Automatisierte Schmiedelinien haben oft drei bis fünf Stationen, in denen verschiedene Stadien der Schmiedeteile liegen. Es werden meist genau so viele Sprühköpfe benötigt, die in der Anordnung der Düsen den belasteten Zonen der Gesenke angepasst sind. Diese werden über lineare Zuführungen, Roboter oder kurvengesteuerte Gelenkarme in den Pressenraum geführt, wenn die Presse sich nach einem Schmiedeschlag geöffnet hat. Ziel verbesserter Sprühtechnik ist es, die Lebensdauer der Schmiedegesenke zu verlängern und Sprühmittel zu sparen.
Neues Design
Durch das Heranführen von jeweils drei verschiedenen Kanälen (Zerstäuberluft, Sprühmedium und Steuerluft mit einem Systemdruck von 4 bis 6 bar) an jede Düse ergibt sich eine komplexe Struktur aus Kanälen. Das besondere Design der SMS group (Siehe auch Patentanmeldung WO 201712609 A2), ergibt sich aus der konsequenten Umsetzung, die funktionsführenden Wege und Kammern mit einer konstanten Wandstärke zu versehen. Ein Verfahren, das sich bei additiv hergestellten Bauteilen für die Strömungstechnik inzwischen auch für andere Bauteile der SMS group anbietet. Für die Sprühköpfe stellte sich das Design im Laufe der Entwicklung als revolutionär heraus, da es gleich mehrere Vorteile bietet: geringes Gewicht, flexibel in der Gestaltung und verwendbar für verschiedene Materialien. Um die Elemente widerstandsfähiger zu machen, können die Sprühköpfe auch aus Metallhergestellt werden, und das ohne konstruktive oder geometrische Änderungen. Dies ist ein wesentlicher Vorteil des von der SMS group entwickelten 3D-Sprühkopfes.
Erfolgreich im Einsatz
Die Sprühköpfe wurden inzwischen erfolgreich bei Kunden getestet und eingesetzt. Dabei konnten meist die vorhandenen Anschlüsse genutzt werden. Die eingesetzten Sprühköpfe aus Polyamid wiesen im Dauerbetrieb eine Temperatur von circa 50 Grad Celsius auf und arbeiteten ohne Probleme. Sprühbild sowie Handling war den konventionell gefertigten Teilen dabei sogar überlegen. Ablagerungen im Inneren, die bei konventionellen Sprühköpfen oft entstehen, wurden nicht festgestellt. Der Grund dafür liegt in einer strömungsoptimierten Leitungsführung zu den Düsen. Der Betreiber Bharat Forge war sehr zufrieden mit dem Einsatz des Sprühkopfes und möchte die Technik in Zukunft in seinem Hause etablieren. „So können wir die Roboter schonen, die sonst bis zu ihrer Belastungsgrenze gebracht werden.“
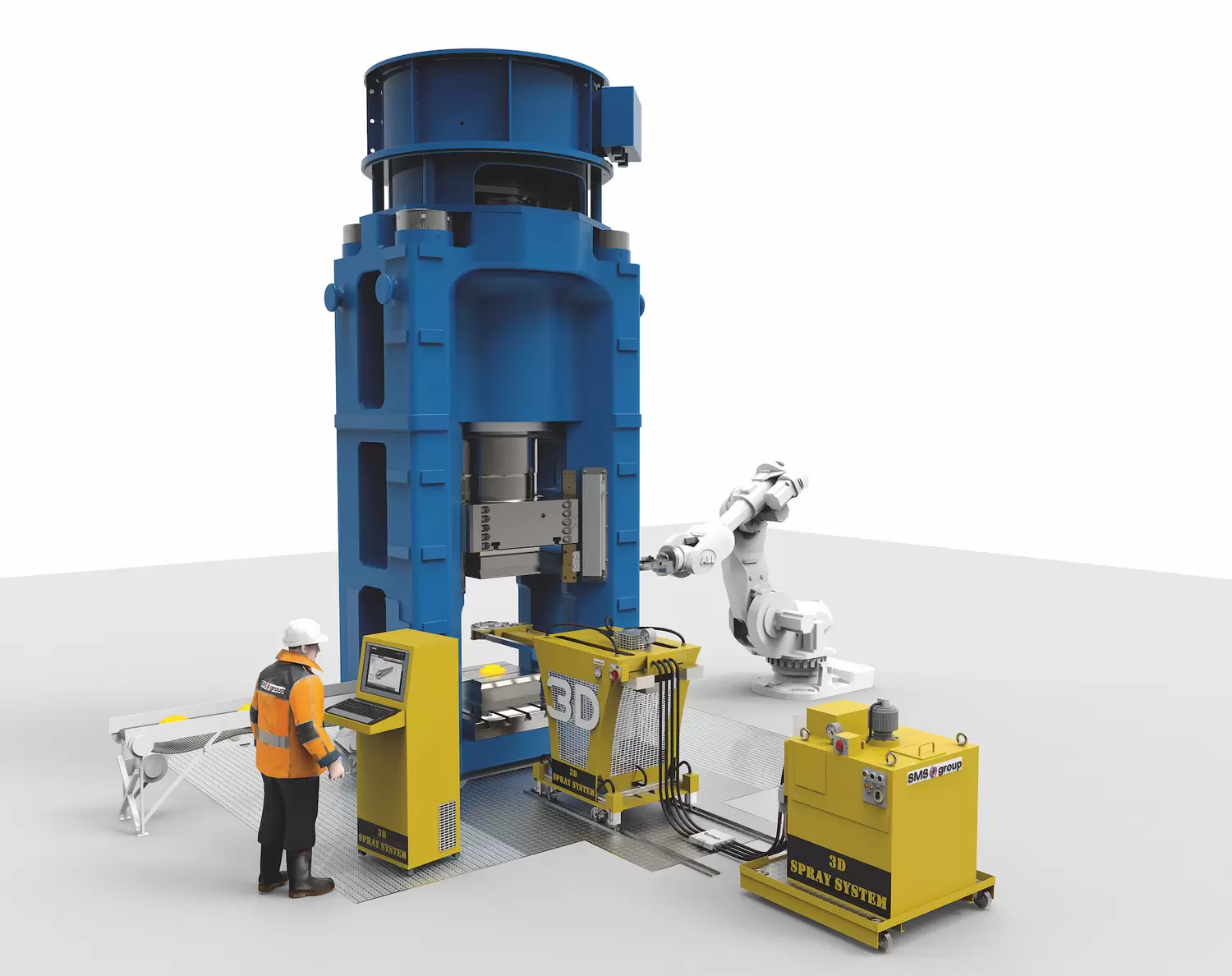
