With the new 28-inch ERW welded tube plant, Zekelman Industries will be able to produce more than 400,000 tons per year while expanding its product portfolio to include 28-inch tubes. After pre-assembly in Germany, the plant went on its journey to Blytheville (Arkansas) in early January. The COVID-19 pandemic and the resulting travel restrictions and quarantine arrangements posed an additional challenge. This meant that during the loading processes, the project team could only be on site with a reduced number of employees – and beyond that, relied on local support.
From Lebach to Saarlouis/Dillingen port, Germany (January 2021)
The first stage of the impressive transport starts in Lebach (Germany). Enormous weights totaling more than 500 t and dimensions of up to nine meters are about start their journey to the USA. Due to the very high degree of pre-assembly, the plant components could only be transported upright. Facing a tight schedule, the project team had decided in favor of this high degree of pre-assembly in order to reduce the time required for assembly and installation on site. However, this made transport considerably more challenging and cost-intensive. Conventional resources available on site, such as bay cranes or hydraulic pumps, could not be used – instead, special equipment was required.
Safely packed and loaded, the goods weighing between 190 t and 230 t were transported to the Saarlouis/Dillingen inland port by means of 20-axle modular trailers and one tractor and one pusher each. As with every heavy load transport, permits had to be obtained from the competent authorities beforehand. In contrast to other heavy load transports, this transport was mostly carried out on waterways. Thus, the distance to be covered on the road only amounted to approximately 30 kilometers. In this way, costs incurred by, for example, having to pass through narrow towns or cities – which requires special equipment – or railway crossings with suspended overhead lines could be reduced to a minimum.
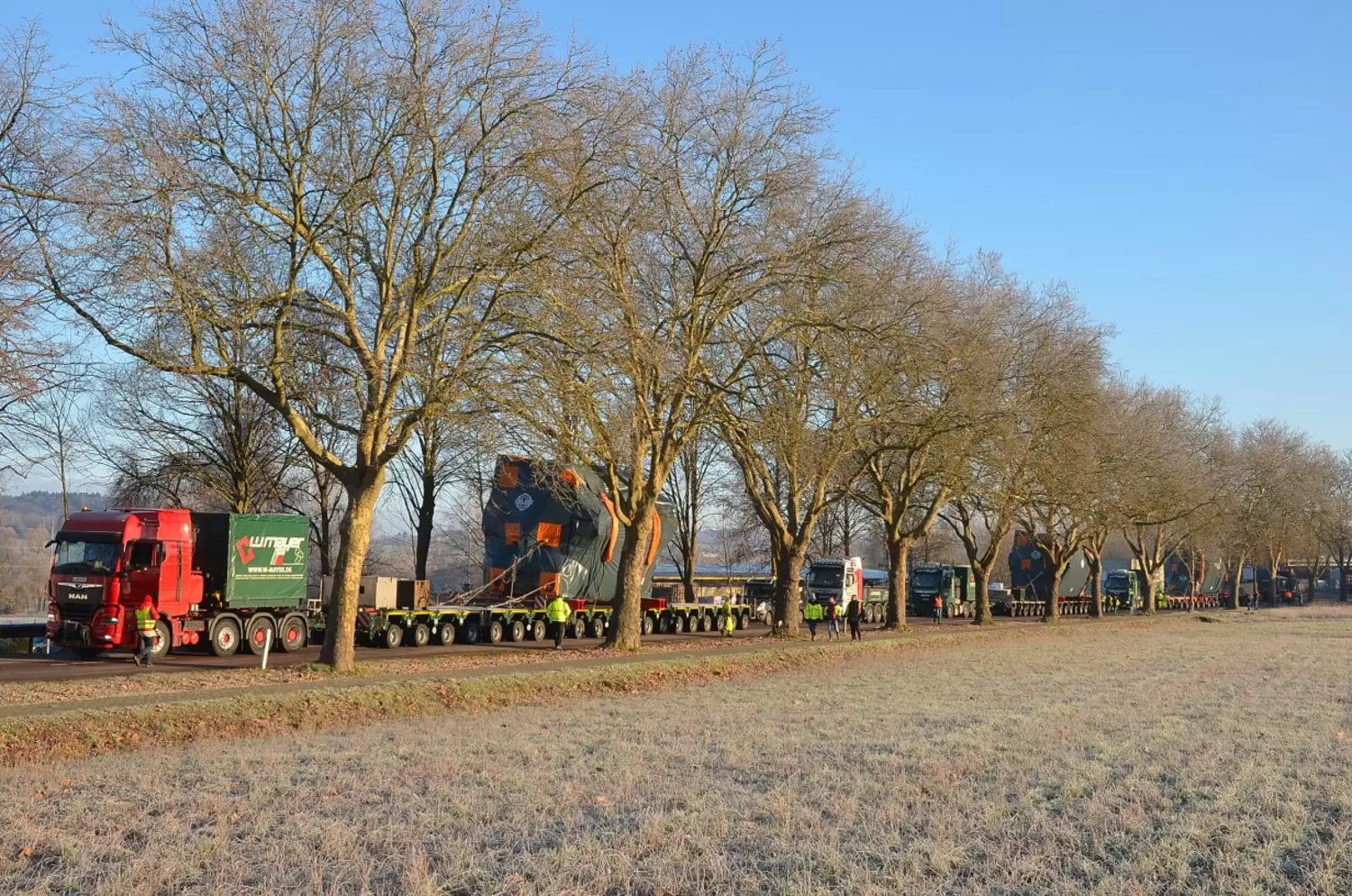
On inland vessel to Antwerp, Belgium (January 2021)
At the German inland port of Saarlouis/Dillingen, the parts were then loaded onto an inland vessel by means of two 500 t mobile cranes. After a journey of almost 5 days, the transport arrived at the port of Antwerp. There, the components were loaded onto a seagoing vessel by means of two mobile harbor cranes and then continued their 8,000 km journey to North America by sea.
