Prof. Dr. Hans Ferkel, Chief Technology Officer der SMS group GmbH, spricht im Interview mit der Zeitschrift Prozesswärme über den Einfluss von Wasserstoff auf den metallurgischen Anlagenbau und wie sich die SMS group im Wettbewerb um die beste Lösung für eine CO2-freie Stahlproduktion positioniert.
Die erste CO2-freie Bramme soll auf einer SMS group-Anlage produziert werden, das haben Sie auf der Pressekonferenz der METEC 2019 verkündet. Wann wollen Sie dieses Ziel erreichen?
Hans Ferkel: So schnell wie möglich! Im Grunde kann man das heute schon. Dabei können zwei Wege verfolgt werden: Der eine ist das Recycling durch Einschmelzen von bestehenden Stahlschrotten im Elektrolichtbogenofen mittels grünem Strom; also Strom, der durch regenerative Energie CO2-neutral erzeugt wurde. Der andere Weg ist die Herstellung von Roheisen mit Hilfe der Direktreduktion von Eisenerz mit dem Midrex-Verfahren im Schachtofen. Dabei nutzt man grünen Wasserstoff anstelle von Erdgas. Das so erzeugte direkt reduzierte Eisen (Direct Reduced Iron – DRI) kann dann im Elektrolichtbogenofen weiterverarbeitet werden. Je nachdem, welche Stahlsorten man herstellen möchte, kann eine unterschiedlich ausgeprägte Kombination dieser Verfahren gewählt werden.
Welche Bedeutung hat das Thema Wasserstoff für die SMS group?
Hans Ferkel: Wasserstoff ist von zentraler Bedeutung bei der Herstellung von grünem Roheisen und somit auch für die SMS group als führender Anlagenhersteller im Bereich der Stahlherstellung und Verarbeitung. Voraussetzung dazu ist, neben einer effizienten Herstellung von Wasserstoff mittels Elektrolyse, die Bereitstellung des dafür erforderlichen Stroms, der CO2-frei hergestellt wurde.
Wie positionieren Sie sich im Wettbewerb um die beste Lösung für eine CO2-freie Stahlproduktion?
Hans Ferkel: Wir verfolgen da einen ganzheitlichen Ansatz. Zum einen bieten wir Anlagen für die Herstellung von DRI mittels Gasreduktion an. Dazu favorisieren wir die bewährte Midrex-Technologie. Unsere Tochtergesellschaft Paul Wurth in Luxemburg hat erst letztes Jahr die weltgrößte Midrex-Anlage mit einer Produktionskapazität von 2,5 Mio. Jahrestonnen in Algerien gemeinsam mit unserem Kunden in Betrieb genommen. Und wir bauen gerade eine weitere mit der gleichen Kapazität.
Um gleichzeitig auch eine Lösung für die effizienteste Herstellung von Wasserstoff unseren Kunden anzubieten, beteiligt sich die SMS group über seine Tochter Paul Wurth an dem Startup-Unternehmen Sunfire. Wir setzen dabei bewusst auf die Hochtemperaturelektrolyse (HTE). Gegenüber den klassischen Verfahren der Elektrolyse von flüssigem Wasser verwenden wir bei der HTE Wasserdampf. In vielen Industrien wie der Stahlindustrie wird die Abwärme – besonders die niederkalorische mit Temperaturen zwischen 150 und 250 °C in den meisten Fällen ungenutzt in die Atmosphäre abgegeben – kurz weggekühlt. Der Transport dieser Abwärme für z. B. Fernwärmeanwendungen ist oft wirtschaftlich und ökologisch nicht sinnvoll. Diese Abwärme lässt sich aber bestens für die Herstellung des erforderlichen Wasserdampfes niedrigen Druckes für die HTE vor Ort nutzen. Die erforderliche Dissoziationsenergie für Wasser im Dampfzustand ist deutlich geringer als für Wasser im flüssigen Zustand. Wir schlagen also gleich mehrere Fliegen mit einer Klappe: Wir nutzen diese ungenutzte Wärme, um die Effizienz bei der Herstellung von Wasserstoff mittels HTE auf über 82 % zu realisieren. Herkömmliche Elektrolyseverfahren erreichen kaum 60 %, da diese mit flüssigem Wasser arbeiten müssen.
