Welche Bedeutung hat der Digital Twin für die Fertigungsindustrie?
Der Begriff „Digital Twin“ bezieht sich auf die Definition von Grieves und Vickers aus dem Jahr 2002. Im Jahr 2016 wurde diese Definition auf die folgende Formulierung aktualisiert:
“Der Digital Twin ist eine Zusammenstellung virtueller Informationskonstrukte, die das Potenzial oder das tatsächliche physikalische Produkt von der Mikro-Atomebene bis zur makrogeometrischen Ebene vollständig beschreiben. Im besten Fall können alle bei einer Inspektion eines hergestellten Produkts gewonnenen Informationen auch von seinem Digital Twin geliefert werden.” [Grieves and J. Vickers (2016). Digital Twin: Mitigating Unpredictable, Undesirable Emergent Behavior in Complex Systems.]
Was bedeutet das in der Praxis?
Der Digital Twin ist eine virtuelle Darstellung eines materiellen oder immateriellen Objekts der realen Welt, das nicht unbedingt existiert, etwa in der Konstruktionsphase einer Maschine. Da das Konzept des Digital Twins universell ist, kann es auf fast alles angewendet werden: Auf Maschinen, Werkzeuge, Prozesse, Humankapital, Produktion, Qualitäts-KPI, und vieles mehr. Die Eigenschaften dieser Informationen sind ebenfalls vielfältig und umfassen alle Arten von Datenquellen, etwa Prozessdaten, Stammdaten, Meta-Daten oder ERP-Daten. Algorithmen und Anwendungen im Allgemeinen können dazu beitragen, diese Daten mit Informationen anzureichern.
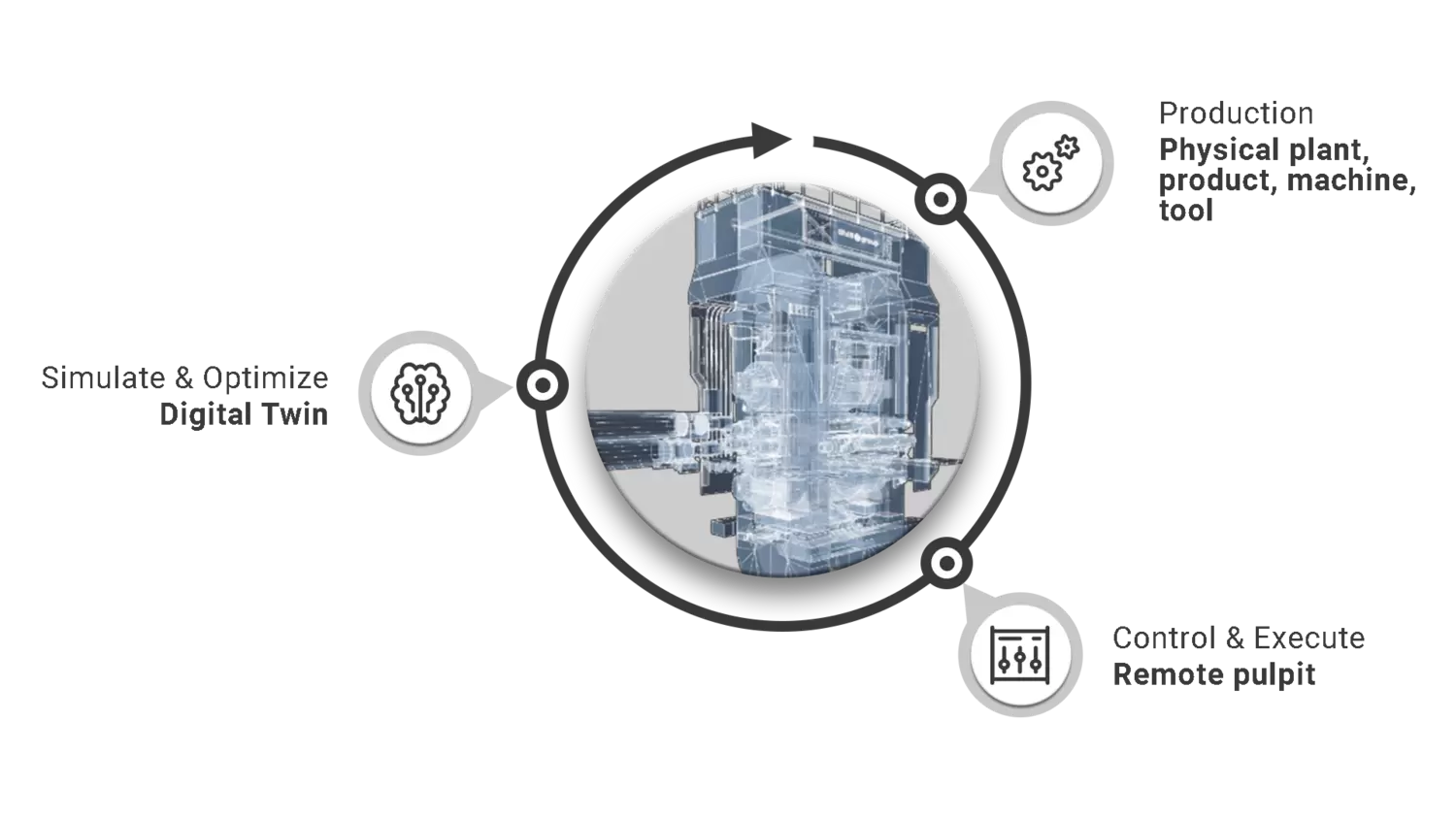
Digital Twins sind Teil der Lieferkette, die sich über den gesamten Lebenszyklus von Produkten und Maschinen bis hin zu Prozessen und Dienstleistungen hinausstreckt und bieten in jeder Phase einen besonderen Nutzen und unterschiedliche Vorteile. Bereits in der Konstruktionsphase eingesetzt, kann der Digital Twin komplexe Produktanforderungen oder schnelle Entwicklungszyklen verarbeiten und verschiedene Konstruktionen mit spezifischen Simulationen testen, sodass physisches Prototyping zunehmend überflüssig wird. Dies führt zu Zeit- und Kosteneinsparungen bei der Entwicklung neuer Produkte und optimiert Aggregate und Prozesse bereits in der Konstruktionsphase. Die Simulation von Funktionalitäten und Verhaltensweisen im Hinblick auf alle relevanten Aspekte verringert den Grad der Unsicherheit. Da alle Funktionen simuliert werden können, ist die Inbetriebnahme einfacher und die Prozesse sind fehlerfrei.
