Identifiying keys to success with SMS group
Since the turn of the millennium, world steel capacity has more than doubled. Due to the fact that the steel demand has not increased in accordance with development, steel producers worldwide are facing problem of overcapacity. The Organization for Economic Co-operation of Development (OECD) Steel Committee expects excess capacity of steel to reach 750 million tons, alone in 2016. Consequently, the cost pressure on the plant operators has been growing. However, there are indeed profitable market niches and growth markets. For example, high-strength steel grades for automotive light-weight construction are still much in demand, as well as large-size components for wind power plants or gear components, or special formats, like thicker gage sheet or special long products. Most plant operators have therefore been increasingly concentrating on modernizing their facilities and asking questions like: Which is the best modernization strategy for me to remain competitive? What kind of modifications are needed to maximize the efficiency and sustainability of existing plants?
The future of the plant owners is at stake. Therefore, modernization today is much more than the mere replacement of old parts with new ones. Integrative and foresighted concepts are needed in order to be able to reduce to a minimum the downtimes associated with a revamp, while speeding up the commissioning activities, achieving a fast sms group newsletter 03 / 2016 ramp-up and making the plant “Industry 4.0-ready” with intelligent components, today! SMS group opens up new competitive opportunities for plant operators by implementing targetoriented, customized modernization strategies.
Forward-thinking revamps
Throughout the world, the SMS group’s revamping specialists are very close to their customers. For us, customer proximity is not only a geographical term, but an entrepreneurial mission. The SMS experts actively approach the plant operators, suggesting ways to implement efficient modernization measures that will open up new market opportunities for them. As a matter of course, customers also directly turn to SMS for concrete revamping requests. In both cases, the SMS specialists will first conduct a fact-finding process based on which an engineering concept will be elaborated. From such a concept, a well founded solution will be derived outlining how the production process may look like in the future. Such intensive preliminary work and consulting service pay for our customers, as the modernization projects developed or modified by SMS group provide higher cost-efficiency and allow our customers to reach their targets in a more sustained manner.
Implementing Customer requirements
The fact that SMS group operates its own in-house manufacturing facilities enables us to manufacture components perfectly tailored to the specifics of the modernization project on hand. This, of course, would not be possible without our highly qualified and, above all, long-time employees who have the necessary knowledge and expertise to master the challenges and complex mechanical engineering tasks we encounter in our industry. SMS group has been active in the modernization business for many decades. That gives us a clear competitive edge in the market in terms of practical experience as well as innovative technologies. Especially with a view to growing digitization and for quality improvements, the latter is a decisive aspect because it will become increasingly critical to have intelligent components in place which are capable of communicating more intensively and effectively with higher- level systems.
