- Modernization, maintenance, repair: The service workshops of SMS group are able to handle orders flexibly
- Customers benefit from short repair times, the use of cutting-edge technologies and total quality management
- With the help of digital solutions – such as predictive maintenance – downtimes can be further reduced
Our own workshops play a central role in the service of the SMS group. One example is the service workshop at Mönchengladbach, where the main focus is on plants for bright steel, bar and wire rod mills, tube and pipe plants as well as all forging lines and presses.
Since 2016, the service workshop in Mönchengladbach is fully operational. The equipment available is state-of-the-art and includes most varied test devices, new CNC machines and machining centers as well as all facilities for comprehensive quality management and final commissioning tests.
Filipe Martins Ferreira: „Our modern equipment alone is not yet decisive for the success. Intelligent use of capacities is essential. We have developed customized solutions providing good capacity utilization of our machine resources on the one hand, but also having sufficient free spaces to be able to react to short-term customer requirements in a quick and flexible manner. Customers benefit from reduced repair times.“
Predictive maintenance
Maintenance shutdowns and servicing within the scope of predictive maintenance are among the main tasks of the service workshop and are meticulously pre-arranged together with the customer.
In the case of predictive maintenance this involves preventive maintenance when most modern sensor technology and digitalization are applied. With predictive maintenance measures, plants can be serviced proactively so that downtimes are reduced significantly. Prior to a malfunction, maintenance work can be ideally initiated by an intelligent data analysis. Such action is more targeted than regular maintenance during scheduled downtime periods.
The more information is available and the better the information provided beforehand, the more our maintenance assignments and the required parts can be specifically prepared. This is a prerequisite to make sure that downtimes are reduced considerably which applies to the scope of predictive maintenance as well as to scheduled maintenance shutdowns.
Overhauling of complete assemblies
A second key factor for valuable time savings is overhauling complete assemblies. Thanks to a modulated machine structure, complete assemblies can be removed and ideally replaced directly by an existing assembly. The assembly is then locally machined either by the Technical Service of SMS group or else by SMS group’s service workshop in Mönchengladbach, where stocked spare parts or provided semi-finished products adapted on the plant can be accessed by the shortest route.
