The complex nature of the steelmaking process, an ever-changing process automation technology landscape, and the continuously evolving requirements of markets and customers make one thing very clear: The plant automation systems must be continually updated and able to learn from and adapt to their environment.
In addition to its ongoing functionality improvements, typical challenges for automation systems today are:
- Security and operation system updates
- Database maintenance and supervision in Level 2
- Control of the communication between different levels and apps
- Gaps in automation performance due to new grades or materials
- Unexpected impacts of changes in the software
- Wear-and-tear impact of the mechatronic behavior and related process improvements.
Our software design addresses these challenges. X-Pact® (Process Automation Control Technology) automation focuses on holism, openness, and learning. Gerald Mayr, Executive Vice President of Electrics/Automation at SMS group, stands firmly behind this approach. “We take responsibility for our automation systems over the entire plant life cycle. Along with the main focus on process guidance for operation and control, our innovative, structured, and modularized Level 1 and Level 2 software architecture facilitates multi-directional connectivity. This results in a digital-ready delivery enabling the complete world of digitalization without additional efforts.”
Openness: Vital for connectivity
Modular software architecture is essential here. SMS group combines its modules with open-source and third-party products to provide application openness and eliminate dependency on a single supplier. Using state-of-the-art software and development tools, SMS group implements international standards in its innovative, structured, and modularized software architecture in Level 1 and Level 2. The system design focuses on consistent version management and integrating testing. Individual update processes and procedures for each delivery can be pretested in-house during X-Pact® Plug & Work integration testing that SMS group runs for each project long before on-site installation.
Gerald Mayr explains: “Thanks to our process guidance approach, we have standard interfaces in our models for Level 2 and above via a communication adapter. Like a travel plug adapter, we offer all state-of-the-art communication protocols without interfering with the application’s kernel. This means that whatever our customers select, we can connect without any additional integration effort. We have the same approach for databases: Our application connects to any customer database – including open-source products like Maria DB or licensed products like Oracle. We simply plug in.”
Additionally, SMS group has developed different software layers to stabilize real-time performance. With this approach, the system can reply to requests much faster than before to guarantee flawless production performance.
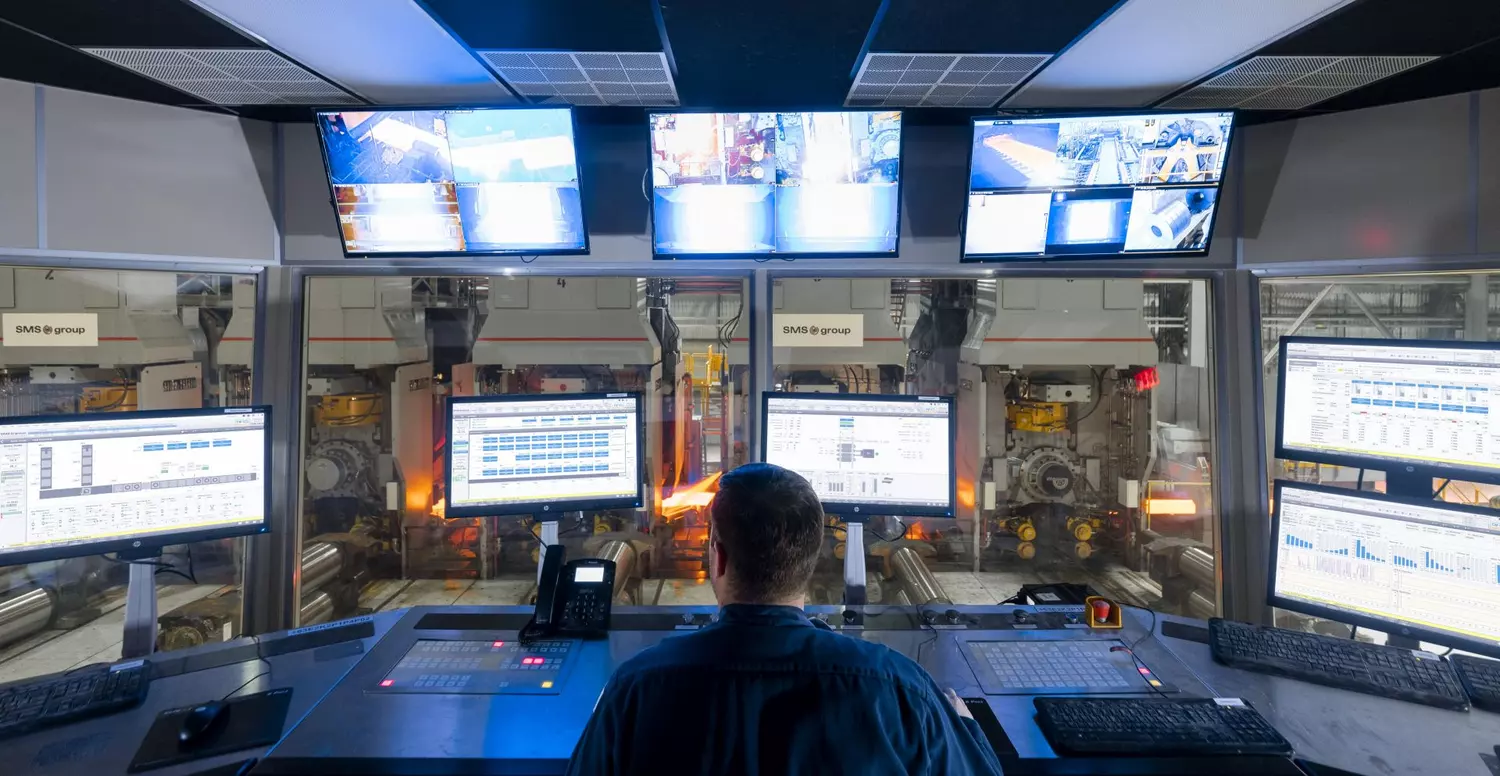
Learning: Thanks to digital readiness
All SMS plants come digital-ready, with all machine and automation data described in contextual meta-information in a standardized format via supported interface technologies. With SMS DataFactory, these data can be gathered centrally and, thanks to the harmonized description, made easily accessible for all digital solutions. The content and the data genealogy are reduced to one interface for apps without any impact on system performance in Levels 1 and 2.
