Ringwalzmaschinen stehen bis zur Hälfte der Zeit still, etwa weil be- oder entladen oder auf die Erwärmung von Werkstücken gewartet wird. Um den Energieverlust durch diese vergleichsweise hohen Nebenzeiten zu senken, sind Spezialisten bei SMS group auf die Idee gekommen, elektrohydraulische Direktantriebe zu nutzen. „Unsere Kollegen in den Fachabteilungen haben ein sehr breites Wissen zum Thema Elektrik und Hydraulik“, erzählt Markus Gellhaus, der bei SMS group den Vertrieb von Ring- und Räderwalzanlagen leitet. „Also lag für sie die Frage auf der Hand: Warum sollte man die Antriebe, die an anderer Stelle funktionieren, nicht auch bei Ringwalzmaschinen einsetzen können?“
Exakt gesteuerte Bewegungen
Beim elektrohydraulischen Direktantrieb treibt ein Motor eine Pumpe an, und in einem Hydraulikzylinder wird das in eine Bewegung umgesetzt. Wird die Drehzahl der Pumpe gedrosselt, gehen gleichzeitig Energieverbrauch und Geräuschemissionen deutlich zurück. Bei Ringwalzmaschinen werden diese Antriebe direkt auf den Walzachsen montiert. Sie können so sehr exakt gesteuert werden – ohne dass die Bewegung jedoch an Kraft einbüßt. Stehen die Achsen still, wird die Pumpe heruntergeregelt und der Motor verbraucht in dieser Zeit keine Energie.
Die benötigte Antriebs-Energie verringert sich dadurch um 25 bis 40 Prozent. Der Lärmpegel sinkt um rund 15 Prozent. Weiterer Pluspunkt des Konzeptes mit Namen RAW EH sind geringere Investitions- und Betriebskosten gegenüber konventionellen Ringwalzmaschinen. Denn mit dem Wegfall der Zentralhydraulik muss nicht – wie bislang üblich – ein extra Raum dafür gebaut werden. Auch die sehr aufwendige Verrohrung wird nicht mehr gebraucht. Die Menge an Hydrauliköl kann um 90 Prozent reduziert werden. Daneben besteht keine Gefahr mehr von Umweltbelastungen durch austretendes Öl. In das Konzept sei Know-how aus über 500 gebauten Ringwalzmaschinen eingeflossen, heißt es. Die Erfahrungen mit den elektro-hydraulischen Kompaktantrieben zeigen, dass sich Position und Kraft der Achsen hervorragend regeln lassen. Durch die geringe Anzahl der Komponenten ist das System sehr robust und wenig störanfällig.
