Coiler mandrels are an essential element in the X-Roll® coiles and Uni PLUS coilers of SMS group hot strip mills and belong to the high-tech products of this plant type. Now, SMS group has manufactured the 400th coiler mandrel in its workshop in Hilchenbach.
In October 2020, SMS group was able to deliver to the customer the 400th X-Roll® coiler mandrel manufactured in the Hilchenbach workshop. The development and manufacture of the X-Roll® coiler mandrels at SMS group can be traced back to the year 1967. Already at the end of the 1980s, the delivery of the 100th coiler mandrel took place followed by the 200th coiler mandrel leaving the Hilchenbach manufacturing center in the year 2000. The delivery of coiler mandrel number 300 took place in April 2008. Some of the coiler mandrels manufactured by SMS group have been in operation for more than 40 years, which is due to the extremely high development and manufacturing expertise.
Experience and comprehensive know-how for extremely high forces and torques
Since 1980, SMS group has sold and commissioned around 215 X-Roll® coilers. Both the many years of experience and the comprehensive know-how of the company have been incorporated into the permanent and sophisticated further development of the coiler components. The first coiler mandrel developed and manufactured by SMS group already had a function decisive for the coiling quality: the re-expansion. Further milestones were the introduction of the mandrel support bearing and the continuous grease lubrication of the mandrel.
The ever-increasing market demands for high-strength hot strip with strengths of up to 1,400 megapascals in combination with increasing strip thicknesses and strip widths have resulted in particularly intensive development activities in recent years. For these new materials and dimensions, the UNI plus coiler has been developed. Here, the coiler mandrel is exposed to extremely high forces and torques, especially during winding of the initial wraps. The experts in the SMS group competence centers for design, development and manufacturing have continuously developed the coiler equipment and especially the coiler mandrels on the basis of these new requirements using state-of-the-art tools. The coiling process is simulated in order to determine the exact forces and torques for dimensioning the components and thus to optimize the design and selection of the suitable materials for all components.