For Thy Marcinelle S.A. (T.M.) in Belgium (part of the Riva Group) which operates a two-strand wire rod mill SMS group’s service workshop has overhauled for example the gear unit of the loop laying head during a maintenance shutdown. The gearbox was delivered to the service workshop on December 18, 2019, and was returned to the customer on time on December 30, 2019. Thy Marcinelle’s head of maintenance was highly satisfied: “Proper maintenance work can only be ensured by good advance planning. We are pleased to have SMS group as partner guaranteeing reliability.”
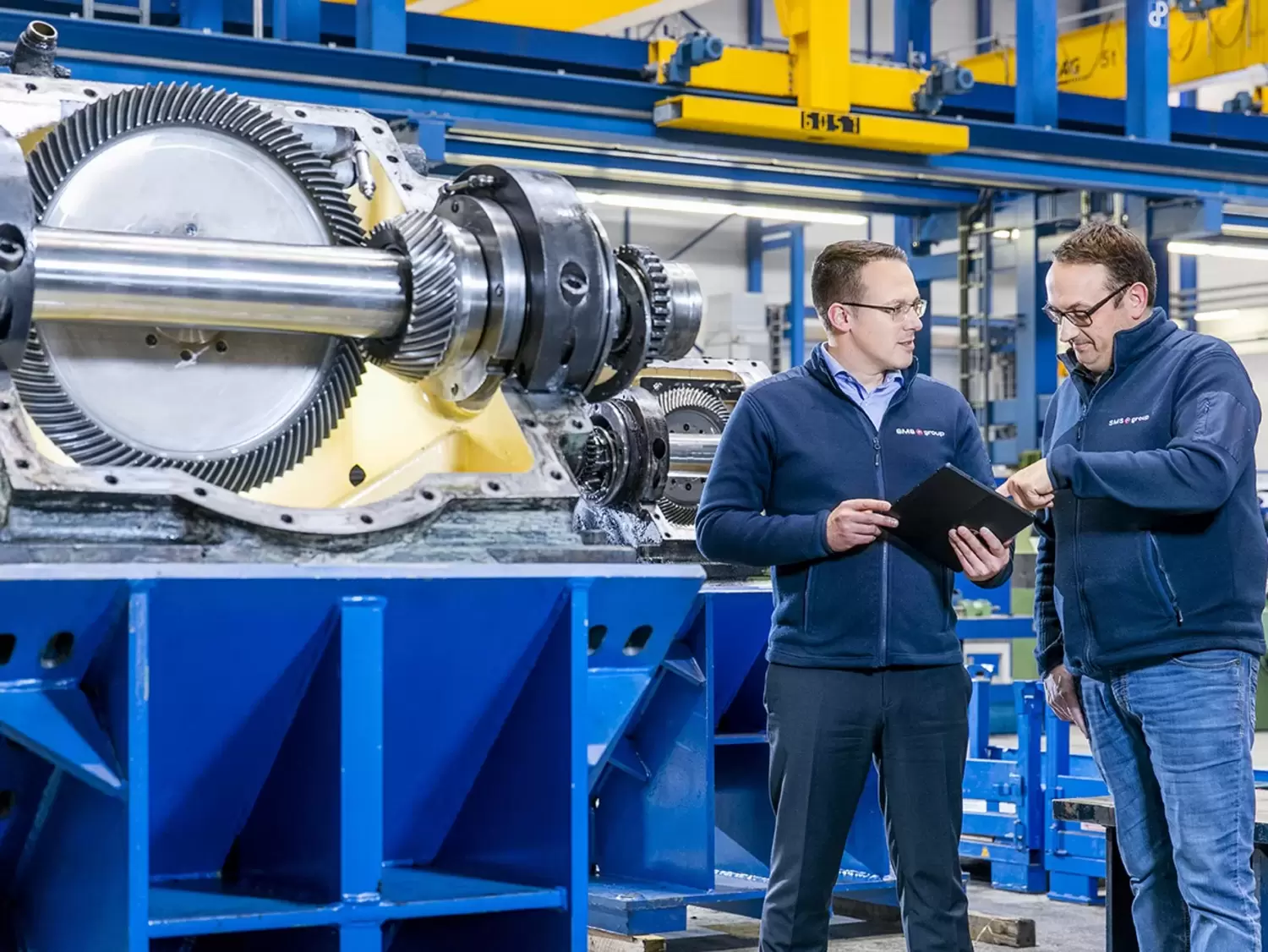
Optimum preparation for short-term repairs
When it comes to failures due to defective plant components, repair measures have to happen very quickly.
It is a major strength of SMS group‘s service workshop experts in Mönchengladbach to be perfectly prepared when unexpected cases of damage occur.
In Filipe Martins Ferreira’s words: “We have matched our machine capacities as well as our personnel resources with these special repair situations. This means, that our flexible shift planning enables us to be adequately prepared to handle emergency cases of the customers so that help can be provided immediately or even at night. For we know: almost each damage case means significant financial losses to our customers when operations are interrupted. For that reason, all repair orders are important for us. We look after each order with utmost priority – regardless of the contract volume.“
For repair parts manufacturing on demand is available in the workshop and service experts are able to manufacture required parts expeditiously.
How a repair assignment is executed in practice and how the deadline is met despite additional expenditure is shown in the example of a French customer. It dealt with the repair of six bevel gears and two finishing blocks of a wire rod mill. In only 14 days, SMS group has carried out the disassembly, damage analysis, reconditioning, replacement of antifriction bearings and wear parts and the quality test, the shop assembly and the packing including return shipment to the customer. Within this time period, communication took place with the customer at the same time about the inspection results, recommendations and quotation approvals.
Worthwhile OEM modernizations
Modernizations are also part of the workshop’s scope of services.
And it is an advantage that as-new solutions are virtually created from old installations at comparatively favorable conditions. Equally important advantages are also certifications concerning in particular plant operators who manufacture components for the aerospace industry or for automotive applications. Modernization solutions of SMS group as plant manufacturer ensure that costly new certifications or audits for their production processes are saved or significantly reduced.
