Trend to peeling on a large scale - BGH plays a pioneering role
The market for forged bar steel requires large sizes, high-quality and in particular round material free from surface flaws with close tolerances. Peeled bars with diameters larger than 200 millimeters were rarely requested in the past, but nowadays this demand has increased due to a growing energy market.
With the investment in the peeling machine of the PMH 600 type, BGH Edelstahl from Siegen, Germany, has now reacted to the changing market situations as one of the first producers; because especially high-quality grades with large diameters are now almost exclusively supplied with machined surfaces and correspondingly high inspection requirements. With a manufacturing diameter of up to 600 millimeters this machine enters new dimensions.
“With the existing machines, we would not have been able to produce higher sales volumes any more,“ explained Jost Kretzer, Plant Manager at BGH. ”BGH evaluated the installation of turning machines and a new peeling machine and decided in favor of a peeling machine for various reasons. However, the new machine needed certain properties, i.e. machining of bar steel with a total weight of 25 tons and a diameter range of up to 600 millimeters should be possible. “We approached the peeling machine manufacturers with these figures because a machine of this scale did not exist before. With SMS group we have then designed this machine according to our requirements within a project planning period of two years,“ recalls Jost Kretzer.
Pioneering work in the development of the indexable peeling insert
For a peeling machine of this dimension a tool has not yet been available until now with which the required chip removal rates could be realized. For this reason, BGH turned to the experts of Cutting Solutions by CERATIZIT in Reutte, Austria, who offer a comprehensive range of indexable peeling inserts for diverse applications in the area of peeling with specialized knowledge in this field. The specific needs of BGH and the demands on the tool made by one of the largest peeling machines worldwide convinced CERATIZIT to develop entirely new indexable peeling inserts.
Product manager Ronald Huber still remembers well the development when the tool experts from Reutte have done a great piece of pioneering work: ”Concerning its positioning the existing round insert had decisive disadvantages. We therefore redesigned the roughing plate to an outer polygonal form to make sure that in addition to an exact indexing of the insert seat better cutting properties are also reached.“ As Huber explained, a perfect chip break is essential for a reliable peeling process. The formation of long chips must be absolutely avoided since about five tons of chips accrue per hour in the peeling process. “With the new hexagonal roughing plate we not only ensure top chip formation. It also withstands extremely high feeding speeds of up to 24 mm/rev. In doing so, we stepped forward together with BGH and SMS group to peeling areas where no one has ever been before and where no one is present until today except us,“ emphasized the product manager of CERATIZIT.
Peeling for top diameter tolerance and surface roughness
BGH Edelstahl in Siegen produces stainless steel and special alloys for maximum stresses. To ensure the desired surface quality, dimensional accuracy and roundness of its steel bars the bars are peeled by BGH prior to delivery. This results in semi-finished products further machined by turning shops. The bars serve as starting material for mechanical engineering, oil and gas industries or the chemical industry. Also heavy-duty wind turbine gearboxes emerge from the starting material of BGH. “Our customers want a machined bar steel without a rough forging surface,” Jost Kretzer explained. To make sure that the desired diameter tolerance and surface roughness are achieved the oxide layer and the rolling skin of the forged bars are peeled.
Only through close cooperation between user, machine builder and tool supplier the envisaged success criteria could be attained and new market segments be opened. Jost Kretzer summarizes the trusting cooperation with SMS group as machine manufacturer and Cutting Solutions by CERATIZIT as preferred tool supplier as follows: “If not all parties involved would have pulled together in one direction such result could not have been achieved. We as users will continue to be under an obligation and have to communicate the advantages and disadvantages openly and honestly. As long as tool supplier and machine manufacturer listen to these opinions the results can be further increased which is beneficial to all parties involved.\"
Challenge for optimally peeled bars
A special challenge for the production of bright steels is that often difficult cutting materials such as stainless steels and nickel-based alloys are machined. Here, the machines of the PMH series provide higher power reserves than their predecessors. What’s more, the starting material for large bar formats is usually forged. This manufacturing process will, however, mean that the material is significantly more out-of- round than is known from rolled material.
Here, it was previously the case that most of the forged bars exceeding 250 millimeters have been machined to bright steel on turning machines which is inefficient in three ways: on the one hand, a turning operation lasts up to 16 times longer compared to peeling. And on the other hand, higher setup times such as centering, clamping and reclamping are necessary during turning. In addition to that, higher machining allowances are needed during the turning process since the peeling machine can follow slight bar curvatures in comparison to turning operations.
This is also the case for previous peeling machine concepts, insofar as they operate with rigid guide systems at the in- and outlet section. The new PMH series is different: depending on customer requirement, the machine is not only able to operate with rigid guides in accordance with the traditional principle but it adapts to the curvature of the bar if needed and only removes a minimal amount of steel.
