Hydraulics are particularly important for the operation of any metallurgical plant, because if the hydraulic system is down, in most cases the entire production has to be stopped. The causes of potential damages are extremely diverse, and often the sources cannot to be localized at first glance.
As a supplier of integrated fluid systems for the metallurgical industry and rolling mills, we are a competent partner of our customers all over the world. In addition to the state-of-the-art methods and processes we can refer to more than 50 years of experience in the planning, design and manufacture of hydraulic, pneumatic, oil lubrication and descaling systems.
Customers can benefit from this expertise in a variety of ways to ensure maximum availability and performance of the hydraulic system. Be it for a short-term fault analysis and correction, as part of a modernization or through our maintenance service.
Fast troubleshooting
Once problems with the hydraulic system occur, this invariably leads to an unwanted system shutdown and an immediate loss of revenues. Now a fast localization of the fault is important. Therefore, plant operators should leave nothing to chance when troubleshooting and entrust themselves directly to experienced experts.
For all of our services, but especially in an emergency during analysis and troubleshooting, the customer benefits from the system competence of the service experts of SMS group. Thanks to the extensive process know-how of a plant manufacturer and the knowledge of the plant control system, the technical service of SMS group is able to carry out comprehensive troubleshooting and to find causes that go deeper than a burst hose or a faulty valve.
In the past, SMS group has been able to demonstrate this competitive edge many times by supporting customers with loss of performance or unwanted downtimes due to hydraulic failures. Following a targeted analysis, the end result was always the localization of the problem and the short-term correction of the error, as well as a detailed documentation of the solution approach.
One customer for example reported problems with all pushers on his two slab grinding machines. SMS group carried out a fact finding on the hydraulic systems of the slab grinding machines. Defective 4/3 way valves were identified as the cause of the uncontrolled driving movements of the pushers. Replacing the defective parts was initially unsuccessful. As it turned out after further investigations, the directional control valves were damaged by extreme shocks due to faulty hydraulic controls.
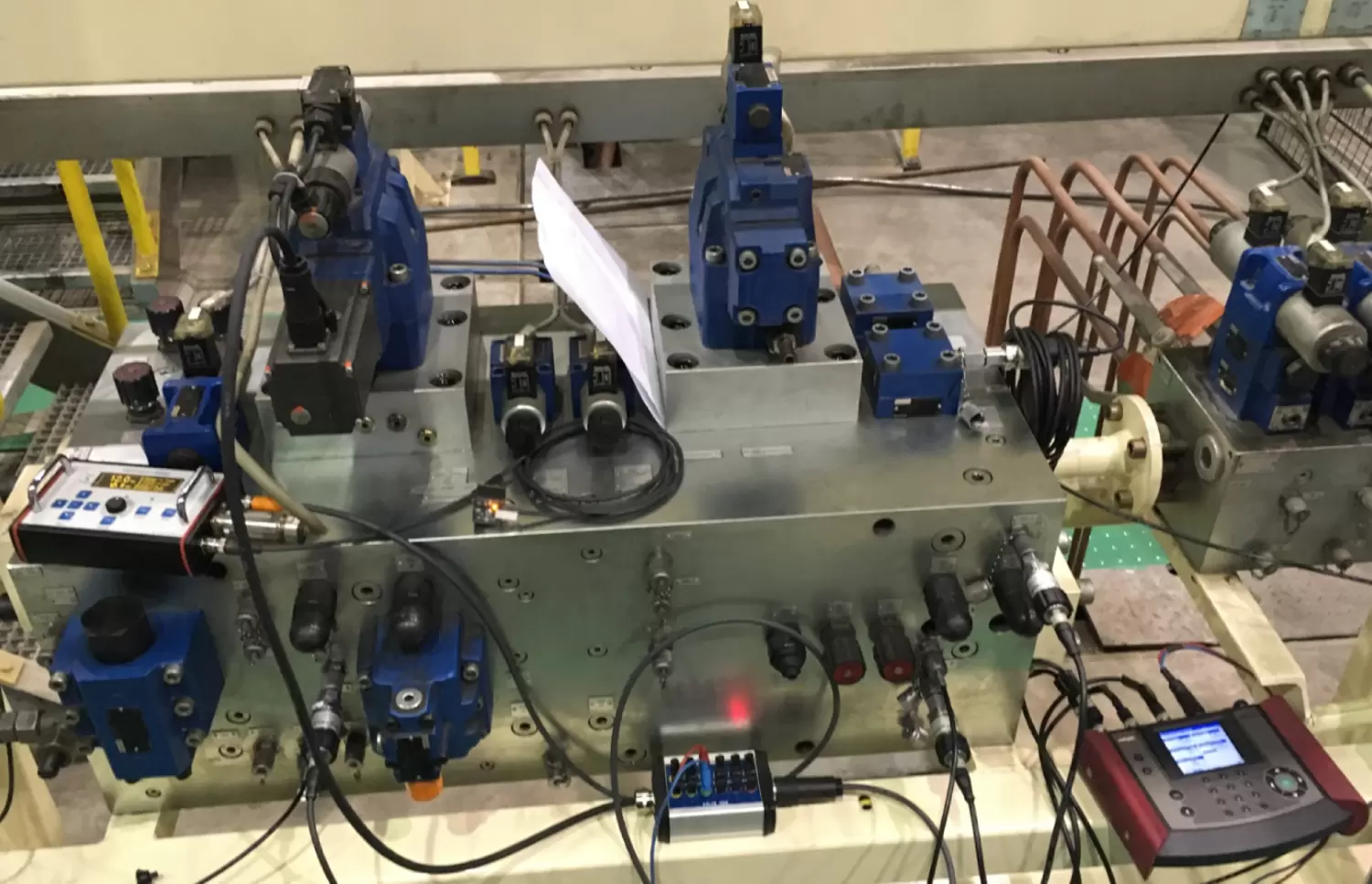
How to keep your hydraulic system state-of-the-art
