Kimihiko Nakamura, General Manager at the International Machinery Department Itochu-Machine Technos Corp., speaks of TCG43 as the best machine for the production of premium joints that require a much higher quality of the high-alloy material compared to API.
TCG43 is the best machine.
“The reason why a major Japanese pipe producer introduced a second TCG43 threading machine is that they recognize the key to produce the premium joint in a constant quality and fast cycle time – which requires the high rigidity to bear the counter force from the cutting tool. This has been proven through the repeated cutting test before the Japanese pipe producer decided to introduce the first TCG43. TCG43 is the best machine that can realize the above mentioned requirement for producing this Japanese pipe producer’s premium joint which require much higher quality in high alloy material compared to API.”
Thread cutting machines of the TCG type operate according to the principle “rotating tube, stationary tool“, producing high-precision premium threads for seamless tubes and longitudinally welded pipes. Premium threads produced on thread cutting machines of SMS group meet the demanding standards according to ISO 13679: 2019 / 2011 and API 5C5 and in addition to that attain outstanding results for threads to API 5B and GOST R 53366 (formerly GOST 631/632/633).
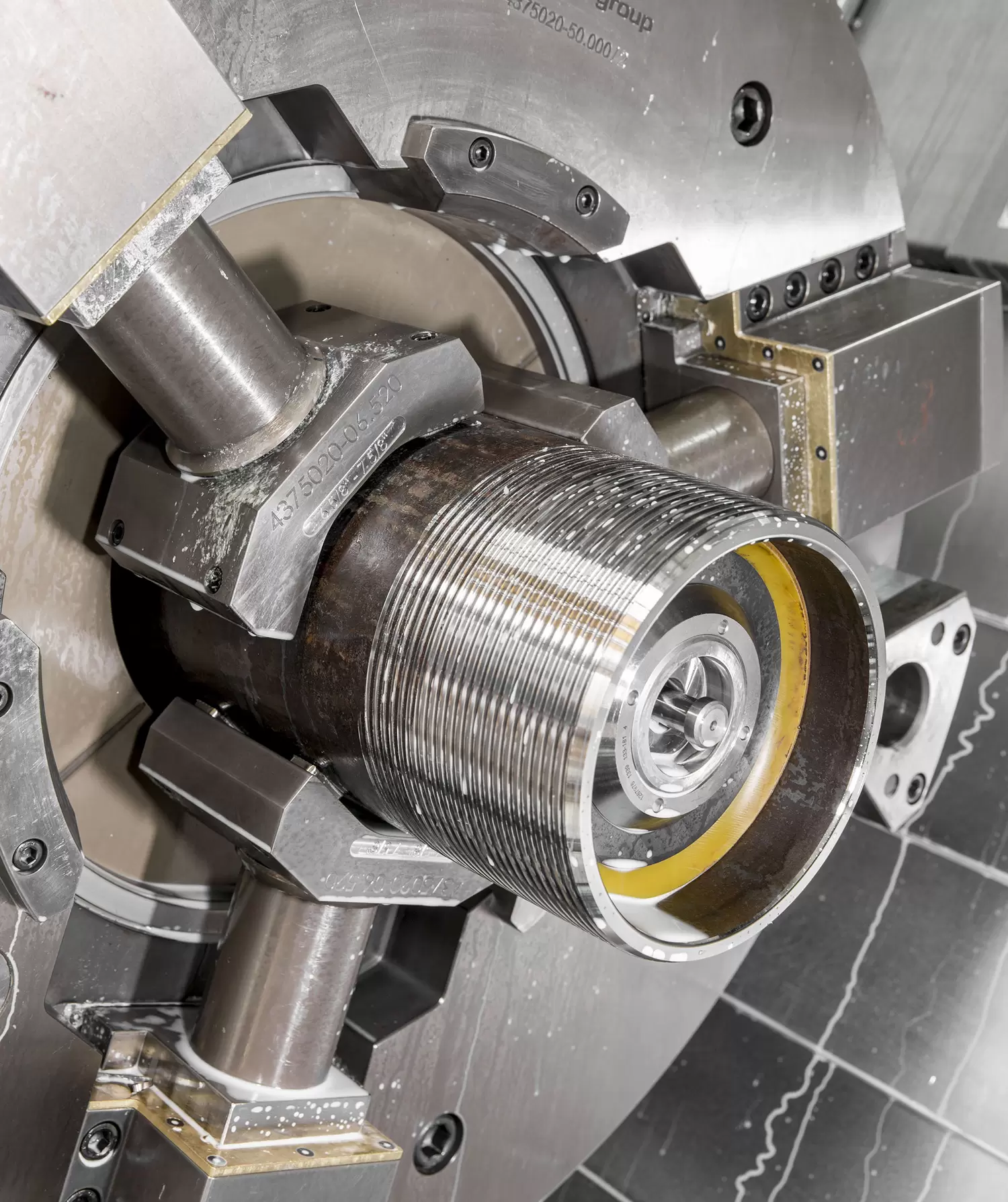
Why are premium threads decisive in the future?
