Ring rolling machines are at a standstill for up to half the time during the ring rolling process – either because they are being loaded or unloaded, or because the operator has to wait until the workpieces have been heated. So, to reduce energy losses resulting from these relatively high dead cycle times, experts at SMS group came up with the idea of using electrohydraulic direct drives. "Our colleagues in the specialist departments have very wide-ranging knowledge of electrical and hydraulic systems", explains Martin Gellhaus, who is in charge of sales for ring and wheel rolling plants at SMS group. "So for them the obvious questions was: Why not use the drives that work well in other areas for ring rolling machines too?"
Precisely controlled movements
With the electrohydraulic direct drive, a motor drives a pump, and this is converted into a movement in a hydraulic cylinder. If the speed of the pump is reduced, energy consumption and noise emission levels also drop significantly at the same time. In the case of ring rolling machines, these drives are mounted directly on the rolling axes. This means that they can be controlled extremely precisely – without the movement losing any of its force. When the axes are stationary, the pump is decelerated, at which point the motor does not consume any energy.
Therefore, the drive power required is around 25 to 40 percent lower. The noise level is also reduced by about 15 percent. Another major advantage of the concept known as RAW EH is the lower investment and operating costs compared to conventional ring rolling machines. As the central hydraulic system is no longer required, a room does not have to be built specifically for it, as was usually the case up to now. The costly and labor-intensive pipework is also no longer needed. The volume of hydraulic oil can be reduced by 90 percent. In addition, there is no danger of environmental pollution from escaping oil. This concept incorporates the expertise accumulated with over 500 ring rolling machines that have been built to date. The experience gained with the electrohydraulic compact drives shows just how well the position and force of the axes can be controlled. The reduced number of components means the system is highly robust and barely susceptible to faults.
The RAW ecompact® series was developed for newcomers to ring rolling as well as for job shops. It is available in five sizes – from 63 to 125 tons of rolling force. The RAW ecompact® boasts SMS group's Ecoplants plants label, which the company awards to efficient plant solutions.
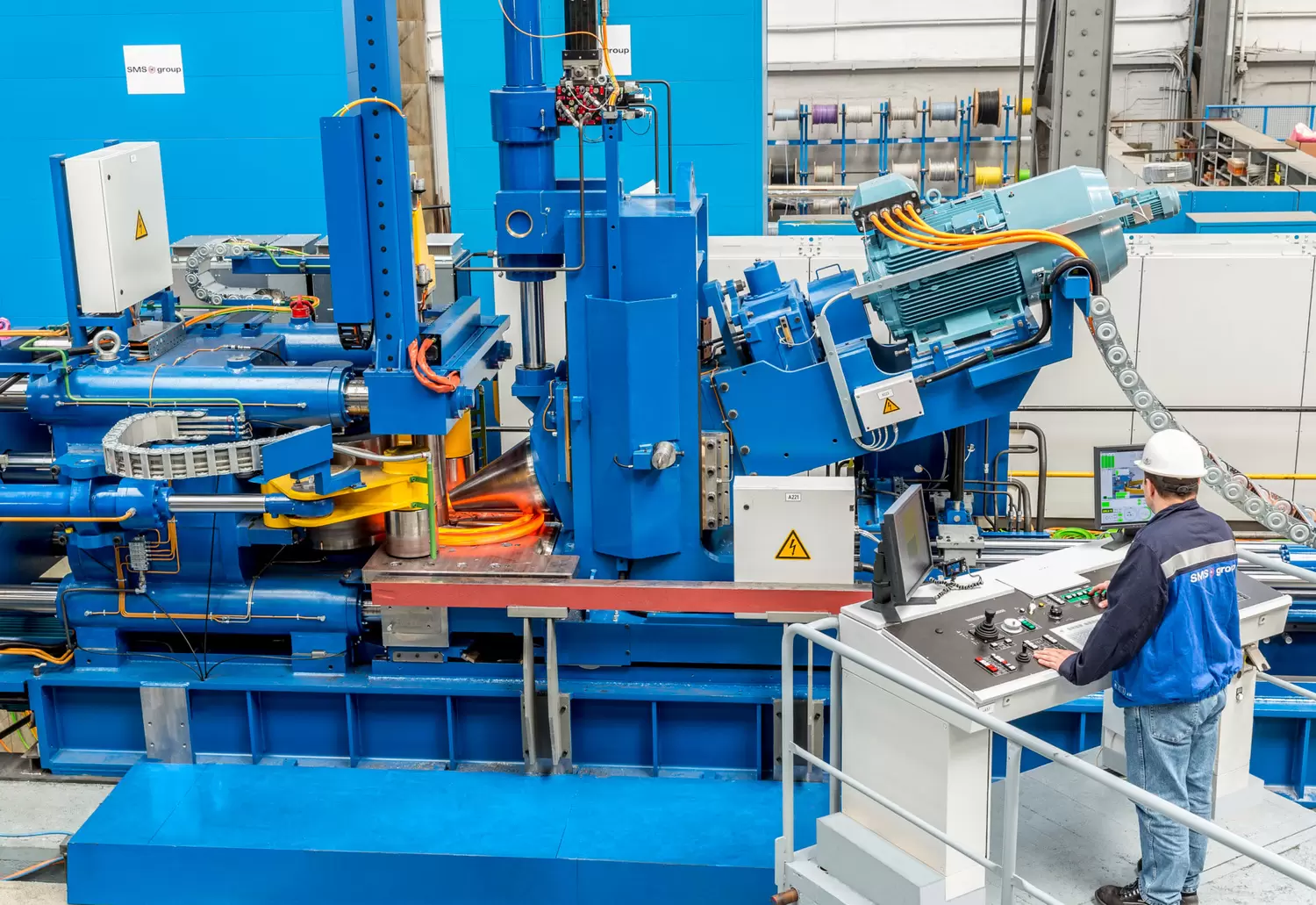
Transferable concept
These innovations do not signify any major change for either SMS group engineers or customers. "Nothing is different for the operating personnel – the look and feel of the machine are still the same. We have to train the maintenance personnel, but that's also the case with conventional drive units", explains Martin Gellhaus. "In terms of the mechanical equipment, other cylinder types that are installed differently in the machine are used", he says in reference to his own team's work. "But those are typical modifications, which are an engineer's daily bread."