Für Neueinsteiger in das Ringwalzen und sogenannte Job Shops wurde die Baureihe RAW ecompact® entwickelt. Sie ist in fünf Größen verfügbar – von 63 bis 125 Tonnen Walzkraft. Die RAW ecompact® trägt das Ecoplants-Label der SMS group, mit dem das Unternehmen effiziente Lösungen kennzeichnet.
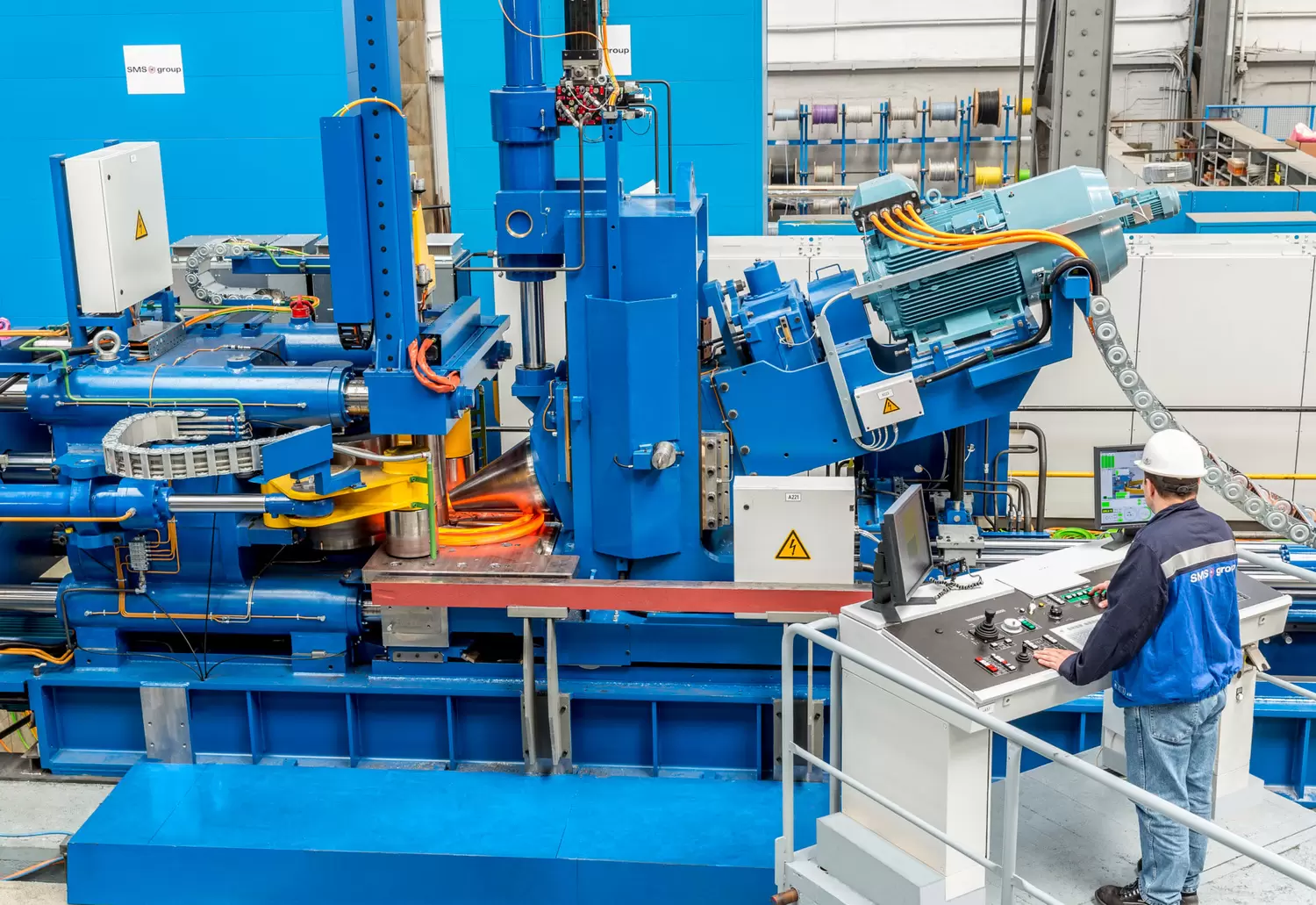
Konzept lässt sich übertragen
Sowohl für die Ingenieure bei SMS group als auch für Kunden bedeuten die Neuerungen keine große Umstellung. „Für das Bedienpersonal ändert sich nichts – Look and Feel der Maschine bleiben gleich. Das Wartungspersonal muss von uns geschult werden, aber das ist bei konventionellen Antrieben auch der Fall“, erklärt Martin Gellhaus. „Im Bereich Mechanik werden andere Zylinderbauformen verwendet, die in der Maschine anders angebracht werden“, sagt er mit Blick auf die Arbeit der eigenen Mannschaft. „Aber das sind typische Anpassungskonstruktionen – das täglich Brot eines Ingenieurs.“
Gellhaus kann es sich gut vorstellen, weitere Produkte mit elektrohydraulischen Antrieben auszustatten – zum Beispiel Räderrohlingpressen. „Bei Räderrohling- und bei Kümpel-Loch-Pressen könnten wir das gleiche Prinzip verwenden, wie wir es bei den Ringrohlingpressen eingeführt haben“, erklärt er. 2014 hatte SMS group ein Konzept entwickelt, um drehzahlgeregelte Axialkolbenpumpen in einer 2.000-Tonnen-Ringrohlingpresse einzusetzen. Je vier Motoren bilden dabei den Antriebsstrang eines Zylinders. Clou an dem Prinzip ist auch hier, dass die Energiezufuhr für den eigentlichen Pressvorgang getrennt wird – hier von der für das Heben und Senken. Die Flächen der Zylinder werden dazu über Ventile eingestellt: Beim Pressen sind die Zylinderflächen groß, daraus resultieren hohe Kräfte bei kleinen Pressgeschwindigkeiten. Beim Eilgang – also dem Heben oder Senken – wirken über kleine Flächen kleine Kräfte und große Geschwindigkeiten. Die Bewegung der Presse wird über einen Drehrichtungswechsel der Servoantriebe umgekehrt.
