The 2015 Paris Agreement of the United Nations Framework Convention on Climate Change (UNFCCC) calls for limiting the global temperature increase to 1.5°C. This international agreement requires governments worldwide to drive forward decarbonization of all sectors of the economy. The aim is to reduce CO2 emissions and achieve net zero emissions by 2050.
Even though the legislative process will take some time, steel producers need to start preparing and becoming aware of green technologies. Any strategy to decarbonize reheating has to consider the related process up- and downstream of the rolling mill. Additionally, the local availability of fuels also guides the selection of the best available technology and lowest risk strategy for the reheating furnace. As part of its vision of turning metals green, SMS group is adopting a holistic approach to the entire plant.
SMS group tackles emission sources in reheating furnaces
Concerning the political guidelines for the reduction of CO2 emissions the question arises as to regarding the main sources of CO2 emissions in rolling mills. In a typical hot rolling mill, the reheating furnaces account for around 80% of CO2 emission.
Of course this number varies based on the location factors from plant to plant. SMS group bundles know-how from the areas of digitalization, service, electrics, and automation as well as plant engineering to maximize sustainable plant potential and offer advisory support to customers, considering individual plant requirements to offer the best available reheating technology.
Lean or rich gases? The right burner enables the reduction of OPEX and may enable the transition to a hydrogen economy
The possibility to decarbonize the reheating furnace depends mainly on the upstream process. For instance, if the rolling mill is part of an integrated steel-making plant, lean gases – by-products like blast furnace gas (BFG) or basic oxygen furnace gas (BOFG) – may be accessible and can replace natural gas as fuel. If so, utilizing these gases in the reheating furnace can prove to be a cost-effective and efficient solution for reducing operational costs and the overall carbon footprint of the mill.
SMS group offers two lateral burner product families with additional configurations designed for a wide range of locally available fuels.
- The SMS ECOFlame+ family is suitable for multiple lean gases, from the lowest heating value such as blast furnace gas (BFG) to the highest such as natural gas (NG) or propane.
-
The SMS ZEROFlame family is suitable for use with rich gases, such as coke oven gas (COG) and natural gas (NG).
After assessing the local fuel infrastructure of a specific plant, the best available technology is chosen, considering potential future scenarios. This includes the option of operating with a gas and hydrogen blend, even up to 100%. This not only provides an alternative in case of a future fossil fuel shortage but also serves as a transitional solution towards a hydrogen-based economy, allowing the gradual introduction of H2 into the fuel mix at different percentages. SMS group offers a comprehensive combustion system, ensuring maximum fuel flexibility without compromising the technical performance of the furnace.
From lean gases to hydrogen with the SMS ECOFlame+ family
The SMS ECOFlame+ burner family is a single-fuel burner operating in flame mode suitable for any kind of plant. In its standard configuration, the burner features a single fuel and a double air inlet. It can operate with a variety of gases, from the poorest in terms of lower heating value (LHV) such as BFG to the richest like natural gas or propane. By utilizing lean gases, such as blast furnace gas (BFG) generated as a by-product of the steel production process, in the reheating furnace area, the need for additional natural gas (NG) is minimized. The mill’s carbon footprint can therefore be reduced. The triple air staging ensures a well-diluted flame pattern, guaranteeing low NOx emissions regardless of the type of gas used. In addition to the standard version, the SMS ECOFlame+ is also available in the Hydrogen Hybrid HY2, Dual, and Regen configurations. For instance, the Dual configuration allows the mixing of various fuels at the burner according to the heat requirement of the respective combustion control zone. This configuration enables the maximization of the exploitation of lean gas utilization, thereby reducing operational costs. To further facilitate the transition to a hydrogen economy the SMS ECOFlame+ can be equipped with a Hydrogen Hybrid HY2 configuration, which is already capable of utilizing up to 100% hydrogen.
