Strip processing lines have to treat a wide product range including state-of-the-art high-strength steel grades. Although some of the materials are difficult to weld, they must properly be joined in the entrysection of a strip processing line within a short period of time.
Particularly suited for modernization projects
As early as in the development phase of the machine, special attention was paid to a compact design with simple requirements on the foundation. The core machine needs an installation space of just 3.5 x 4.0 x 7.5 meters and can hence be provided for in an existing line layout even under challenging space conditions. This means the machine is not only suited for integration in new strip processing lines, but is also perfect for modernizations and for replacing obsolete welding technology.
For the revamp of its pickling line in Hämeenlinna, Finland, SSAB Europe decided in favor of an X-Roll® laser welder. Despite the demanding product portfolio, commissioning could be done within a short time followed by a steep ramp-up curve. At present, a further machine is being installed in the entry section of a continuous cold rolling mill at another European customer.
In SSAB’s modernized pickling line, the X-Roll® laser welder joins steel strip with thicknesses from 1.5 to 6.5 millimeters and widths between 650 and 1,650 millimeters. The welding machine at the Hämeenlinna works in Finland is equipped with a solid-state laser. SSAB decided in favor of the X-Roll® laser welder as the machine permits welding of high-alloy steel grades while keeping cycle times short. After the revamp phase at the end of 2018, SSAB was able to expand its product portfolio. The company can now connect even state-of-the-art high-strength steel grades without any problems and pickle strips in a continuous process at high speeds.

Patented inductive heat treatment of the weld and automated quality assurance system
The welder offers a substantial advantage and that is the patented inductive pre- and post-treatment of the weld, which allows for an individual heat treatment process. Since every combination of materials comes along with individual demands and the range of possible material combinations has grown significantly, the spaces between and hence the timing as well as the applied power of the inductive units can be varied. This means the duration of treatment and temperature are flexibly set to suit the respective material combination.The highly efficient, deep-thermal treatment using medium-frequency induction makes sure the material is completely heated within almost no time and prevents hardness increases in the weld seam area and thus the related risk of a strip breakage. The special design of the inductor considerably reduces holding time as compared to conventional systems and permits even hard-to-weld materials to be welded such as martensitic grades or those with high carbon or high silicon content.
