Zekelman und SMS group schreiben Rekordgeschichte: mit einer kontinuierlichen 28-Zoll-ERW-Rohrschweißanlage mit bis zu 25,4 Millimetern Wanddicke. Neben SMS group's Know-how, bewährter Anlagentechnik und den notwendigen Neuentwicklungen finden sich im Lieferumfang auch das von SMS group entwickelte PERFECT arc® -Querschweißverfahren – für einen kontinuierlichen Fertigungsprozess.
Zekelman meets the market
Im Rahmen des Projektes investiert das Familienunternehmen Zekelman Industries über 150 Millionen US-Dollar in seinen Standort in Blytheville, USA. Mit einer Kapazität von mehr als 400.000 Tonnen pro Jahr wird die neue 28-Zoll-Anlage innerhalb von Zekelman Industries deren Rohrsparte Atlas Tube ergänzen.
In unserem Unternehmen werden wir das langjährige Ziel weiterverfolgen, die Zukunft zu gestalten und nicht auf sie zu warten.
Damit kann Zekelman zukünftig Konstruktions- und Pilingrohre mit Durchmessern im Bereich von 10 ¾ Zoll bis 28 Zoll (273 bis 710 Millimeter) und Wandstärken von bis zu 1 Zoll (25,4 Millimeter) herstellen. Darüber hinaus ist es möglich, quadratische und rechteckige Hohlprofile mit Maßen von 8 Zoll x 8 Zoll bis zu 22 Zoll x 22 Zoll bzw. 34 Zoll x 10 Zoll zu produzieren. Die hochautomatisierte ERW (Electric Resistance Welding)-Rohrschweißanlage wurde im April 2019 bestellt und wird bereits Mitte 2021 in Betrieb gehen. In Summe werden über 75 neue Arbeitsplätze geschaffen.

Für den nordamerikanischen Markt bedeutet dies nicht nur ein breiter aufgestelltes Produktsortiment an HSS- Produkten (Hollow Structural Sections): Mit der neuen Anlage ist Zekelman Industries erstmalig in der Lage, Produkte einer ERW-Rohrschweißanlage größer 20 Zoll im Inland zu produzieren..
So profitieren Zekelman-Kunden von der neuen Anlage
Ausführung und Konfiguration der Anlage erfüllen die höchsten Anforderung an Produktqualität und Durchsatz. Das intelligente X-Pact® Quicksetting System aus dem Hause SMS group sorgt nach einem Dimensionswechsel für die automatische Anstellung der Walzen auf ihre neue Arbeitsposition.
Neben einer Produktionsgeschwindigkeit von bis zu 35 Metern pro Minute bietet die Anlage ein ausgesprochen weites Abmessungs-/Wanddickenverhältnis, das gemeinsam mit der sehr kurzen Umrüstzeit für eine hervorragende Flexibilität bei der Produktion unterschiedlicher Erzeugnisse sorgt.
Erstmalig wird auch für eine Anlage größer 16 Zoll der automatisierte horizontale Walzenwechsel mittels Wechselwagen durchgeführt. Dies hat nicht nur eine verkürzte Umbauzeit zur Folge, sondern erhöht auch die Betriebszeit und somit die Produktionskapazität. Zudem stellt eine kurze Umbauzeit eine größere Produktionsflexibilität sicher – ein erheblicher Erfolgsfaktor in der Konstruktionsrohrherstellung.
