Innovative high current switch-mode rectifier for greater sustainability
The X-Pact® High Current switch-mode rectifiers enable customized, module-based DC power supply for electrolytic coating processes, including galvanizing, tinning, chromating, and stainless steel lines. They increase energy efficiency, reduce CO2 emissions, and improve plant availability.
Additionally, X-Pact® High Current delivers maximum process-oriented power supply performance, strengthening our customers' competitiveness. Leveraging advanced technologies such as pulse plating, these rectifiers enable surface design options that cannot be achieved with traditional thyristor DC systems.
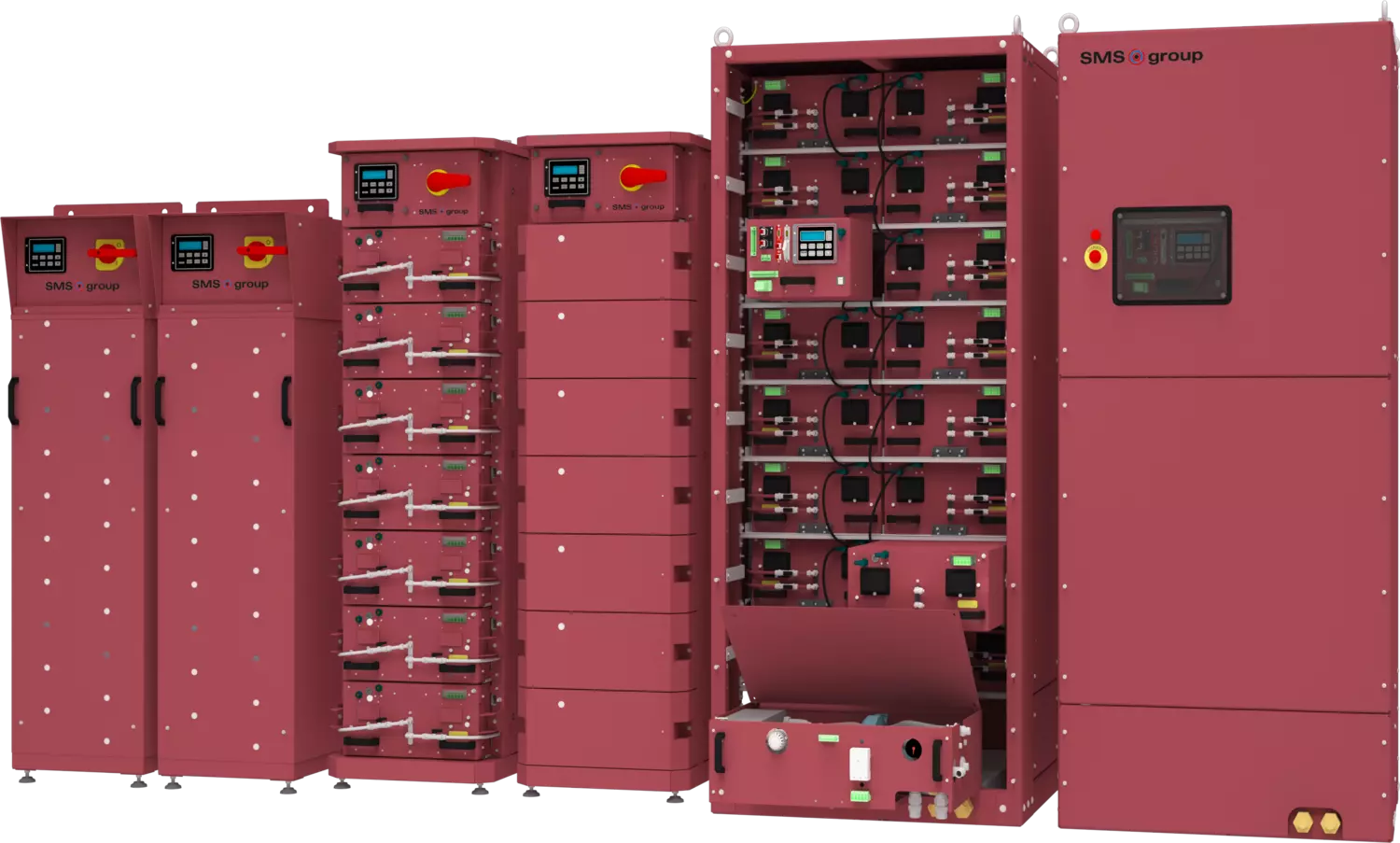
Customer challenges addressed
- Improved surface quality
- Increased wear resistance
- Variable/adjustable hardness
- Enhanced corrosion resistance
- Possibility of multi-layer deposition
- Faster coating process
- Reduction of so-called "paint cracks"
- Decreased risk of "hydrogen embrittlement"