Our extensive expertise in drive systems, honed over years through constructing new metallurgical plants, also includes numerous modernization projects focused on enhancing performance and production flexibility of existing facilities. Our portfolio spans the design and execution of drive system projects, offering solutions that include drive transformers, medium and low voltage converters, and motors such as induction and synchronous types. This broad capability ensures we can deliver customized solutions for maximum efficiency and reliability.
The intelligent networking of drive controls allows for central access to each drive, facilitated by uniform application software that integrates drive-related functions with our X-Pact® automation system. This integration offers customers unparalleled flexibility in production, ensuring that their plants can adapt to changing demands.
Applications of X-Pact® Drive and X-Pact® Torque Drive
To solidify our position as a full-scope supplier, we launched our own low-voltage drive system, X-Pact® Drive, many years ago. X-Pact® Drive represents our proven solution for low-voltage applications and is part of a comprehensive service offering. The system offers high energy efficiency and optimized lifetime costs and is tailored to meet specific process requirements. It features integrated control and monitoring of fans, brakes, and temperature, along with other feedback signals. The power range of the system covers from 0.75 kW to 5300 kW, and it includes interchangeable power modules to reduce spare parts inventory. X-Pact® Drive modules are pre-tested before commissioning to ensure smooth integration. Training courses on maintenance and repair at real converter equipment are provided at our training centers.
X-Pact® Drive has been installed by us in numerous plant types, delivering over 3255 drive units for more than 105 line-ups. A notable achievement was the commissioning of a synchronous motor for the coiler mandrel drive at Big River Steel's CSP® plant in the USA. With a power rating of 1,000 kW and 200% overload capacity, this unit is among the most powerful motors in the low-voltage range, crucial for coilers handling thin-gauge strip due to its lower inertia compared to asynchronous motors.
Meanwhile, X-Pact® Torque Drive is our highly successful solution leveraging torque motor technology. The direct drive system achieves a total efficiency of 98%, significantly reducing operational expenses (OPEX) due to its efficient motor technology and elimination of gear units. The absence of gear oil and circulating lubrication makes the system environmentally friendly. Additionally, the lack of a separately driven fan further reduces energy consumption and noise pollution. With no gear part wear and minimal moving masses, the system is virtually maintenance-free, offering high control performance and reliability. The reduction in mass inertia and the use of a permanently excited synchronous motor enhance the system's dynamics and control performance, making it more efficient than traditional asynchronous motors.
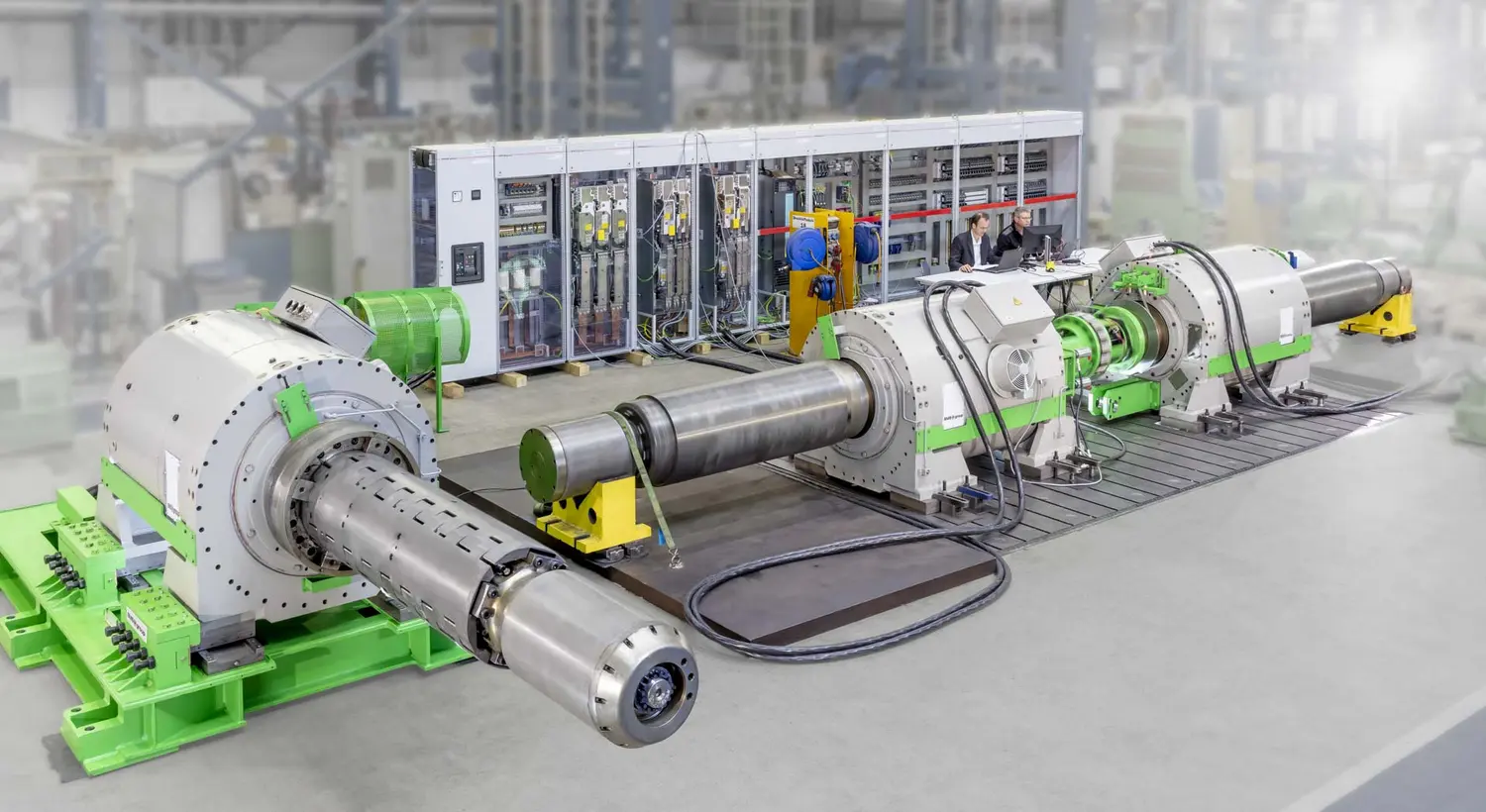
X-Pact® Torque Drive has been effectively integrated into various applications, such as the edge scrap coiler at MMPZ Group's tinplate production complex, showcasing its ability to deliver high torque at low speeds without gear units, thereby reducing maintenance needs. Its use in pay-off and tension reels for electric strip annealing and insulating lines at thyssenkrupp Steel Europe highlights its gearless efficiency, resulting in a more compact system with improved dynamics and control performance. For the edge scrap balers in the new can coating line at Aluminum Dynamics' flat rolling complex, our mechatronic solution, X-Pact® Torque Drive, will also ensure maximum process-oriented drive performance.
Engineering excellence and global reach
Additionally, our global expertise in drive systems encompasses integrative engineering of the drive train, specific sales specifications for drive systems, planning and realization of drive solutions, and the dimensioning and simulation of electrical drives. We also focus on adapting to existing supply networks and load profiles, ensuring EMC planning and cabling advantages.
By providing completely customized packages from engineering to commissioning, we support the selection of the best-fitting equipment for each project, independent of any equipment manufacturer. Our extensive portfolio of services and hardware supplies covers a wide range of drive applications, and we remain open to new challenges, leveraging our experience from successfully executed projects.