Since the target settings for CO2 emissions have become more and more stringent and this development is accompanied by an ongoing trend, especially in the automotive industry, towards ever lighter structures and hence to an increased use of the material aluminum, there is consequently a higher demand for innovative heating and heat processing applications.
The advantages, in addition to a small footprint, are flexible, dynamic temperature setting, low scale formation or oxidation, and recently the use of CO2-neutral electrical energy.
The good electrical conductivity reduces the attainable electrical efficiency of the induction heating process for aluminum compared to that of steel. According to the physical law of Wiedemann-Franz, the good electrical conductivity of a material is proportional to its thermal conductivity. This means that material temperature differences are compensated faster than in steel parts, for instance. For that reason, aluminum workpieces, usually cylindrical billets, with diameters of up to 800 millimeters can be inductively heated in a fast and efficient manner.
Two types of heating
At present, the most widely used induction heating procedures for aluminum billets are individual heating and pusher- type heating. In the individual heating mode, billet diameters rather range from medium to large size (150 to 800 millimeters) with long cycle times between just a few up to 30 minutes. In the pusher-type mode, diameters are small (between 20 and 150 millimeters) and cycle times short lasting just a few seconds.
Individual heating
The individual heating mode is preferred for long cycle times as encountered in the extrusion of aluminum billets with large diameters and provides the advantage of flexibility when heating different billet lengths. Additionally, nonproductive times for billet transport are of little significance due to the long cycle times involved. The typical procedure is to feed in the billets via a portal and deposit them on a water-cooled transport system ahead of the inductor. Together with the