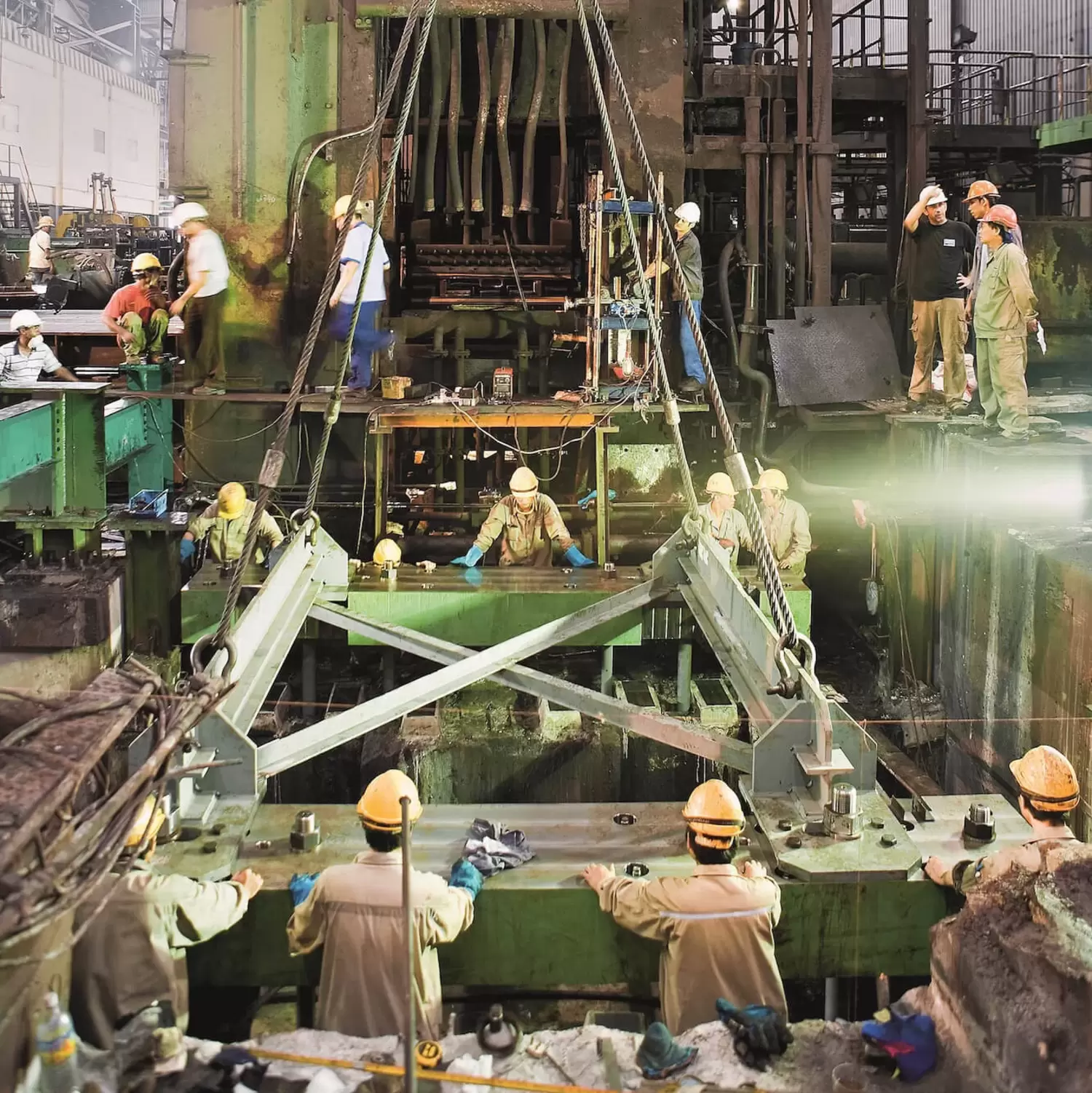
Leveraging expertise
There are basically three options for revamping a production plant: revamping the mechanical equipment, revamping electrics and automation or revamping both the mechanical equipment and electrics & automation. As OEM, SMS group boasts in-depth know-how for all three options. However, the task is not only to bring an obsolete plant back to the state-of-the-art, but above all to increase the product range, the product quality and the flexibility of production – while decreasing the costs of operation. At the same time, a modernization will also reduce the environmental footprint of a plant, allowing it to meet the growing environmental standards.
Highly skilled employees with many years of experience, intelligent components and machines, in-house manufacturing facilities and practical experience from a great many projects are the keys to success in plant modernization.
A look at recent modernization projects reveals the advantages of modernization concepts by SMS group. At Arcelor- Mittal in Gent, Belgium, SMS group is revamping the mechanical equipment of the hot strip mill. The objective of the project is to expand the product portfolio to include high-strength and multi-phase steels. To this end, SMS group will install new finishing stands, new gears and new high-performance spindles. Installation will take place during two scheduled mill shutdowns. The functions of the preassembled components will be checked in comprehensive pre-installation tests in the SMS group’s manufacturing workshops in Hilchenbach together with specialists of ArcelorMittal. One advantage of this procedure is, for example, that later on it will be possible to commission the stands without any readjustment. The new stands will be assembled in the works right next to the running rolling mill. When the old stands will have been disassembled, the new ones will be ready to be shifted into the production line in place of the old stands.
A typical example of a project involving the revamping of both the mechanical equipment and E&A handled by SMS group on a single-source basis is the modernization of the tandem rolling mill at our Russian customer PAO Severstal. In that case, SMS group revamped a plant built in 1963, which today allows our customer to produce high-grade cold-rolled strip for the automotive industry. In addition to new rolling stands and new drive equipment, the customer received bespoke X-Pact® electrical and automation systems for levels 0 through 2, including process models and technological controls that achieve best gage tolerances and extremely short off-tolerance lengths.
An example of a modernization project focusing on electrics and automation systems is the CSP® caster at the Dolvi plant of Jindal South West Steel in India. The project involved the implementation of the level-2 process models for pass schedule calculation and shape, contour and flatness control as well as cooling section control, and the replacement of complete basic automation systems. All systems were tested and optimized with the SMS group’s Plug & Work procedures in real-time simulations. Also operator training took place before the on-site installation using the original control pulpits. All those measures resulted in a very short commissioning phase and a steep ramp-up curve.
