The thin-gauge toolbox is hot
Rolling thin-gauge hot strip presents both opportunities and challenges. Higher prices are paid for thin strip dimensions due to the increased challenges and risks associated with their processing. Disruptive cobbles, unscheduled roll changes, and downtimes are a significant concern.
To address these challenges, SMS group offers mechanical and automation packages as part of a “toolbox” for improving process stability in hot strip mills. The toolbox includes fast mechanical actuators and control elements, mechatronic packages and sophisticated process models, well-designed strip-guiding systems, and advanced strip steering control modules to ensure straight transfer bars and stable thin-strip rolling.
Rolling low-carbon thin-gauge strips at high speeds within the austenitic temperature range brings with it metallurgical and process challenges. The use of a coilbox helps to maintain a nearly constant strip temperature during rolling, whereas without a coilbox, temperature losses at the strip end require process acceleration to reach the final rolling temperature. The SMS coilbox provides a heat balance above the transformation temperature, ensuring consistent mechanical properties of thinner gauges. To mitigate temperature losses, HIBOX heat insulation hoods can be used. By implementing hold-down blowers and narrow-pitch roller tables, the demand for high process speeds is taken into consideration. Sophisticated and holistic process models for temperature, profile, contour, and flatness, as well as advanced control systems for thickness and mass-flow, help stabilize the rolling behavior and enable the production of thinner strips or higher-strength steel grades.

Steering malfunctions can cause ripped tail ends, which occur when the strip moves off center, turns, and is rolled double thick or with breaks. SMS group’s X-Roll® Guide System ensures a straight and wedge-free transfer bar and improves control in the finishing mill area. The system includes roll alignment control strategies, side guiding mechanical equipment, and camera-based measuring systems for real-time feedback on the strip position. X-Pact® Centerline Control offers integrated strip guidance and is crucial for the stability of the rolling process, especially for high-value thin-gauge and high-strength materials. It reduces the number of unplanned roll changes and supports the operator by suitable visualization.
For strip center measurement, the system uses X-Pact® Sense hotCAM designed against harsh environmental conditions like high strip temperature, fog, steam, dust, and vibrations. X-Pact® Centerline Control uses a closed-loop algorithm to calculate the strip center line deviation and provides a levelling correction signal for the mill stands. A smooth transition between the control actions in the different phases is ensured. These advancements help to make the rolling process fully automatic and improve rolling stability throughout the hot strip mill.
The new X-Roll® Guide system is the next step towards digitalization and is aimed at achieving a fully automatic rolling process. It embodies our holistic approach to improving hot strip mill rolling stability in all relevant stages of the process. This comprises:
- Roughing mill: X-Roll® Guide for camber-free rolling of perfectly straight transfer bars with minimal wedges
- Finishing mill entry: X-Roll® Guide with finishing mill entry arrangement for stabilizing the rolling process
- Finishing mill area: X-Roll® Guide for stable threading and tail-out
- Downcoiler area: X-Roll® Guide coiler for straight coils with minimum telescopicity.
All X-Roll® Guide systems can be understood as performance modules combining reliable mechanical actuators, sensors, and automation systems with appropriate control loops and tracking functions. These mechatronic systems are controlled and adapted with corresponding measuring devices. They can be integrated in an existing rolling plant as a whole unit or in packages. Each module comes with specific advantages and helps to increase the rolling stability and yield of a hot strip mill.
Handling with care – thin-gauge rolling in a tandem cold mill
Producing strip with a final thickness of below 0.25 mm is a demanding task for a fully continuous pickling line and tandem cold mill (PL -TCM). The challenges of the continuous process include avoiding frequent strip breaks as well as taking into account the higher demands with regard to production planning and process control and the increased maintenance involved.
SMS group recently implemented two PL -TCMs in Asia. The five-stand arrangement with hydraulic screwdown system provides the necessary reduction capacity in order to achieve a final thickness of 0.16 and 0.18 mm as well as the desired production volume. The 6-high stands ensure perfect flatness control independent of incoming hot strip profiles. The equipment includes CVC® plus systems on intermediate rolls, work rolls, and positive/negative bending systems for the intermediate rolls. The last stand features a multi-zone cooling system. Both mills (maximum strip width 1,350 mm and 1,560 mm) are capable of rolling at 1,800 meter per minute.