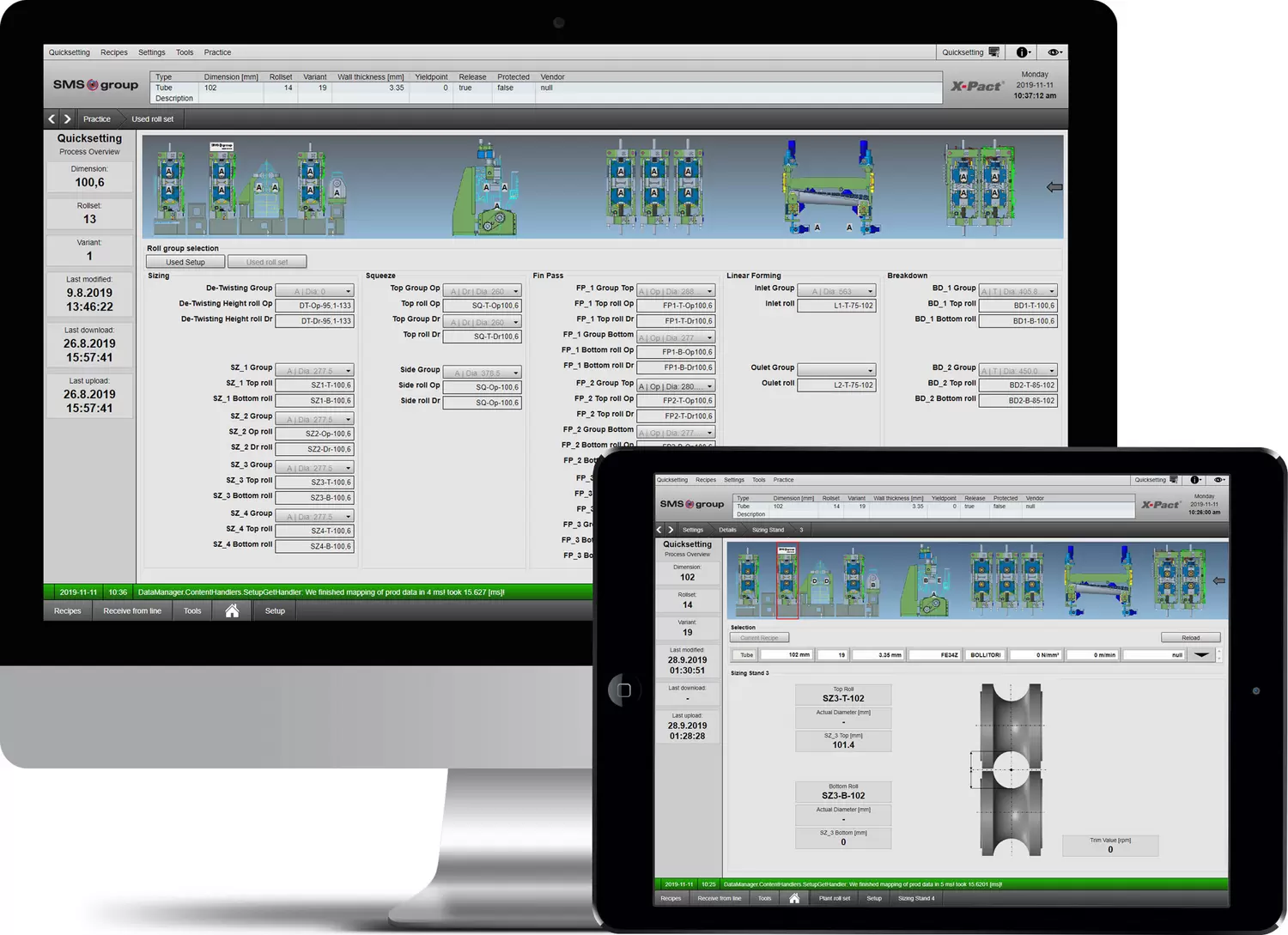
Die Anlage ist darauf ausgelegt, den Walzenwechsel in weniger als 2,5 Stunden zu ermöglichen. Unser langfristiges Ziel ist es, diese Zeit in Richtung 90 Minuten zu optimieren.
„In den vergangenen Jahren stellten wir eine zunehmende Nachfrage nach größeren im Inland erzeugten HSS-Profilen im Brücken-, Transport- und Bausektor fest“, sagt Tom Muth, Präsident von Atlas Tube. „Außerdem werden dickwandigere HSS-Profile, die strengere Anforderungen der seismischen Bestimmungen der AISC beim Breiten-Dickenverhältnis erfüllen, bei seitlichen Verankerungssystemen nachgefragt.“
Sicheres Querschweißen bis 25,4 Millimeter Wandstärke
Zur prozesssicheren Herstellung einer Quernaht bis zu 25,4 Millimeter Banddicke wird an der Querschweißmaschine das von der SMS group entwickelte und patentierte PERFECT arc®-Schweißverfahren eingesetzt. Dabei handelt es sich um einen MSG-Tandem-Schweißprozess (MSG = Metall-Schutzgaß-Schweißen), der in der Lage ist, die 25,4 Millimeter dicken Blechenden in nur einem Schweißdurchgang prozesssicher zu verbinden. Dies spart deutlich Taktzeit in der Querschweißstation und erhöht somit die Produktivität der Gesamtanlage. Geschweißt wird mit bis zu 800A pro Draht.
Die PERFECT arc® Inverter-Schweißstromquellen erreichen einen Wirkungsgrad von über 90 Prozent. Die Energieeinsparung gegenüber älteren Schweißtechniken liegt damit je nach Arbeitspunkt bei bis zu 30 Prozent.
Zur Sicherstellung dieses kritischen Prozesses arbeitet die SMS group mit der Technischen Universität Berlin sowie dem Fraunhofer-Institut in Berlin zusammen. Gemeinsam wird das Querschweißverfahren produktspezifisch getestet und die Einstellungen optimal parametriert. Die aus diesen Versuchen gewonnenen Prozessdaten fließen in die Prozesssoftware ein und können über Synergiekurven jederzeit abgerufen werden – so wird die Zuverlässigkeit, Reproduzierbarkeit und Qualität des Querschweißprozesses deutlich gesteigert.