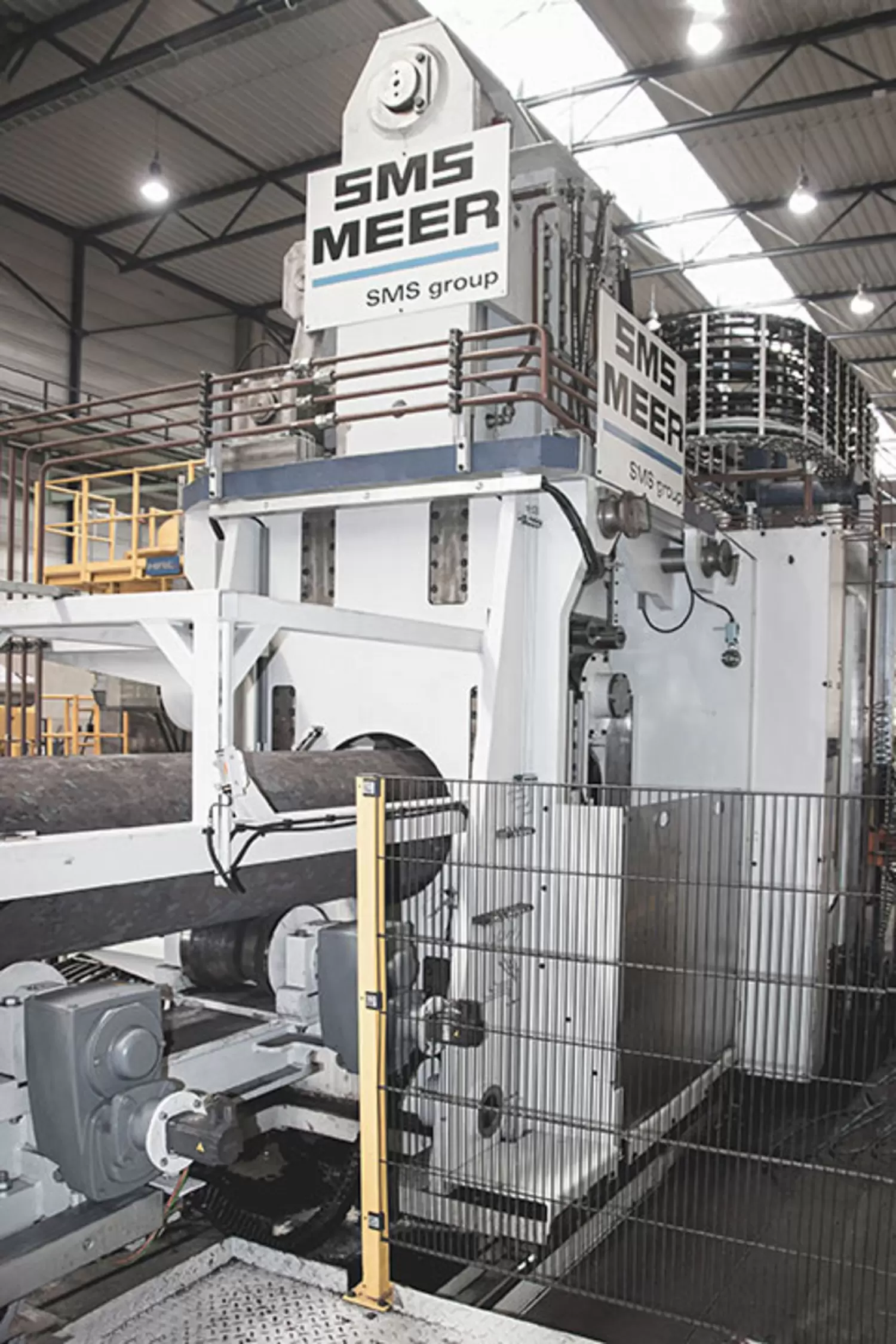
Few problems with bar curvatures
The working principle of the guide systems at the in- and outlet section is simple: an infeed carriage first clamps the bar centrally and transports it to the peeling machine. The driven rolls of the entry roller table and the driven support rolls integrated in the carriage bed ensure uniformity.
Then, the infeed carriage guides the bar head end to the opened entry guide, travels again in the direction of the bar tail end / entry roller table and clamps the bar at a distance of at least three meters from the entry guide. In this case, clamping takes place eccentrically. At first, the clamping jaws of the infeed carriage contact the bar in a path-controlled manner. Thereafter, the clamping pressure is increased evenly on both sides and constantly kept on both clamping cylinders. Finally, the infeed carriage pushes the bar further through the machine and the peeling process begins.
Thought-out working principle
During peeling the process center is dictated by the entry guide. Possible unevenness of the bar is compensated by the extraction carriage since the clamping cylinders as a package are floating horizontally. As soon as the bar head end exits the peeling machine the extraction carriage starts to move. The speed of the extraction carriage is synchronized with the velocity of the infeed carriage before the extraction carriage also starts clamping eccentrically. For a short moment the bar is clamped in the infeed as well as the extraction carriage before the bar is completely transferred to the extraction carriage.