However, it is not necessarily a fault that affects the system. Wear, dirt or high temperatures lead to the system's performance deteriorating over time. In addition to the loss of performance, higher costs are the result of this process. The so-called fact finding audit is designed to help improve overall plant effectiveness (Overall Equipment Effectiveness - OEE). Any possible wear parts (too high zero leak oil flows of the servo valves, pumps, etc.) are identified and replaced, and performance tests are carried out.
Both analysis results and reports on the state of the system are often used as the basis for optimization. On this basis, we advise you on possible standardized upgrades or extensive modernizations to ensure that your hydraulic system remains competitive for decades.
You benefit in the long term from permanently low operating costs, high product quality and productivity.
Against the background of changing regulations, you should also keep an eye on occupational and operational safety. As part of our modernization concepts, we also bring your hydraulic system and your plant up to date.
SMS TECademy offers trainings dedicated to hydraulics
In our SMS TECademy, training courses especially dedicated to hydraulic systems transfer the know-how and experience gathered by our experts to your employees.
Individual practical training in our modern classrooms or on site provides comprehensive overview of the interaction between control mechanics and hydraulic automation. We give customers an insight into the measurement and test equipment required to determine the performance and condition of hydraulic components such as pumps, servo valves, cylinder control circuits or liquids. The training courses can be executed in our training rooms as well as in the form of webucation programs.
The complexity of the systems, and the cause analysis, and troubleshooting in the event of failures – also part of the SMS group hydraulic seminar - illustrate in practice the need for predictive maintenance, always resulting in cost savings compared to a standstill.
You focus on your core business - We look after your hydraulics
Preventive or condition-based maintenance and necessary repairs of individual components are essential to ensure maximum performance. Benefit from our on-site repair service or in one of our workshops in your area. State-of-the-art production and a highly qualified team in our worldwide service workshops ensure the optimum maintenance and repair.
Our employees profit from ongoing training, regularly exchange information with our design and development specialists for all product areas and therefore have the latest know-how of integrated systems. The ideal prerequisites for having your system professionally serviced in the long term and core components repaired by our experts in OEM quality.
