SMS group and DanSteel partner to enhance production efficiency in heavy plate steel production
The production of structural heavy plate steel is a multi-step process where each stage impacts both product quality and production. Among these stages, slab reheating for rolling stands out as a crucial step, directly influencing the quality and cost-efficiency of the end product.
At DanSteel's rolling complex 4200, slabs are heated in either a walking hearth furnace or a walking beam furnace, depending on their dimensions. For large and heavy slabs with cross-sections up to 400×2800 mm, the new walking-beam reheating furnace by SMS group, commissioned in 2022, offers a significant advancement.
The primary goals behind installing this new furnace were to expand DanSteel's product range to include XXL high-quality heavy plates, which are in high demand in industries such as offshore wind power and bridge construction. Further, it was aimed at improving production efficiency and environmental performance of the slab reheating process.
DanSteel has a long-standing partnership with SMS group, leveraging their expertise to advance their production capabilities. Alan Thomasen, Technical Manager at DanSteel, explained, "We recognized the need for a more advanced and automated furnace to ensure consistent slab reheat. The furnace from SMS group caught our attention as it offered the perfect solution to address our requirements. Additionally, we were attracted to the potential productivity boost it could provide, allowing us to meet increasing customer demands effectively."
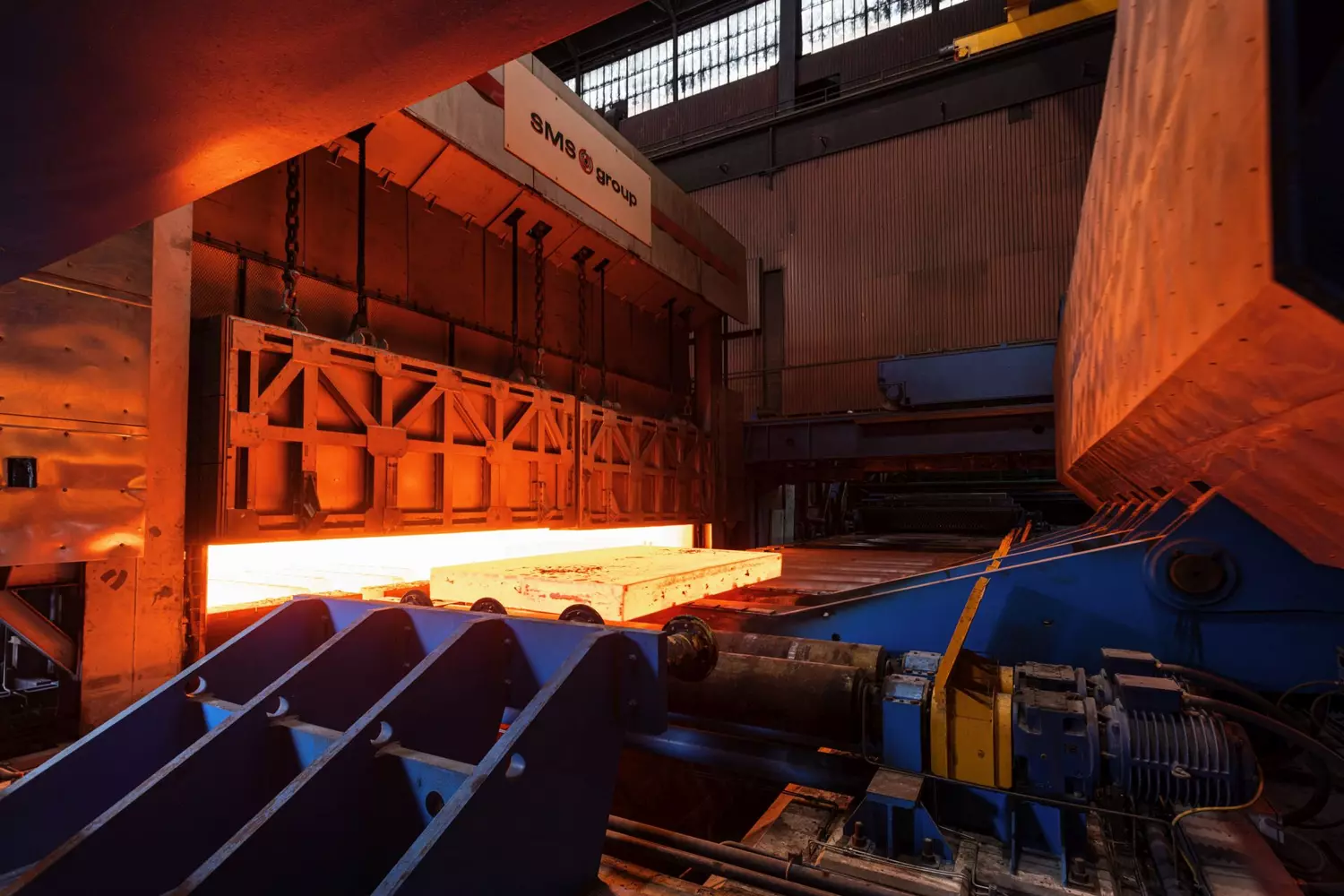
Enhancing sustainability and competitiveness with the new walking-beam furnace
The new walking-beam reheating furnace, which was installed in 2021 and commissioned in 2022, represents an upgrade aimed at supporting the production of high-quality XXL heavy plates. It is able to heat up to 100 tons of slabs per hour, accommodating slabs with a maximum cross-section of 400 × 2,800 mm. Another product feature is the uniform heating capacity, with a maximum temperature difference of just 30°C between the coldest and hottest points on the slabs. Moreover, the new furnace was designed with a strong focus on environmental and energy efficiency. CO2 emissions are reduced by 17-18% compared to the existing furnaces at DanSteel. This reduction is achieved through innovative design features, such as the SMS ZEROFlame burner, which operates in flameless mode to achieve extremely low NOx emissions. The reduction in CO2 emissions aligns with global efforts to minimize the environmental impact of industrial processes.
By increasing production capacity and improving product quality, DanSteel can better meet the demands of industries that require high-quality heavy plates. This positions DanSteel as a leader in the market, capable of delivering superior products while maintaining a commitment to sustainability. This modernization effort underscores the importance of adopting advanced technologies to achieve both economic and environmental goals in the steel industry.