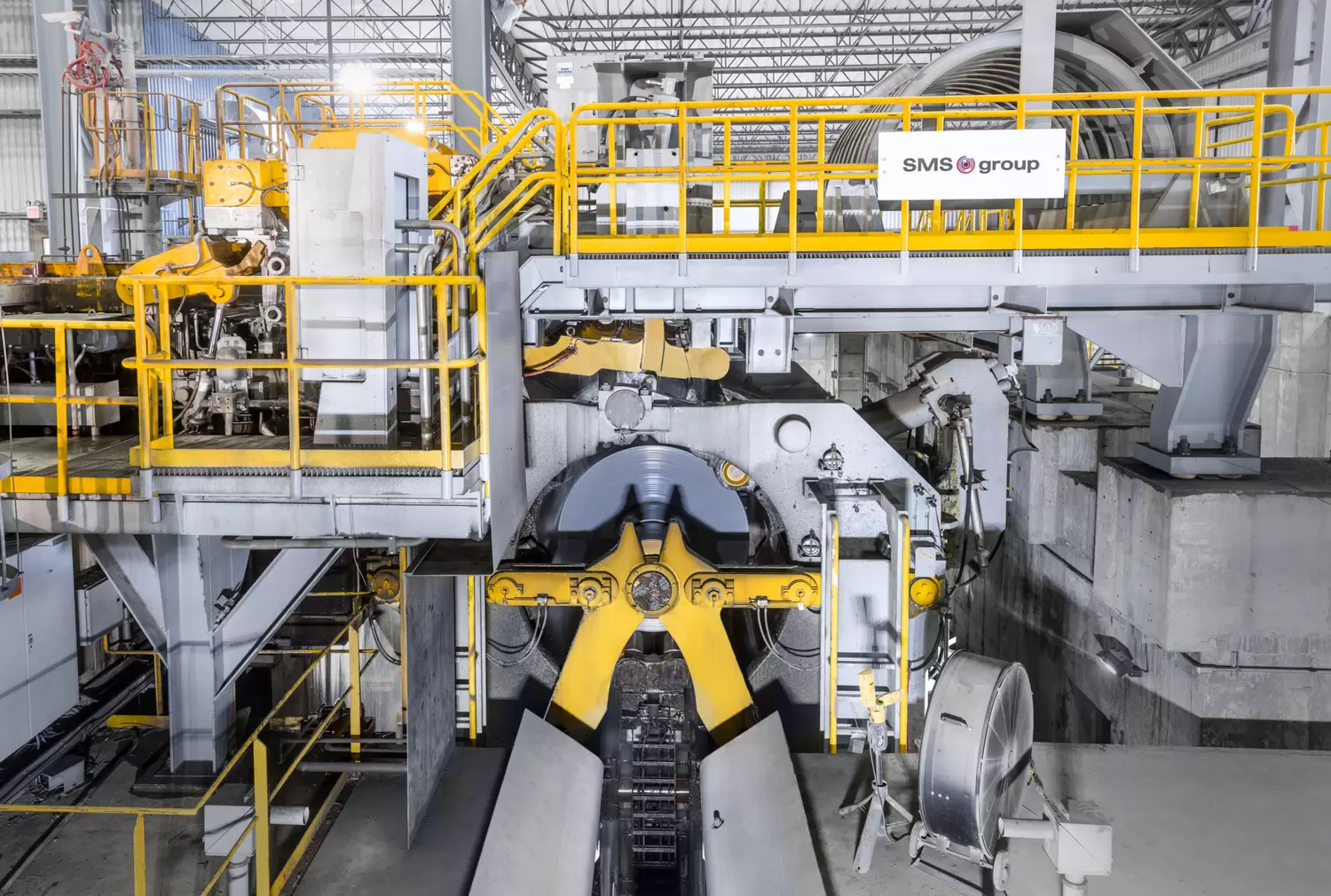
An essential milestone in this development work is the patented X-Roll® coiler mandrel of closed-type design. In recent years, SMS group has already manufactured 77 of these mandrels, which are designed for coiling API-X80 pipe steel with strip thicknesses of up to 25.4 millimeters and again feature extended service lives.
Marc Hoffmann, Head of the Flat Rolling Mills Business Unit: “Our customers demand 100% plant availability simultaneously with a long service life of the core components. For this reason, the X-Roll® coiler mandrels are designed and manufactured at SMS group in Hilchenbach and subjected to a workshop test in the manufacturing center specially equipped for this purpose”.
Inspection, maintenance and repair service
In addition to the sale of new coiler mandrels, SMS group puts its focus on regular and demanding inspection, maintenance and repair services.
Christoph Bald, Head of Service Workshop at SMS group in Hilchenbach: \"We are optimally equipped for our both own coiler mandrels and third-party makes, and possess knowledge and skills on successful repair accumulated over many years in our manufacturing center. Through regular inspection and maintenance, the service life of the core component X-Roll® coiler mandrels can be considerably extended, while ensuring the highest coiling qualities”.
At regular intervals, the tailor-made repair is carried out in the SMS group's specially equipped repair centers. In coordination with the design department, mandrels of older designs and third-party makes can also be brought to state-of-the-art technology.
The possibilities at the SMS manufacturing center in Hilchenbach include the inspection, maintenance and repair of core components at the highest technical and technological level. These include e.g. X-Roll® coiler mandrels, AGC/HGC cylinders, CVC® bending and shifting systems, spindles, gear units, oil film bearings, valve stands for high-pressure/low-pressure hydraulic systems, mechanical adjustment systems, Sermes adjustment systems, shears and chocks.