Gellhaus can well imagine fitting electrohydraulic drives in other products – like wheel blank presses, for example. \"With wheel blank or dishing and piercing presses, we could apply the same principle we introduced for our ring blank presses", he continues. In 2014, SMS group developed a concept for utilizing speed-controlled axial piston pumps in a 2000-ton ring blank press. Each cylinder drive train consists of four motors. What's special about this principle is that the power supply for the actual forging process is separated – in this case from the power used for lifting and lowering. The cylinder surface areas can be adjusted by means of valves: the cylinder surfaces are large during forging, which produces high forces at low press speeds. During rapid traversing movements – i.e. lifting and lowering – small surface areas bring about small forces and high speeds. The movement of the press is reversed by switching the rotational direction of the servo drives.
This allows energy to be used efficiently here too. As well as applying the power-on-demand principle, the potential energy of the moving mass during lowering is converted into electrical braking energy, just like the decompression energy and the elastic spring energy of the press frame in an unloaded state. This energy is saved in the converter's intermediate circuit and fed back into the mains.
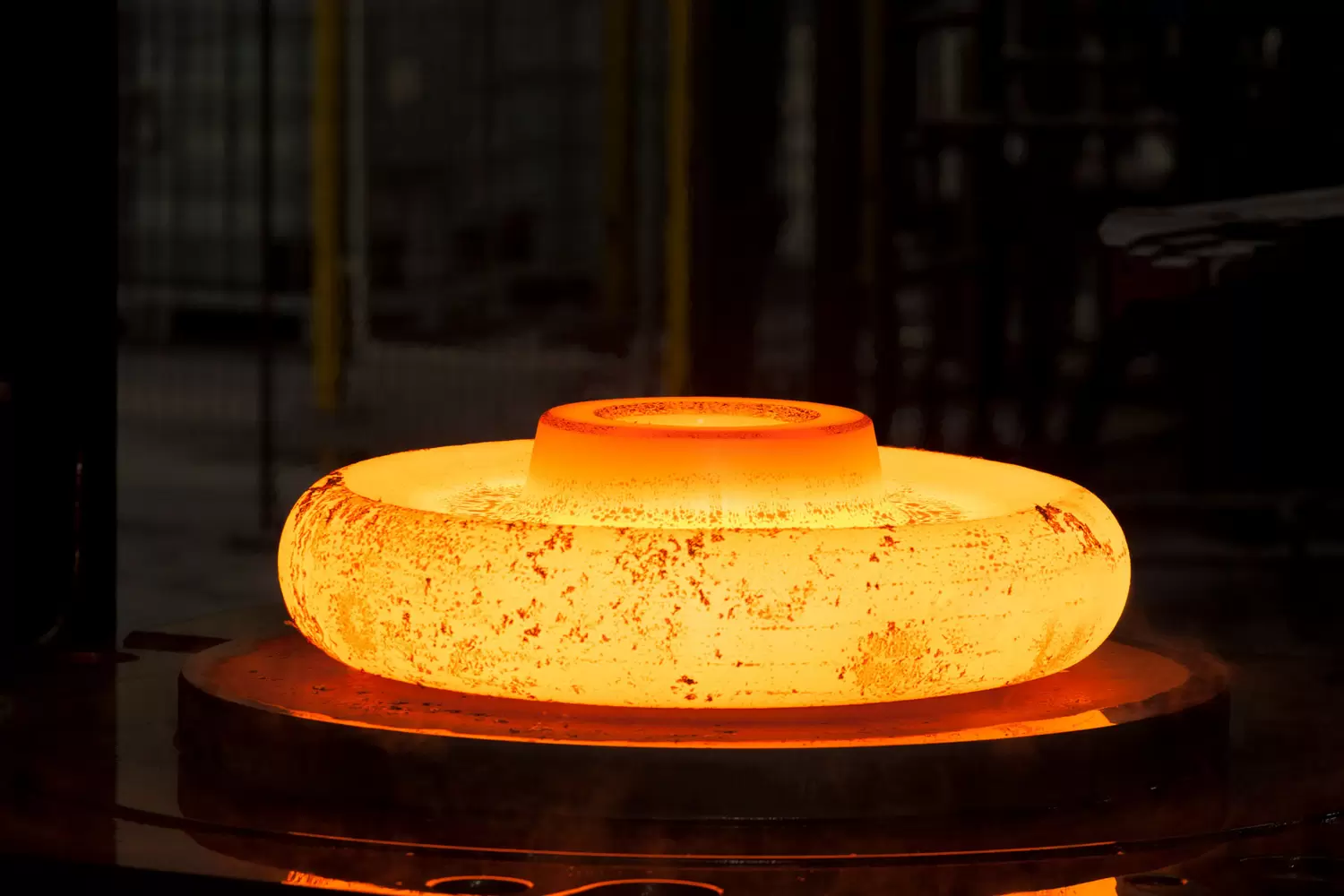