Sprühköpfe aus Kunststoff
Die Sprühköpfe aus Kunststoff sollten thermisch nicht überlastet werden. Für den Fall, dass die Schmiedeteile mit Sprühköpfen in Kontakt kommen, müssen Schutzmaßnahmen getroffen werden,um die Standzeit der Sprühköpfe nicht vorzeitig zu verkürzen. Empfohlen wird das sofortige Zurückziehen des Sprüharms und das Auslösen einer Notkühlung mit Druckluft. Ein weiterer großer Vorteil liegt im geringen Bauteilgewicht. Ein 3D-Sprühkopf aus Kunststoff wiegt gerade einmal ein Zehntel eines konventionellen Sprühkopfes. Bei Metall ist der 3D-Sprühkopfimmer noch bis zu 70 Prozent leichter als ein vergleichbarer konventioneller Sprühkopf. Die beschleunigte Masse ist geringer und ermöglicht im Endeffekt eine höhere Taktzeit der meist automatisierten Prozesse. Letztendlich ist die Herstellung mit der additiven Technologie in Kombination mit diesem Design auch energieeffizient, da nur genau so viel Material eingesetzt wird wie benötigt.
Enge Absprache mit dem Kunden
Es hat sich gezeigt, dass die Konstruktion der 3D-Sprühköpfe nicht sehr aufwändig ist. Die SMS group hat dafür ein Verfahren entwickelt, bei dem der Anwender nur noch die Positionen der Düsen festlegt und übermittelt. Das könnten auch per Hand auf einer Zeichnung eingetragene Kreuze sein oder Positionsangaben in einer Tabelle. Da die SMS group ihre Kunden als beste Experten für die eigenen Produkte sieht, wird vornehmlich die Platzierung der Düsen verwendet, die der Kunde vorgibt. Selbstverständlich übernehmen die SMS group-Technologen für die Gesenkschmiede auch die gesamte Auslegung. Über Verbesserungspotential wird ebenfalls beraten. Da Änderungen in den Düsenpositionen oder Winkelanstellungen keinen weiteren großen Aufwand bedeuten, kann nun auch schrittweise vorgegangen werden: So können beispielsweise auch im ersten Schritt Sprühköpfe aus Polyamid hergestellt werden und anschließend die gleichen Geometrien aus Metall. An dieser Stelle hat ein Umdenken stattgefunden, das durch den 3D-Druck in Gang gesetzt wurde. Der Kunde hat die freie Wahl. Obwohl der Sprühkopf das Kernstück dieser Technologie darstellt, sind all diese Vorteile ohne eine optimal angepasste Peripherie nicht möglich. Die SMS group bietet ihren Kunden ein komplettes Paket, das in der Folge auch noch weitere Vorteile anbieten kann. Es besteht aus drei größeren Blöcken, die eine Einheit bilden – Sprühtechnik, Automation und Steuerung.