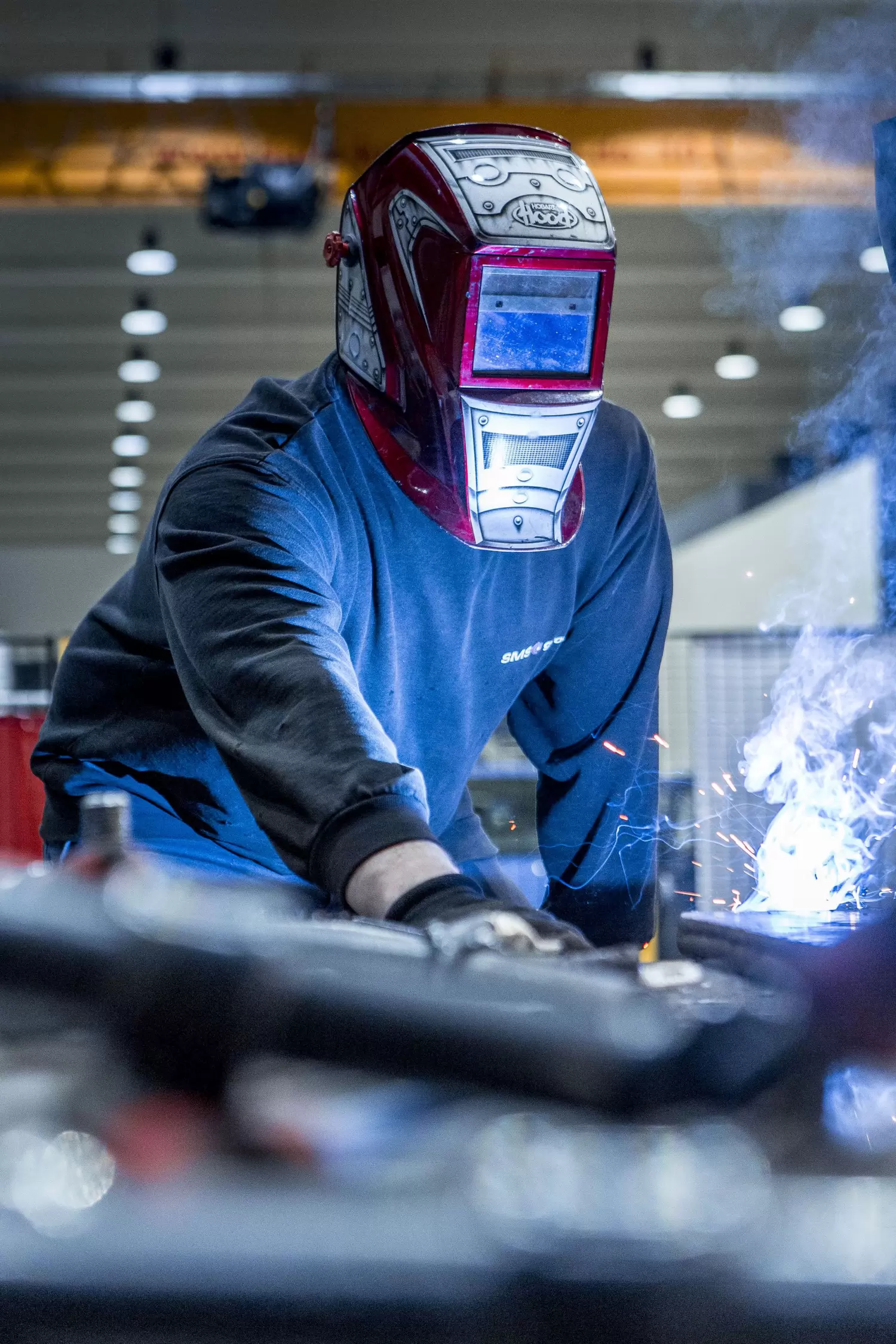
Warum Zekelman sich auf die SMS group verlässt
Zekelman Industries und seine Konstruktionsrohrsparte Atlas Tube setzen bereits seit Jahrzehnten auf die Rohrschweißanlagentechnologie der SMS group. Die Erfolgsgeschichte und der Aufstieg der Firma Atlas Tube – heute die Rohrsparte von Zekelman Industries, unter der Führung von Barry Zekelman – begann bereits mit den ersten beiden ERW-Rohrschweißanlagen der SMS group, die 1994 und 2000 an den Standort Harrow, Kanada, geliefert wurden.
