Advantages of the SMS method
The VCC® features spooling technology developed by SMS group for producing compact coils consisting of rebars, rounds, squares and hexagons. The geometry assures smooth de-coiling during the downstream process. SMS group’s VCC® produces coils with weights up to 5,000 kg. The higher weight significantly contributes to a reduction in times for downstream coil changing and to significant yield enhancements through minimized material losses. In addition to that, the vertical spooling solution, compared to the horizontals, prompts other positive effects: the equipment is simpler and can be easily installed; the required civil works are minimized as well as maintenance operations.

The compact coil is a crucial step forward in improving the pack-up quality of the final product
These coils have preselected dimensions that, thanks to VCC®, remain consistent for all products processed on the same line. At the same time the compact coil size is ideal for storage, transport and handling. This is particularly beneficial when coils are reworked next to construction sites, where there is a build-up of rebar stirrups and other concrete reinforcing structures, especially in metropolitan areas with many space constraints. The hot rolled condition of the compact coils allows for direct cold working with high ductility during the elastic deformation process, as well as for low energy demand for final forming.
Out of all its features, the one that stands out is the method of winding the bar directly into a vertical position. Just by this aspect any plant operator can eradicate the need for transferring from different angles, all while reducing the cycle time and compacting the coil, as all of them are formed in the final stage. The product is in line to be stored immediately once coiling has been completed and the coils have cooled down. Reduced handling also minimizes the overall risk of damaging the coil surface.
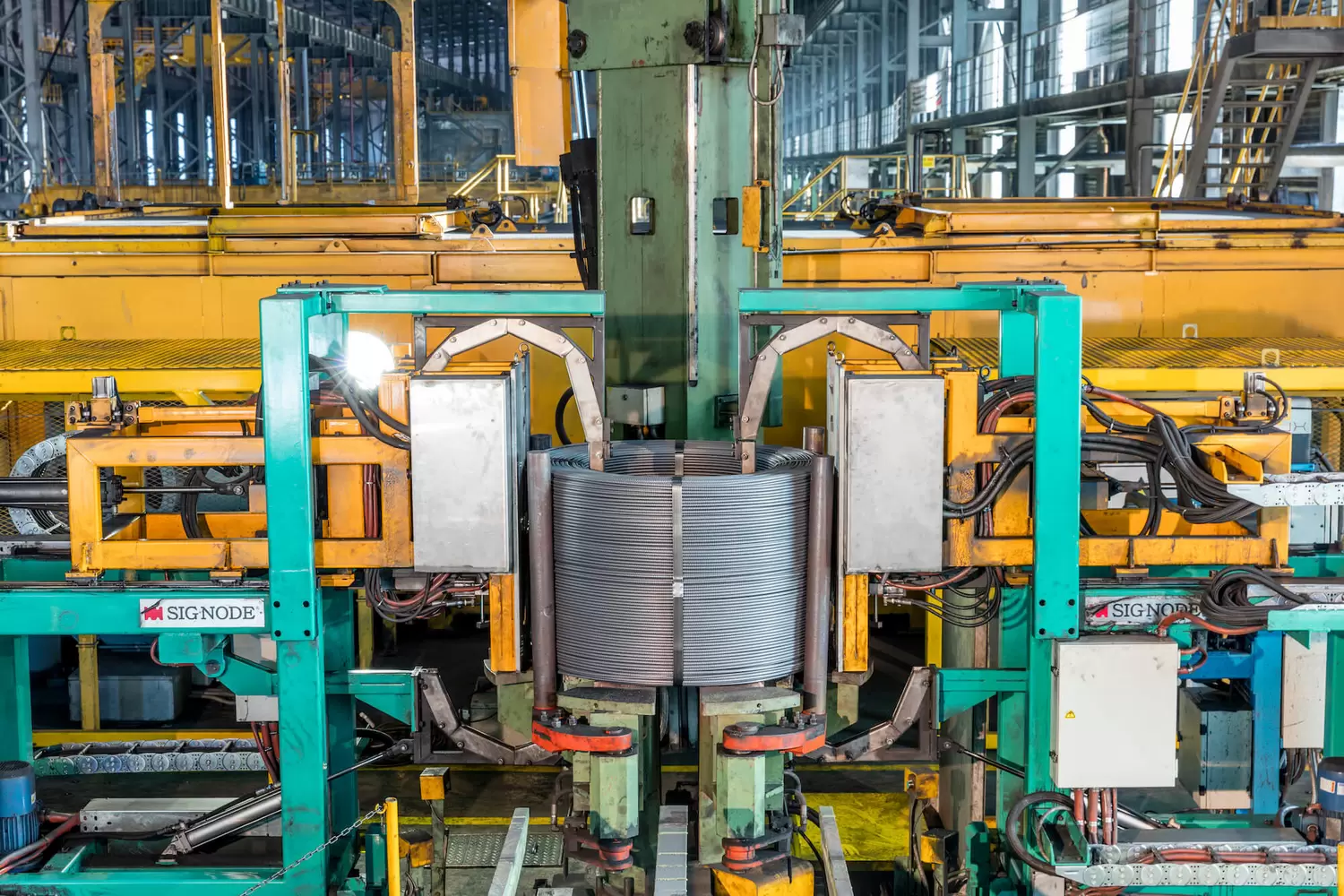