Copper possesses a number of properties that contribute to its high value and versatility, mainly heat conductivity, electrical conductivity, formability, and toughness. Without copper, there would be no use of renewable energies such as solar power. Cars could not run without copper. The weight of the copper components installed in a typical passenger car today consists of approximately 9 kg to 23 kg, which is equivalent to a half mile of copper cabling. Copper and copper alloys are utilized in electric and hybrid vehicles in even greater quantities: up to 91 kg of copper and copper alloys can be found in fully electric vehicles. The ever-growing power requirements and increasingly small dimensions of computers and smartphones would be equally inconceivable without copper’s fast signal transmission capability. It is also ideal for semiconductor chips that need ultra-thin, ultra-compact wiring.
Parallel to these developments, copper has become scarcer on the global market. Experts even see a gap emerging between copper supply and demand in the years ahead. This results in a growing call for high-quality copper from recycled material.
Great demand for high-quality copper recycling
Worldwide, around 10 million t of copper scrap is recycled every year. Due to the high value and extensive range of applications of copper, copper scrap recycling is part of the circular economy.
The advantages of secondary copper production are considerable. Recycling saves up to 85% of the energy required for primary production, which results in a reduction of approximately 2.1 t of CO2 per t of copper. Consequently, recycling copper scrap significantly conserves natural resources while lowering carbon emissions. It reduces energy consumption and minimizes environmental impact compared to mining new copper. It also provides economic benefits, cuts waste, and ensures a stable supply of high-quality copper for industrial use.
Copper scrap is categorized into various grades based on the purity and form. Common qualities include bare bright copper (Millberry), #1 copper to #3 copper, and insulated copper wire. Consequently, there are several options for recycling processes within both primary plants and secondary plants that treat only scrap material.
The quality of available copper scrap plays an essential role in determining the most efficient secondary copper processing route. The process involves collection, sorting, cleaning, shredding or baling, melting, refining, casting, and manufacturing. The smelting and refining of copper scrap is challenging due to the inherent impurities, the heterogeneity of scrap materials, and the tendency of copper to oxidize during processing. Additionally, these processes are energy-intensive, must comply with strict environmental regulations, and are influenced by fluctuating market prices. These factors collectively complicate the efficient and profitable recycling of copper scrap.
Melting, refining, and casting in one unit
For copper scrap recycling, SMS group has developed a new generation of tilting refining furnaces, enabling the production of anode copper, fire-refined, high-conductivity (FRHC) copper, or even copper granules for copper foil manufacturing.
Tilting refining furnaces (TRF) and elliptical tilting refining furnaces (ETRF) perform the task of melting, refining, and casting copper scrap in one flexible unit. By combining the tilting refining furnace with a casting wheel, high-quality anodes are produced. The type of furnace employed depends on the desired production capacity. The TRF is designed for large capacities of up to 500 t, whereas the ETRF handles capacities up to 100 t. The copper scrap is charged in the form of bales or loose scrap via the charging doors. Depending on the desired product and quality, different grades of copper scrap (grades 1 to 3, e.g., birch or cliff) can be used. The units can also be offered “H2-ready,” enabling CO2-reduced copper production.
Additional equipment such as top blown rotary converters (TBRC) or basic rotary refiners (BRR) can be added for recycling slag, lower-grade copper scrap, and e-waste. The flexibility of the TRF/ETRF process ensures that the copper quality is adequate for the partial replacement of cathodes for a fire-refined semi-product.
