The steel industry is faced with a major challenge: On the one hand, the pressure to reduce CO2 emissions is growing, and on the other hand, the demands on flexibility, product quality and cost optimization are increasing. It is therefore essential for operators of CSP® plants to continuously modernize existing production lines in order to remain competitive.
"Our customers are faced with the challenge of not only making their plants more efficient but also more sustainable – and that at maximum productivity," says Dr. Jochen Wans, Head of Casting Flat at SMS group.
Cost and energy optimization: The key to new competitive opportunities
Energy is one of the largest cost factors in steel production – and at the same time a central lever for sustainable efficiency increases. Operators of CSP® plants are faced with the challenge of optimizing their processes in such a way that the energy consumption per ton of steel is reduced without affecting productivity. A decisive approach is the introduction of the X-Pact® Integrated Process Model (IPM), which enables higher-level control and adaptation of all relevant process steps to the current requirements.
"The Integrated Process Model improves the process control over the entire production chain – from continuous casting to coiling – and can thus considerably reduce the energy requirement," explains Dr. Kai Grybel, Senior Expert Process Hot Rolling at SMS group.
In addition, the Integrated Process Model enables the consumption of alloying elements to be reduced through predictive process control in combination with the Microstructure Property Model (MPM). Further process optimizations provide for a maximization of the productivity by means of adaptations of the setting values for e.g. casting thickness or intermediate slab thickness or also of the temperatures. An optimized production method to extend the service life of critical plant components is also planned.
Productivity increase: Permanently increased throughput
The production capacity of a CSP® continuous caster is a decisive factor for the competitiveness. By increasing the casting thickness and casting width, more material per sequence can be processed, thus increasing the overall capacity of the plant. The extension of the strand guide system also plays a major role. Depending on the plant concept, it can be implemented either by an additional segment or by a combination of a segment and a separate pinch roll unit. An extended strand guide system improves the solidification conditions of the steel and allows higher casting speeds without jeopardizing the process stability.
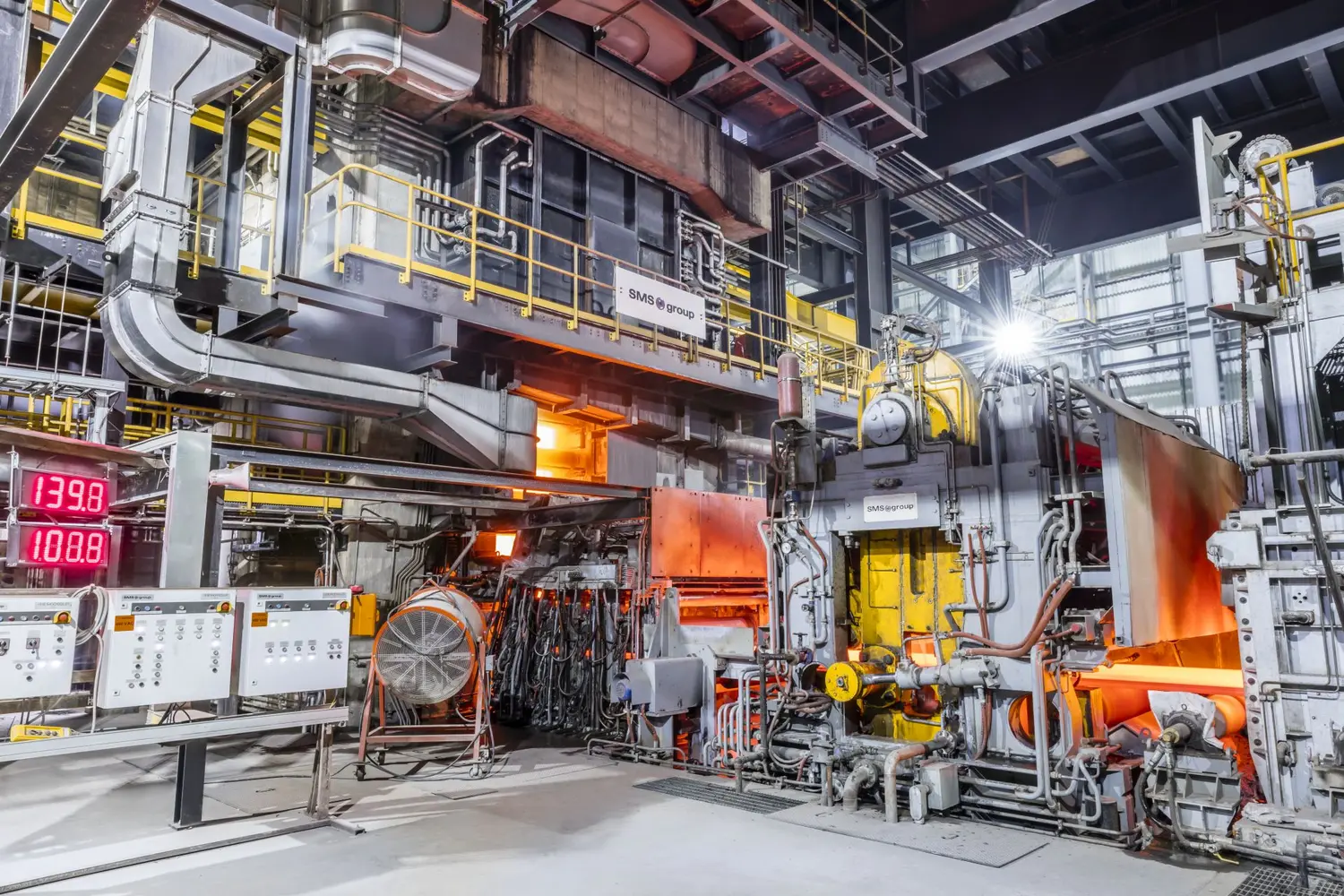
Expansion of the product mix: New steel grades for growth markets
The demand for highly specialized steel grades is growing continuously. In particular, electric steels for e-mobility and energy-efficient applications are gaining in importance. To remain competitive, CSP® continuous casters must become more flexible and supply a wider range of steel grades with an optimized internal structure and consistent surface quality. A key technology in this area is electromagnetic stirring (SEMS). By selectively influencing the solidification structure, SEMS improves the internal properties of the slabs and reduces segregation in the centerline. The result is a uniform microstructure with a higher proportion of equiaxial solidification, which is advantageous above all for silicon steels. In addition, modern casting technologies such as Soft reduction can be employed in order to further enhance the internal quality. Soft reduction is just as important for the internal quality. It’s a technological process where the strand shells will be compressed together at the area of final solidification. This serves to compensate the volume shrinkage caused by solidification and the minimization of segregation and porosity in the center of the slab. By combining these measures, new products can be efficiently integrated into the existing CSP® line without the need for extensive new investments.
