Trend zum Schälen im großen Stil - BGH nimmt Vorreiterrolle ein
Der Markt für geschmiedeten Stabstahl erfordert große Abmessungen, hochqualitatives und insbesondere oberflächenfehlerfreies Rundmaterial mit engen Toleranzen. Wurden früher selten geschälte Stäbe mit Durchmessern größer als 200 Millimeter gefordert, ist dieser Bedarf heute aufgrund des wachsenden Energiemarktes angestiegen.
Mit der Investition in die Schälmaschine vom Typ PMH 600 hat die BGH Edelstahl aus Siegen nun als einer der ersten Produzenten auf die sich verändernden Marktsituationen reagiert. Denn gerade hochqualitative Güten werden auch mit großen Durchmessern fast nur noch mit bearbeiteten Oberflächen und entsprechend hohen Prüfanforderungen ausgeliefert. Mit einem Fertigdurchmesser von bis zu 600 Millimetern stößt diese Maschine in neue Dimensionen vor.
„Die höheren Verkaufsmengen hätten wir mit den bestehenden Maschinen nicht mehr abbilden können“, erklärt Jost Kretzer, Betriebsleiter bei der BGH. „BGH hat zwischen der Installation von Drehmaschinen und einer neuen Schälmaschine abgewogen und sich aus verschiedenen Gründen für eine Schälmaschine entschieden.“ Die neue Maschine musste aber bestimmte Eigenschaften mitbringen. Mit ihr sollte die Bearbeitung von Stabstahl mit einem Gesamtgewicht von 25 Tonnen und einem Durchmesserbereich von bis zu 600 Millimetern möglich sein. „Mit diesen Zahlen sind wir an die Schälmaschinenhersteller herangetreten, weil es solch eine Maschine in dieser Größenordnung bis dato noch nicht gab. Mit der SMS group haben wir dann in einem Projektierungszeitraum von zwei Jahren diese Maschine nach unseren Wünschen konzipiert“, erinnert sich Jost Kretzer.
Pionierarbeit bei der Entwicklung der Schälwendeplatte
Für eine Schälmaschine dieser Dimension gab es bis dato auch noch kein Werkzeug, mit dem sich die geforderten Zerspanungswerte realisieren ließen. Aus diesem Grund wandte sich die BGH an die Experten von Cutting Solutions by CERATIZIT in Reutte/Österreich, die für die verschiedensten Anwendungen im Bereich Schälen ein umfangreiches Programm an Schälwendeschneidplatten anbieten und über ein fundamentales Fachwissen auf diesem Gebiet verfügen. Die speziellen Bedürfnisse der BGH und die Anforderungen, die eine der weltweit größten Schälmaschinen an das Werkzeug stellen, veranlassten CERATIZIT, völlig neue Schälwendeschneidplatten zu entwickeln.
Produktmanager Ronald Huber erinnert sich noch gut an die Entwicklung, bei der die Werkzeugspezialisten aus Reutte ein großes Stück Pionierarbeit geleistet haben: „Die bestehende Rundplatte hatte gerade hinsichtlich ihrer Positionierbarkeit entscheidende Nachteile. Wir haben die Schruppplatte daher auf eine mehrkantige Außenform umgestaltet, um neben der exakten Indexierung im Plattensitz auch bessere Zerspanungseigenschaften zu erreichen.“ Wie Huber erklärt, ist ein guter Spanbruch ausschlaggebend, um prozesssicher zu schälen. Langspanbildung gilt es unbedingt zu vermeiden, da im Schälprozess pro Stunde rund fünf Tonnen Späne anfallen. „Mit der neuen Sechskant-Schruppplatte gewährleisten wir nicht nur beste Spanformung. Sie hält auch den extrem hohen Vorschüben von bis zu 24 mm/U stand. Damit haben wir uns gemeinsam mit der BGH und der SMS group in Bereiche des Schälens vorgewagt, wo noch keiner war und bis zum heutigen Tage – außer uns – noch keiner ist“, betont der Produktmanager von CERATIZIT.