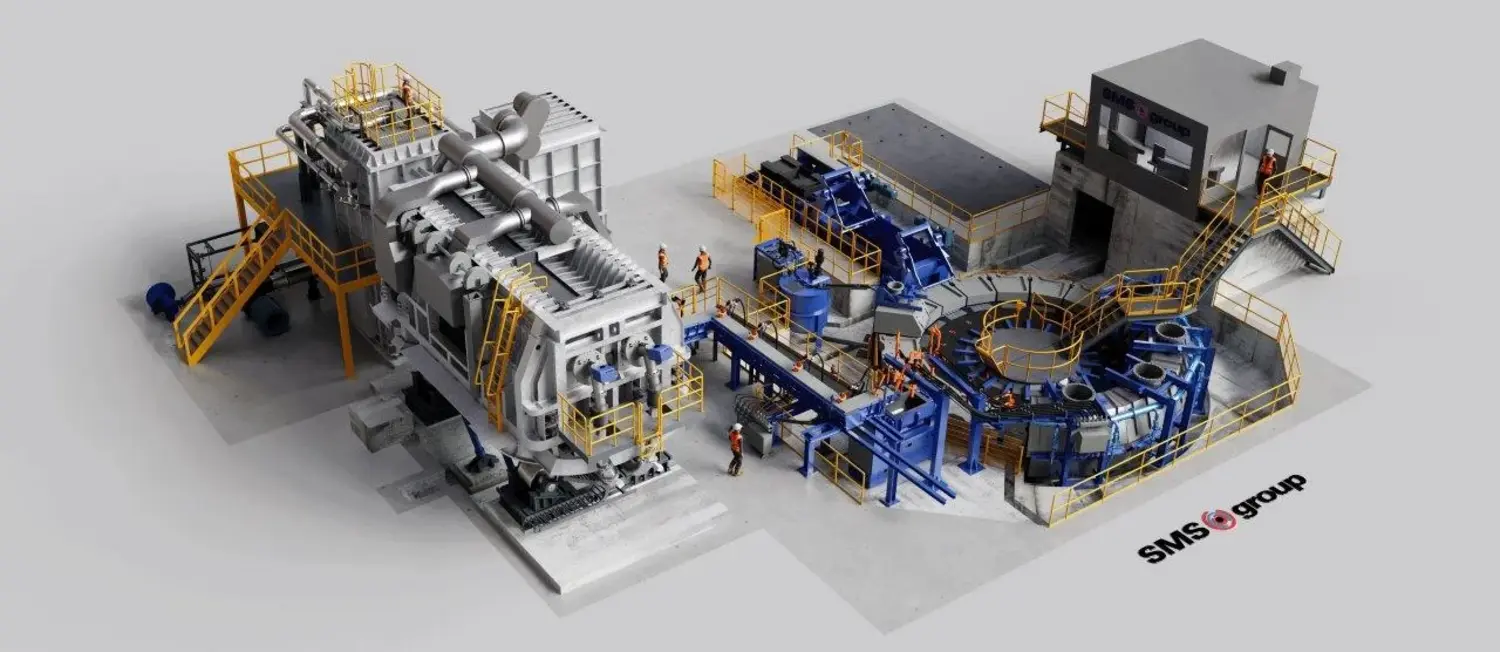
Maximize profits: BlueControl process control system
Maximum recycling rates are attained by combining plant technology and automation. The BlueControl calculation engine is designed to optimize metallurgical processes, aiming to achieve the highest copper content with the lowest impurities in the copper anode. It employs two core applications: simulation and optimization. The simulation controls the copper scrap refining process, calculating the mass and impurities concentration of anode copper at the end of the refining steps. The calculation happens in seconds and evaluates more than 100 potential operation points, choosing the best fit – both at the batch start and during operation. AI support also ensures the system’s self-learning capability. It dynamically adjusts parameters such as air blowing, oxidation, reduction, and purification rates, to meet the desired copper purity and composition.
The optimization algorithm embedded in BlueControl maximizes copper yield and minimizes impurities by finding the optimal combination of fluxes based on input parameters such as copper scrap weight, composition, feed temperature, and gas rates. This enhances production efficiency, yield, quality, and throughput, and reduces production costs. Our comprehensive metallurgical expertise coupled with innovative furnace design and our new BlueControl process control system are what make the difference. A first prediction for a large-scale TRF with a capacity of 350 t shows an annual saving potential of more than 10 million euros – only by software optimization.