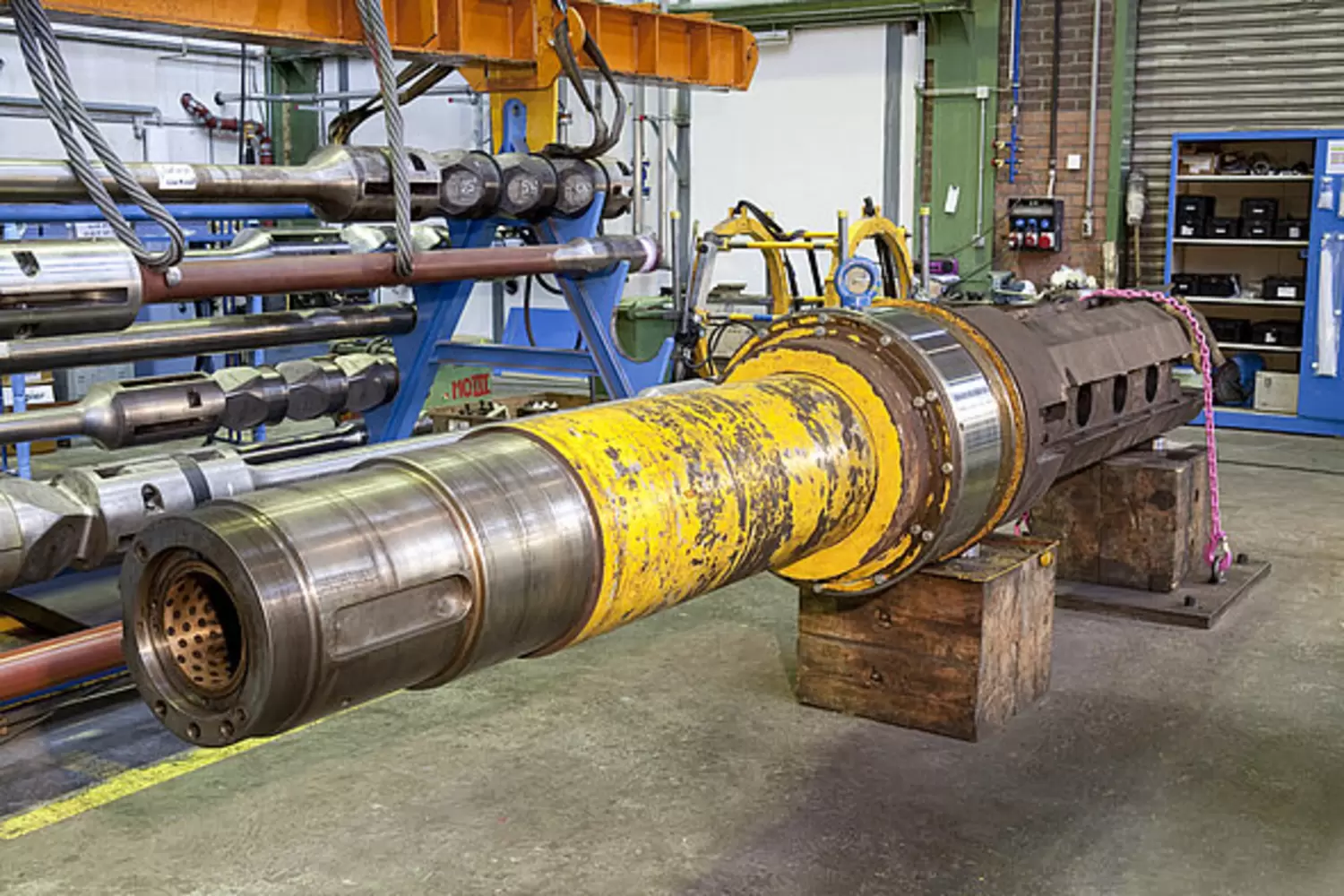
Digitalization
The latest generation of the SMS group coiler systems can be equipped with intelligent components, sensors and corresponding software solutions from SMS group and SMS digital, such as the Process Condition Analyzer (PCA) or Genius CM®. “This way, the coiling process is permanently checked, the plant condition is monitored and corresponding recommendations are provided to the customer's operating and maintenance team”, says Wolfgang Fuchs, Head of Hot Rolling Mills / Heavy Plate Rolling Mills Product Unit, summarizing the possibilities of digitalization for coiler systems.