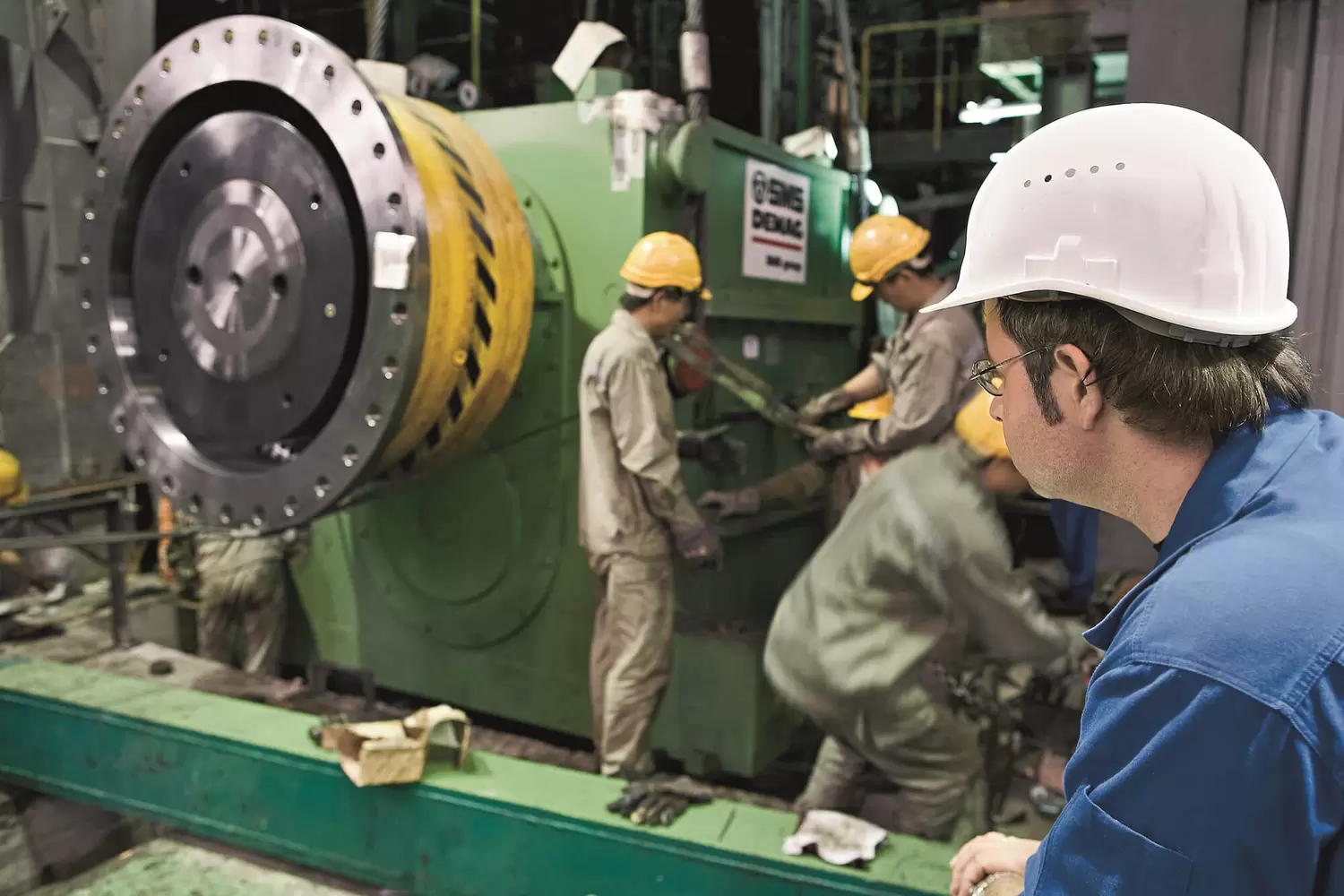
More intelligent components
The intelligent components designed by SMS group show how closely E&A and mechanical equipment must intermesh in order to meet the future requirements of Industry 4.0. In future, we will offer such intelligent components for any plant modification. For example, drive spindles may be designed in such a way that, in addition to transmitting a torque twice as high as before without increasing the spindle diameter and the required installation space, they may also be equipped with a special computer and an energy source for transmitting information about the condition of the spindle to higher-level systems. As a result, preventive maintenance can be significantly improved because it will be possible to predict the point of time when a spindle needs to be replaced most precisely as the system takes into account the actual mode of operation. Similar technologies are available for gears, hydraulic systems, oscillation systems in continuous casting plants and for coiler mandrels.
The use of data alone does not enable Industry 4.0. What’s needed is a holistic approach to the development of integrated solutions based on harmonized systems. SMS group develops such solutions – also for modernization projects.
Enabling Industry 4.0
Those talking about Industry 4.0 should never forget that it is indispensible to have reliable plant data and that those data must be properly evaluated in a Big Data context. Being plant engineering specialists, SMS group understands which concrete benefits a plant operator may derive from the measured values. For practical operation, this means: Intelligent components are essential for intelligent machines and intelligent machines form the basis for intelligent plants meeting the requirements of Industry 4.0. SMS group consistently pursues this future-oriented path not only in the new plant business, but above all in plant modernizations.
After a new or a revamped plant has been successfully commissioned, SMS group is there for its customers with a world-spanning service network. Depending on their specific requirements and their personnel situation, the plant operators can choose from a wide range of service products offered by SMS group. The portfolio includes everything from comprehensive master service agreements to specific service packages that may focus on issues such as quality assurance or stability of plant operation.