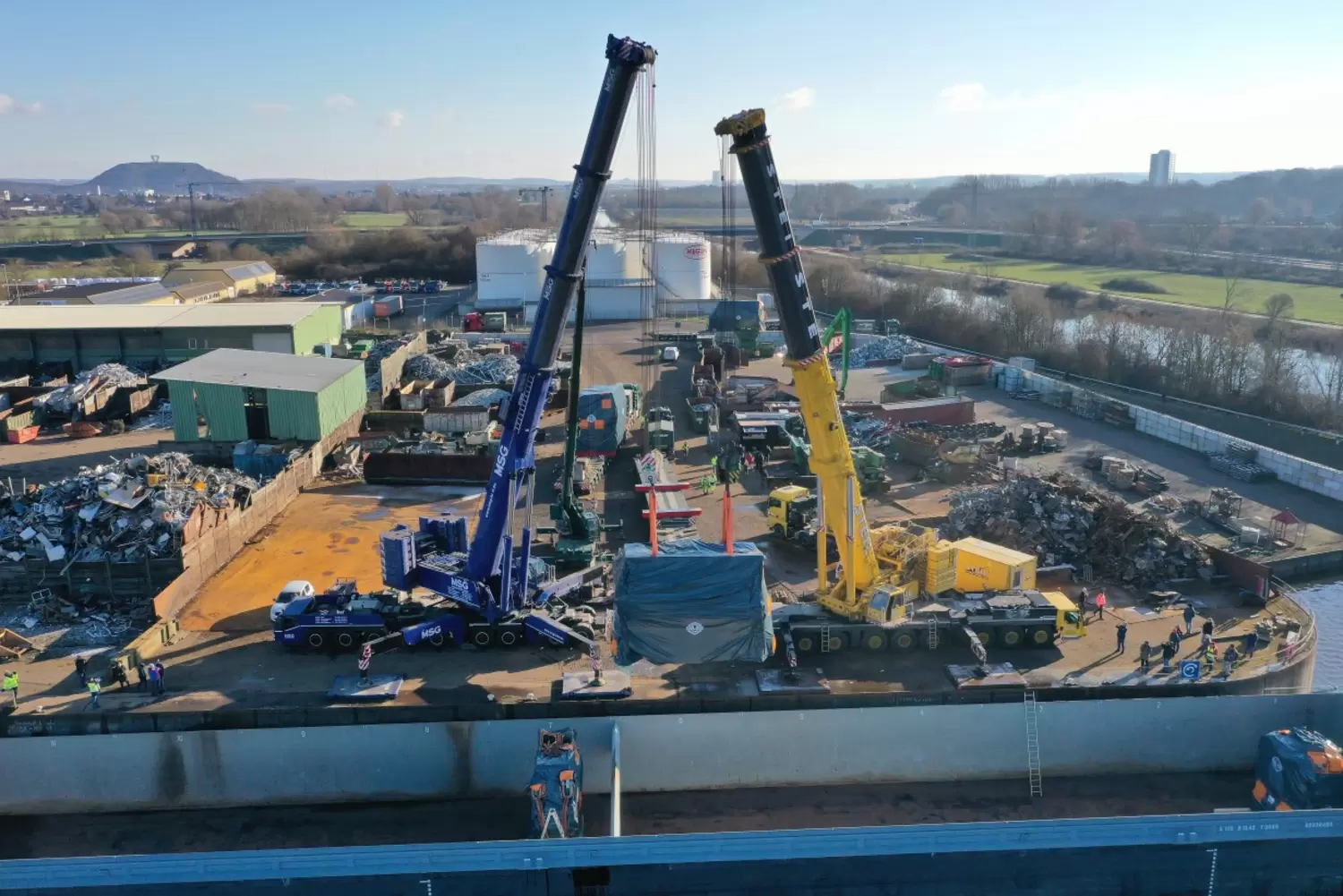
From Europe to New Orleans, USA (January/February 2021)
The journey across the Atlantic to New Orleans took 32 days. Arriving at the seaport of New Orleans (Louisiana), the components were loaded onto a deck barge by a 1,000 t floating crane for onward transport to Blytheville (Arkansas).