The conditions of oil production are becoming more and more ambitious; safety and rigidity of the pipes and particularly their connections must be assured. Only with premium threads of the highest ISO standards as produced on the TCG thread cutting machines from SMS group can the varied and complex requirements be fulfilled and and the oil deposits be safely tapped.
With premium threads OCTG (oil country tubular goods) pipes are prepared for the most demanding oil extraction conditions. This includes that oil drilling with these high-performance pipes is able to penetrate into further depths of several thousand meters onshore as well as offshore.
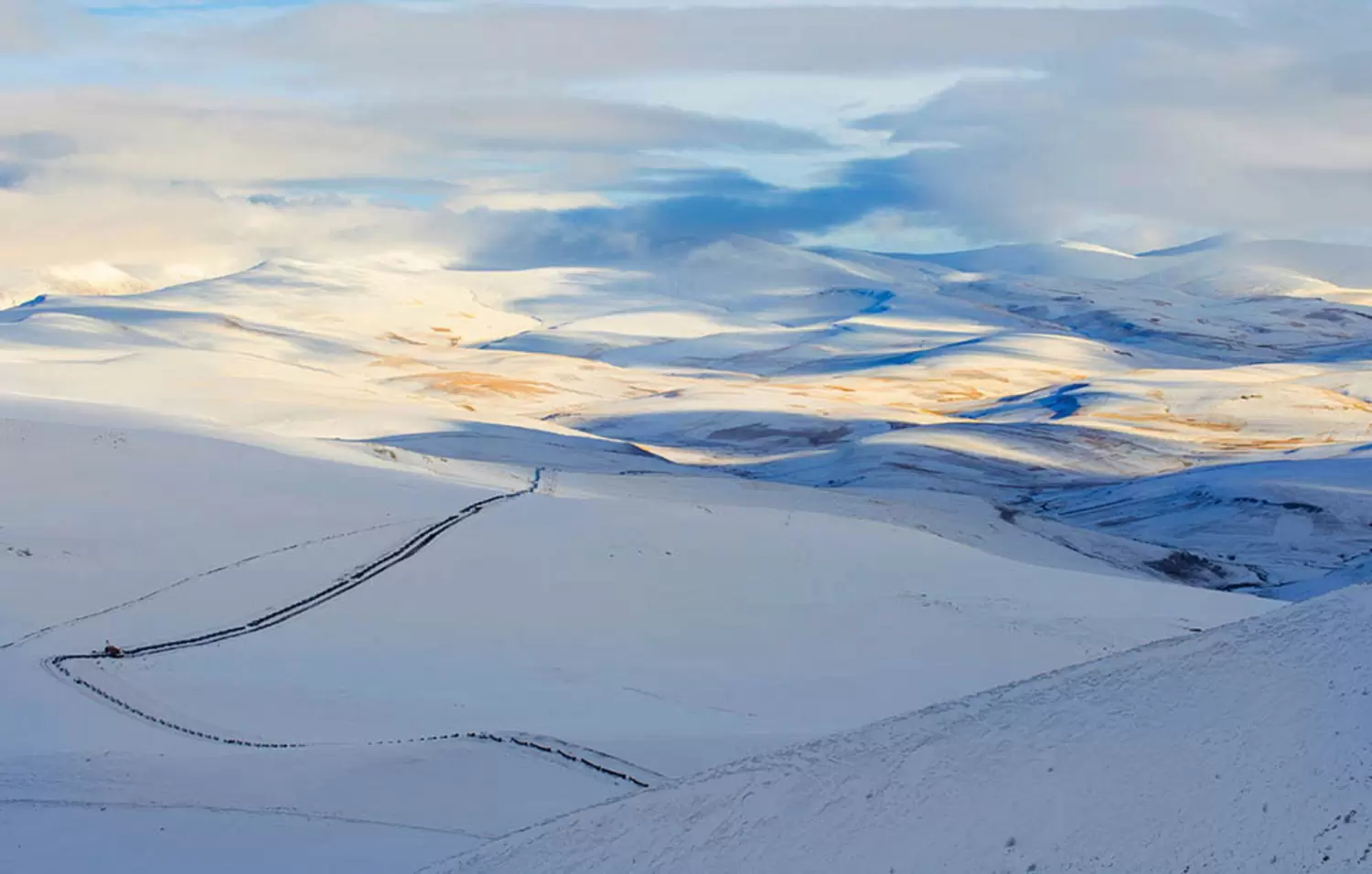
So-called sour service pipes with premium threads withstand aggressive and corrosive conditions such as hydrogen sulfide and sulfuric acid. Large deposits near the polar circle can only be explored since the high-strength and highly alloyed pipes including their threads withstand extreme temperature differences.
