Die Stahlindustrie steht vor großen Herausforderungen. Was sie produziert, ist für alle modernen Gesellschaften auch in Zukunft unverzichtbar. Aber es bedarf einer Anpassung der heutigen Produktionsprozesse, um die Emission von Treibhausgasen drastisch zu reduzieren und so einen Beitrag zur Begrenzung des Klimawandels zu leisten.
Um unsere Kunden auf ihrem Weg zur Dekarbonisierung noch effizienter zu unterstützen, haben SMS group und Paul Wurth ihr in insgesamt 300 Jahren erworbenes Know-how gebündelt, um zukünftig die technologischen Standards in der grünen Stahlproduktion zu setzen. Gemeinsam legen wir den Fokus auf Herausforderungen im Bereich Metallurgie sowie zukunftsweisende Wasserstofftechnologien. Darüber hinaus verfügen wir über umfangreiche Kompetenz bei Direktreduktionsanlagen, Umweltschutzlösungen und Recyclingtechnologien.
Dekarbonisierung für Brownfield- und Greenfield-Projekte
Grundsätzlich gibt es drei wesentliche Prozessrouten zur industriellen Erzeugung von qualitativ hochwertigem, kohlenstoffarmen Stahls. In diesen Verfahren werden erhebliche Mengen an Rohmaterialien eingesetzt und gleichzeitig, je nach Anforderungen an das Endprodukt, auch Schrott, um CO2-Emissionen zu reduzieren. SMS group ist in der einzigartigen Lage, für jede dieser drei Prozessrouten voll integrierte Lösungen und führende Technologien zu liefern - vom Eisenerz bis zum Endprodukt. Da es in diesem Bereich keine „One-fits-all“-Lösung gibt, ist dies ein wesentlicher Faktor.
Wirtschaftlichkeit und Realisierbarkeit der einzelnen Prozessrouten hängen stark von den jeweiligen Bedingungen vor Ort ab. Viele Ansätze zur Dekarbonisierung setzen auf die Verfügbarkeit großer Mengen - vorzugsweise grüner - elektrischer Energie und benötigen von Zeit zu Zeit eine ausreichende Kurzschlussleistung. Auch andere Faktoren, wie die Verfügbarkeit von Rohstoffen sowie lokale Gesetze, Richtlinien und Vorschriften spielen bei der Technologieauswahl eine große Rolle.
- Bei „Greenfield“-Anlagen liegt der Schlüssel zur Reduzierung der Emission von Treibhausgasen auf unter 100 kg CO2 pro Tonne Warmband in der Kombination von grünem Wasserstoff, Direktreduktion und der Elektrifizierung aller nachgeschalteten Prozesse.
- In existierenden integrierten Hüttenwerken - sogenannte \"Brownfield\"-Standorte – erreichen wir eine Senkung der Treibhausgasemissionen durch den schrittweisen Umbau der Produktionsanlagen und der Infrastruktur. Dieses Vorgehen erfordert eine kontinuierliche Neubewertung der Energiebilanzen und eine Neuorganisation der Energieflüsse. Als Full-Liner bieten SMS group und Paul Wurth integrierte Lösungen für diesen Wandel. Mit diesem Ansatz können wir für all unsere Kunden die passende Roadmap für ihren Weg zur Kohlenstoffneutralität entwickeln.