Depending on the bar length, the transfer between infeed and extraction carriage is repeated several times. After extraction the bar is transported by the support rolls integrated in the carriage bed and by the rolls of the exit roller table, and is then ejected onto the deposit grate. The working principle with an infeed carriage has even more advantages compared to the use of an infeed unit with rolls: the fact that the bars in the infeed carriage are clamped in a fixed position makes it possible that bar turning during the peeling process is prevented effectively.
These so-called bar twisters occurred again and again in conventional machines in combination with forged and relatively inaccurate material causing damage to machinery, substantial in part.
Lower operating costs
The central concern was to realize an operating cost concept for the new PMH series over the machine’s lifecycle in combination with the peeling innovations implemented. Compared to large-size peeling machines of the previous generation, maintenance work for PMH peeling machines has been significantly reduced and expenditure for tool changes considerable minimized. By using e.g. low-wear infeed rolls regular roll changes can be dispensed with. Changing worn rolls of an infeed unit not only generates material costs of several thousand euros but requires up to half a working shift during which the machine is not able to produce. Besides, a tool change of the PHM series from SMS group is restricted to replacing the tool cassettes and enables a minimal changing time of the peeling tools. For conventional machines the complete slide unit must be changed. Likewise, the entire adjustment range of the machine can be covered with only one single tool.
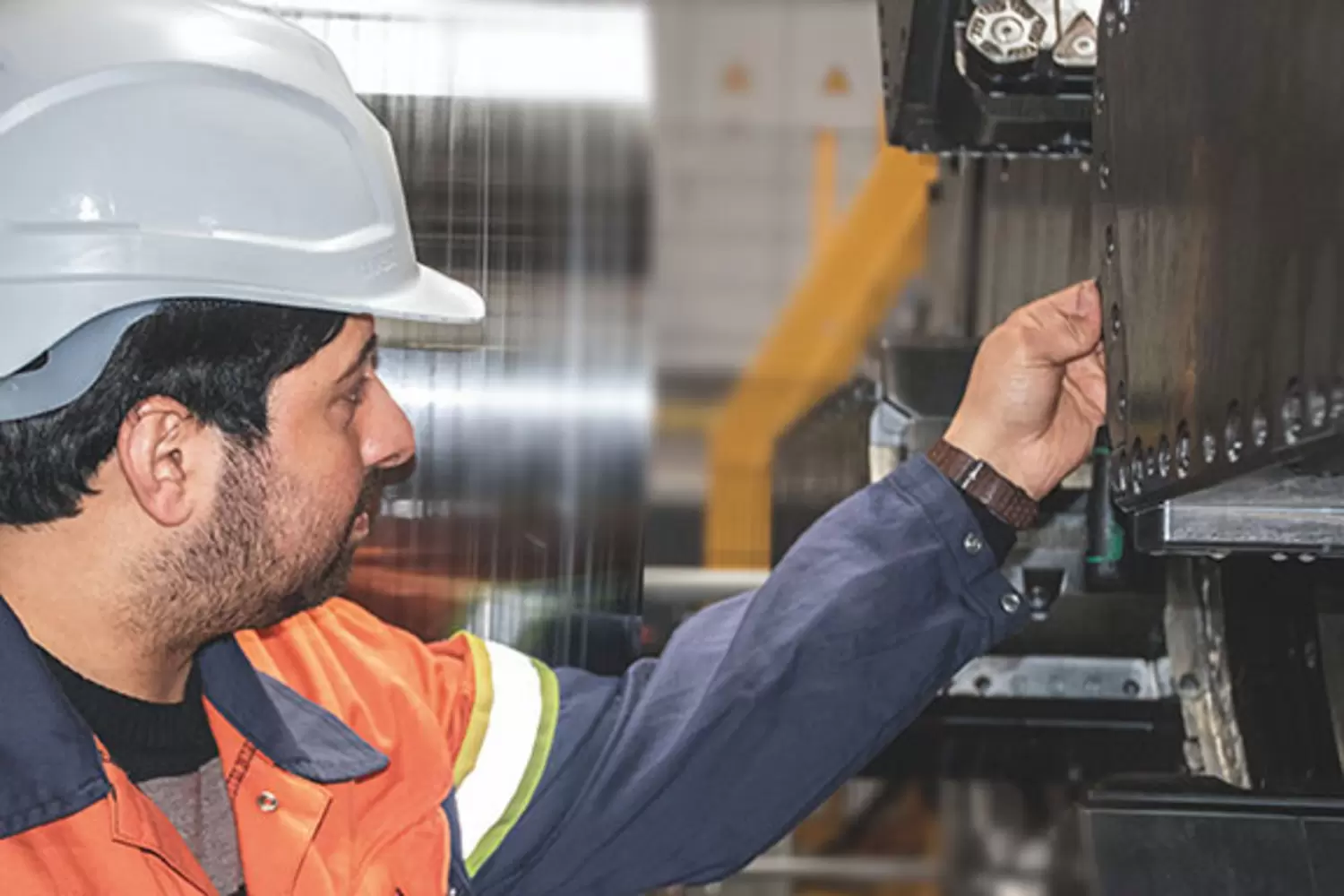