Für die 2006 nach Blytheville, Arkansas, verlagerte 16-Zoll-Rohrschweißlinie, die bereits im Rahmen der Verlagerung durch SMS weitgehend modernisiert und ausgebaut wurde, erhielt die SMS group 2017 mehrere Folgeaufträge. Zur Erweiterung des Produktspektrums sowie zur Verbesserung der Produktivität wurde die Anlage für die Produktion von 18-Zoll-Rundrohrdurchmessern ausgebaut und zuletzt mit einer komplett neuen Kalibrierstrecke ausgestattet. Durch den Einsatz von URD®(Uniform Rigidity Design)-Gerüsten mit horizontalem Gerüstschnellwechsel wurden die Umbauzeiten beim Dimensionswechsel stark reduziert.
Damit baute Zekelman seine führende Position in der Herstellung von Konstruktionsrohren in Nordamerika weiter aus. Seit vielen Jahren verbindet Zekelman Industries und die SMS group eine langfristige und vertrauensvolle Partnerschaft. Der jüngste Auftrag – die weltgrößte kontinuierliche ERW-Rohrschweißanlage – ist der nächste Schritt in der erfolgreichen Zusammenarbeit.
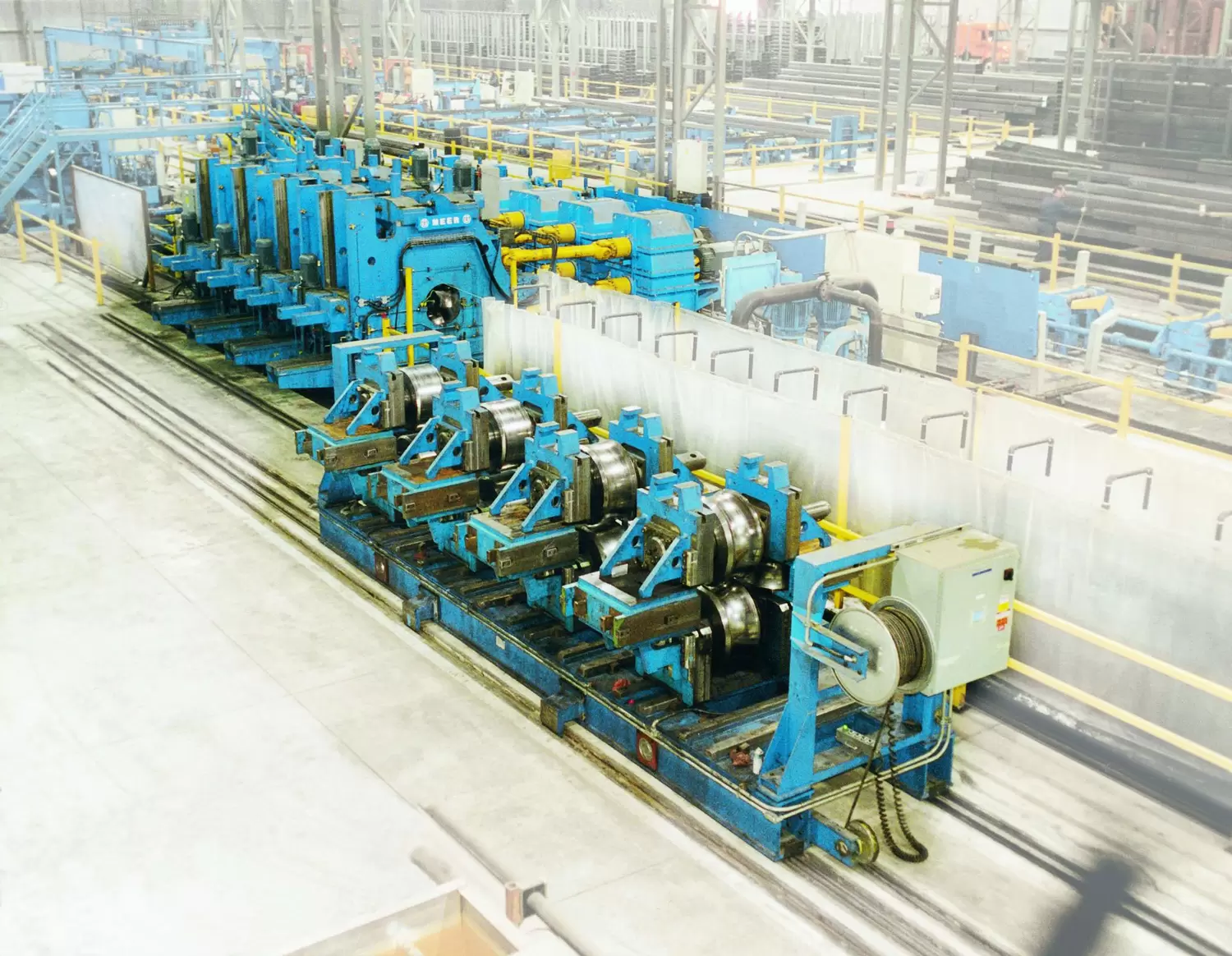