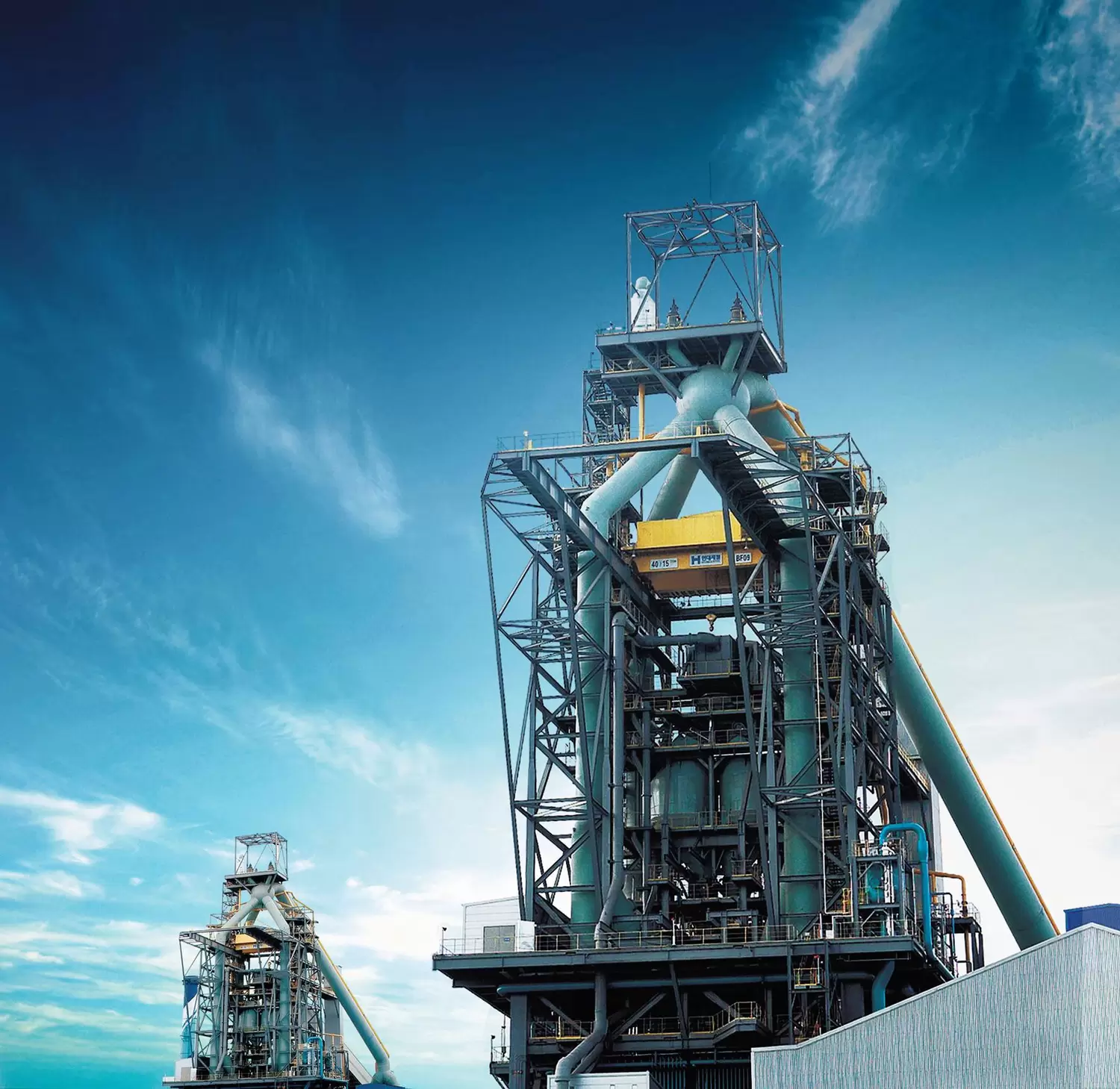
Die Roadmap für eine klimaneutrale Stahlindustrie
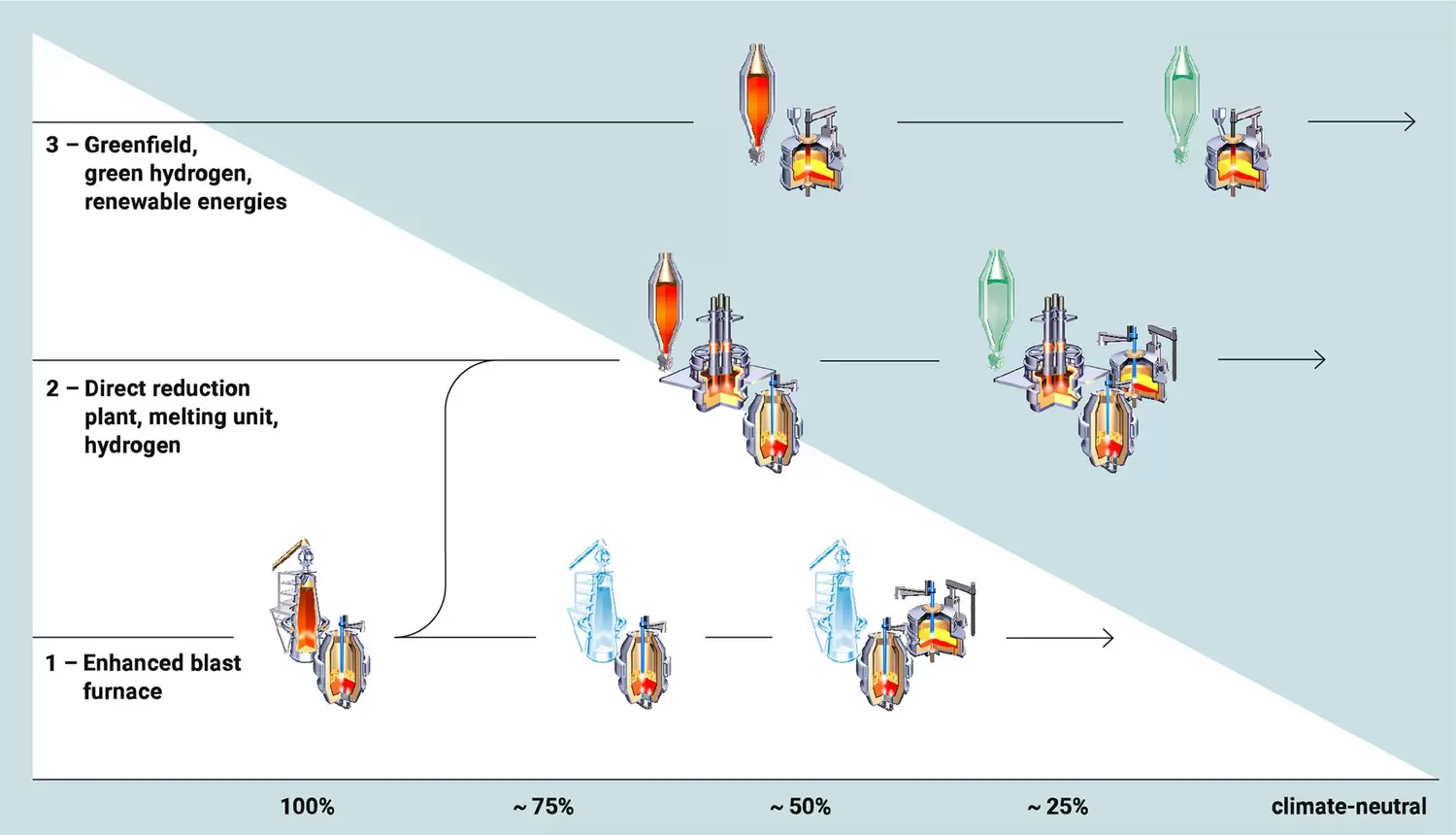
Brownfield-Projekte: „Blue Blast Furnace“ und BOF-Konverter
Bei der integrierten Hochofen-Sauerstoffblaskonverter-Route (Blast Furnace-Basic Oxygen Furnace, BF-BOF) werden große Mengen Eisenerz eingesetzt - oft mit einem geringen Eisengehalt von lediglich 65 %. Bei dieser sogenannten „Primärroute“ können während des Konverterverfahrens begrenzte Mengen an Schrott zugegeben werden (ca. 20 Prozent). Aufgrund des Einsatzes von Koks zur Eisenerzreduktion weist die BF-BOF-Route von allen Prozessrouten zur Stahlerzeugung die höchsten CO2-Emissionen auf.
Aus diesem Grund hat Paul Wurth mit großer Sorgfalt eine Technologie entwickelt, die eine wesentliche Verbesserung sowohl der Hochofen- als auch der Koksherstellungsverfahren darstellt und den Koksanteil auf bis zu 200 kg pro Tonne Roheisen reduziert, wodurch auch die CO2-Emissionen sinken.