Going flameless and hydrogen with the SMS ZEROFlame family
If the local fuel infrastructure can provide rich gases, such as coke oven gas (COG) and natural gas (NG), the flexible SMS ZEROFlame burner family is an excellent choice. This burner family ensures optimal combustion control, energy efficiency, and high flexibility in the choice of flameless, flame, and booster modes, consistently delivering exceptional performance with well-defined flame patterns and extremely low NOx emissions. Additionally, the SMS ZEROFlame, aside from the standard version is also available in the Hydrogen Hybrid HY2, Dual Flame, and Regen configurations. The Hydrogen Hybrid HY2 configuration can operate with up to 100% hydrogen in the fuel mixture, maintaining extremely low NOx emissions even with hydrogen use. This multi-fuel flexibility enables customers a gradual transition to a hydrogen economy and effectively managing uncertainties in hydrogen availability.
Going green with flame or flameless mode? The NOx emissions make the difference
One of the main differences between the two lateral burner families from SMS group is that the SMS ECOFlame+ family can operate in modulating mode or with the level 1 automation system X-Pact® DigiMod Control, thanks to its wide turn-down ratio. On the contrary, the SMS ZEROFlame family is specifically designed for flameless combustion, resulting in a narrower turn-down ratio and requiring digital control, such as the X-Pact® DigiMod Control.
Flameless combustion contributes to a more consistent temperature field in the furnace chamber due to robust flue gas recirculation and the absence of a stable front flame. Both burners can incorporate hydrogen in the fuel blend. The addition of hydrogen mildly affects NOx emissions when the burners operate in flame mode, while this effect is negligible in flameless operation. Despite this divergence, the SMS ECOFlame+ family serves as a promising initial step toward decarbonization and compliance with the 2030 emission regulations, stated in the Fit for 55 package.
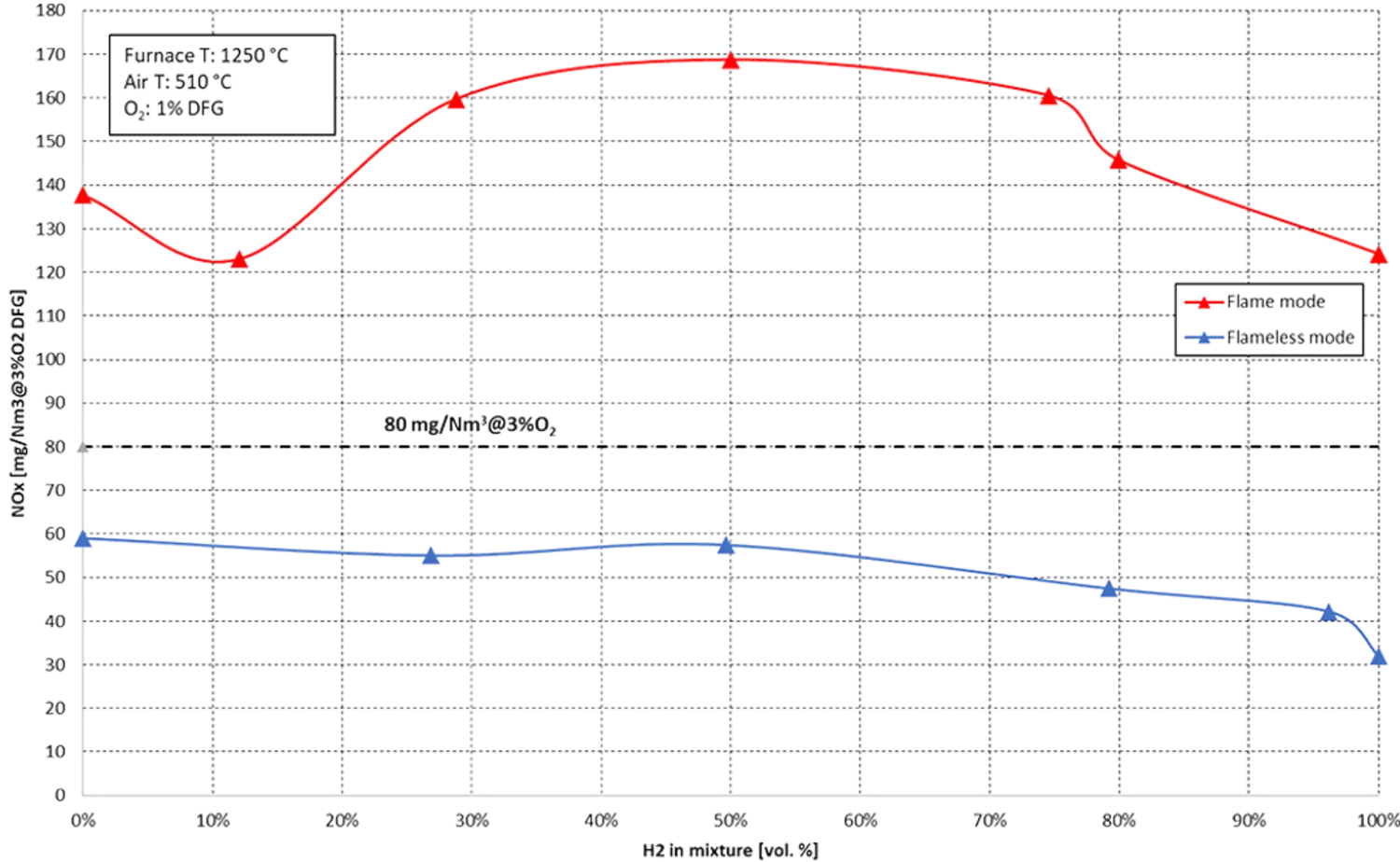
Rich or lean gases? – The best of both burners with SMS ZEROFlame with Dual configuration
The SMS ZEROFlame equipped with the Dual configuration seamlessly integrates the flexibility of dual-fuel technology with the benefits of flameless technology. It is the new best available technology of SMS group for the use of flameless operation in combination with lean gases. Thanks to its innovative design, the lean gas (BFG, BOFG, syngas, etc.) is burned by a special central lance in flame mode, while the rich gases (NG, COG, hydrogen) can be injected either in flame mode or in flameless mode. With this configuration, SMS customers can exploit all the energy coming from the lean gases and have all the exceptional performances of SMS ZEROFlame technology.
