SMS group will supply the mill to the Korean steel market, facing post-pandemic recovery and focusing on eco-friendly steel plants. Thanks to cutting-edge solutions for gas purification, water treatment, low emissions, and energy efficiency, the plant complies with the highest sustainability standards in melting, reheating, and fume treatment technologies.
Based in a growing residential area in Busan, YK Steel needs to move the existing facilities to Dangjin, close to Pyeongtaek location of the existing Daehan’s plant supplied by SMS group, in order to facilitate the billet logistics and to feed both plants.
Electric arc furnace and casting technology
The minimill plant will be fed by a 100% scrap-based meltshop reengineered to incorporate parts of the existing equipment into the new facility. A completely new 115 t EDGE™ Electric Arc Furnace equipped with a 102-MVA transformer will integrate the existing sampler and other reusable equipment, though introducing latest technologies in the newly supplied portions. The ladle furnace will be relocated while a complete new high efficiency fume treatment plant and material handling system, feeding EAF and LF required additions, will be purposely designed.
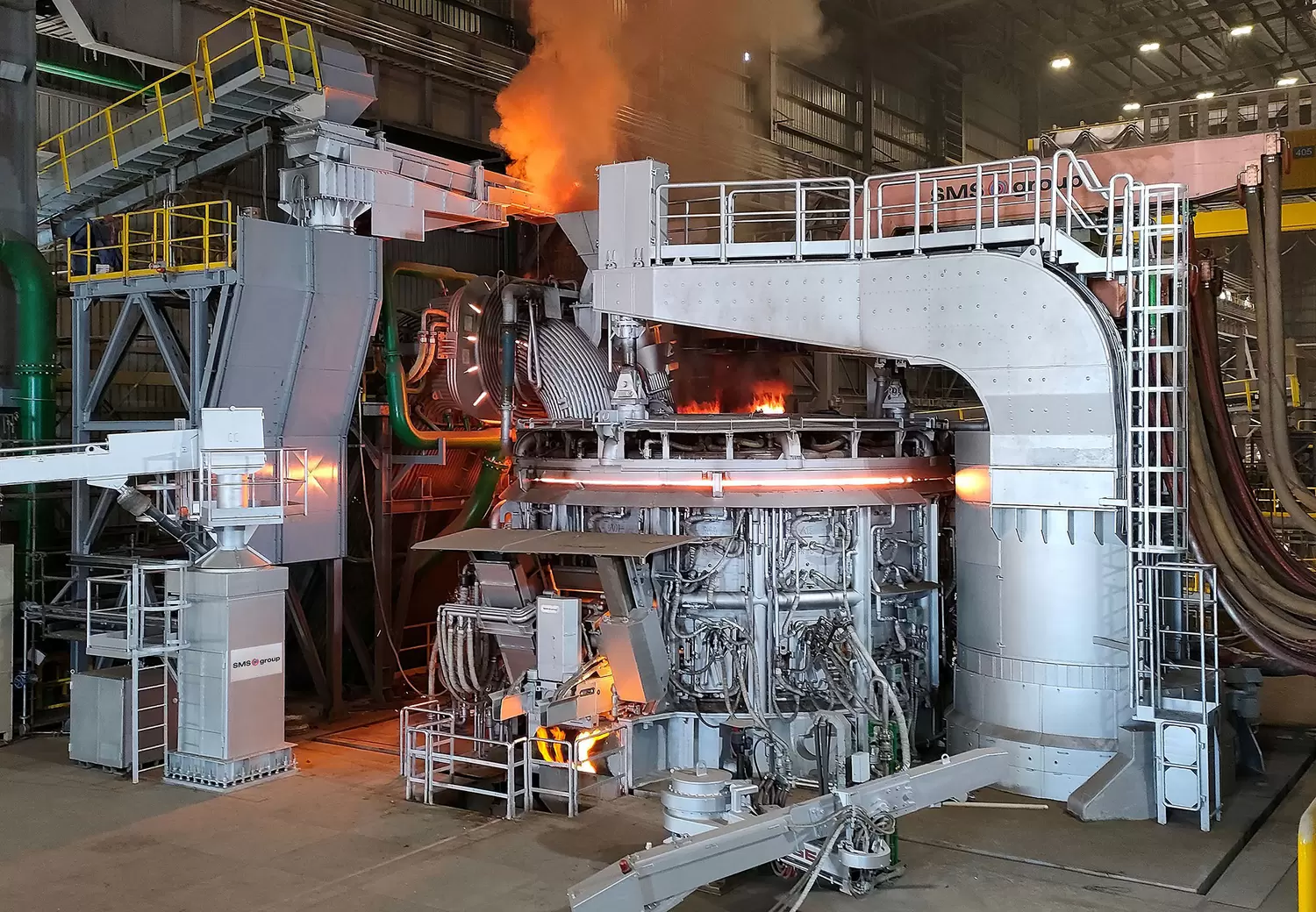
The 5-strand billet-casting machine will produce 150 millimeter square billets and will include the well proven CONVEX mold technology in order to achieve the required casing speeds up to 4.5 meters per minute resulting in throughput per strand of 45 tons per hour. CONVEX mold tubes maintain optimal contact to the strand throughout the length of the mold tube, thus improve the heat transfer and enable uniform cooling of the steel. In addition, the nozzle manipulator allows casting speed adaptions during operation. The billet caster is further equipped with the electromechanical oscillation CONDRIVE and the CONSTIR system for a most uniform solidification conditions in the mold.
