Metix was founded in South Africa in 2003 as a privately owned company with a focus on the submerged arc furnace (SAF) business. Although the company initially focused on technology and equipment for submerged arc furnaces, our later worldwide participation in large Engineering, Procurement and Construction (EPC) projects was the key to our success. We joined SMS group in 2011 and in 2018 we were announced as the worldwide Center of Competence (COC) for SMS group’s SAF business.
Our focus was to do business on a sustainable basis, ensuring continued client support on completed and ongoing projects as well as technological queries. The availability of key individuals from the previous submerged arc furnace division in Germany, who are now members of the nonferrous division, was vital for continuity and support during that period. An important aspect is to synchronize our current processes and activities with the more than 100 years of successful SAF business conducted by the SMS group.
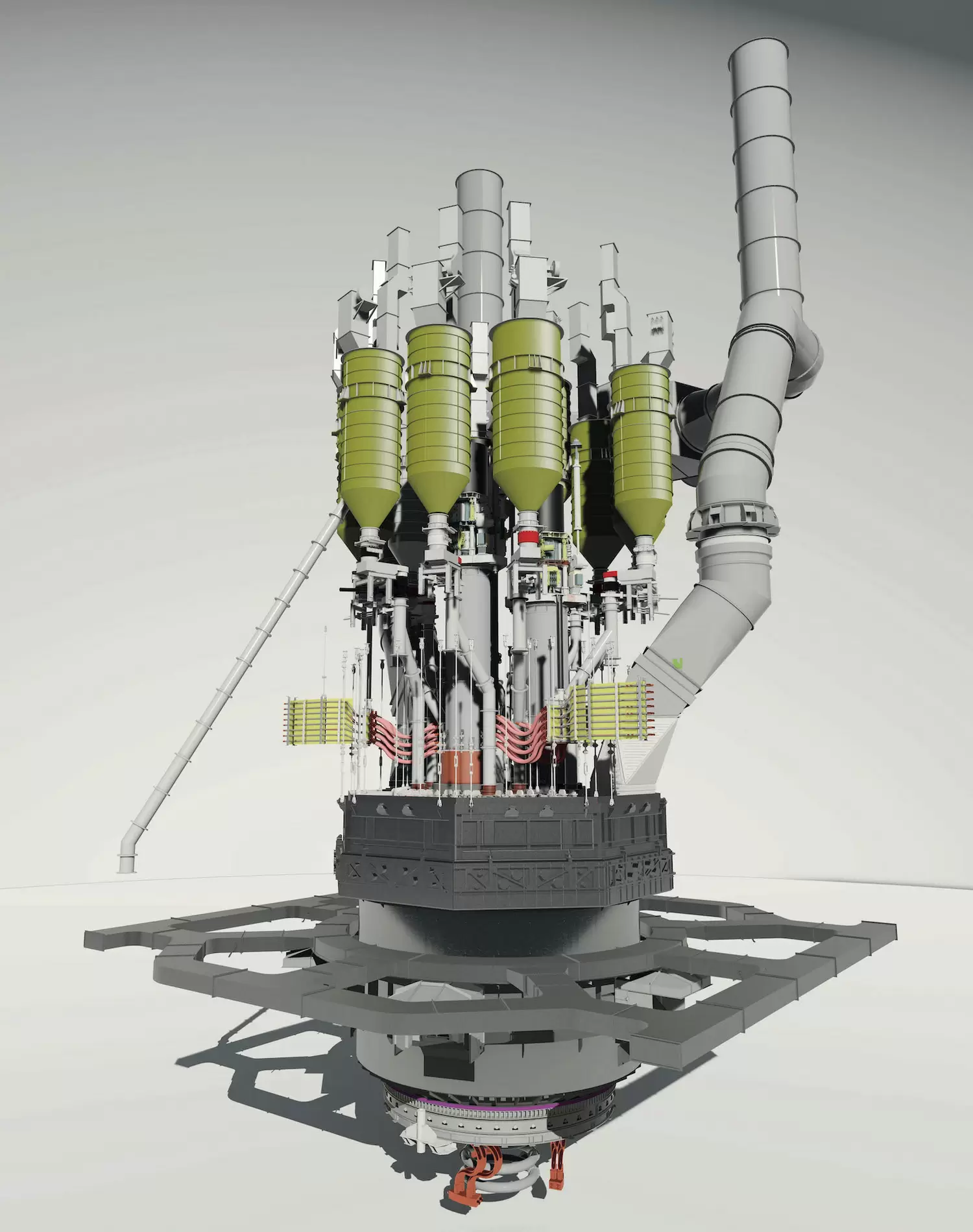
Our focus will be to concentrate our core competences in one location, while supplying competitive solutions for metallurgical furnaces, equipment and complete plants for the production of ferro-alloys, silicon metal, special metals and slags to customers around the world.
The recovery of valuable elements from by-products and wastes plays an essential role.
And we are continuously striving to maximize the value chain. Therefore, the recovery of valuable elements from by-products and wastes plays an essential role here. Our latest product, developed with our non-ferrous partners, improves the recovery of copper (Cu) metal from slag considerably. We are applying slag cleaning and matte settling technologies to other commodities with potentially very profitable returns for our customers. This permits not only the recovery of valuable metals, but also the declassification of by-products that otherwise have to be stored in highly capital-intensive, environmentally compliant facilities - in some cases, even resulting in commercial products as, for example, inert slag sold to the construction industry as aggregate material.
We have a keen interest in additive manufacturing, and we have made good progress in understanding the current status of the market and application potential of SAFs. Inhouse and external consultations have given us new ideas of how to overcome the challenges of extremely hard operating conditions characterized by high temperature, high currents and fluctuating pH regimes.