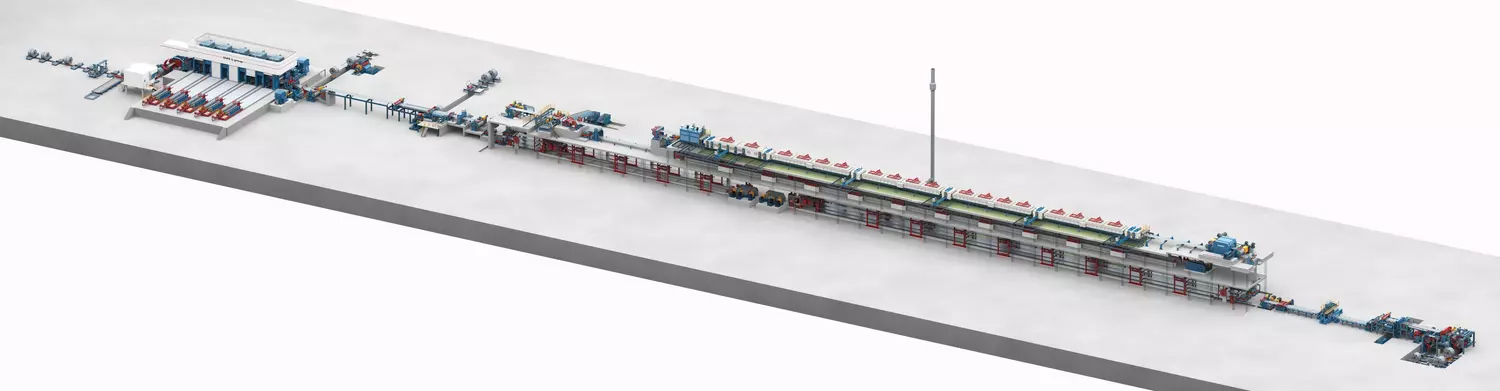
Challenges and solutions
The main challenges in rolling thin gauges are avoiding strip breakage, ensuring fast rolling speeds, and maintaining the reproducibility of rolling conditions. Essentially, these are guaranteed by reliable mechanical equipment, automation systems for smooth operation with almost no operator intervention, perfect mass flow and flatness control, precise adjustment of the draft distribution and emulsion parameters, special handling provisions for thin strip in automation mode, as well as high-level maintenance and process knowledge.
The skills and competencies required to operate a PL-TCM for such applications include ongoing operator training, a particular focus on equipment maintenance, and ensuring stable work roll quality with roll grinding procedures. Design aspects such as achievable flatness results, cooling systems, and emulsion system stability to keep the work roll and strip temperature within set limits are important too. The careful selection of measurement devices is also relevant in this context.
Regarding process automation, SMS group’s widely proven X-Pact® automation solutions with powerful level 2 process models are imperative when rolling thin-gauge strip. It must at least include X-Pact® Pass Schedule Calculation for the generation of optimal set points and X-Pact® Profile, Contour and Flatness Control for the CVC® plus system and the bending system. Final strip flatness control is assured through the interaction of the reliable and precise X-Shape Flatness Measurement roll and control equipment in the mill. With CVC® plus, bending and multi-zone cooling is dynamically controlled based on the measured shape. When rolling thin gauges, the interstand flatness plays a more important role in the rolling process. Excessively high edge tension, in particular, can cause strip breaks. The technological models calculate the setup values for the actuators together with the parameters for acting on dynamic disturbances, such as roll force variations, and ensure the requested flatness in the mill. All this emphasizes the role of automation in dealing with sensors and actuators, providing for perfect thickness and mass flow control, and the specialized strategy for handling thin strips during transfer to the tension reel.
The technological tasks involved in rolling thin strips at high speed focus on the adaptation of the emulsion conditions, roll roughness, and tensions. The characteristics of the emulsion used and the influence of various parameters have to be considered. Establishing a stable working point and addressing chatter issues is also essential. If all these measures are implemented, strips with a thickness of under 0.25 mm can be handled with special care and the highest yield levels can be maintained.