In the offshore area near oil platforms premium threads help to ensure that oil extraction pipes permanently withstand high movements. And mining operations not only take place vertically, but change directions for geological reasons – even these enormous challenges are managed by OCTG pipes and premium threads.
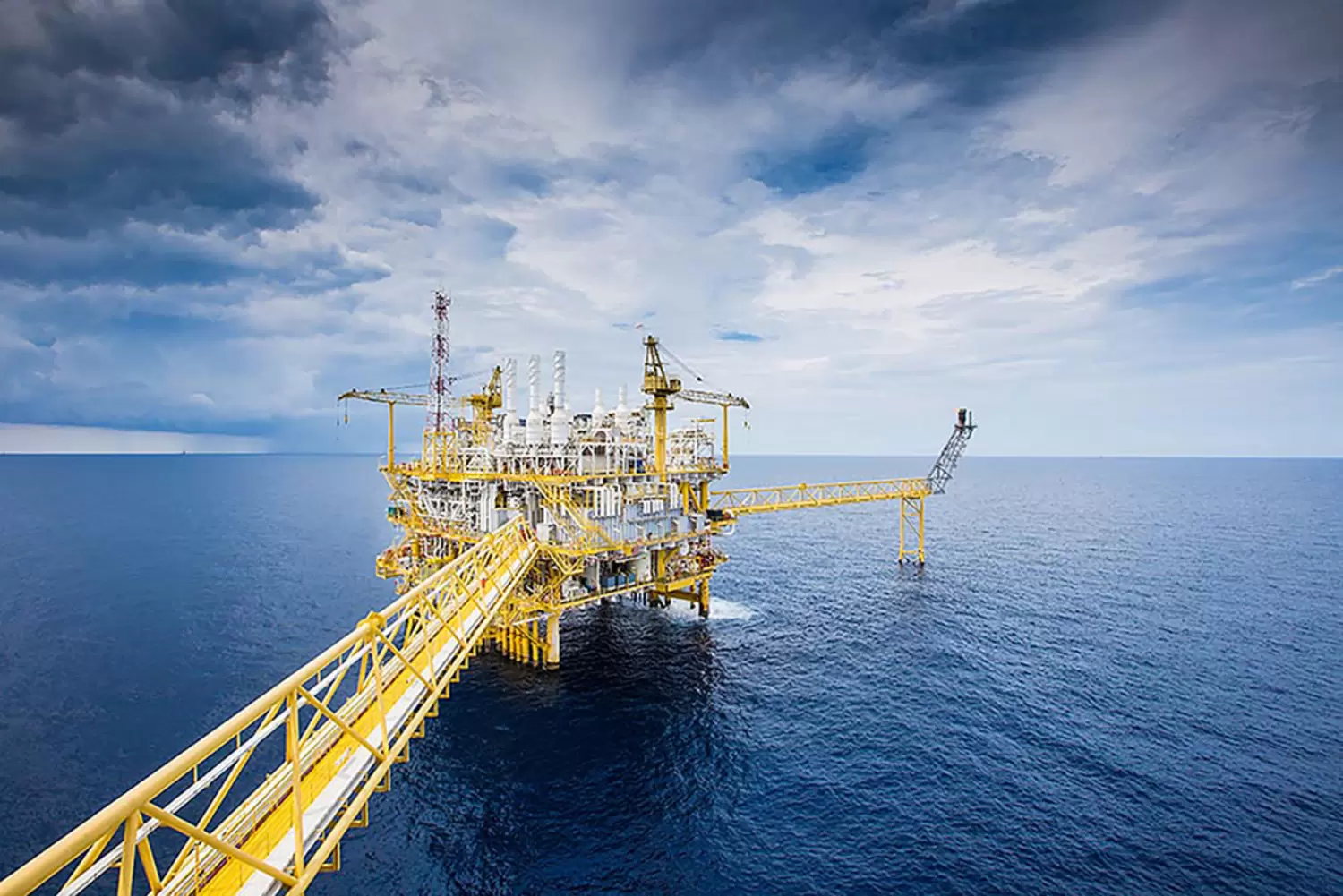
How does SMS group achieve this unique thread precision?