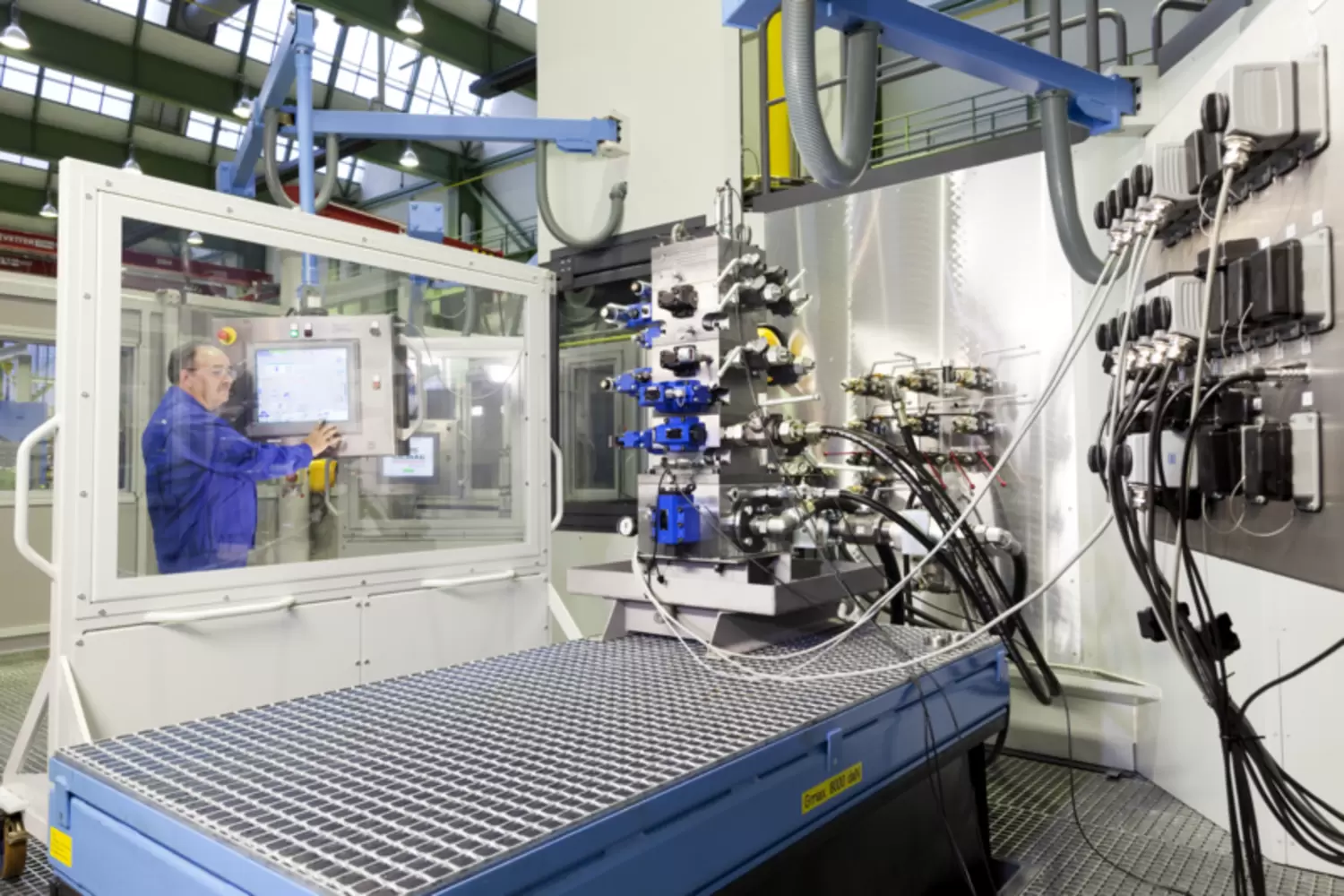