Ein Digital Twin bietet die Möglichkeit, Risiken zu überwachen und zu reduzieren. Das wiederum kann zu einer Erhöhung der Gesamtverfügbarkeit einer Maschine oder einer Prozesslinie führen. Es können nicht nur aussagekräftige Prognosen über Eigenschaften, Qualität und Verhaltensweisen von Produkten und Maschinen gemacht werden, sondern auch die Ersatzteilplanung und Untersuchungen von Upcycling-Potenzialen sind möglich. Da das Konzept des Digital Twins einen ganzheitlichen Blick auf Produkte, Maschinen, Prozesse und die gesamte Lieferkette in Echtzeit erlaubt, wird auch die Kommunikation zwischen Lieferanten, Herstellern und Kunden schneller und komfortabler.
Die Rolle der Digital Twins im lernenden Stahlwerk
In der Vision des Lernenden Stahlwerks spielt das Konzept des Digital Twins eine entscheidende Rolle. Der Digital Twin deckt alle Informationen über Maschinen, Produkte und Prozesse vollständig ab und ist ein effizientes Werkzeug, um mit Hilfe künstlicher Intelligenz, maschinellem Lernen und sogar menschlichen Studien über vergangene und zukünftige Szenarien ein tieferes Verständnis und Wissen zu schaffen.
Die wesentlichen Vorteile, die die SMS group und SMS digital mit dem Digital Twin bieten, sind:
- Monitoring: Alle relevanten Anlagen-, Maschinen- oder produktbezogenen Informationen werden einfach und verständlich visualisiert. Es ist sogar möglich, Prozessdaten in Echtzeit als 3D-Replizierung des realen Objekts dort anzuzeigen, wo sie erscheinen.
- Simulation: Das Testen neuer Produkte oder Produktionsroutinen auf dem Digital Twin ist kostengünstiger und schneller als reale Kampagnen im Testbetrieb durchzuführen. Prozessoptimierung und Feineinstellung können unter Vermeidung von Risiken und Produktionsverlusten stattfinden.