“Significant for precision and quality are machine rigidity and vibration reduction“, Tim Küppers, Head of Design Department Finishing Lines, SMS group, explains. “We have subjected all components of a thread cutting machine to continual testing which has resulted in new developments. In conclusion, they are interacting optimally and are gaining optimum thread results.”
In the development, SMS group has applied state-of-the-art FEM simulations. By means of finite element calculations structural components such as machine frame, gear units, turret arrangement and drive elements with linear guides and preloaded ball screws were examined and optimized. The results were then again subjected to an objective and independent examination and then confirmed by the RWTH Aachen University: the TCG thread cutting machine attains supreme values in machine rigidity and vibration-free running.
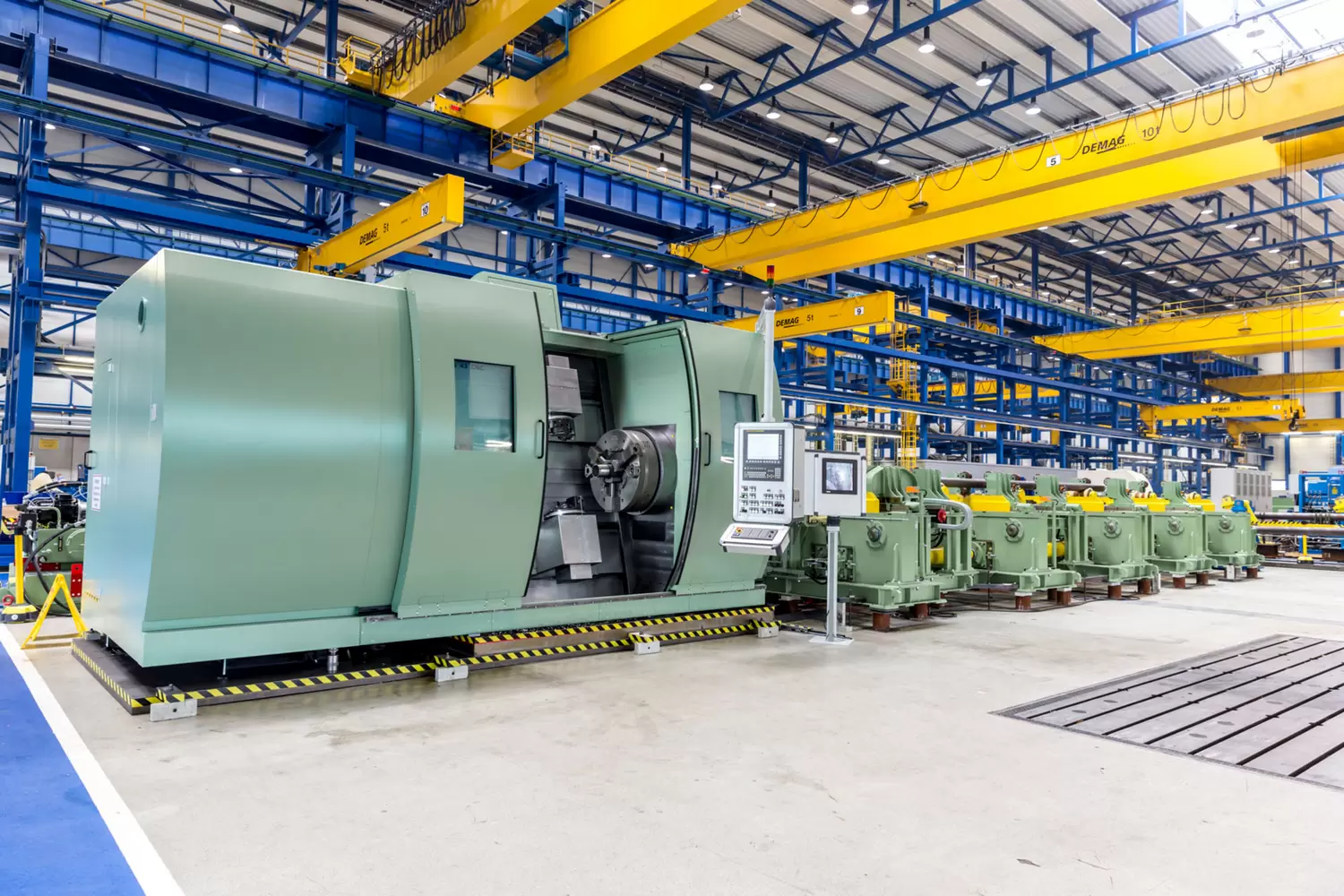
Key factors of precision and main innovations include the positioning of the turret (tool holder) with its short distances to the pipe and vertical arrangement to the machine axis as well as a separate, self-supporting centering chuck. With this construction the excess pipe length for clamping can be kept as short and stable as possible, whereby also welded thin-walled OCTG pipes can be processed in a highly precise manner.