The integrated, automated quality assurance system evaluates the entire welding process. A user-friendly interface provides the operator an indication of the total process. The system checks most different parameters of the weld seam, as for example geometry or temperature, and includes them in the overall quality assessment of the weld seam.
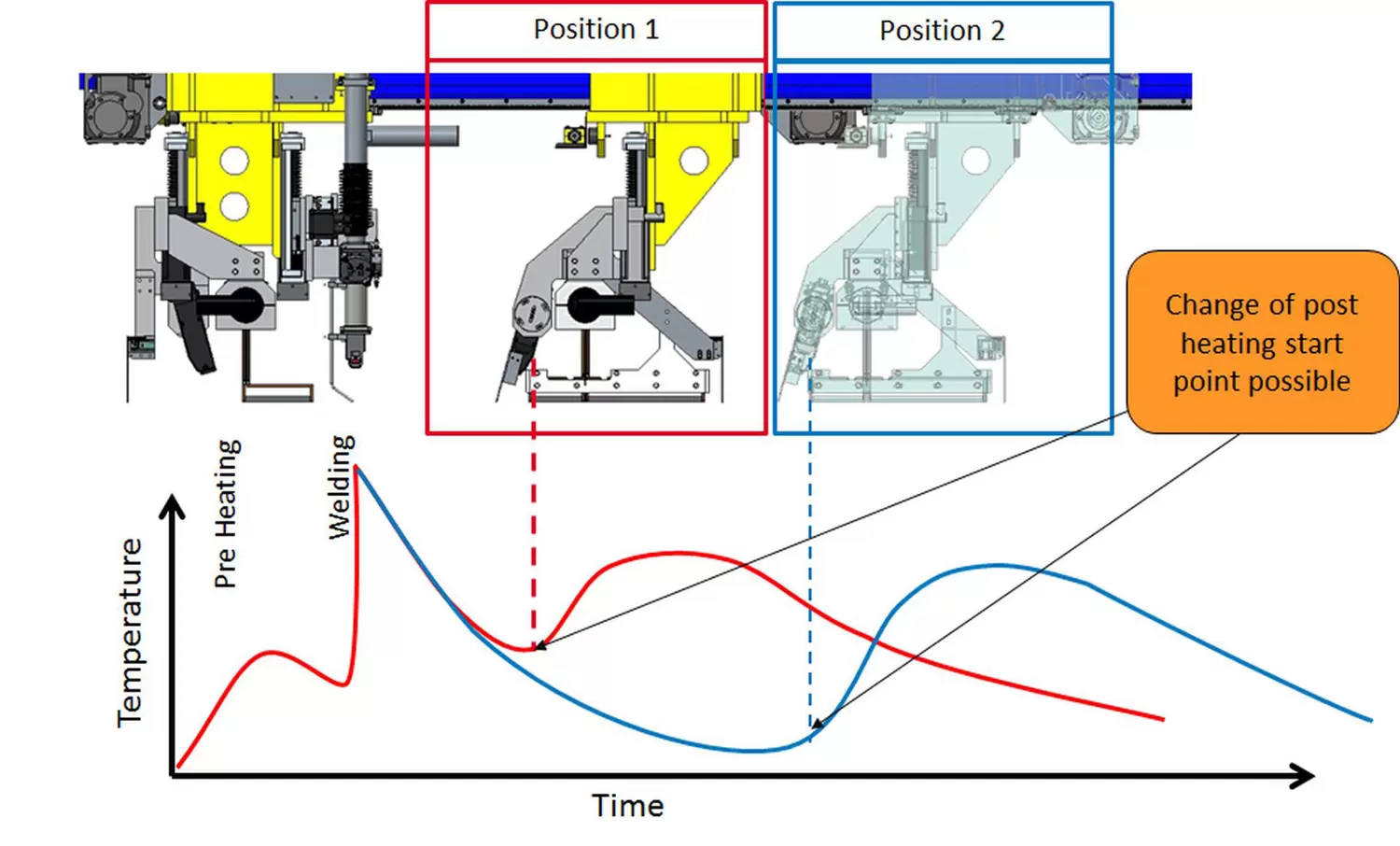
Automatic calculation of weld parameters
Based on the chemical analysis of the steel melt, the automated calculation system individually adapts all weld parameters to the material combination that needs to be welded. Thanks to this automated calculation it is possible to directly and reliably weld even combinations of unknown steel grades. The only data needed for the calculation are the geometrical strip data and the steel melt analysis of the two steel strips.
90 percent of the operating expenses can be saved as compared to conventional machines with carbondioxide laser source thanks to high efficiency as well as lower running and maintenance costs.
Features for high productivity and easy maintenance
Short cycle time reduces idle times
Another highlight of the machine is its clearly shorter cycle time. Thanks to the intelligent machine design all sequences within the welding cycle are optimized, which leads to distinctly shorter total cycle times than common on the market so far. The short welding cycle time results in reduced - downtimes in the entry section of the lines and indirectly permits production to be increased. So, an expansion of the product portfolio is not the only advantage when replacing an existing welding machine.
Fast change of knife cassettes
The time needed to change the shear top and bottom knife cassettes is extremely short, too, thanks to a special system. Both cassettes can be changed in less than 30 minutes. This is the result of an “intelligent machine design” without additional equipment needed by the machine to make such a rapid change possible.
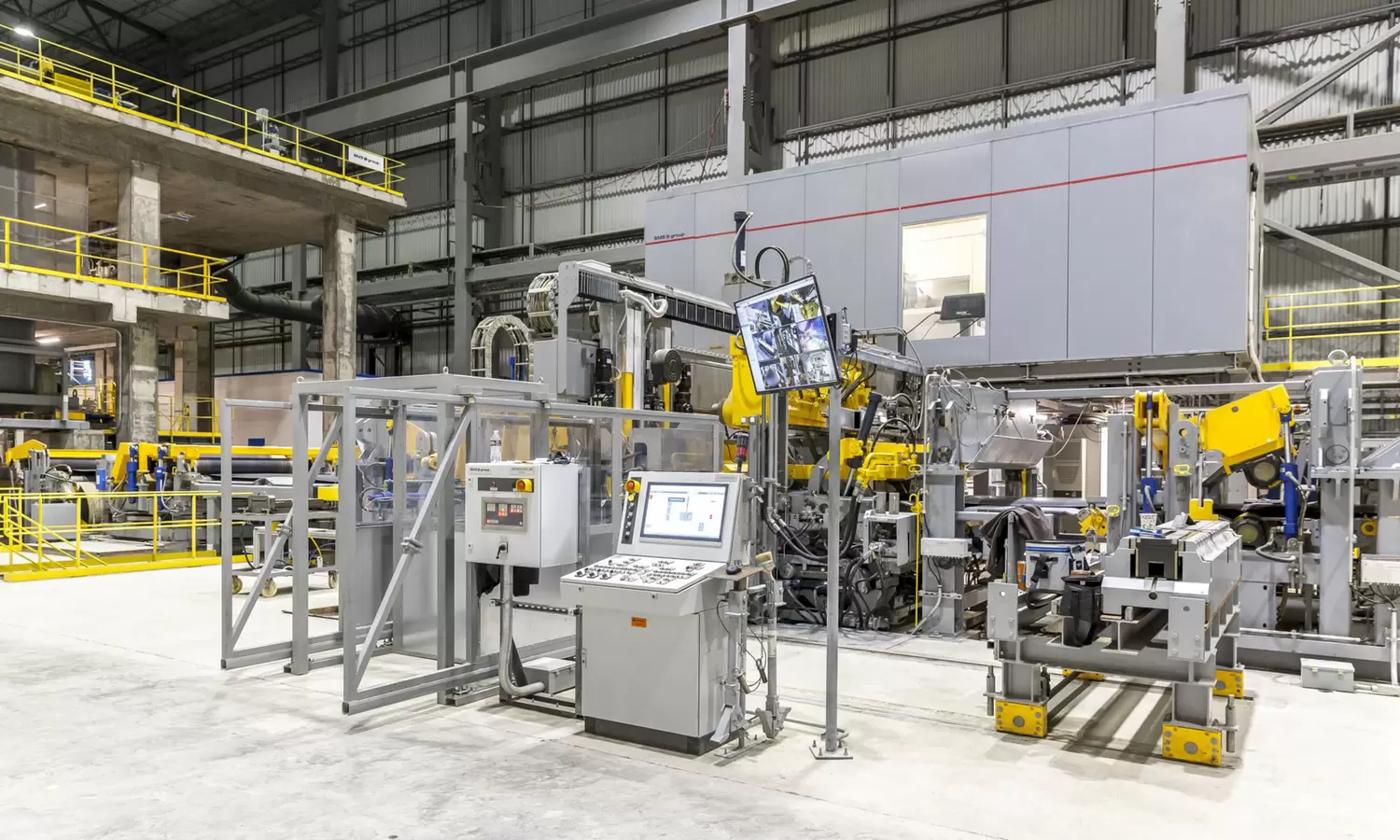
Freely selectable laser source
Due to the modular design of the welder and hence the separation of weld seam preparation and welding process, the laser source can be exchanged easily. This allows customers to use both, a conventional carbon-dioxide laser source or a modern solid-state laser source. The high efficiency, low operating and maintenance costs of a solid state welder make operating expenses drop by 90 percent as compared to conventional machines with carbon-dioxide laser source.