Schälen für beste Durchmessertoleranz und Oberflächenrauigkiet
Die BGH Edelstahl in Siegen produziert Edelstahl und Sonderlegierungen für höchste Beanspruchungen. Um die gewünschte Oberflächengüte, Maßgenauigkeit und Rundheit ihrer Stabstähle zu gewährleisten, werden die Stäbe von der BGH vor der Auslieferung geschält. Das Ergebnis sind Halbfabrikate, die von Drehereien weiterverarbeitet werden. So dienen die Stäbe als Vormaterial für den Maschinenbau, die Öl- und Gasindustrie oder die chemische Industrie. Auch hochbeanspruchte Getriebe für Windkraftanlagen entstehen aus dem Vormaterial der Firma BGH. „Unsere Kunden wünschen sich einen mechanisch bearbeiteten Stabstahl ohne rohe Schmiedeoberfläche“, erklärt Jost Kretzer. Um sowohl die gewünschte Durchmessertoleranz als auch die Oberflächenrauigkeit zu gewährleisten, wird die Oxyd- und Walzhaut der geschmiedeten Stäbe abgeschält.
Nur durch die enge Zusammenarbeit von Anwender, Maschinenbauer und Werkzeuglieferant konnten die gewünschten Erfolgskriterien erzielt und neue Marktsegmente erschlossen werden. Jost Kretzer fasst die vertrauensvolle Zusammenarbeit mit der SMS group als Maschinenhersteller und Cutting Solutions by CERATIZIT als bevorzugtem Werkzeuglieferant wie folgt zusammen: „Wenn nicht alle Beteiligten an einem Strang gezogen hätten, wäre ein solches Ergebnis nicht möglich gewesen. Wir als Anwender sind auch weiterhin in der Pflicht und müssen offen und ehrlich die Vor- und Nachteile kommunizieren. Solange Werkzeuglieferant und Maschinenhersteller ein offenes Ohr für diese Belange haben, können die Resultate weiter verbessert werden. Dadurch gewinnen alle Parteien.“
Herausforderung für optimal geschälte Stäbe
Die besondere Herausforderung innerhalb der Fertigung von Blankstählen besteht darin, dass hier häufig zerspanungstechnisch schwierige Werkstoffe wie rostfreie Stähle und Nickelbasis- Legierungen verarbeitet werden. Die Maschinen der PMH-Baureihe bieten hierzu höhere Leistungsreserven als ihre Vorgänger. Des Weiteren ist das Vormaterial bei großen Stangenformaten in der Regel geschmiedet. Dieses Herstellverfahren führt jedoch dazu, dass das Material deutlich unrunder ist, als man es von gewalztem Material kennt.
Hier war es bislang so, dass das Gros der geschmiedeten Stangen über 250 Millimeter auf Drehmaschinen zu Blankstahl verarbeitet wurde. Dies ist in dreierlei Hinsicht ineffizient: Zum einen dauert das Drehen gegenüber dem Schälen bis zu 16- mal länger. Zum anderen sind beim Drehen höhere Rüstzeiten wie Zentrieren, Aufspannen und Umspannen erforderlich. Darüber hinaus sind bei der Drehbearbeitung höhere Zugaben erforderlich, da die Schälmaschine gegenüber der Drehbearbeitung leichten Krümmungen im Stab folgen kann.
Bei bisherigen Schälmaschinen-Konzepten ist dies ebenso der Fall, weswegen diese mit starren Führungssystemen an Ein- und Auslauf arbeiten. Anders bei der neuen PMH-Baureihe: Je nach Kundenanforderung kann sie nicht nur nach dem herkömmlichen Prinzip mit starren Führungen arbeiten, sondern passt sich bei Bedarf der Krümmung der Stange an und nimmt nur minimal Stahl ab.