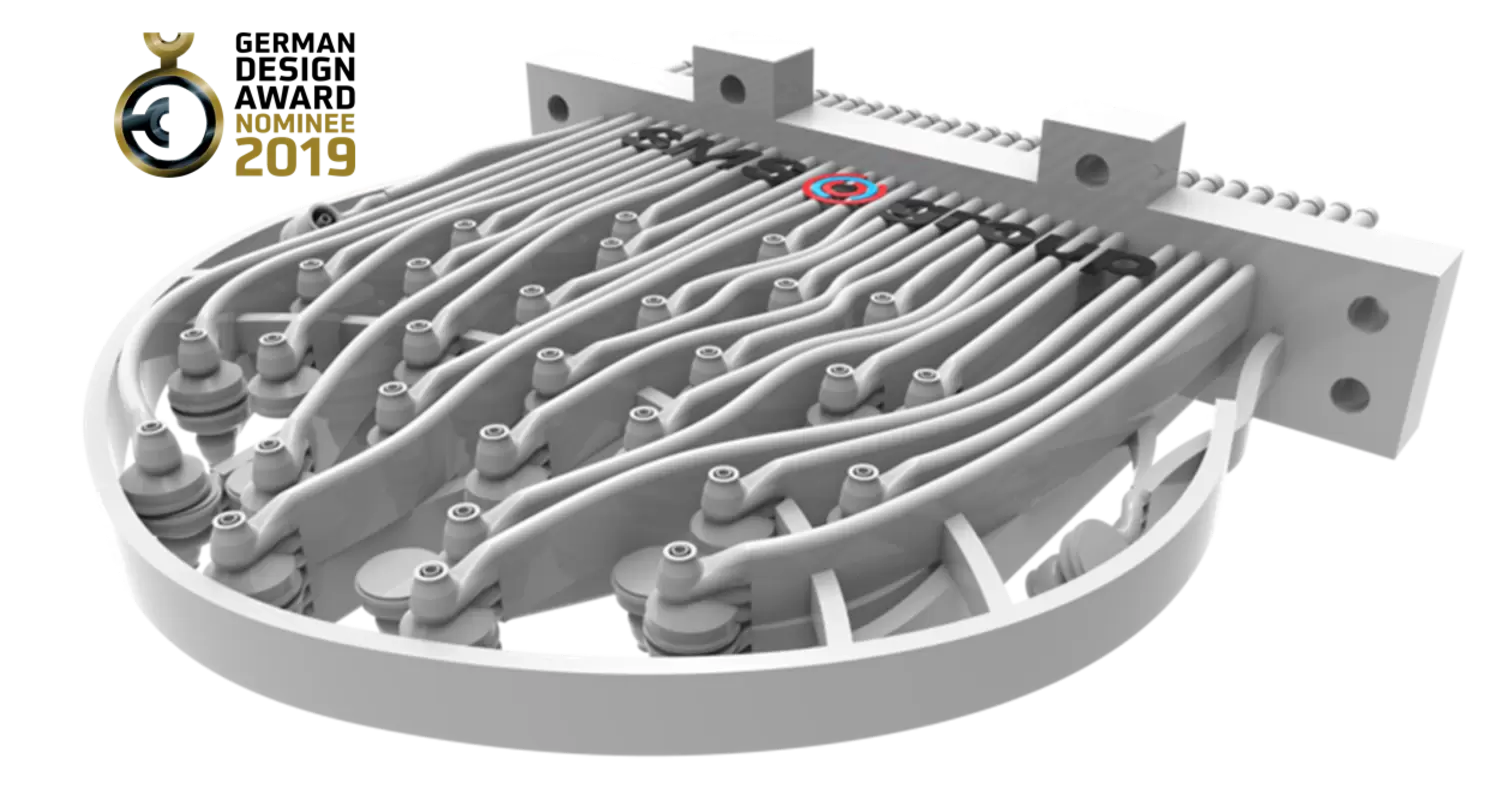
Aufeinander abgestimmtes Komplettpaket
Die schnelle Zuführung der Automation ist linear und dem geringeren Gewicht der zu tragenden Sprühköpfe angepasst. Die angeschlossene Sprühtechnik mit der Steuerung bietet noch ganz andere Möglichkeiten, die bisher in diesem Umfang in der Sprühtechnik der Gesenkschmiede so nicht bekannt waren. Durch die additive Herstellung ist der Komplexitätsgrad für die Herstellung nicht mehr relevant und das wirkt sich auch auf die Steuerungstechnik aus. Ob nun drei oder zwanzig Düsen einzeln, kurz hintereinander oder im Wechsel geschaltet werden, spielt für den Anwender keine Rolle. Prinzipiell kann die Ansteuerung jeder einzelnen Düse am Eingabebildschirm verändert werden. Zur Optimierung der benötigten Sprühmediummenge wird der Prozess von Sensoren permanent überwacht. Stromführende Elemente können in Form von Aussparungen direkt in der Struktur beim Druck mit vorgesehen werden. Während früher die Einstellung von einzelnen Drücken und Schaltzeiten separat angegeben werden musste, ist nun eine intuitive einfache Eingabe möglich. Ein standardisierter Anschluss macht den Austausch der 3D-gedruckten Teile zudem einfach, sicher und schnell. Durch intelligente Sensorik, intuitive Bedienung, Auswertung in Echtzeit und permanente Prozessoptimierung wird das 3D-Sprühsystem fit für Industrie 4.0.