- Optimierung: Durch die verfügbaren Konstruktions- und Verhaltensdaten einer gesamten Anlage mit all ihren Prozessen, Materialflüssen und Arbeitsroutinen ist es möglich, Engpässe in der Material- oder Kranlogistik mittels Produktionssimulation zu erkennen. Änderungen von Parametern, Maschinen und Einbaulagen führen zu einer optimierten Anlagenauslegung mit optimalen Produktionsbedingungen.
- Vorhersage: Mit dem Einsatz von maschinellem Lernen und künstlicher Intelligenz können kritische Aspekte von Prozessen, Anlagenzustand und Verfügbarkeit sowie Produktqualität vorhergesagt und schließlich an die aktuellen Umstände angepasst werden.
- Domain Know-how: Als Systemlieferant für die Metallindustrie ist SMS group in der Lage, Mechanik, Elektrik und Automation, Service und Digitalisierung aus einer Hand zu liefern. Sämtliche Daten, Pläne, Layouts und Informationen lassen sich leicht in einem Digital Twin für SMS-Erzeugnisse zusammenfassen. Natürlich ist auch die Integration von Fremdeinrichtungen möglich.
- Schulung: Mit der idealen Replizierung von realen Maschinen und Prozessen in der virtuellen Welt in Kombination mit einer 3D-Visualisierung, die direkt aus den Konstruktionsplänen erstellt wurde, können Bediener und Wartungspersonal einfache Wartungsaufgaben sowie komplexe Prozesssteuerung einfacher und schneller erlernen.
Der Digital Twin Application Layer
Um alle oben genannten Vorteile bieten zu können, muss der Digital Twin bestimmte Funktionalitäten und eine zugrunde liegende Software-Architektur erfüllen. Für fast jedes Thema gibt es eine Softwarelösung, etwa für eine einfache Berechnung der Wandtemperatur in einem Ofen oder für die komplexen Mechanismen, die zu ihrer Steuerung benötigt werden. Ein weiteres Beispiel ist der Integrationstest für die Level-1-Automatisierung, der durchgeführt wird, um Prozesse und Produktion zu simulieren, bevor das Automatisierungssystem in der realen Umgebung eingesetzt wird. Diese Testumgebung dient auch zur Ausbildung und Schulung der Bediener. Das Potenzial, das durch die Bündelung dieser isolierten und getrennten Lösungen geboten wird, findet seinen Weg in der Anwendung als Digital Twin:
Die Digital-Twin-Anwendung dient hauptsächlich als zentrale und einheitliche Schnittstelle. Dies bedeutet, dass alle Anwendungen der SMS group, SMS digital und ihrer Kunden sowie auch Anwendungen Dritter sich mit dem Digital Twin verbinden können. Ziel ist es, das gesamte Wissen und die Ergebnisse, die in bestehenden Anwendungen gebündelt sind, an den Digital Twin zu liefern, um seine Daten anzureichern. Auf diese Weise wächst der digitale Zwilling weiter und wird immer zuverlässiger mit der Anzahl der mit ihm verbundenen Anwendungen. Die Tatsache, dass eine Digital-Twin-Instanz an ein einziges reales Objekt gebunden ist, vereinfacht die Identifizierung in der virtuellen Welt für externe Anwendungen, die normalerweise ihre eigene ID verwenden, um Objekte zu verfolgen.
