At its core, the project represents a new benchmark in plant design and execution for SMS group, marking the largest and most ambitious order in over 150 years of corporate history. “Since the success of our bid, we have leveraged a consortium of entities from inside SMS to supply the talent and resources required within the enormous scope and quickly developed a holistic project execution approach,” comments Hubertus Jakobi, who led the initial project development and continues to play a central supervisory role. “This, along with the continued determination and commitment from the incredible people we have within the project, will ensure we deliver the best financial results for SMS and our client in this order execution.”
From a project management standpoint, it is a monumental international undertaking, with significant engineering, logistical, and workforce complexity. For this order, SMS is taking on the role of EPC (engineering, procurement, construction) partner, providing thyssenkrupp Steel with a service that includes plant design, through procurement and implementation, right up to the final commissioning. Starting in 2025, up to 1,500 people from SMS, thyssenkrupp Steel, and third-party contractors will be working on the construction site, and even today, project teams across multiple continents within SMS are engaged solely in the execution of this order. So, just how do we design and build a mega-project of this scope, at this speed, and within one of the world’s largest and busiest working steel complexes?
Financial oversight on a whole new scale
With an order volume of over 1.8 billion euros – the largest single order SMS has ever received – every euro budgeted must reflect diligent allocation, something that the project’s Contract Manager, Christine Lohbeck, is tasked with overseeing. “One of the first things is creating a culture of transparency across all project stakeholders” , Christine explains. “There are a number of different entities within SMS that are involved in this project, and it is essential that we are all working in consistent ways,” Christine comments further. In order to drive this success, the development of harmonized structures to have a clear budget and cost allocation have played a vital role. This, along with the constant identification of risks and chances, close collaboration between sales and order execution teams from the start and a stringent reporting structure, are working together to support the project’s commercial success.
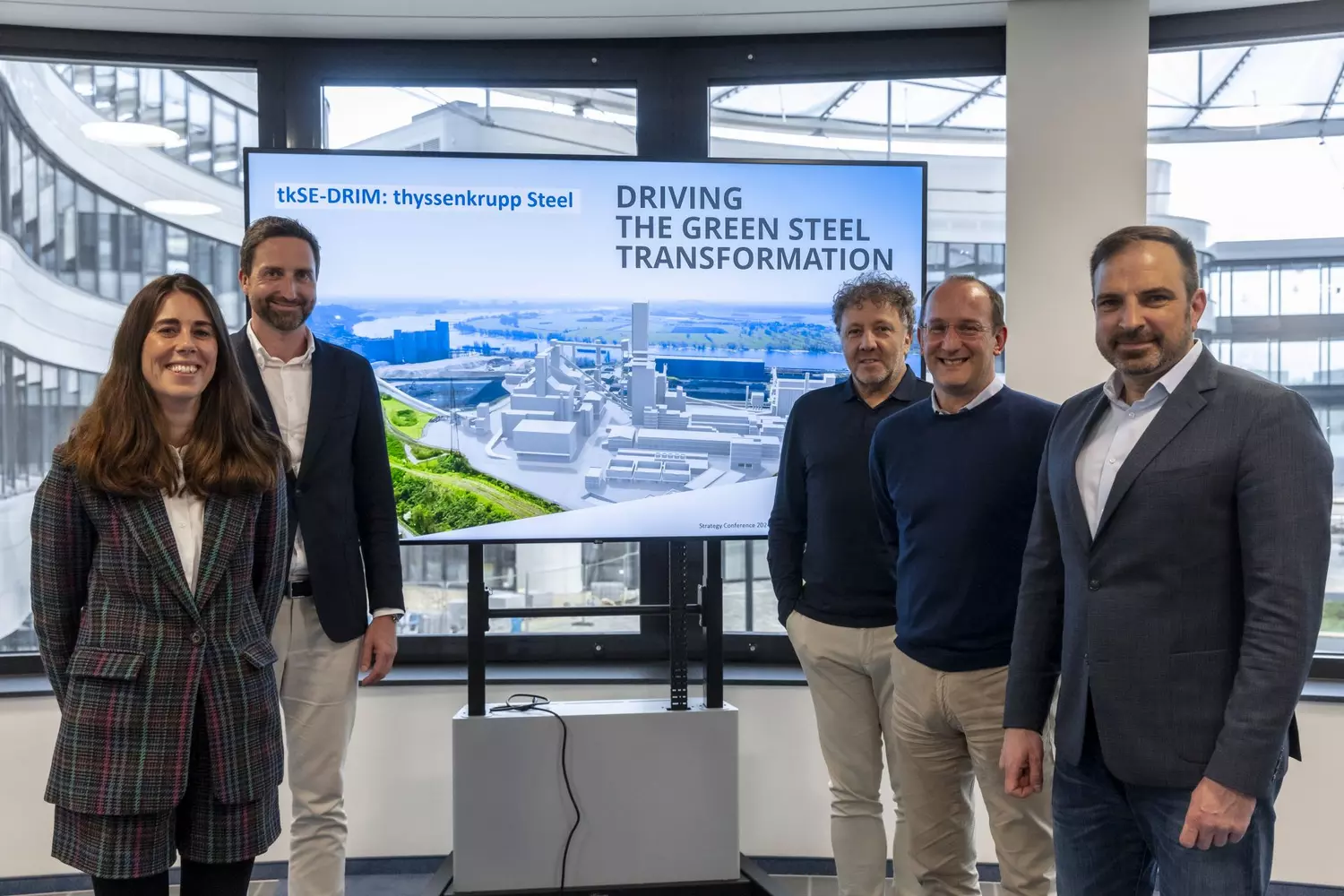
A virtual world of opportunities
One of the more exciting advancements in the project engineering has been the introduction of a virtual reality tool that models elements of the completed plant site in a detailed, to-scale rendering. Transforming the possibilities of collaboration, the tool allows global project team members to enter and discuss elements of the design from within the plant itself, at any time and from any location. By experiencing the design, at its actual scale, and seeing how elements are positioned after installation, the team is able to pinpoint and work through any topics of concern prior to construction and avoid future delays as the project scales through its phases of implementation. “We are only starting to experience the capabilities of virtual reality in revolutionizing our ways of working,” comments Jan Buchner, who spearheaded this element of the project. “We can now work inside the structure and critically examine the infrastructure of the plant, before it even exists, which is truly a game changer in engineering,” he concludes.