Digitalization
To keep the production process as simple as possible, a number of digital solutions have been implemented in this machine. All relevant data are saved in an archive and may serve as a basis to prepare a maintenance schedule. The machine documentation is available digitally and linked to the various applications. In addition, SMS group offers a remote service able to respond to the customer’s problems at short notice. For this purpose, the expert will virtually connect to the customer’s machine and perform an initial problem analysis.
Technical key data of the X-Roll® laser welder for hot strip
Strip material | Carbon steel, stainless steel, silicon steel |
Strip thickness | 1.0 to 6.5 mm |
Strip width | 650 to 1,950 mm |
Core machine size | 3.5 m (width) x 4.0 m (height) x 7.5 m (depth) |
Core machine weight | 65 t |
Laser source | CO2 / Solid-State |
More information
More information about our X-Roll® laser welder needed? Log in to SMS group #Connect and read our technical paper.
Strip processing lines have to treat a wide product range including state-of-the-art high-strength steel grades. Although some of the materials are difficult to weld, they must properly be joined in the entrysection of a strip processing line within a short period of time.
The X-Roll® laser welder offered by SMS group has been specifically developed to meet the requirements involved in joining hard-to-weld strip material. One of the components developed to master this challenge is a patented, inductive heat treatment system. Further advantages are an automatic welding parameter calculation system, a quality assurance system, short cycle times and an exchangeable laser source. The laser welder has been installed in numerous new plants, but also as part of modernization projects.
The X-Roll® laser welder offered by SMS group has been specifically developed to meet the requirements involved in joining hard-to-weld strip material. One of the components developed master this challenge is a patented, inductive heat treatment system. Further advantages are an automatic welding parameter calculation system, a quality assurance system, short cycle times and an exchangeable laser source. The laser welder has been installed in numerous new plants, but also as part of modernization projects. For the revamp of its pickling line in Hämeenlinna, Finland, SSAB Europe decided in favor of an X-Roll® laser welder. Despite the demanding product portfolio, commissioning could be done within a short time followed by a steep ramp-up curve. At present, a further machine is
being installed in the entry section of a continuous cold rolling mill at another European customer.