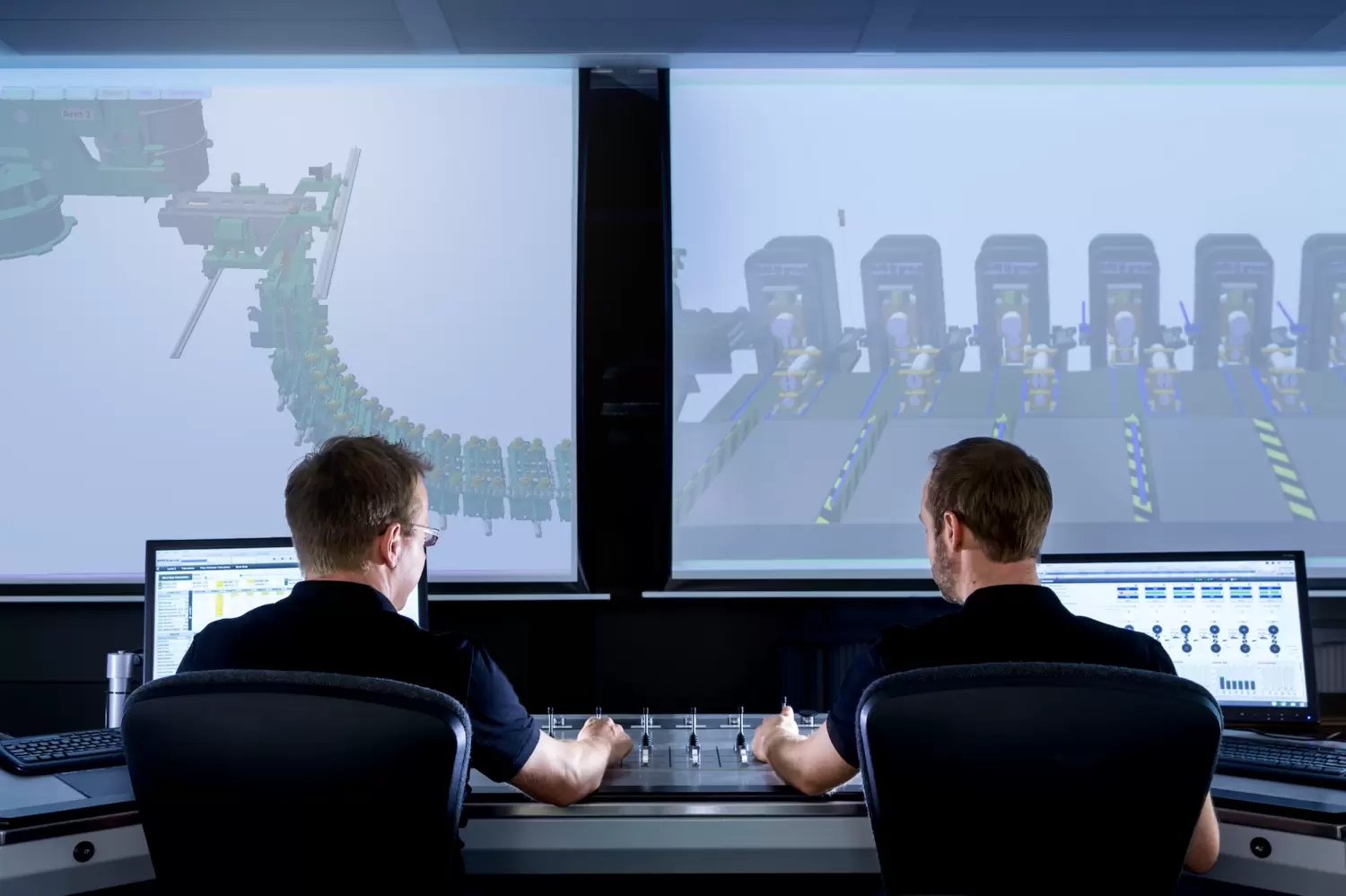
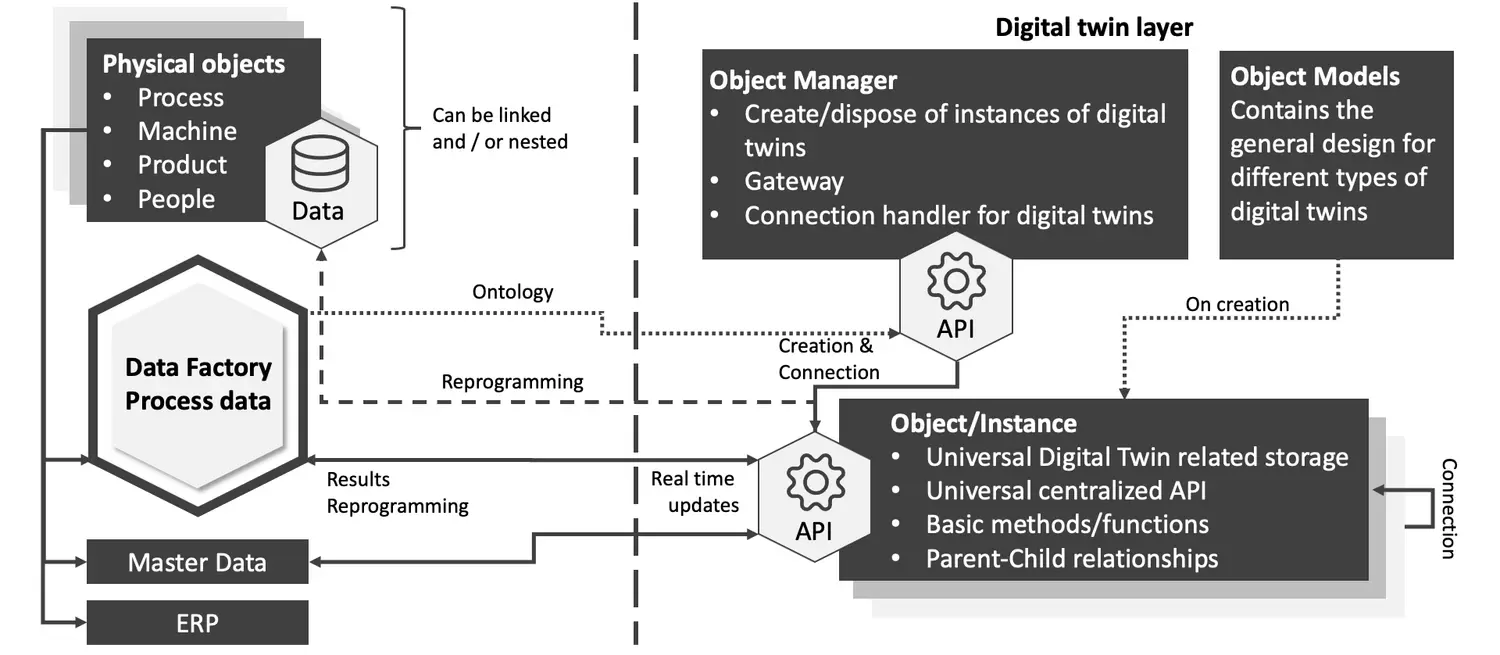
Der Aufbau eines Digital Twins erfordert ein hohes Maß an Konnektivität zwischen Daten, Anwendungen, Twins anderer Entitäten und zum Objekt in der realen Welt. Konnektivität erfordert auch die Homogenisierung von Daten und Protokollen, also eine allgemeine Form zur Speicherung und Übertragung von Daten oder digitalen Inhalten. Diese beiden Themen sind die Hauptherausforderungen und bilden auch unabhängig vom Anwendungsfall die Grundmodule des Digital Twins. Ein weiteres Thema ist der modulare Aufbau der Anwendung des Digital Twins, der die Abbildung von verschachtelten und verknüpften Strukturen ermöglicht. Beispielsweise benötigt der Digital Twin des Gießprozesses den Digital Twin der Gießmaschine, der auch die Digital Twins seiner Teile enthält. Diese Sub-Twins müssen miteinander verbunden werden. Darüber hinaus muss auch ein Digital Twin der Produkte, die im Prozess auftreten, berücksichtigt werden: Aus verschiedenen Schmelzen, die in den Verteiler gegeben werden, entsteht ein Strang, der schließlich geschnitten und in Platten oder Blöcken organisiert wird.
Insgesamt bietet die Anwendung des Digital Twins mit ihrer Konnektivität, Modularität und Datenorchestrierung für jede Anwendung eine geeignete Plattform, auf der sie laufen kann. Da die Daten der Vergangenheit, der Gegenwart und sogar der Zukunft auf homogene Weise angeboten werden, ist es einfach, maschinelles Lernen und künstliche Intelligenz anzuwenden, Simulationen durchzuführen und Vorhersagen mit Auswirkungen auf Produktion und Verfügbarkeit zu treffen.
Ein Digital Twin ist nicht einfach ein Produkt, sondern eine individuelle Lösung, die vollständig auf die Anforderungen des Kunden zugeschnitten ist. Es kann eine komplette Anlage als Digital Twin dargestellt werden, aber auch einzelne Prozessmodelle oder Werkzeuge. Der Digital Twin ist also nicht als \"one fits all\"-Lösung für ein konkretes Problem konzipiert, sondern enthält verschiedene Funktionalitäten, die an unterschiedliche Problemstellungen angepasst werden können. Verschiedene Anwendungen können über eine Schnittstelle gebündelt werden und nahtlos auf Informationen aus anderen Anwendungen zugreifen.