Quality improvement: Optimized surfaces and microstructures
In addition to the geometry of the product, the focus is on the internal and external quality of the slabs. The optimization of the surface quality already starts in the continuous caster. The changeover from conventional roller grids to roller cassettes thus ensures a uniform support of the strand and prevents mechanical damage to the surface. As already described, technologies such as electromagnetic stirring (SEMS) and Soft reduction play a central role in improving internal quality. Both systems help to reduce segregations and porosities and ensure a more homogeneous solidification.
Digitalization: Process stability and efficiency thanks to intelligent systems
The precise control of the process parameters ensures constant quality, increases reproducibility and reduces manual interventions to a minimum. An essential part is the further development of the Level 2 automation system. By integrating advanced process models as part of a modernization project, temperature curves, casting speeds and cooling strategies can be dynamically adapted.
Dr. Ina Hüllen, Head of Process and Technology Casting Slab, SMS group: "Automation is the key to consistent quality and maximum process efficiency. A modern control system makes it possible to correct even the smallest deviations in real time."
Data analyzes and tools for predictive servicing supplement the process automation. Thanks to the continuous recording of machine conditions, maintenance measures can be planned in a targeted manner and unscheduled shutdowns can be avoided. At the same time, the state-of-the-art control systems enable greater flexibility during product changes and ensure faster adaptation to changing market and production requirements.
Sustainability: Decarbonization as a strategic advantage
The steel industry has a responsibility to reduce its CO2 emissions in order to achieve international climate targets. Through targeted, efficient modernization measures, CSP® plants offer great potential to reduce energy consumption and to produce more efficiently. An important lever is process optimization through digital control systems. Their use reduces the required amount of energy. An optimized temperature control system reduces the fuel consumption in the heating furnaces and significantly reduces the CO2 emissions per ton of steel. In addition, SMS group technologies contribute to sustainability by reducing scrap and material losses. A further measure is the targeted adaptation of cooling strategies in order to minimize water consumption and reduce the overall ecological footprint of the plant.
"The modernization of CSP® continuous casters is therefore not only a question of competitiveness, but also a decisive step toward sustainable steel production," summarizes Björn Kintscher, Senior Technology Professional CSP®, SMS group.
References: Successful projects from practice
Numerous modernization projects show how targeted investments in CSP® continuous casters increase competitiveness and improve production performance.
At Nucor Crawfordsville, revamps have been carried out continuously since its first commissioning in 1989 in order to increase the productivity and flexibility of the mill. The most important measures include the extension of the strand guide system, the introduction of new casting technologies and the implementation of advanced automation systems. These measures have helped to increase production capacity while at the same time reducing production costs.
Nucor Berkeley was relying on a comprehensive modernization of the continuous caster in order to expand its product range. By increasing a casting strand by 200 mm, installing Liquid Core Reduction (LCR) and a new oscillation technology, it was possible to include new steel grades in the production process. The modernization was supplemented by an induction heating system, which considerably increased the flexibility of the production process even further.
At JSW Dolvi, the focus was on increasing productivity. The extension of the metallurgical length of the strand guide system by 2.5 meters, combined with new bending and leveling systems as well as electromagnetic brakes, enabled a capacity increase of more than 10% and at the same time improved the internal quality of the slabs.
Future-proof CSP® continuous casters through targeted modernization projects
The requirements placed on CSP® continuous casters are constantly changing. Energy efficiency, increased productivity, flexible production possibilities and sustainable operation are crucial for long-term competitiveness.
Targeted modernizations allow owners to adapt their plants to new market requirements without having to invest in completely new production lines. The modernization of the CSP® continuous caster is therefore not only a technological necessity but also a strategic decision. Operators who today invest in efficient and flexible solutions secure a decisive advantage in an increasingly volatile market environment.