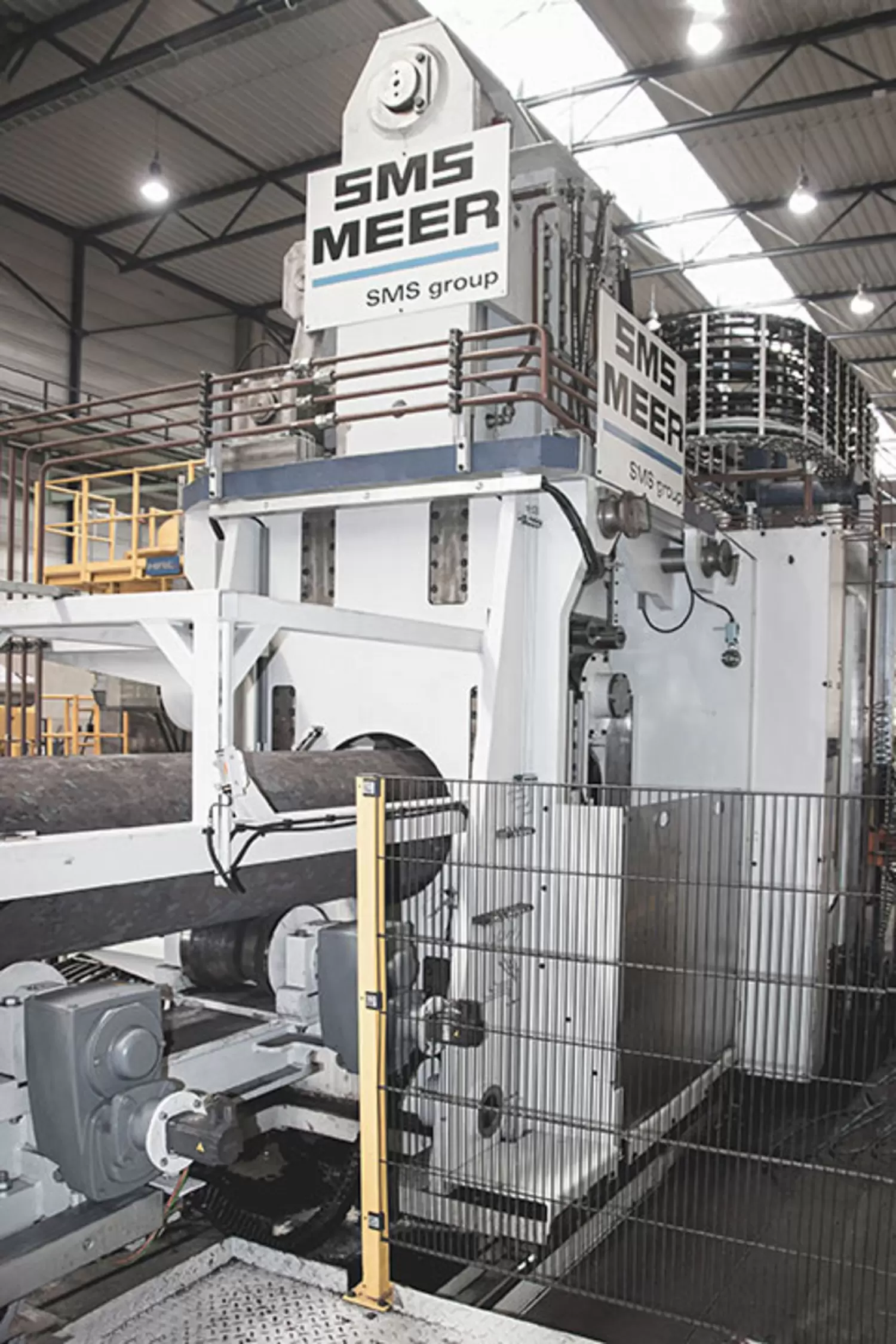
Wenig Probleme mit Stabkrümmungen
Das Arbeitsprinzip der Führungssysteme am Ein- und Auslauf ist einfach: Ein Einschubwagen klemmt den Stab zunächst mittig und transportiert ihn zur Schälmaschine. Die angetriebenen Rollen des Einlaufrollgangs sowie die im Wagenbett integrierten, angetriebenen Stützrollen sorgen dabei für Gleichmäßigkeit. Der Einschubwagen führt den Stabanfang dann in die geöffnete Einlaufführung ein, fährt wieder in Richtung Stabende/Einlaufrollgang und spannt den Stab in einem Abstand von mindestens drei Metern zur Einlaufführung. Das Spannen erfolgt hierbei außermittig. Die Spannbacken des Einschubwagens fahren zunächst weggesteuert auf Kontakt zur Stange. Danach wird der Klemmdruck beidseitig gleichmäßig angehoben und an beiden Klemmzylindern konstant gehalten. Dann schiebt der Einschubwagen den Stab weiter durch die Maschine und der Schälvorgang beginnt.