In addition, the pipes can be optionally stabilized by using an internal clamping device. The newly developed chuck is characterized by its compactness, low inertia and flexibility, enabling to pick up each pipe optimally. Turret tools not required during the thread cutting process cannot collide with the clamping chuck. In this way, the pipe can be clamped as short as possible and the tendency to vibrate can thus be minimized.
“Furthermore, high pressure coolant system and specially designed tool blocks work for better chip flow (long chip), CNC operated mandrel/plug avoid the inclusion of cooling into the pipe very well, and the pipe centering accuracy is secured very well with the centering chuck + floating/rigid chuck, which support the continuous operation without intervention. We believe, this major Japanese pipe producer is happy to work with this sophisticated threading machine.“ said Kimihiko Nakamura, General Manager with the International Machinery Department Itochu-Machine Technos Corp.
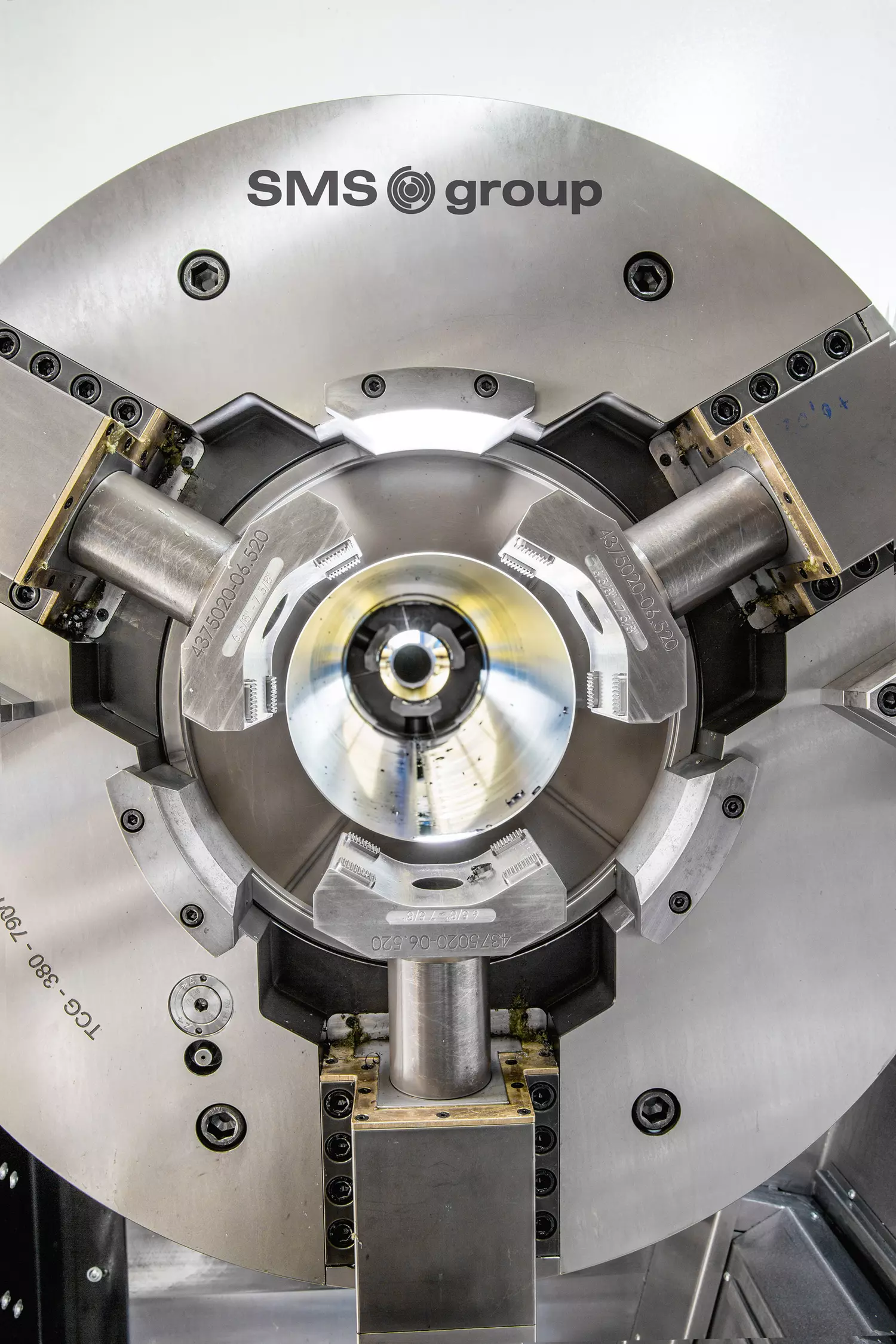
What are the characteristics of high productivity and availability?
Short cycle times and high productivity are made possible by the fully automated processes. This already begins with the transportation systems in front of the machine center. Special pinch roll units ensure fast pipe feeding. By tracking the machine knows among others values such as pipe dimensions and steel grades. Based on this data, the dynamic adaptation takes place automatically and secondary setup times are reduced to a minimum.
Each of the two turret heads is equipped with six tools so that the machine is provided with a total of twelve tool positions. Consequently, the machine is prepared for corresponding material properties such as highly alloyed steels and machining processes such as roughing, finishing or thread cutting. As a result, the production processes can be carried out in an interruption-free and highly productive way. Pre-positioned tools enable the production of most varied thread types and are provided with a powerful coolant application so that maximum process speeds can be realized. Coolants are collected, cleaned and once again fed to the production cycle which in addition to energy efficiency contributes to the sustainability of the thread cutter.
To avoid downtimes, all sensitive machine parts such as tool carriages are protected against direct impact of chips or cooling emulsion. The pipe is protected with a plug internally fitted fully automatically and variably depending on pipe and thread. In addition to that, the whole interior space is provided with smooth surfaces ensuring that adhesion of chips is prevented. Continuous chip removal is realized fully automatically. A chip extraction system can be installed additionally.
An automatic lubrication system also contributes to high availability and minimization of maintenance assignments. Moreover, an up-to-date plant design enables optimum accessibility of all assemblies. The machine equipped with integrated access and security systems provides wide sliding doors with roof opening, whereby production staff is not affected by dripping coolants and crane application is simplified when assembly groups are replaced.