Rolling mill
The linked rolling mill will be fed by a hot-charge roller table, connected to a new 140 t/h walking beam furnace, fitted with the latest eco-friendly technology such as low-NOx self-recuperative burners. Recent SMS group furnaces technologies such as flameless burners are developed to ensure NOx lower than 40 ppm with efficiency levels as low as 250 kcal/kg, performed with the most advanced mathematical models connected to SMS group integrated automation systems.
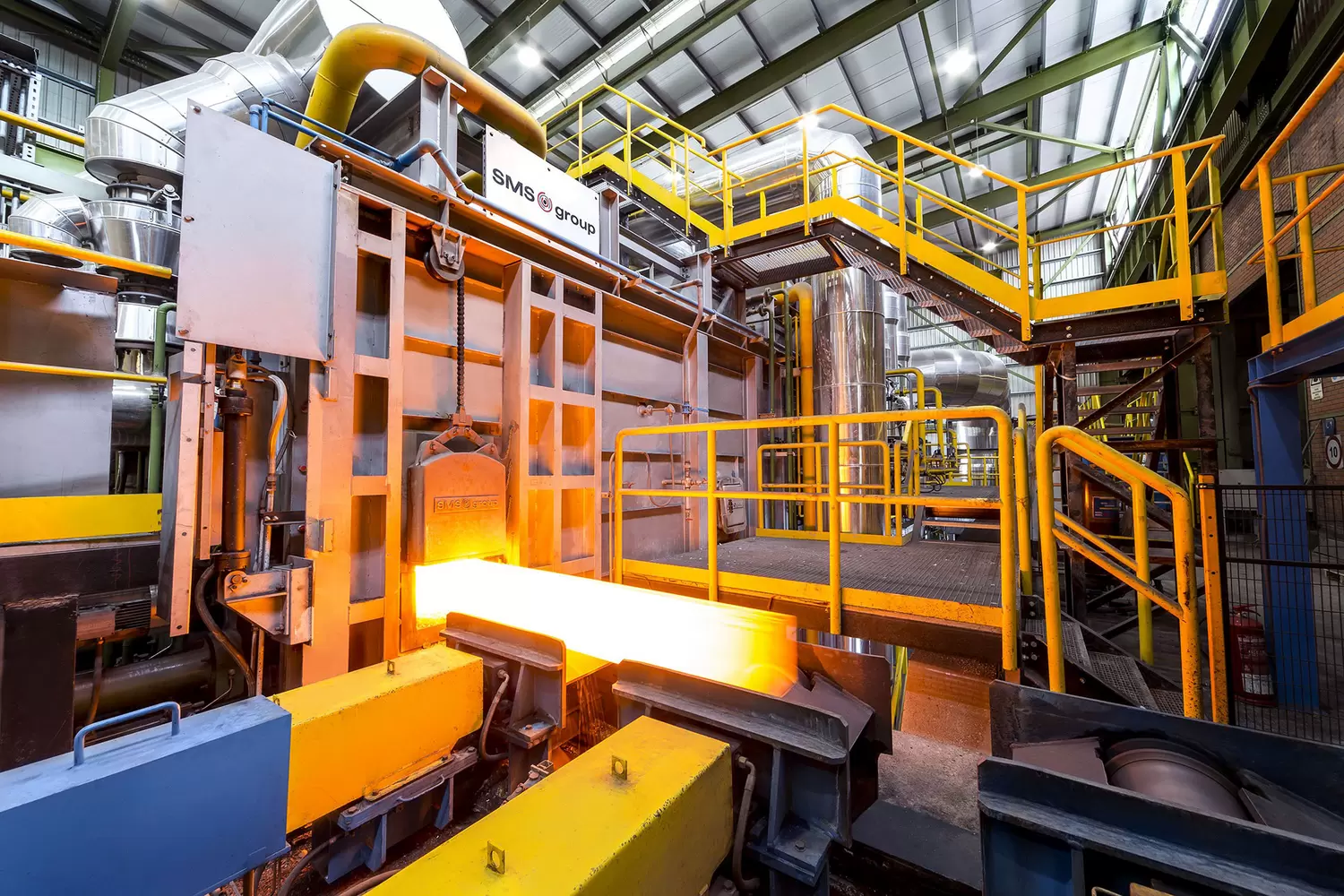
The rolling mill is composed of eighteen relocated housing stands, a new thermo-processing water cooling system for rolled stock temperature control and quenching operations, with a cooling bed and associated bar finishing services, including bundling and sub-bundling stations. It will serve the market with 6 and 12-meter long sub-bundles with a weight of maximum 450-550 kg and master bundles having the same length, with weight of up to 2 tons.
The supply includes also an SMS group Level 1 and 2 automation system and a complete supply with all auxiliary plants and services.