Mr. Sandberg, in what strategic direction is SSAB aiming in terms of CO2 reduction and sustainability?
Jacob Sandberg: We are already one of the world's most carbon emission-efficient steel companies and, with this project, we are set to revolutionize iron-ore based steelmaking. Our aim is to be the first in the world to deliver fossil-free steel to the market by 2026. We will largely eliminate CO2 emissions from our own operations by around 2030, offering customers the competitive advantage of a completely fossil-free value chain. The new electric arc furnace (EAF) will play a crucial role in realizing our transition plans and in lowering total CO2 emissions in our country by 3%.
What CO2 savings does SSAB expect to achieve with the secondary route? Will SSAB be able to offer new low CO2-emission steels?
Jacob Sandberg: Our goal is to enable our customers to achieve significant CO2 savings by reducing emissions across the value chain, and we want to be very transparent about that. With our Fossil-freeTM steel, our customers know that their products are manufactured from premium material using only fossil-free energy sources. SSAB Fossil-free™ steel will be launched on the market in 2026.
In 2023 already, we launched SSAB Zero™, a zero-emission steel made from recycled raw material. By incorporating recycled steel into the production process, SSAB Zero™ contributes to the circular economy and helps to reduce the environmental impact of the steel industry. The EAF facility in Oxelösund will be very flexible, allowing us to produce Fossil-freeTM, SSAB Zero™, or conventional scrap-based steel semis.
Besides the sustainability aspects of electric steelmaking, what expectations do you have of your new plant and what do you expect from SMS group after the project is finished?
Jacob Sandberg: We expect more environmental benefits beyond CO2 emission reductions. Emissions of SO2, NOx, and dust will be significantly lower, and process water emissions will be avoided completely. Sea water will be used only for cooling, and heat exchangers will be employed. We also anticipate improvements in volume and cost flexibility.
We look forward to continuing our close partnership with SMS, not only in steelmaking but also in digitalization, as we have seen with plate production.
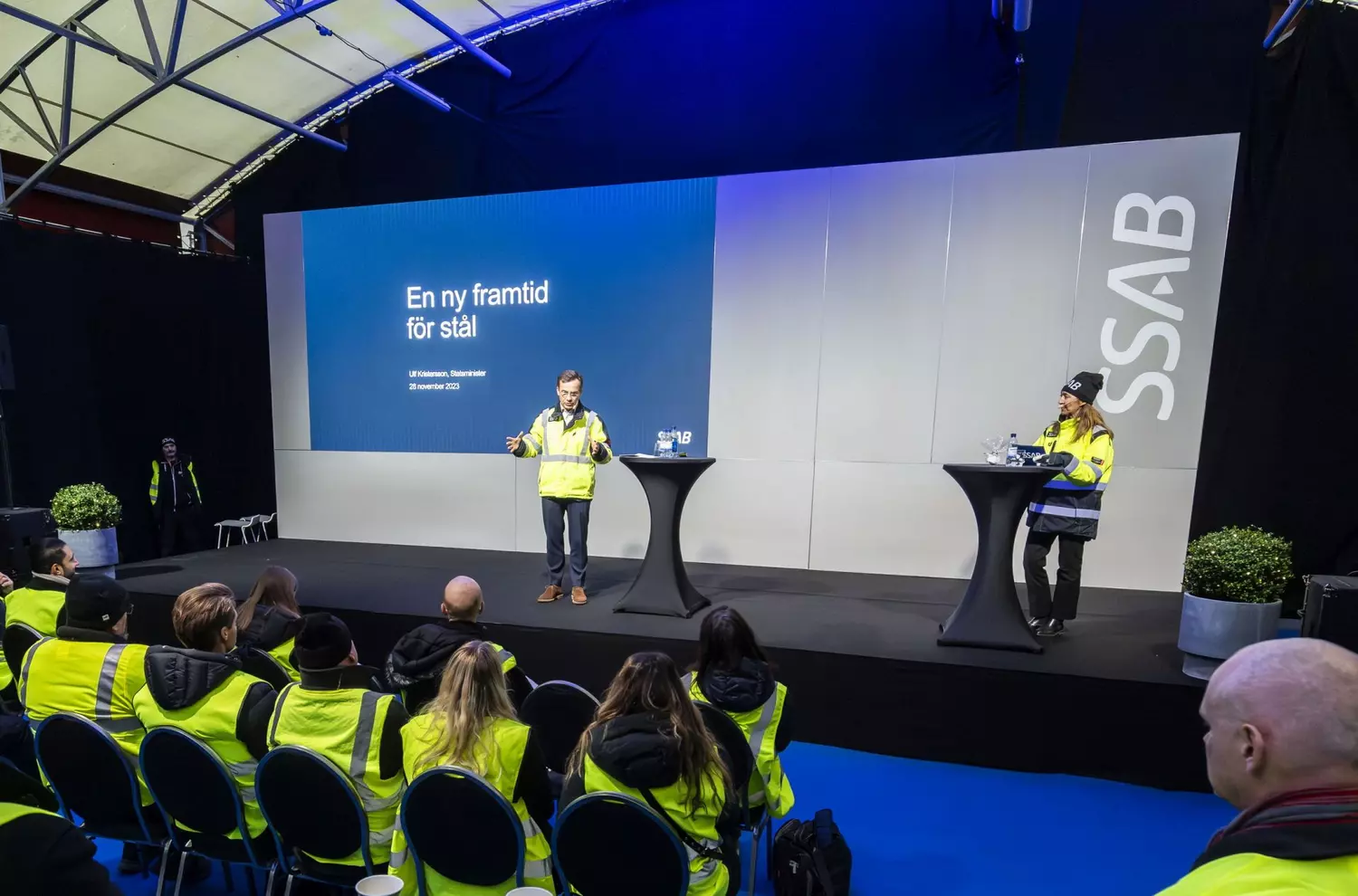
With an upper shell diameter of 9.3 meters, the new EAF is one of the largest installations in the world for similar applications. Are we setting a new standard here?