Multi-fuel capability increases flexibility, but combustion optimization is key
Tailor-made combustion system design and careful burner selection are a prerequisite for reducing the fuel consumption and carbon footprint of the reheating furnace. Combustion control systems play also a crucial role in this respect to optimize the fuel consumption in the reheating furnace area. SMS group’s level 1 automation system X-Pact® DigiMod Control and level 2 optimization system X-Pact® Prometheus are the tools that can guarantee the best performances in terms of stock heating quality and fuel saving.
The X-Pact® DigiMod Control integrates the modulating control of the combustion control zones with the digital control for each burner ensuring the right flame pattern and furnace thermal profile under various working condition.
The X-Pact® Prometheus functions as an online computational process model, providing real-time simulation of the stock's temperature profile. It compares this with the theoretical heating curve and automatically adjusts furnace temperature set points. This combustion optimization system aims to achieve the desired temperature profile and uniformity for any stock and steel grade with minimum fuel consumption, decarburization, and scale losses. X-Pact® Prometheus can adapt the heating curves based on the stock charging temperature optimizing the process also during the furnace mixed charge. X-Pact® Prometheus has complete reporting to trace the heating history of processed stock and advanced functionality for managing planned or unplanned mill stoppages.
Decarbonizing an entire rolling mill goes beyond reheating furnaces
Various reheating technologies are available to meet the political guidelines of the Paris Climate Agreement. SMS group, serving as an advisory consultant, considers all the plant peculiarities to define a tailor-made solution.
As the measures for CO2 reduction in rolling mills also go beyond the reheating furnaces, SMS group adopts a holistic consulting approach. In this regard, SMS group provides solutions that are tailored to the plants, processes, and individual emission sources.
Feel free to reach out to us and we will collaborate with you and our experts to develop tailor-made solutions that encompass the entire plant. Through an integrated and partnership-based approach, we aim to support your plant effectively and sustainably throughout its entire lifecycle.