Processes that enhance plant performance, and optimize operating and maintenance costs drive cutting-edge technology in our automation for hot rolling mills. This enables our customers to adapt themselves to changing market requirements and to increase their competitiveness by more flexible and sustainable production, superior product quality and minimized operational costs.
SMS group has extensive domain know-how and understanding of all important process steps in hot rolling. Thanks to our widely proven X-Pact® automation solutions and modern software development technologies we implement latest production standards. By doing so and also by supplying our plants digital ready our customers benefit from digital applications that ensure future viability of their plants.
Key features
- Power supply and drive systems for greater sustainability
- Innovative measuring systems
- Modular basic and process automation packages with sophisticated process models
- Innovative X-Pact® Vision HMI-concept for smart operation and visualization
- Diagnostics for startup, devices, sequences, safety, and plant
- Quality monitoring and predictive system for condition analysis
- Digital pre-commissioning of automation systems during the X-Pact® Plug & Work integration test
- Advanced operator training at an early stage before commissioning
- Fast start-up and commissioning of the hot rolling mills
- Perfect infrastructure for remote support with X-Pact® Service
OT products and solutions
X-Pact® Pass Schedule Calculation (PSC®)
Physical based process model for perfect set-up generation
X-Pact® PCFC®/PFC®
Optimum set-points for the actuators of CVC® plus system and the bending system
X-Pact® Cooling Section Control
In-bar temperature control over the entire strip length
X-Pact® Mill Stand Control
