The long-lasting partnership between SMS group and Aluminum Dynamics LLC (ADL), a joint venture of Steel Dynamics, Inc., has been instrumental in navigating the complexities of this endeavor, ensuring adherence to timelines and quality standards. The CCL represents a pivotal addition to ADL's aluminum production infrastructure.
SMS group’s coating lines allow for high-quality coating of aluminum strip suited for direct processing to final products. Precise coatings with excellent surface quality and resource-saving as well as energy-efficient operation are the characteristics of these lines. The material produced on the new CCL line at ADL is used for can end material, which involves the highest demands in terms of food industry certification. Depending on the type of beverage can, various paints must be applied with an accuracy of one thousandth of a millimeter.
The line was designed to operate flexibly with both solvent- and water-based paints, covering a wide product portfolio. A further outstanding feature is its ability to coat ultra-thin strip at high speeds. The line is equipped with all necessary equipment ensuring a further increase in material quality. From mechanical equipment to electrical and automation systems, all were supplied by SMS group from one source.
Key process highlights
The initial stages of the CCL process include unwinding, trimming, pre-cleaning and leveling of aluminum strips, laying the groundwork for precise coating application. To ensure maximum surface quality, the strip treatment begins with thorough alkaline and acidic cleaning to activate the strip surface for the following process steps. In the chemical treatment section, a thin passivation layer is applied via a chemical roll coater. After that, the strip is prepared for the paint application.
Epoxy varnish is uniformly applied on top and bottom side of the strip via a roll coater. Equipped with three rolls each and various automatic adjustment options, the top and bottom deck of the coater ensure precise coating results.
Advanced curing methods, including the utilization of a flotation dryer, facilitate efficient drying processes by keeping the strip floating, dried and cooled. Environmental considerations are addressed through waste air treatment via a regenerative thermal oxidizer (RTO), boasting superior heat recovery capabilities. The RTO serves as a critical component, ensuring regulatory compliance and emissions control, while also contributing to energy efficiency by recovering energy from solvent-containing exhaust air. Cleaning the solvent-containing exhaust air by the RTO exemplifies efficient energy recovery. Post-combustion of the extracted solvents occurs in a three-chamber system with catalytic blocks. Hot air is then fed to the flotation dryer through a heat exchanger, enabling the dryer to operate in autothermal mode without requiring additional energy, provided, that the solvent content of the paint is sufficiently high.
Integrated solutions
Electrics and automation is one of the cornerstones in the SMS group’s scope of supply for the new can coating line, ensuring seamless system integration. The software's innovative architecture incorporates a modular design adhering to international standards and enables extensive connectivity. The X-Pact® Level 1 system, built on Siemens TIA platform, delivers stable real-time line performance. Enhanced diagnostics with faceplates and pop-ups allow for rapid response, advanced production analysis, high system availability, quick troubleshooting, and flawless production.
For the edge scrap balers at ADL’s new can coating line, the energy-efficient X-Pact® Torque Drive offers low noise, minimal maintenance, and optimal drive performance. SMS group's design incorporates all electrical components into the necessary mechanical structure allowing the machine to achieve a total efficiency of up to 98 percent.