billet, this transport system moves into the inductor without any friction between workpiece and system. After the inductor has heated the billet to the specified temperature, the billet is returned to loading position ready for further processing. Individual heating may be advisable for smaller diameters as well. This applies to small quantities in medical technology, for example, or when aluminum is to be heated up to the thixotropic state. In such cases, billet transport may be accomplished with or without relative movement between deposit and workpiece.
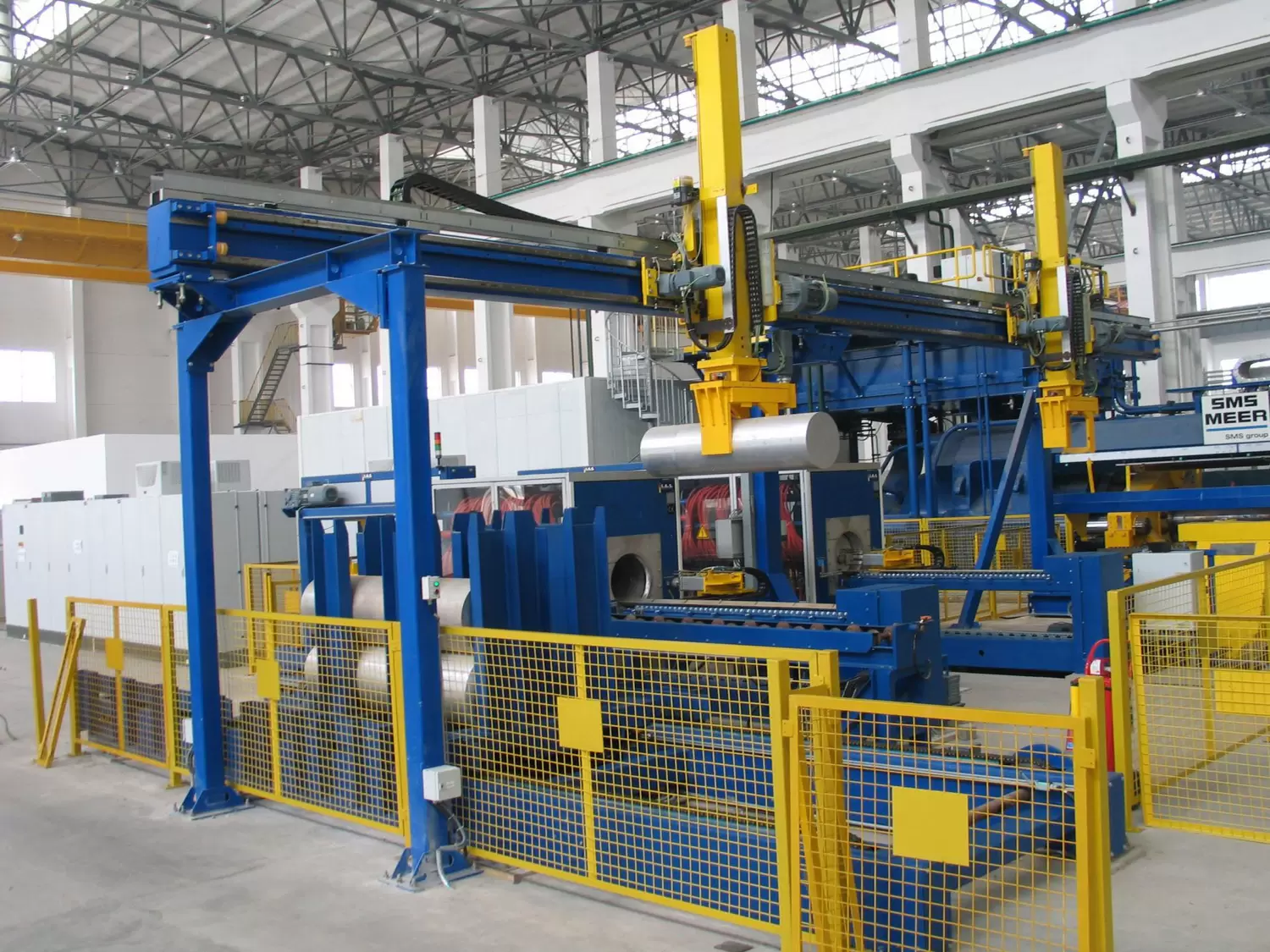
One fact has turned out a special advantage in the heating process, in particular for isothermal extrusion where the temperature setting over the length of a billet is not homogeneous, but rises along the length (taper). Therefore, independently controlled heating zones are integrated in the inductors with each zone being controlled by a separate temperature measuring unit. This allows a temperature profile to be preselected in several temperature steps, which is then adjusted and compensated depending on the performance in the individual zones. Due to the good thermal conductivity of aluminum the temperature profile over the length is almost linear.
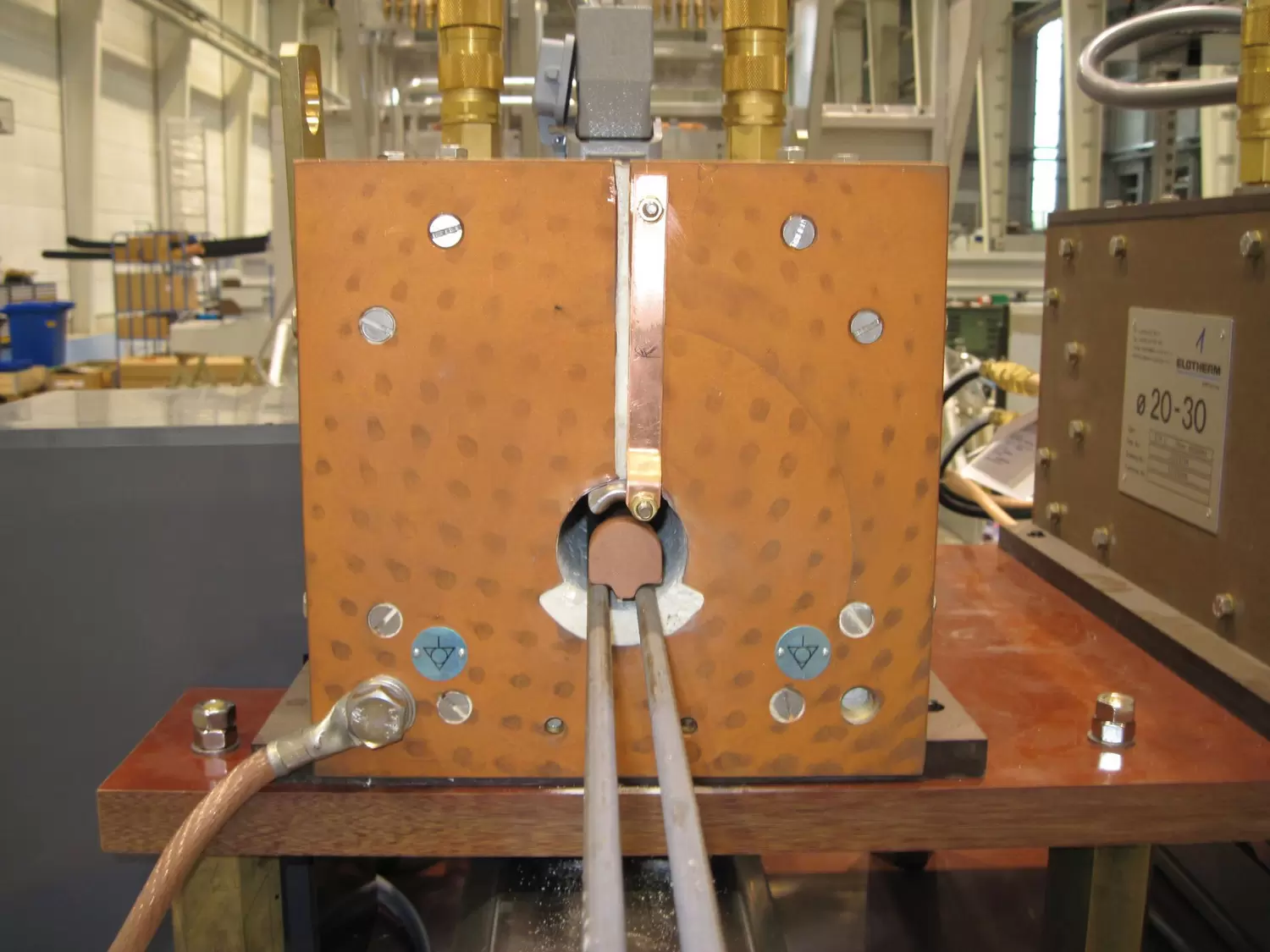
Pusher-type heating
In pusher-type heating systems the material may be fed to the induction heater in different ways, for instance via a vibrating chute or by a robot. One after another, the billets are then pushed through the machine. Pusher systems have proven to be reliable driving units in practice as they can move the material column either continuously or clocked. During the heating process, the column rests and slides on water-cooled guide tubes.
Belt conveyor
Since unit weights of smaller sizes (< 60 millimeters) are low, pusher-type heating hardly creates problems with surface quality. Exceeding a critical combination of unit weight and required surface quality, however, may have negative impacts on the surface in the hot area caused by the skid rails. Simultaneously, cycle time in this diameter range is not yet long enough for individual heating respectively the effort involved is disproportionately high.