SMS group facilitates Level 2 and Level 1 version control and delivery documentation for our software products via our in-house competence center. A team of experts is responsible for keeping libraries up to date and meeting the challenging quality standards before release. Improvements based on feedback from customers and our experts, mainly during the start-up phase (e.g. HMI faceplates), are crucial for delivering updates without changing the core functionality of the individual application. By strictly defined hierarchical software design in the Level 1 according to functional layer modeling, the updates have to be done only in the lower hierarchy level. At the same time, process improvements happen in the upper part of the software architecture.
Based on the functional layer principle, different functionalities like sequencing and technology control are allocated to different layers. Gerald Mayr explains what that means for process improvements: “Based on what our customers need, we can enable them to make their own changes in the sequencing layer. However, technology controls are a different story. They are very complex, have high real-time demands, and have a high potential for negative impacts across all levels when altered by inexperienced personnel. That’s why we offer our customers process improvements in a SaaS (Software as a Service) model by connecting to our own optimization apps, AI modules, or those from third parties. Our strategy is to eliminate the borders between Level 1 and Level 2 by encapsulating the technology control in a highly real-time demanding controller environment as SaaS on-premises. This allows our customers to focus on the production sequences and use the control as an intelligent “gray box” maintained by SMS experts. Nowadays, technological control systems (TCS) present a huge opportunity to adapt to customer needs via outside configuration while keeping the core stable. Connectivity and open interfaces are key. While we prefer our solutions, we are not afraid of the know-how of others. For us, this is competition. Thanks to the openness, a customer could run two models in parallel and evaluate the performance of each.”
Due to hundreds of combinations with thousands of different set points are possible in technological control, the customer benefits for such a “gray box” solution are numerous:
- Customers select the right strategy (for example off gauge length or maximum speed) based on material and yield results and get a properly tuned TCS automatically via an intuitive simplified HMI interface.
- Customers can change the strategy on time without taking care of the controller set points details.
- Background optimization of the set points based on a combination of the selected strategies.
- Customers are free to connect to other providers they want to work with based on the open connectivity interface.
High-performance automation is not limited to the system expertise and architecture. It is more about the additional services for performance improvements throughout the plant life cycle.
Holism: New EaaS/SaaS operational readiness solution
In an exciting new development, SMS group is preparing to introduce a more far-reaching approach. All of the capabilities mentioned above like updates, connectivity, openness, performance improvements, security, and maintenance, could be parts of a new “all-inclusive” solution for “operational readiness”. Combining all these efforts with SMS group’s 24/7 services, this approach represents a new direction in which SMS group wants to go in order to guarantee system performance stability and availability. By combining EaaS (Equipment as a Service) and SaaS on-premise, plant owners will be able to focus exclusively on operations.
In an automotive context, we would call it “readiness to drive”. For an automation system, we call it “operational readiness” it will mean:
- Backup done
- Licenses and certificates are up to date
- Latest version of software applied
- Security regularly checked, no virus or malware
- Databases cleaned and not locked
- Controller, switches, and devices are running
- System ready and available for operation
Gerald Mayr sums up: “With our new concept of operational readiness, we allow customers to focus exclusively on operation. Everything else is taken care of by us.”
Digital ready
Digital readiness is essential for making production units, equipment, devices, automation systems, or any other element ready for digitalization with minimal effort. It means that by providing documented access to data, existing and future software solutions and models can easily be integrated. If an element is digital-ready, its machine and automation data is described via contextual information (metadata), and its data access information is published in a standardized fashion via all supported interface technologies.