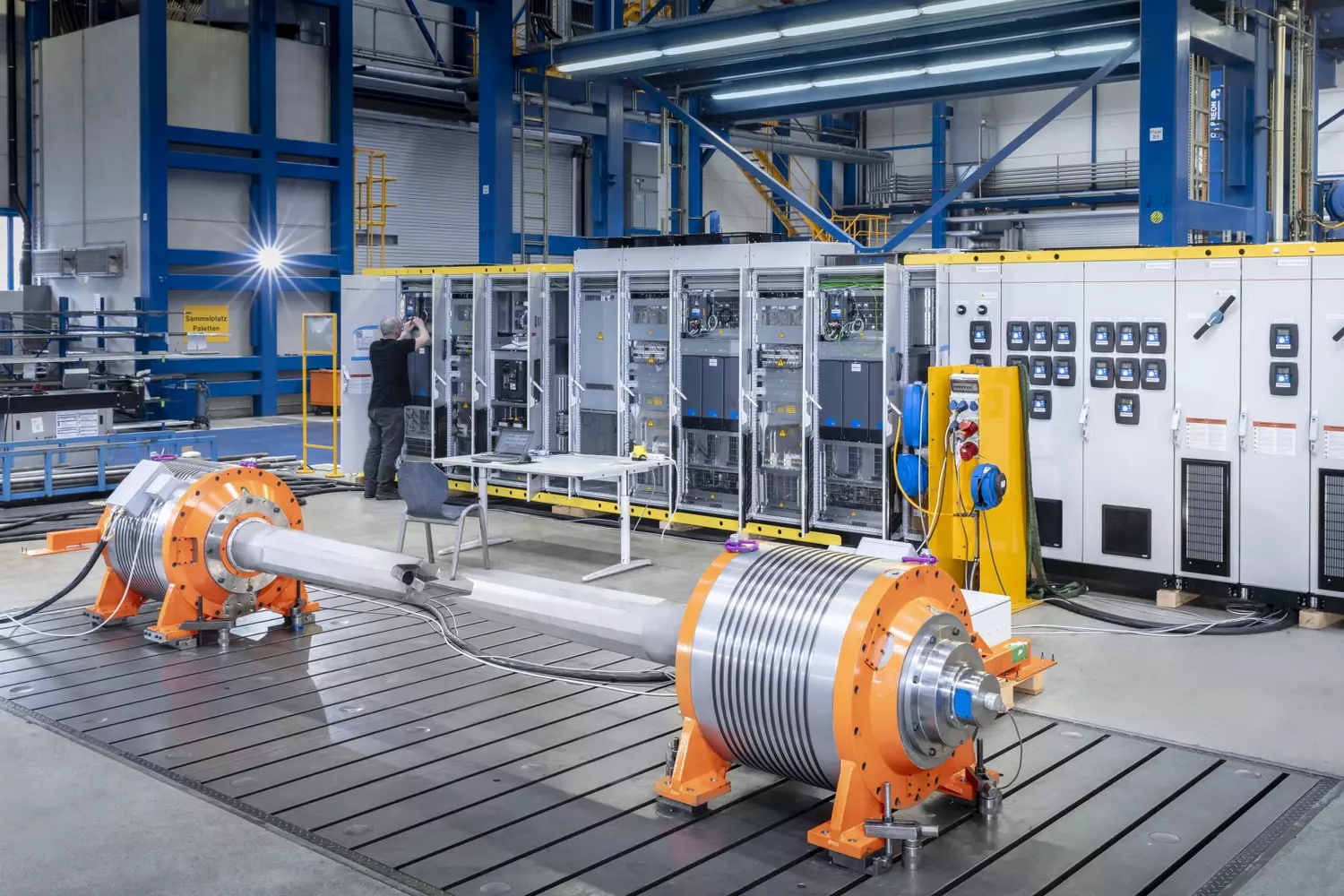
The X-Pact® Drive, a modular and energy-efficient solution for low-voltage frequency converters, meets the demanding process-oriented drive requirements of the new CCL. This system, alongside the direct drive, forms a cohesive concept tailored to ADL’s performance requirements.
As with all SMS projects, the new automation system for CCL will undergo a comprehensive X-Pact® Plug & Work integration test. The SMS group’s experts run extensive tests and optimize the automation as well as the related production processes even before the plant is assembled and in operation, reducing commissioning time. ADL’s operators receive training with real-time process simulations, enhancing their understanding of plant component interactions.
As the assembly and commissioning of the CCL approaches, ADL and SMS group maintain their commitment to innovation and excellence in aluminum production. The installation of the CCL marks a significant advancement in efficiency and sustainability, positioning ADL as a leader in the global aluminum market. This underscores ADL's dedication to operational excellence and responsiveness to market demands. With SMS group's cutting-edge technologies, ADL is well-positioned to set new benchmarks in aluminum production.