This is where the belt conveyor comes in. It unites the advantages of the heating methods mentioned above, and for medium diameters it can implement short cycle times without relative movement between workpiece and machine. Here, the workpieces are supported by an endless textile belt instead of a pinch roller and skid rail combination.
This is a challenge to the belt material. It must not be electroconductive and be capable of withstanding temperatures of about 500 degrees Celsius for a long time. The transport concept selected was a combination of pulling and pushing to keep the mechanical load on the belt as low as possible and thus to attain a long belt service life. The pinch roller already mentioned above is operated in sync with a belt drive and has just a supporting function to prevent the belt from crumpling. Deflector rollers at both ends of the inductor unit are used to thread the belt in and out of the inductor. Thus, a billet resting on the belt is pushed by the pinch roller while, at the same time, the belt is synchronously pulled by the drive. As a result, the material is transported without any relative movement whatsoever at the surface of the workpiece. Hence, the surface quality complies with the initial state.
Hybrid system
If the demand for mere aluminum production is not sufficient to fully use the capacity of a press line, it will possibly be beneficial to have the option for a change. The hybrid concept provides for operation of a conventional inductor set for steel and simultaneously offers the opportunity, just by changing the inductor set, to heat aluminum as well while using one belt conveyor. Thanks to the thermophysical properties of aluminum and the lower forging temperature, it is possible to operate the two inductor sets with the same maximum throughput. This means that the installed inverter capacity can be optimally used for both products.