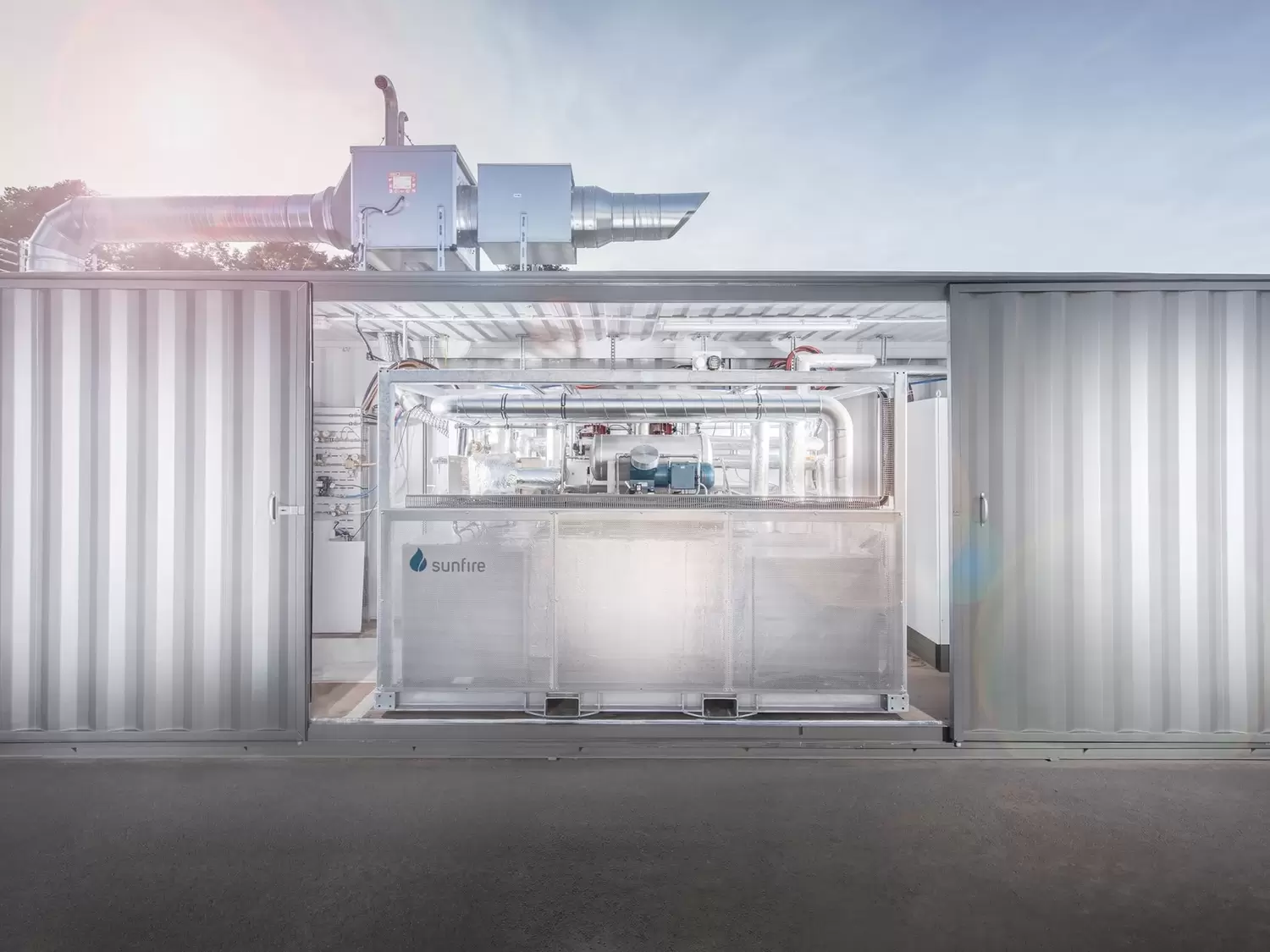
Wie verändert diese technologische Transformation den metallurgischen Anlagenbau?
