In times difficult for big investments, small solutions helping optimize operational costs (OPEX) or reducing tied-up capital (CAPEX) are even more in demand. The CONDRIVE oscillation drive and the deburrer are two examples of such solutions for continuous casting machines for long products. They include EaaS-Solutions (Equipment as a Service), by means of which high capital expenditure can be transferred to operational expenditure, providing the steel plant operator much higher predictability.
CONDRIVE mold oscillation
Mold oscillation plays an essential role for the product quality in continuous casting processes. Inline adjustment of the oscillation curve – quickly and precisely according to the specific steel grade and section size processed – can make the difference. Simple electric drives are compact and cheap, but they do not have the ability of inline adjustment. Hydraulic drives, on the other hand, are the classical solution when inline adjustment is required. However, hydraulic equipment is expensive, both in terms of investment and maintenance. Instead, CONDRIVE combines compact design with advanced inline control features and is even more precise than the other solutions.
Comparison of CONDRIVE versus a hydraulic drive system
CONDRIVE | Hydraulic drive | |
Revamp (old out - new in) | 1/2 day per strand | > 1 day per strand |
Equipment | Drive | Drive, piping, hydraulic station, test stand |
Maintenance | No maintenance for 3-5 years | Once a year: oscillation test, oil check and flushing, seal check (and change) |
(All values are of indicative nature and depend on the conditions on site.)
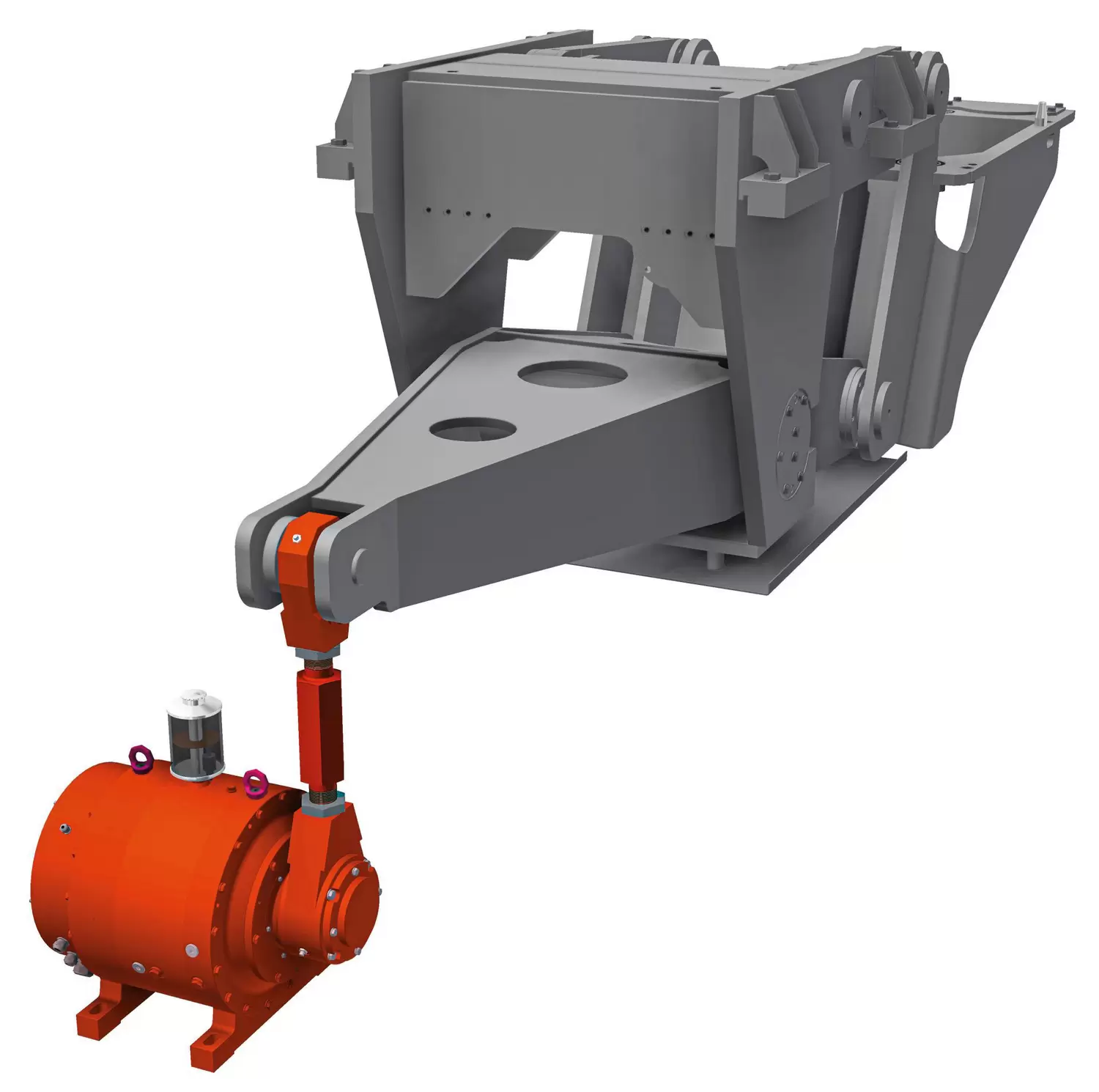
In addition, CONDRIVE’s control unit can be an integrated part of Industrie 4.0 applications - such as SMS group’s product condition analyzer (PCA) – supporting, for example, early detection of possible breakouts.