The plant concept offers a modular design and can be customized to the respective requirements. All resonant circuit capacitors and inverter modules needed for operation are integrated in the related substructure. Inductors and inverter modules can be added depending on the desired throughput.
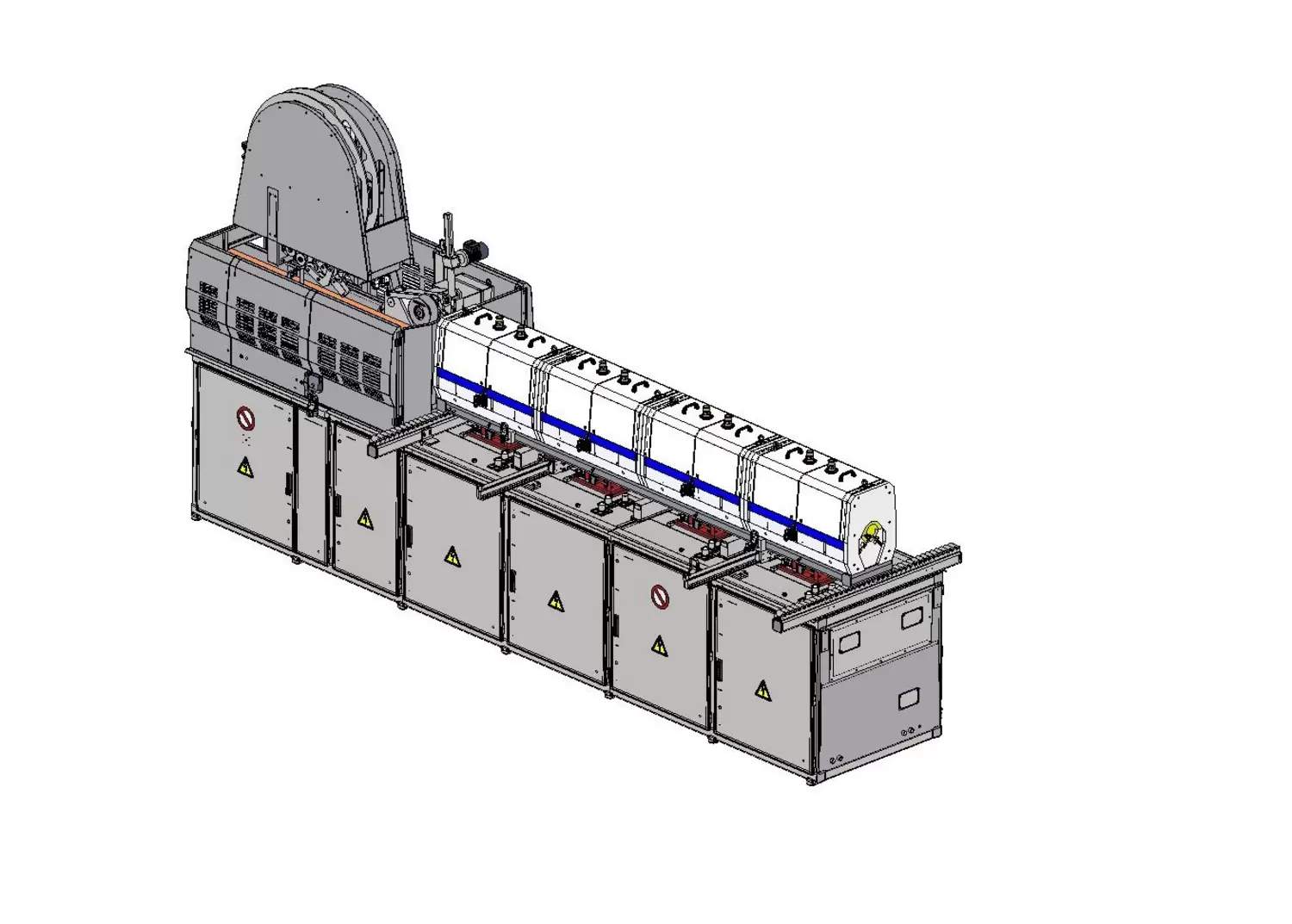
aluminium and steel
Further information
Further information about the world of induction, plant technology and references is also available at www.sms-elotherm.com.