Durchdachtes Arbeitsprinzip
Während des Schälens wird die Mitte des Prozesses von der Einlaufführung vorgegeben. Eventuelle Ungeradheiten des Stabes gleicht der Auszugswagen aus, da die Klemmzylinder als Paket horizontal schwimmen. Sobald der Stabanfang die Schälmaschine verlässt, setzt sich der Auszugwagen in Bewegung. Die Geschwindigkeit des Auszugwagens wird mit der des Einschubwagens synchronisiert, bevor der Auszugwagen ebenfalls außermittig spannt. Für einen kurzen Moment wird der Stab sowohl im Einschubwagen als auch im Auszugwagen geklemmt, bevor der Stab vollständig an den Auszugwagen übergeben wird.
Je nach Stangenlänge wird die Übergabe zwischen Einschub- und Auszugwagen mehrfach wiederholt. Nach dem Ausziehen wird der Stab von den im Wagenbett integrierten Stützrollen und den Rollen des Auslaufrollgangs abtransportiert und auf den Ablagerost abgeworfen. Das Arbeitsprinzip mit einem Einschubwagen hat noch weitere Vorteile gegenüber dem Einsatz eines Einschubapparates mit Rollen: Dadurch, dass die Stangen im Einschubwagen an einer festen Position geklemmt werden, kann wirksam verhindert werden, dass sich die Stange während des Schälprozesses dreht.
Diese sogenannten Stangendreher traten bei herkömmlichen Maschinen in Kombination mit dem geschmiedeten, relativ ungenauen Material immer wieder auf und verursachten teils erhebliche Maschinenschäden.
Günstigere Betriebskosten
Zentrales Anliegen war, für die neuen PMH-Baureihen im Verbund mit den umgesetzten schältechnischen Innovationen ein über die Lebensdauer der Maschine optimiertes Betriebskostenkonzept zu realisieren. Der Aufwand für Wartung und Werkzeugwechsel ist bei der PMH gegenüber den Großschälmaschinen der Vorgängergeneration deutlich reduziert worden. So entfällt beispielsweise durch die Verwendung von verschleißarmen Einschubrollen das regelmäßige Wechseln der Einschubrollen. Ein solcher Wechsel verschlissener Rollen eines Einschubapparates verschlingt nicht nur mehrere Tausend Euro Materialkosten, sondern benötigt bis zu einer halben Schicht Arbeitszeit, in der die Maschine nicht produzieren kann. Ferner beschränkt sich der Werkzeugwechsel bei der PMH der SMS group auf das Tauschen der Werkzeugkassetten und ermöglicht eine minimale Wechselzeit der Schälwerkzeuge. Bei herkömmlichen Maschinen muss hierzu die gesamte Schlitteneinheit getauscht werden. Ebenso kann der gesamte Verstellbereich der Maschine mit nur einem Werkzeug abgedeckt werden.
