The scope of this modernization by SMS includes the replacement of the electrical drives and the electronic machine control system with state-of-the-art equipment including the corresponding control cabinets for the ring rolling machine. The main tools will be driven by frequency-controlled three-phase current drives. These are very energy efficient and require less maintenance compared to the direct-current technology used up to now.
By modernizing our ring rolling machine, we will be able to produce more complex and even more precise seamless-rolled rings with various profiles and cross-sections for our customers.
\"By modernizing our ring rolling machine, we will be able to produce more complex and even more precise seamless-rolled rings with various profiles and cross-sections for our customers. Thanks to new drive technology and control systems, we will benefit from improved energy and process efficiency as well as higher plant availability. This will secure our competitive position for many years to come,\" says Simone Baio, who is in charge of the project at Forgital Italy S.p.A.
New sensors and laser technology will be installed in addition to advanced control software and hardware. By using a line laser to measure the outer contour of the ring, the geometry of the outside diameter can be captured in a non-contact way over the whole ring height during the ring rolling process, and any deviations from the desired shape can be identified. This can be done not only for rings with a smooth outer contour but also primarily for rings with an outer profile. This new measuring technology, which was developed by SMS in conjunction with one of its partners, was used for the first time in the largest ring rolling machine at Forgital Italy S.p.A., the RAW 1000/500-4000/500 that went into production in 2017 and has been producing outstanding results ever since.
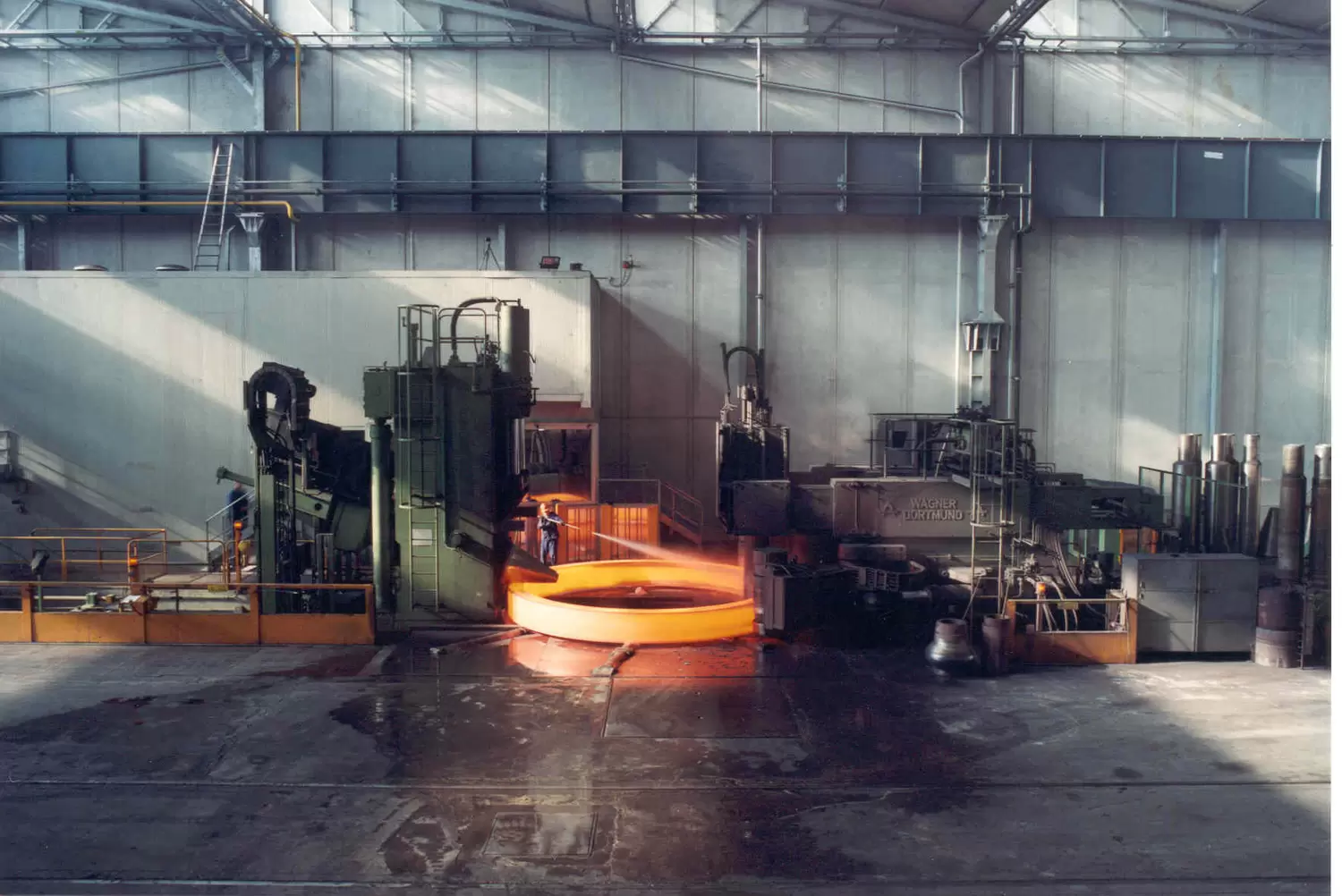
Ring monitoring system
SMS group is also supplying an RMS (ring monitoring system), which it developed in-house. Forgital is impressed with this system, which has already been successfully used in RAW 1000/500-4000/500 ring rolling machine. Working in conjunction with the line laser, the RMS delivers real-time measurements that are displayed in graphical form as the ring geometry and form defects. Form defects can be reduced or avoided entirely thanks to direct feedback to the machine control and interventions in the rolling strategy. This control strategy enables reproducible rolling results and reliably ensures close manufacturing tolerances.