On the Mississippi to Blytheville, USA (February/March 2021)
Almost 60 days after the start of their journey, the components reached the pier in Blytheville (Arkansas), USA. Due to the unusually high water level of the Mississippi River, the pier that had been selected and repeatedly checked in advance could not be used. At short notice, an alternative pier had to be used so that the components could be unloaded safely. As unloading took place at a private pier, again permits had to be obtained.
The remaining five miles between the pier and the final installation location were covered using an SPMT (self-propelled modular transporter).
Despite the exceptional situation caused by the COVID-19 pandemic, the project could be implemented. Right now, the installation of the plant is nearly completed and commissioning is already in full progress.
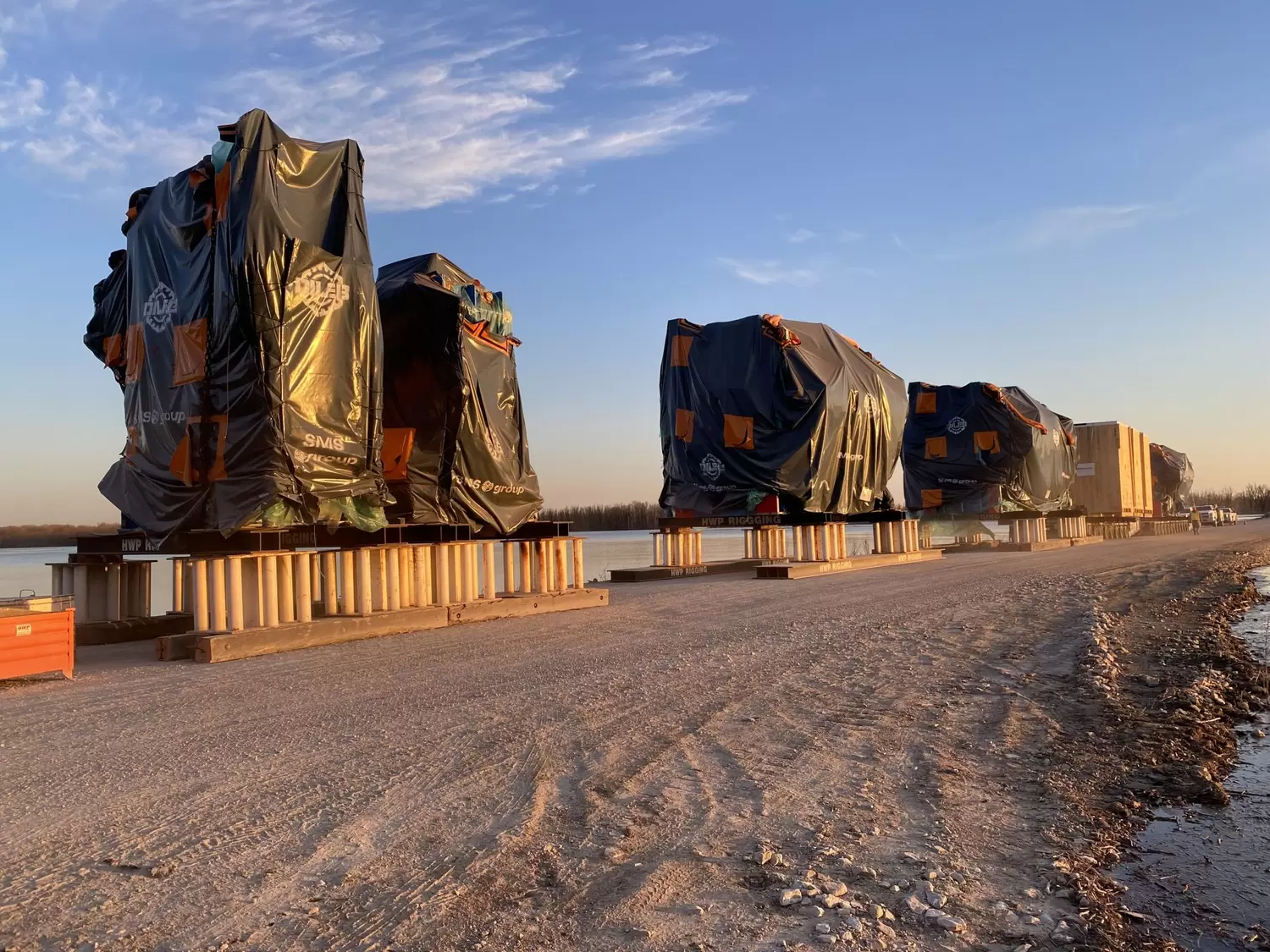