Since the introduction in 2016, all CONDRIVE oscillation drives have been operating successfully and have to date been sold 70 times in total. One of the first CONDRIVEs has now been in field service for four years - without major maintenance (no bearing exchanges needed). In addition, it has been consuming 50 percent less energy than the former electromechanical drive.
A recent modernization project at TMK Seversky in Russia demonstrates CONDRIVE’s suitability for bloom casters and the short revamping time required: in only half a day per strand, the system was ready for casting, running successfully now for more than half a year. “Thanks to the great cooperation between our commissioning team and the SMS Concast specialists on site, the FAC was released only one week after the start-up”, says Alexsandr Murzin, Head of Metallurgy at TMK Seversky. In particular, for the small section sizes cast at higher casting speeds, TMK Seversky could strongly reduce the break out rate to almost zero thanks to the CONDRIVE oscillation drive.
In order to reduce your CAPEX, you may also lease CONDRIVE as EaaS (Equipment as a Service), including the complete CONDRIVE service package.
Deburrer cuts burrs as well as OPEX and CAPEX
Install a deburrer at the discharge of your continuous casting machine and cut cost downstream at the rolling mill. Rolls are expensive, the downtimes to repair or replace them, too. The deburrer cleans your cast billets and blooms from burrs, which damage the rolls in the rolling mill, and helps you reduce your OPEX. If that was not enough, you may also consider leasing the deburrers from SMS Concast and cut your CAPEX in the process.
Each deburrer has two counter-rotating milling heads, one for deburring the head-end and one for the tail-end. The milling heads contact only the head and tail of the strand, efficiently removing all burrs. As compact, stand-alone units, the deburrers easily fit in most steel plants.
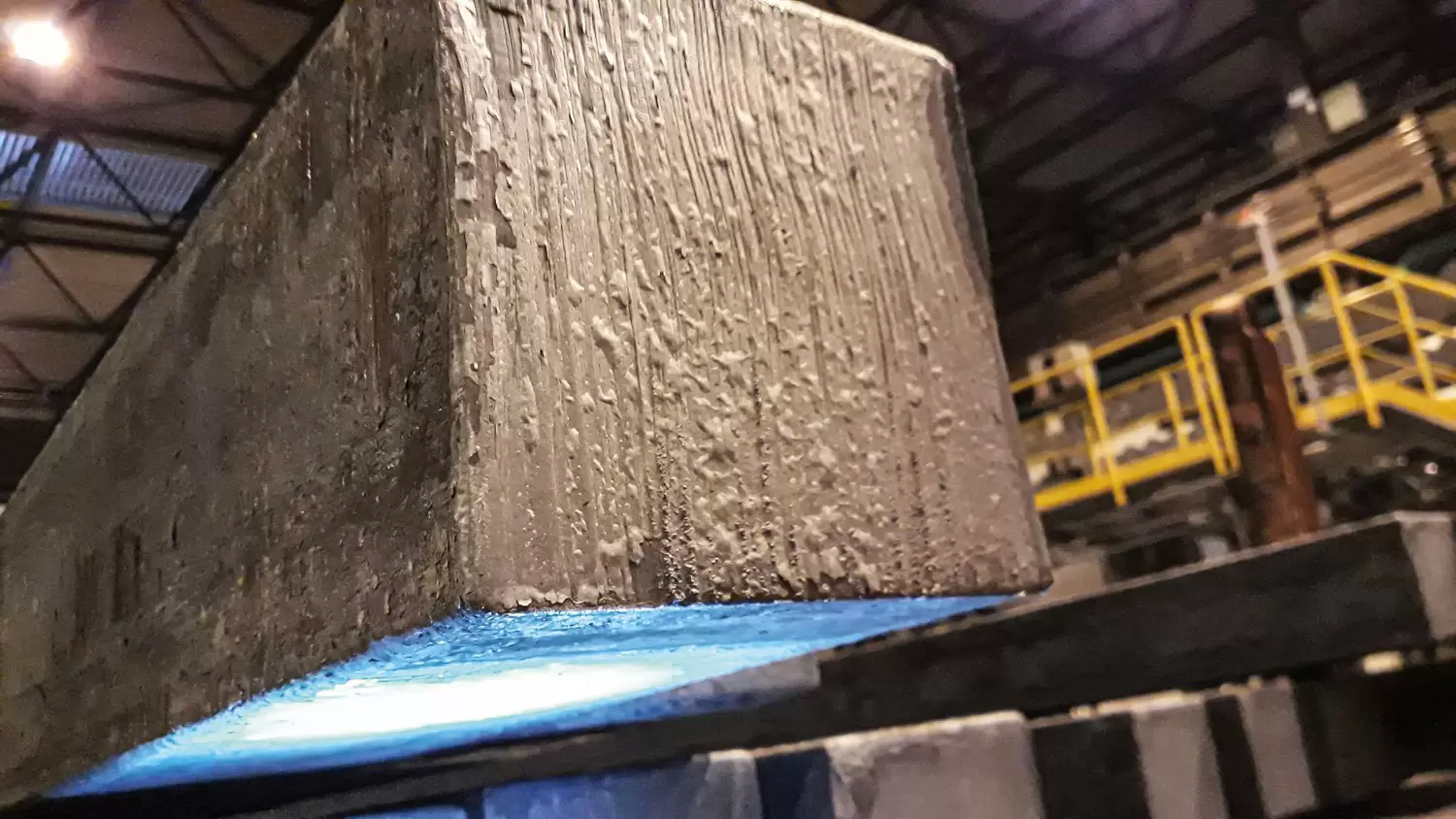