Auch hier wird Energie also effizient eingesetzt. Neben der Umsetzung des „Power on Demand-Prinzips“ wird außerdem die potentielle Energie der bewegten Masse beim Senken in elektrische Bremsenergie gewandelt, ebenso die Dekompressionsenergie und die elastische Auffederungsenergie des Pressenrahmens im Zustand der Entlastung. Diese Energie wird im Zwischenkreis der Umrichter gespeichert und zurück ins Netz gespeist.
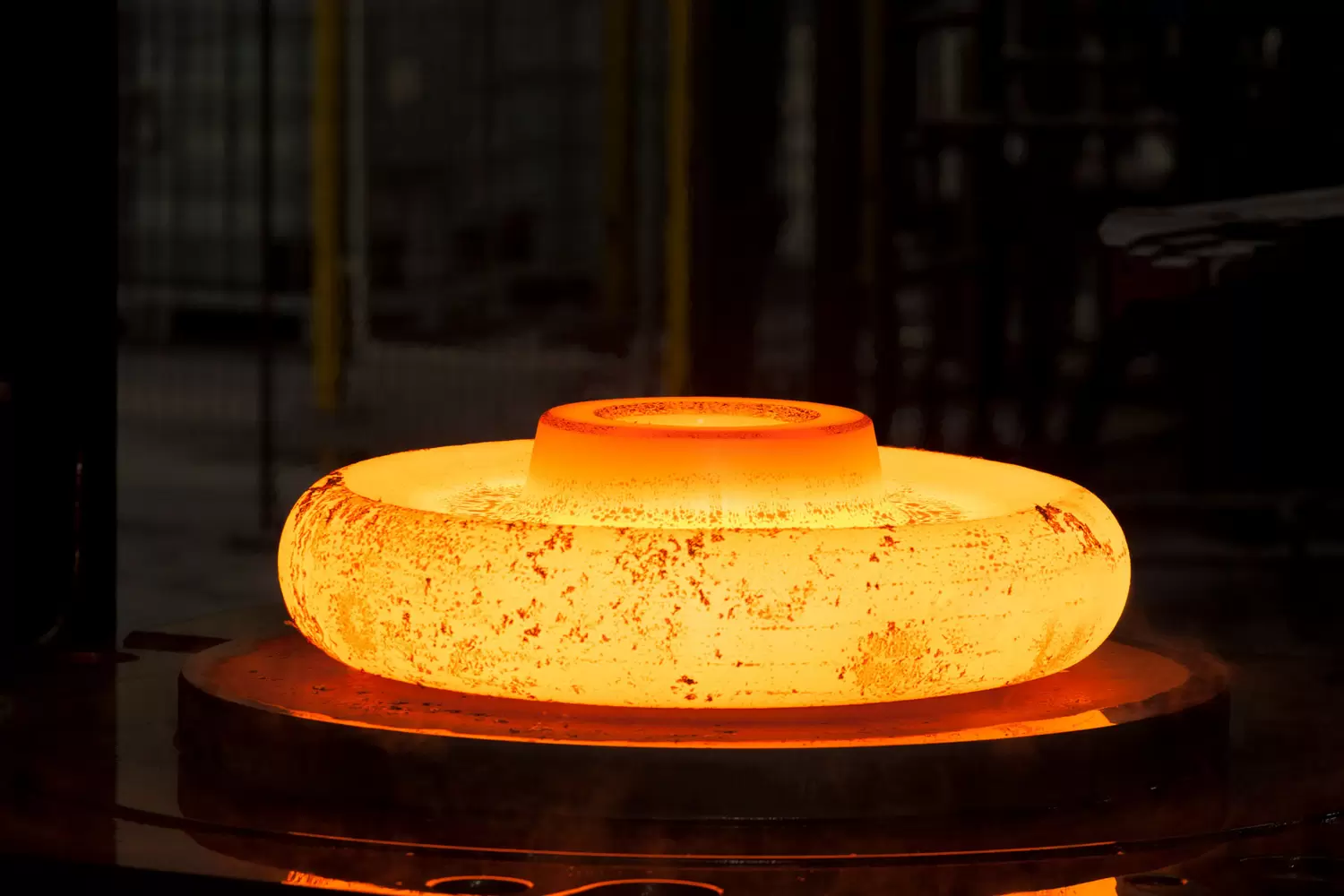