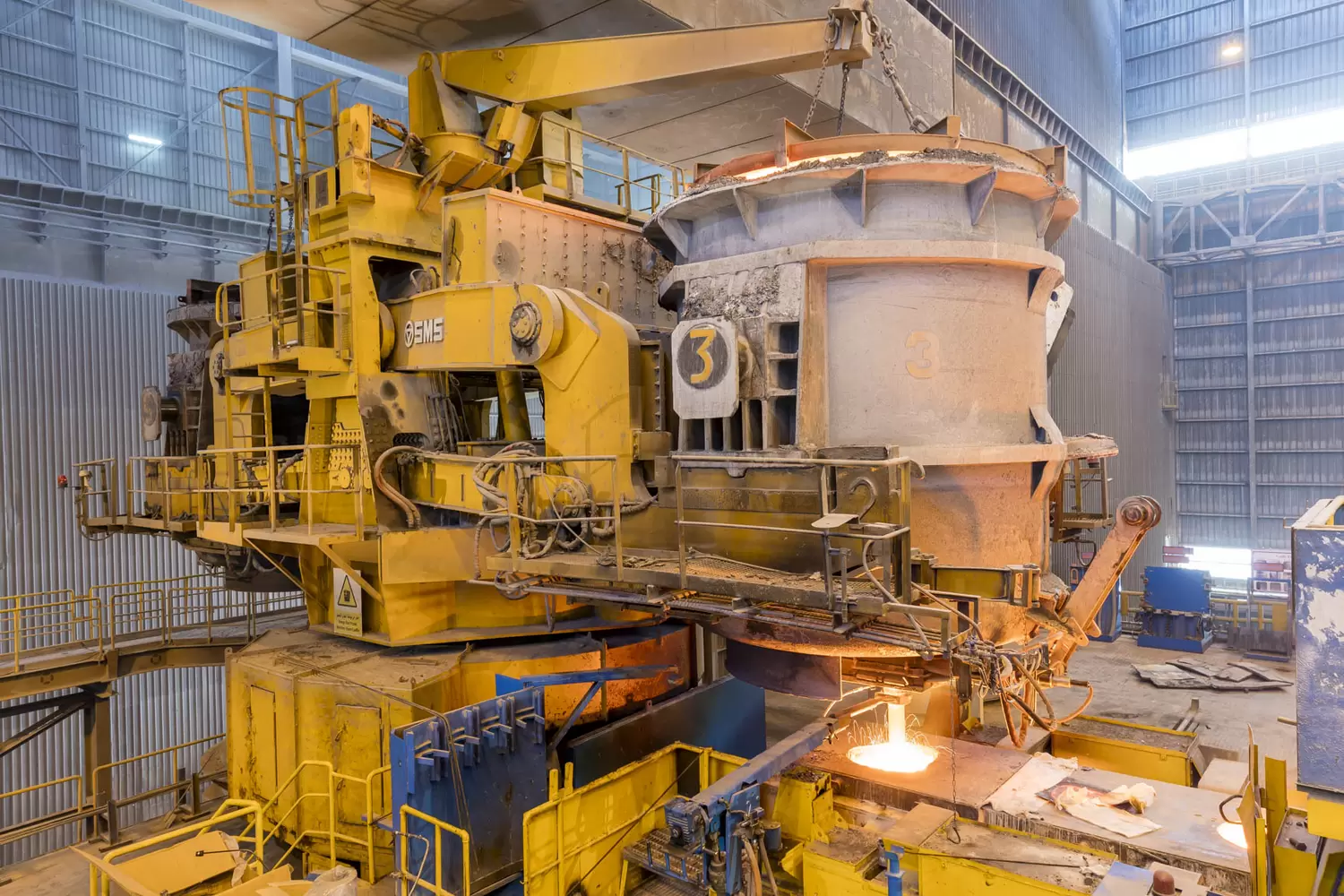
What was the decisive factor that made you place this order with SMS group?
Basically, SMS group was the machine builder and leader of the consortium that originally supplied the plant. Through the past years, we had very good cooperation with SMS, and we were very satisfied about the mill’s excellent performance and the level of technical support from SMS group. Also, SMS group was the only supplier capable to offer us an integrated project covering electrical and mechanical extents.
How important do you feel is the supply of mechanical and electrical equipment plus automation systems from one single source, as provided by SMS group for the project on hand?
In fact, it is one of the key factors for a successful project to have everything in one hand to guarantee the integration of the project. The difficulty of an upgrade project compared to a green-field project made us put more focus on such integration. In addition, SMS group was the only supplier who offered us the complete solution.