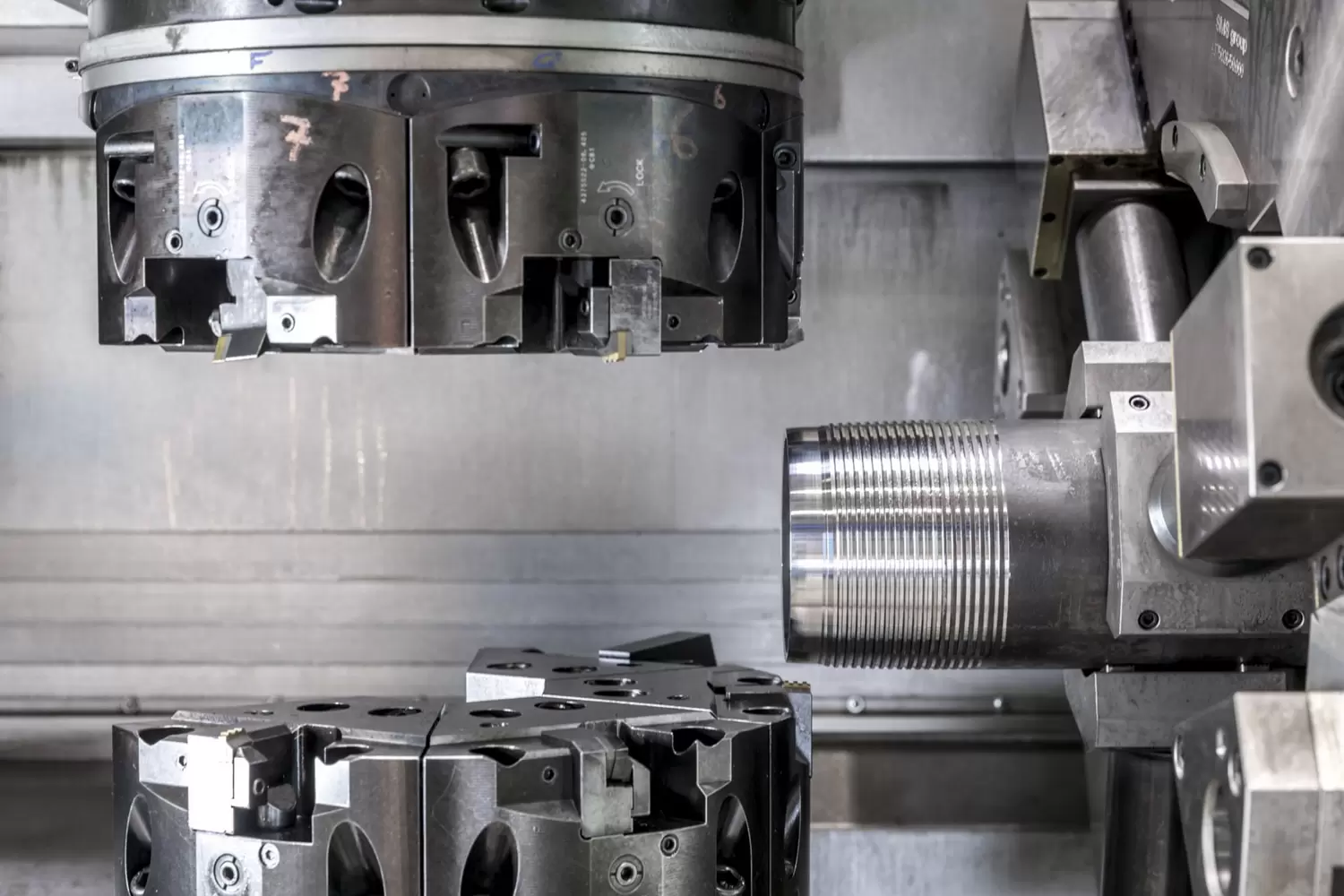
What are the prospects for customers in terms of digitalization and Industrie 4.0?
As regards controls, digitalization and Industrie 4.0, the TCG thread cutting machines are designed to be open – i.e. with their interface approach as well as an integrated sensor technology. For CNC machine control e.g. Siemens or FANUC systems can be used depending on customer specifications. The HMI operating concept is designed intuitively offering maximum transparency for monitoring fully automatic processes and simple, quick intervention and adjustment options.
Christian Benten, Sales Manager Finishing Lines, SMS group: “Our equipment can be integrated seamlessly into existing ERP systems and pipe finishing lines and it supports the corresponding pipe tracking. Through this connectivity and networking the machine is perfectly pre-adjusted to the relevant pipe in the ongoing process. At the same time, the process and thread data are provided for downstream production steps and are integrated in the quality documentation of the customer.