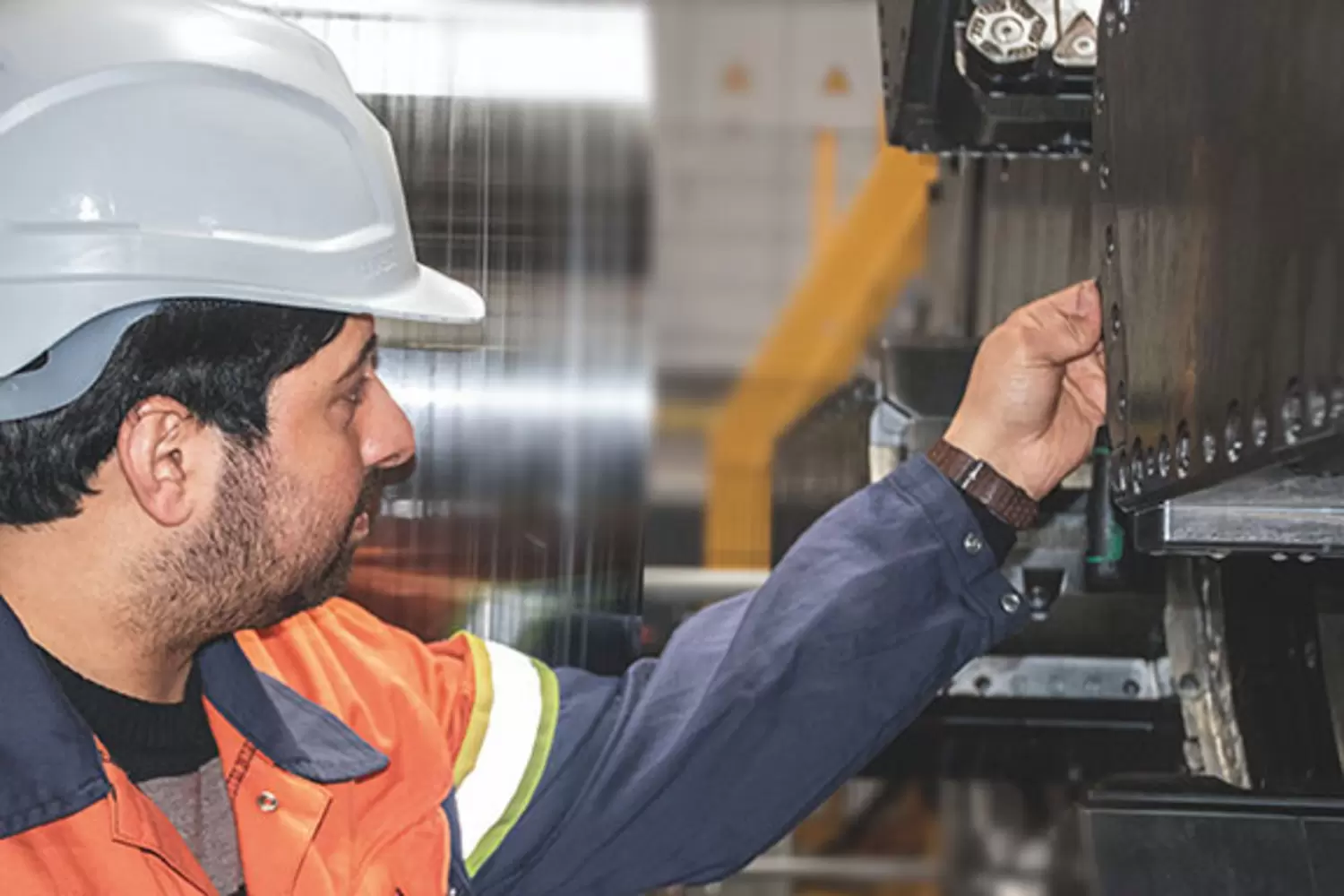