Es ist nicht immer notwendig, Materialproben zu nehmen und damit wertvolle Ressourcen zu verbrauchen, denn die Daten des Digital Twins können für virtuelle Testzwecke genutzt werden. Daher ist der Digital Twin ein hervorragendes Beispiel für die digitale Transformation, die es ermöglicht, die physische und digitale Welt immer realistischer miteinander zu vernetzen und die Fertigungsindustrie effizienter und nachhaltiger zu gestalten.
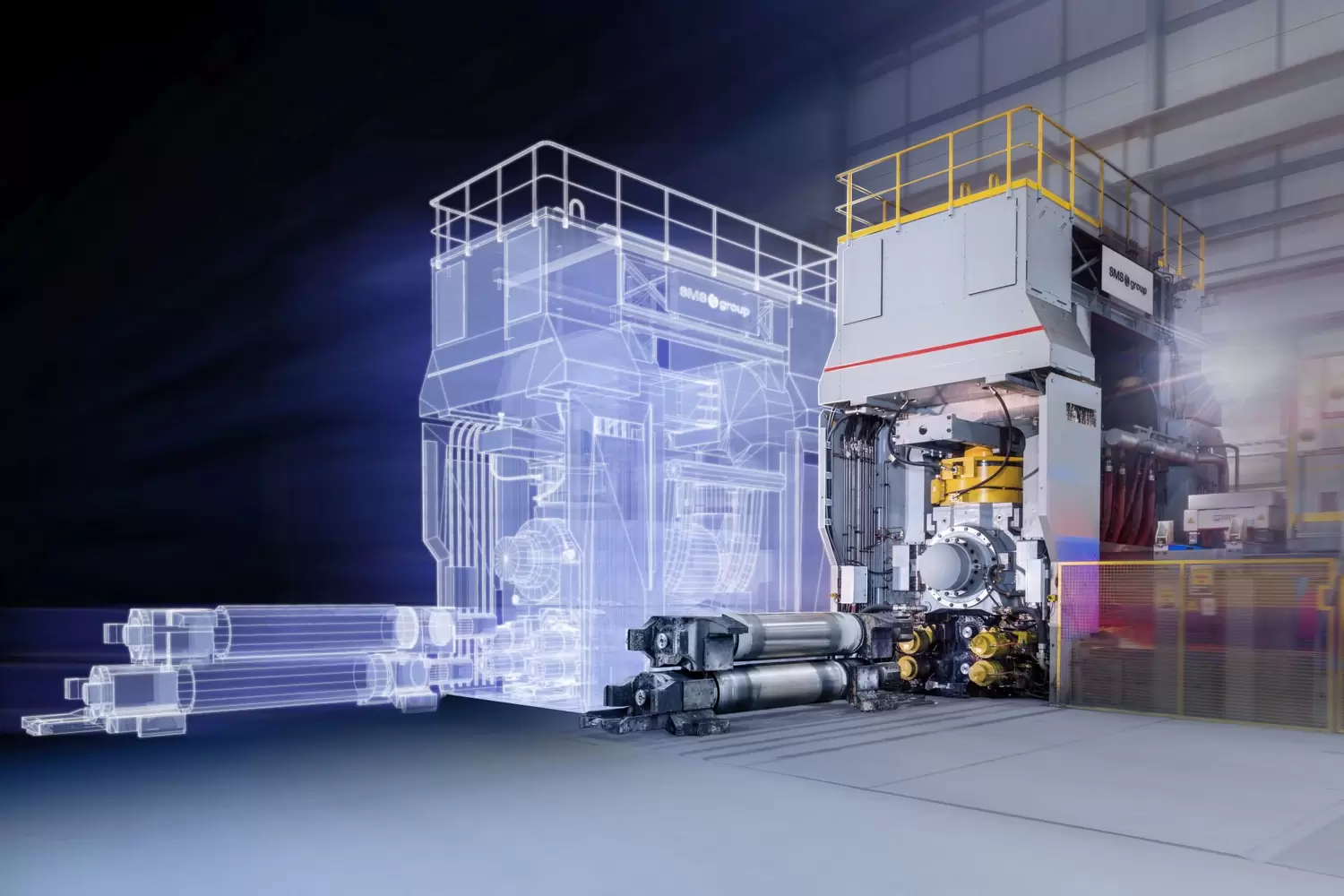
Weiterführende Informationen
Weiter Informationen und Use cases zu Digital Twins finden sie auf unserer Website.