Technological control system to ensure highest product quality
X-Pact® Camber Free Rolling
Control system for camber and wedge-free rolling in the roughing mill area
X-Pact® Tail-Out Monitoring
Maximum productivity at minimum energy and acid consumption
X-Pact® Integrated Temperature Model
Optimized temperature settings to achieve best material properties
Linear position measurement with X-Pact® Sense
Robust linear position transducer for HGC
X-Pact® Strip Steering Control
Straight and safe strip guidance through the finishing mill, especially for head and tail
Strip center measurement with X-Pact® Sense hotCAM
Best strip position between the roll stands
X-Pact® Microstructure Property Model
Calculation of final strip properties and material microstructure
X-Pact® Width Control
Constant strip width over the entire length as close as possible to the target
X-Pact® Steckel Looper
Best mass flow concept between rolls and furnace drum
X-Pact® Coiler Control
Best product quality and high process stability during strip winding on up- and down coilers
X-Pact® Plant Pacing
Optimum throughput and productivity of the entire production plant
X-Pact® Thermo-Mechanical Rolling
Increased rate with sophisticated staggering of plates
X-Pact® Plate Leveler Control
Optimized model setpoint calculation for increased flatness performance
X-Pact® Automatic Shape Control
Best results for plate rectangularity
X-Pact® Plate Cooling Control
In-bar temperature cooling strategies
X-Pact® Plate Cutting Optimization
Best cuts for production of the finished plate
X-Shape Flatness Measurement and Control
Reliable and precise flatness measurement and control
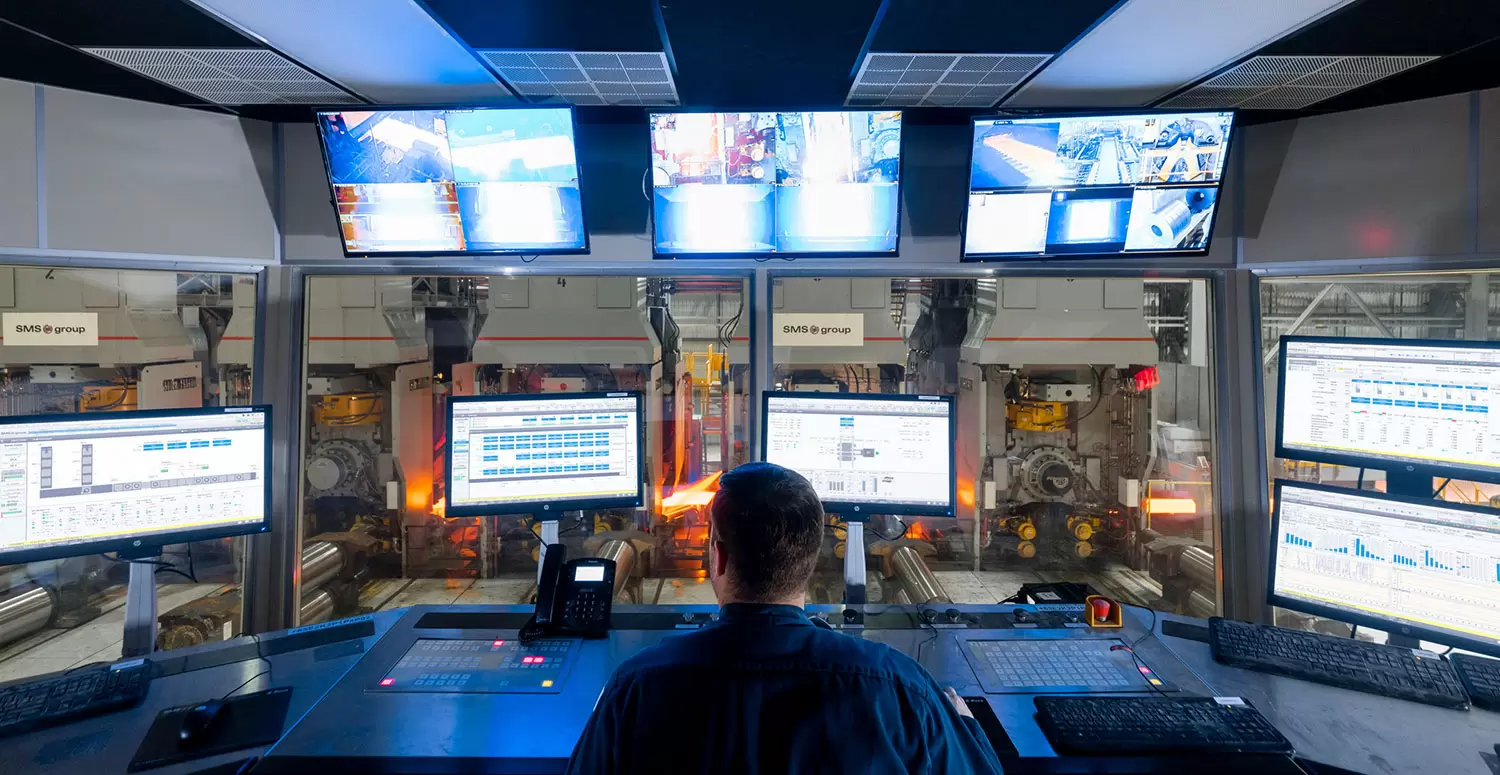
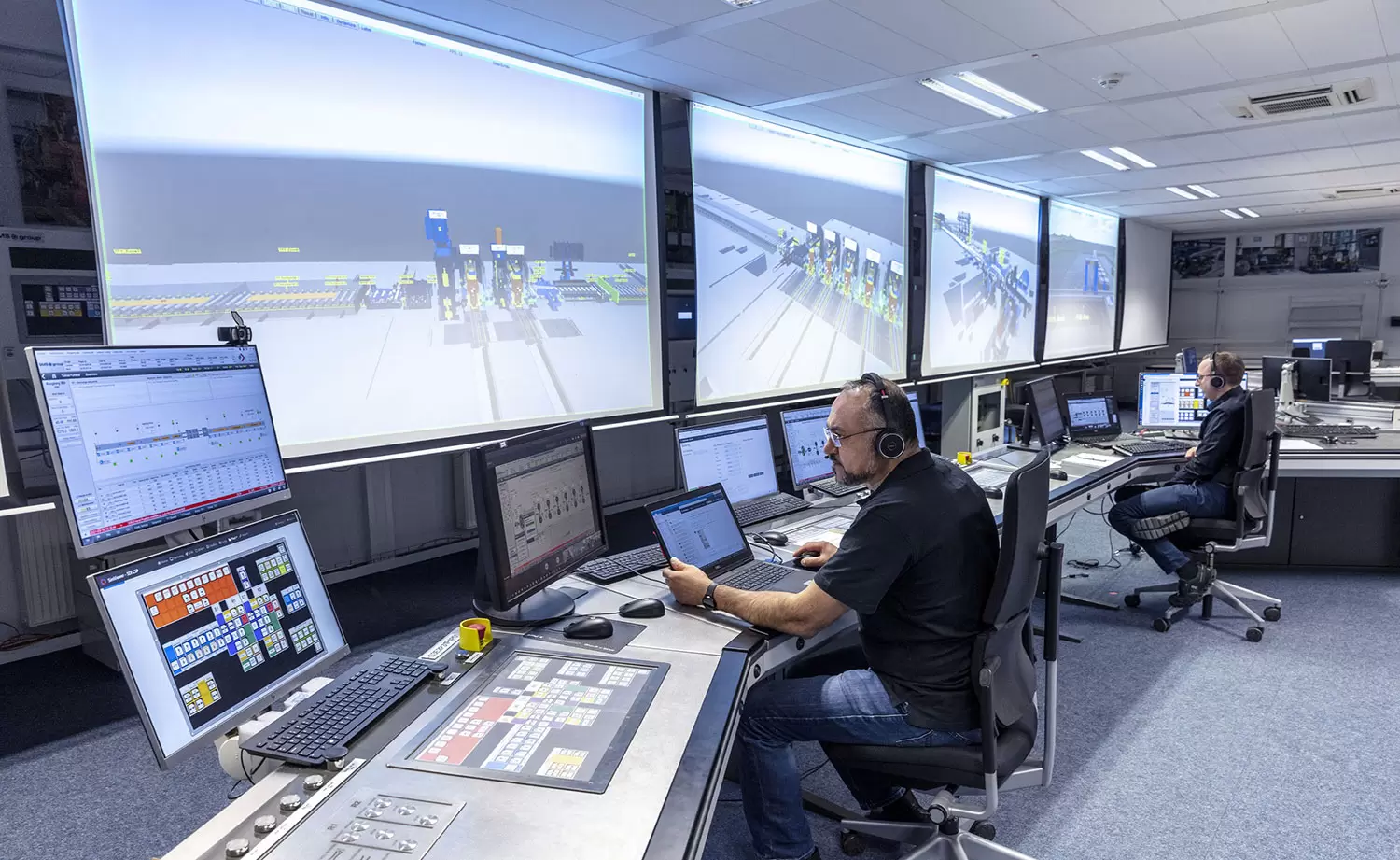
Use our contact form for questions, inquiries or personal contact.