Andrea Lanari: You can count on one hand the number of installations with such dimensions installed around the world. The trend for larger facilities is driven by the need for decarbonization and for replacing the blast furnace-basic oxygen furnace (BF-BOF) route with electric steelmaking. BOF steel shops have larger heat sizes, upwards of 150 tons, therefore the new equipment has to fit in with the existing size of equipment. Another factor is the large amount of DRI to be melted in EAF, as this requires more electrical energy in the balance. SMS is pushing the boundaries as regards size and power, and with 280 MVA, the SSAB furnace will be one of the most powerful installations ever.
Briefly, what are the key features of the new EAF? How does the project and the applied technologies demonstrate both companies' commitment to reducing CO2 emissions and leading the industry towards a greener future?
Andrea Lanari: The design of the furnace enables the charging of scrap and cold direct reduced iron (DRI) from 0 to 100%. Keeping the same productivity with different raw materials requires a perfect balance between mechanical and electrical design. The combination of modern solutions like the automatic slag door, latest-generation chemical package, ferro-alloys feeding, slag detection, and off-gas analysis provides for automatic furnace control. This aims not only at minimizing the carbon footprint but also at enabling fully remote processes. Zero-carbon direct reduced iron is also part of the mix, driving the carbon footprint level down further to unprecedented levels. Process knowledge is a key factor here, and the combination of core metallurgical models with digital AI will enhance the utilization of such a green material.
This project was not only about defining technology and negotiating conditions. Can you describe the roadmap leading to this order?
Maria Kmiecik: The collaboration between SSAB and SMS group has been a visionary journey. It began in 2017, when we were contacted by SSAB Oxelösund to explore the transition to electric steelmaking. We conducted metallurgical calculations for over 20 different charge mixtures, refining the project's parameters through constant dialogue. In 2019, SSAB commissioned us to conduct an engineering study for the implementation of the electric steelmaking plant. Together, we developed a comprehensive process concept that addresses operational requirements and considers environmental and space constraints. By the first half of 2023, the project scope and layout were solidified, incorporating additional constraints such as civil engineering considerations, an extremely ambitious exceptional timeline, and spatial limitations for the construction phase. In August 2023, the cooperative efforts resulted in SSAB entrusting us to advance to the execution phase of this sophisticated melt shop project.
The order also includes advanced automation and digital tools. Can you tell us something more about this?
Maria Kmiecik: Let me explain this with the example of the scrap handling process. Instead of using an open scrap yard, the scrap is stored in containers near the melt shop. Thanks to a high number of containers, continuous production is enabled with a scrap charge of up to 100%. This set-up not only streamlines SSAB’s raw material processes, but also dramatically reduces transportation times, thus optimizing overall operational efficiency and control. In addition, the use of containers ensures minimal noise emissions.
Our new digital scrap logistics system drastically reduces manual labor and potentially provides greater scrap handling precision. The system tracks and schedules the scrap supply and ensures that the right type of scrap is delivered in the correct quantities at the right time.
Beyond scrap handling, the overall digitalization package also consists of a steel plant-specific data warehouse solution, data analytics, and a digital twin of the EAF’s physical asset. These integrated tools ensure better planning and execution of steel production schedules and maintenance activities. By integrating SMS systems, SSAB can more effectively produce the specific steel grades and qualities that their clients order, as the composition and timing of scrap charging are critical factors in achieving the desired steel properties.