Zur Erhöhung des Schrotteinsatzes bieten sich im Stahlwerk Elektrolichtbogenöfen oder z. B. die SMS CONPRO-Technologie an. Dieser Ansatz wird lediglich in solchen Fällen eingeschränkt, in denen spezifische Anforderungen an die Produktqualität die Verwendung von Schrott geringerer Güte, der möglicherweise mit Cu, Sn, Ni, Mo verunreinigt ist, ausschließen.
Brownfield-Projekte: Direktreduktion mit Open Bath Furnace und BOF-Konverter
Bei dieser Verfahrensroute wird der Hochofen durch eine Kombination aus MIDREX®-Direktreduktionsverfahren und einem Open Bath Furnace (OBF) ersetzt. Zunächst kann die Direktreduktion auf Erdgasbasis durchgeführt werden, wobei das Erdgas nach und nach durch immer größere Anteile Wasserstoff ersetzt wird.
Der von der SMS group-Tochter Metix entwickelte OBF ist ähnlich aufgebaut wie ein konventioneller Reduktionsofen (Submerged Arc Furnace, SAF), der im sogenannten „Brushed Arc“-Modus betrieben wird. Für diesen Ofentyp können wir mehrere hundert Referenzanlagen vorweisen. Haupt-Einsatzmaterial bei dieser Prozessroute sind weiterhin Eisenpellets in Hochofenqualität; in der Stahlerzeugung kann dann wiederum Schrott zugegeben werden. Ein nennenswerter Vorteil ist die Möglichkeit, eisenhaltige Abfallprodukte (bis zu 3-5 % der Gesamtcharge) zu verwerten, wie z. B. Hochofen- und BOF-Staub und Walzzunder.
Bei der Integration dieser Route in ein bestehendes, integriertes Hüttenwerk sind die große Erfahrung von SMS und Paul Wurth ein riesiger Vorteil, insbesondere für die Entwicklung der Schnittstellen und die Maximierung der Emissionsreduzierung unter Beibehaltung oder sogar Steigerung der Wettbewerbsfähigkeit.
Greenfield-Projekte: Direktreduktion – Elektrolichtbogenofen
In einem Greenfield-Projekt und bei Verfügbarkeit von grünem Wasserstoff zu wettbewerbsfähigen Preisen und in ausreichenden Menge kann ein völlig anderer Ansatz gewählt werden. Dann wird ein Elektrolichtbogenofen mit vorreduzierten Eisenerzpellets in DR-Güte aus dem MIDREX®-Prozess im Heißeinsatz beschickt. Es ist kein Zwischenschritt erforderlich, und – je nach spezifizierter Endgüte – wird nur eine geringe Aufkohlung benötigt, um den Stickstoff im Stahl zu reduzieren. Von Anfang an kann ein größerer Schrottanteil in den Ofen eingebracht werden, der nach oben hin lediglich durch die Qualitätsanforderungen nachgeschalteter Verarbeitungsstufen begrenzt ist.
Aufgrund der direkten Verbindung aller Anlagen hat diese Prozessroute das Potential, dem Ziel der Kohlenstoffneutralität am nächsten zu kommen. Dies ist besonders dann der Fall, wenn das Konzept um eine hocheffiziente, kombinierte Dünnbrammengieß- und Direktwalzanlage in Form einer CSP®- oder CSP®-Nexus-Anlage ergänzt wird.
Maßgeschneiderte Wege zur Dekarbonisierung
Die drei beschriebenen Prozessrouten stellen aktuell die wesentlichen Optionen für die Dekarbonisierung der Primärphase in der Stahlerzeugung dar. Sie können maßgeschneidert kombiniert oder modifiziert werden, um spezifische Anforderungen zu erfüllen.
Jede dieser Optionen unterliegt jedoch bestimmten Einschränkungen und hat ihre individuellen Stärken und Schwächen. Daher ist es unverzichtbar, die für den jeweiligen Fall vorliegenden Bedingungen sorgfältig zu analysieren, um das beste Verhältnis zwischen Kohlenstoffeffizienz und Wettbewerbsfähigkeit zu wählen. Dank der langjährigen Erfahrung und zahlreichen Referenzanlagen der SMS group bei allen hier vorgestellten Technologien und Verfahren sind wir in der einzigartigen Position, für jeden Anwendungsfall den besten Ansatz auf dem Weg zur Dekarbonisierung zu finden.