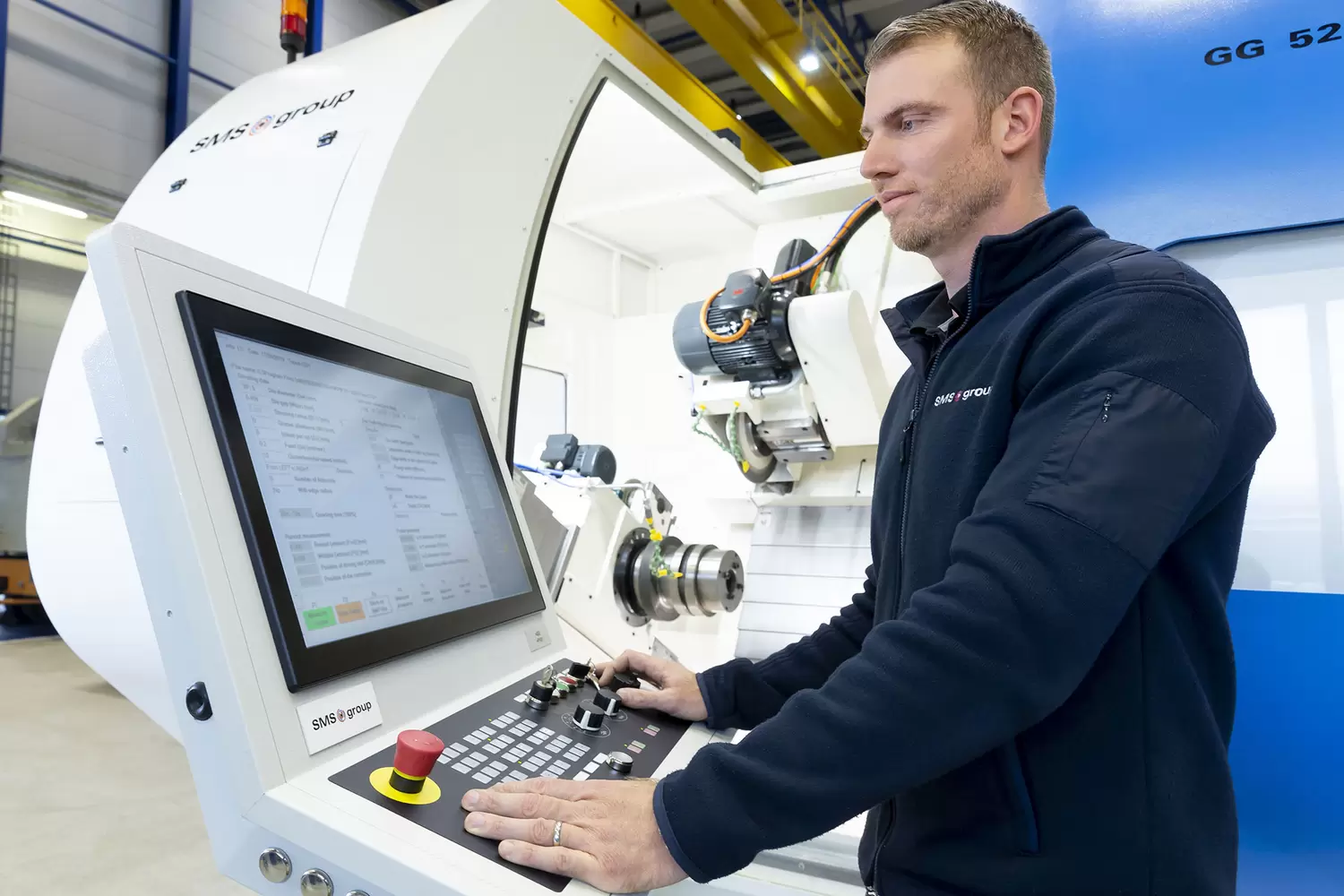
“We have optimally prepared the TCG thread cutting machines for the digital future. We are working on very promising digital and intelligent solutions which further enhance the added value of TCG thread cutting machines for the customers,“ Falk Rößeler, Vice President Bright Steel & Finishing Plants, SMS group, forecasts future prospects of the new machine type.