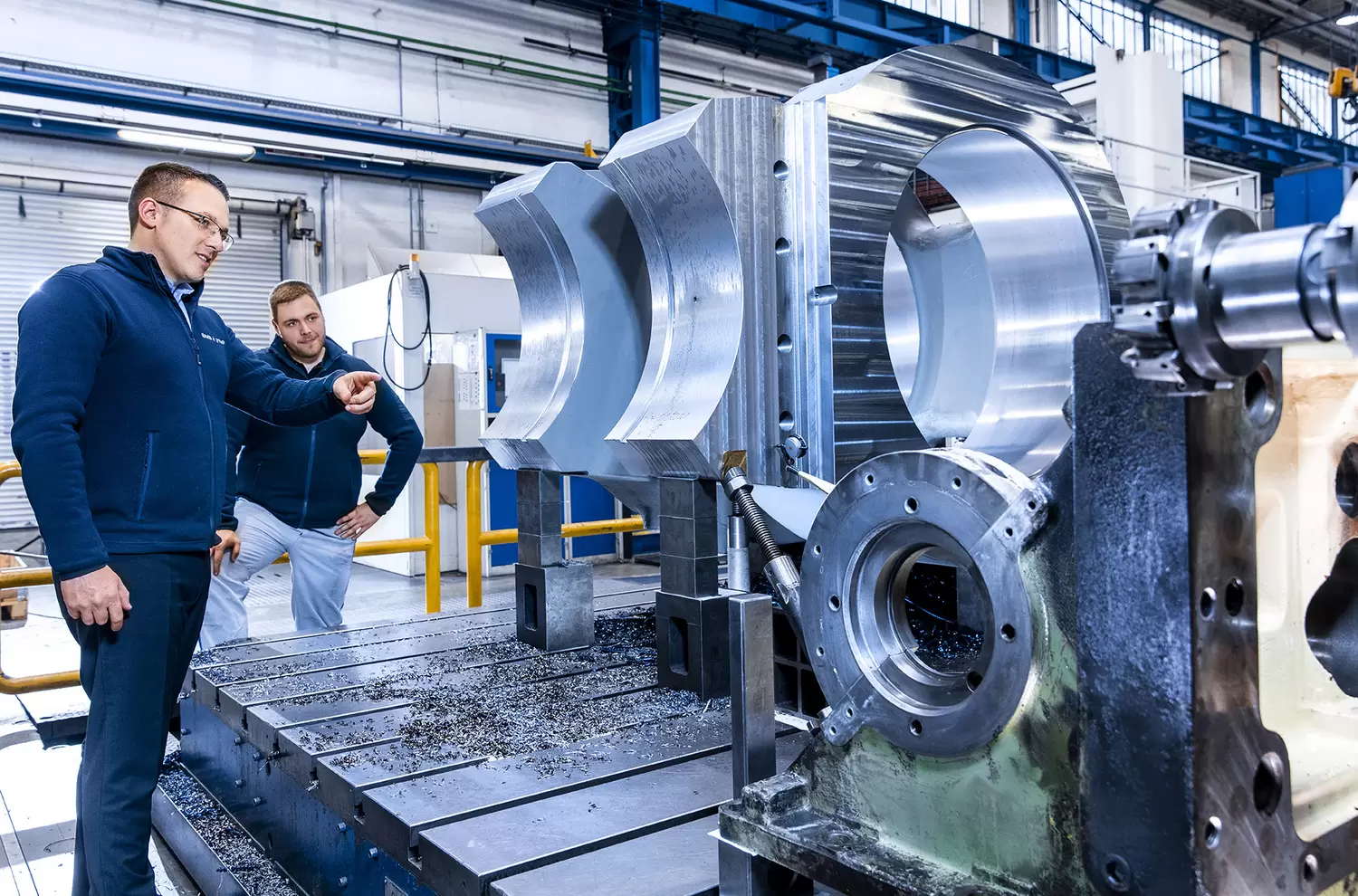
Against this background, a general overhaul of a horizontal forging machine from 1978 should be mentioned. Following the planning, clamping and upsetting slides, overload protection and other assemblies were overhauled. The customer benefitted from a significant increase in efficiency and productivity.
Everything that has ever been manufactured by us can also be repaired by us!
But the example also shows which extensive experiences SMS group’s service experts have gained. Although we live in the digital age and all data and plans of younger machines are instantly provided digitally for service orders this might be different for older installations. The machines of SMS group are often 30 years old or even older. Only old plans and drawings have been recorded.