Our latest furnace offering is digitalization-ready and we have made good progress in understanding the groundbreaking potential of the different products offered. The level to which we can monitor, predict and manipulate submerged arc furnace operation is ‘next level’ and very flexible. By applying the right basics, we can offer clients a gradual plug-and-play set of upgrades that improve productivity, environmental accountability, output and availability.
As an integrated, multidisciplinary EPC (engineering, procurement, construction) company as well as an original equipment manufacturer (OEM) of submerged arc furnace equipment, we have a unique set of software packages that provide us with highly efficient Building Information Management (BIM) and assist us by Design for Construction “D4C”. This stands for the philosophy of “getting it right before the site”. We are continuously developing systems that improve constructability through 4D planning, fault detection and the workflow. Our focus is to minimize the exposure to health, safety, the environment, costs and time on the construction sites.
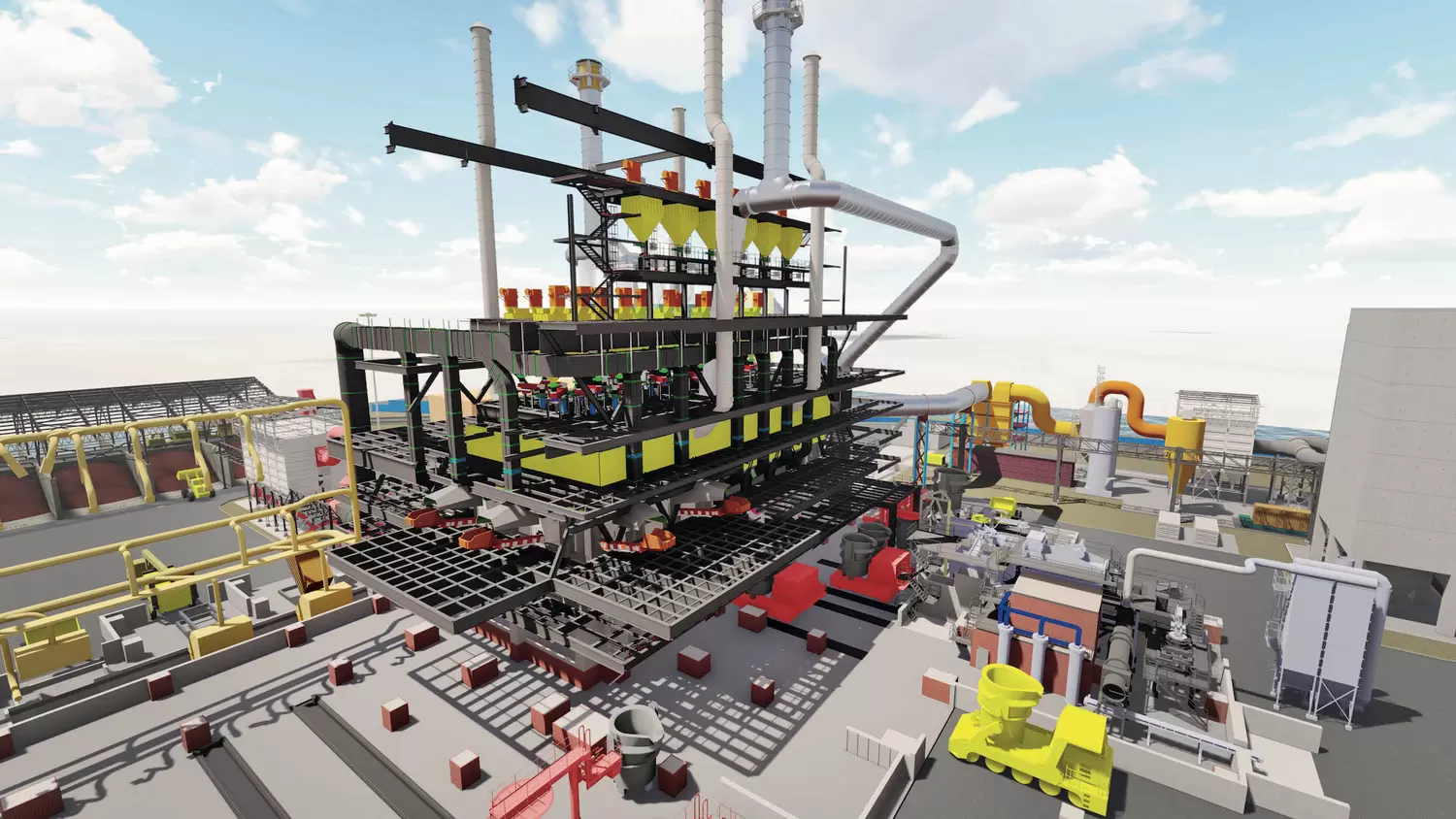
Renewable energy is a hot topic and therefore the production of solar-grade Si-metal (Silicon) is high on the priority list. The Silicon raw material must be of the purest form as well as have the right thermal characteristics, making it a highly specialized material. The secret now lies in developing solutions that upgrade older technologies in terms of energy efficiency, product quality and ultimately production costs. Having supplied some of these plants ourselves, we know how to best go about their optimization and what concepts have proved successful.
Vanadium is on the tip of everyone’s tongue.
Vanadium is on the tip of everyone’s tongue. If it is not in connection with Redox batteries, then possibly in connection with ways of how to increase the structural integrity of construction rebar through higher vanadium content. Although our SAF technology deals with the tail end of this value chain, it is still an exciting market, especially when you also look at the markets for titanium and magnetite.
FeCr (Ferrochrome), FeMN (Ferromanganese), SiMn (Siliconmanganese), ilmenite and other materials are in a constant state of flux. Supply and demand force us into geographical competition with players that are willing to take higher risks. Here we are readily positioned with cost competitive, robust and trouble-free solutions.