90,000 tons of equipment
When designing and building any plant, one of the foremost challenges is sourcing the equipment and transporting it to the site for installation. So, with over 90,000 tons of equipment needed to complete this project, a global sourcing effort was the only way forward, requiring incredibly precise planning and scheduling strategies from the experts in the supply chain core team. “With our meticulous approach to project scheduling and active controlling across execution deliverables, we can be sure that a solution will be found for every challenge, be it in material procurement, transportation, or shipment deliveries,” comments Daniela Cattolico, head of the Supply Chain team. Along with the manufacturing scheduling for the project, identifying reliable suppliers who meet these demands is the backbone of the procurement approach. For this project, the Supply Chain team undertook a total cost of ownership analysis cycle in the supplier selection process. That means analyzing each potential supplier from a procurement, quality, and transport cost viewpoint, in order to make the most effective selection.
Once suppliers who best meet the commercial needs have been chosen, a dedicated expediting team continuously monitors progress to align with agreed dates of delivery. Over and above this, import and quality controls must be further synchronized to ensure a smooth flow of the components and materials.
Delivering the right part, at the right moment
With space extremely limited on-site, logistical operations are heavily dependent on a highly coordinated delivery schedule and the use of multiple short-term warehousing and pre-assembly locations. “The most important thing for me and my team is to create a cohesive execution strategy, based on strong cooperation, which delivers a unified source of truth for all matters related to logistics,” comments Andreas Ulrich, who heads this element of the operation. As the majority of components and materials will be transported on barges on the river Rhine, warehousing areas along the route will be selected. To further minimize costs and environmental impact, the source location of the components is factored into the warehousing selection process and optimized to create the shortest possible journey to the site. In addition, the specific storage conditions for the various materials, which range from sensitive electronic components to large-scale steel structures, will play a critical role in the selection. A sizable proportion of the materials to be delivered comes from outside Europe, which further increases the logistical requirements under these special conditions.
During certain project phases, a high-volume of daily deliveries will be required. “For this project, we have what you might call a ‘just-in-time delivery model’ that ensures materials arrive exactly when they are needed, reducing on-site storage needs and logistical costs,” comments Andreas. To meet the challenges of this highly synchronized approach most effectively, a centralized digital logistics tool has been implemented to enable real-time coordination between our teams, suppliers, warehouses, transport companies, and external construction contractors.
Imagine building an Eiffel Tower in a football field. Then multiply it by eleven.
For the team leading the construction, two words come to mind when discussing the project requirements: space and time. “To build a plant of this magnitude within the allocated space is for me, at least, an unprecedented undertaking,” comments Thomas Dunschen, Construction Manager of the project. To understand just how large the structure on the building site will be, Thomas breaks it down: “We essentially have the steel structures of eleven Eiffel towers being erected within the space of eleven football fields.” On top of this, the construction site is surrounded by active facilities that need to continue operations uninterrupted by the building work. One of the ways the team is alleviating this is by utilizing a 40,000 square meter pre-assembly area about 500 meters from the construction site. The equipment will also be pre-assembled as far as possible, so that as soon as the equipment arrives on-site, it can be picked up and taken to its final position for immediate installation. As the number of activities occurring simultaneously increase during the peak phases of construction, a comprehensive approach towards occupational safety, with rigorous on-site training and controlling, will ensure the well-being of our people remains the top priority during project execution.
One of the most prominent highlights from the construction process will come later next year, when one of Europe’s largest cranes will be installed on-site and remain there for several months. The crane will be a temporary landmark in the skyline, towering over the existing infrastructure as a beacon of the sustainable steel transformation that is underway.
The green revolution is already underway, and together with a customer with one of the most illustrious histories in the industry, we are ready to deliver a new era of production, right in the center of Germany’s heart of steel, for generations to come.