Hans Ferkel: Es wird sich im Wesentlichen der Prozess der Roheisenherstellung verändern. Der klassische Hochofen mit anschließendem Oxygenstahlwerk wird einer Kombination von H2-dominiertem Direktreduktionsverfahren wie dem Midrex-Verfahren gepaart mit einer Elektrolichtbogenroute weichen. Je nach technischer und wirtschaftlicher Verfügbarkeit wird der erforderliche Wasserstoff dann mittels bevorzugt grünem Strom vor Ort oder anderen Ortes mit dem effizientesten Elektrolyseverfahren hergestellt. Dieser Wandel kann mit unseren Lösungen sukzessiv erfolgen – das heißt einzelne Hochöfen können einer grünen Roheisenherstellung weichen. Dabei verfolgen wir mit der Sunfire-Technologie einen modularen Ansatz.
Aktuell hat das Standardmodul für die Wasserstoffaufbereitung die Größe eines Überseecontainers mit einem Strombedarf von ca. 740 kW. Das entspricht dann 200 Nm3/h H2. Für die Herstellung von 1 Mio. t DRI benötigt man mit der Sunfire-Technologie ca. 300 MW. Für diese Größenordnung haben wir bereits Konzepte entwickelt. Das spannende an der Technik ist, dass die Sunfire-Technik bei Bedarf auch zur Elektrolyse von CO2 zu CO und O genutzt werden kann.
Wie kann die kostspielige Umstellung der Hochofenroute auf Wasserstoff von der Stahlindustrie finanziert werden?
Hans Ferkel: Stahl ist zweifelsohne systemrelevant und somit für den Wohlstand und die soziale Marktwirtschaft unerlässlich. Und dabei ist Stahl sogar auch noch 100 % recycelbar. Somit ist es eine gesellschaftspolitische Aufgabe die Versorgungssicherheit mit Stahl und zwar umweltschonenden Stahl sicherzustellen. Es wird auch Aufgabe des Staates und der Politik sein, die finanziellen Rahmenbedingungen und wirtschaftliche Planungssicherheit für diese Transformation zu schaffen.
Wir als Systemlieferant haben uns zur Aufgabe gemacht, eine zukunftsweisende Technik bieten zu können, um gerade die hohen Emissionen an CO2 aus dem Stahlherstellungsprozess zu eliminieren. Ich bin der Meinung, dass jeder Hersteller von Stahl sich mit diesem Thema beschäftigen muss, um unsere Zukunft zu sichern.
In Europa hat fast jeder Stahlhersteller Pilotprojekte initiiert. Glauben Sie, dass diesem europäischen Vorbild alle Stahlhersteller weltweit folgen werden?
Hans Ferkel: Das ist schwer prognostizierbar. Wenn jedoch die Mehrheit der Staaten erkennt, dass generell mit Ressourcen anders umgegangen werden muss, wird wahrscheinlich auch außerhalb Europa anders gehandelt werden. Europa hat das Problem erkannt und handelt entsprechend strategisch. Es bieten sich auch Chancen in der Einnahme dieser Vorreiterposition. Made in Europe und damit auch Made in Germany gilt bereits seit dem letzten Jahrhundert als Exportschlager für Umwelttechniken. Warum denn nicht auch für Technologien, die die Herstellung von grünem Stahl am effizientesten ermöglichen.
Dieses Interview ist zuerst in Heft 3/2020 der Zeitschrift Prozesswärme erschienen. Das vollständige Interview mit Hans Ferkel finden sie hier.