What do you think of the cooperation between your staff and the SMS team?
We are on a high level of teamwork which is attributable to the long-term cooperation between the two companies. In addition, our engineers stayed in Germany after training for joint programming, which enhanced their skills and formed the two teams into one.
Have you heard of the Plug & Work concept before the integration test SMS did for EZDK?
We have been pursuing very closely the development of Plug & Work since its early start. I personally visited the test field together with a group of my team even before starting our project and was very impressed by the test field and the simulation. This concept saves a lot of time and effort during commissioning.
Would you recommend SMS group as modernization partner to other customers?
No doubt, we trust in SMS and definitely recommend this company to any customer looking for a successful project.
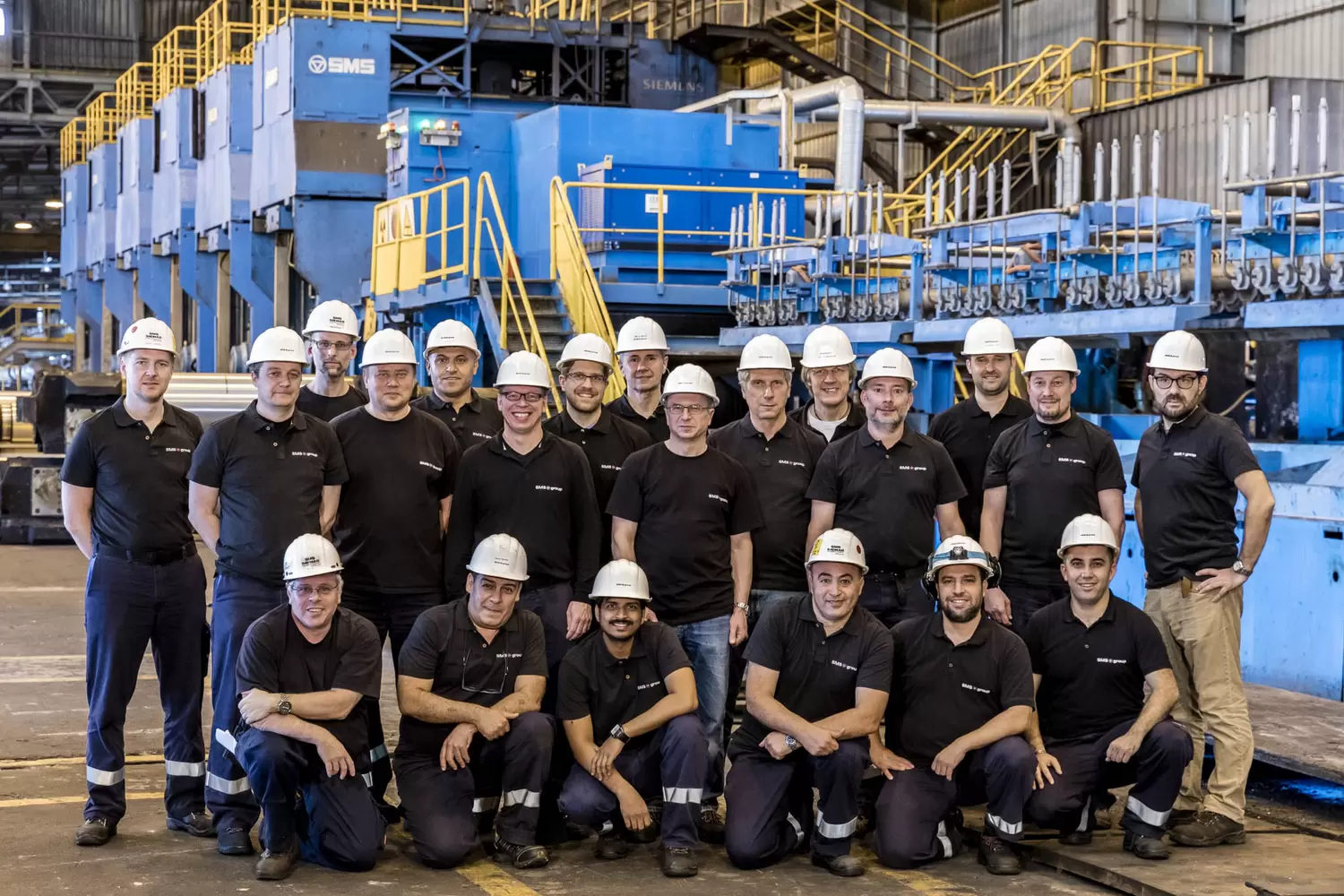