To Nucor Steel Gallatin SMS group supplied a new “heat-to-coat” pickling and galvanizing line based on SMS group's patented technology. With a capacity of 500,000 t/year, up to 180 t/hour of output and a vast product range the new “heat-to-coat” line of Nucor Steel Gallatin in Ghent, Kentucky (USA) sets new standards in hot strip galvanizing. SMS group designed and built the line as a complete unit: Engineering, process technology, equipment, electrical and drive systems as well as the entire X-Pact® plant automation and digital sensors. A holistic digitalization package for material tracking, quality documentation and sophisticated production planning was also installed.
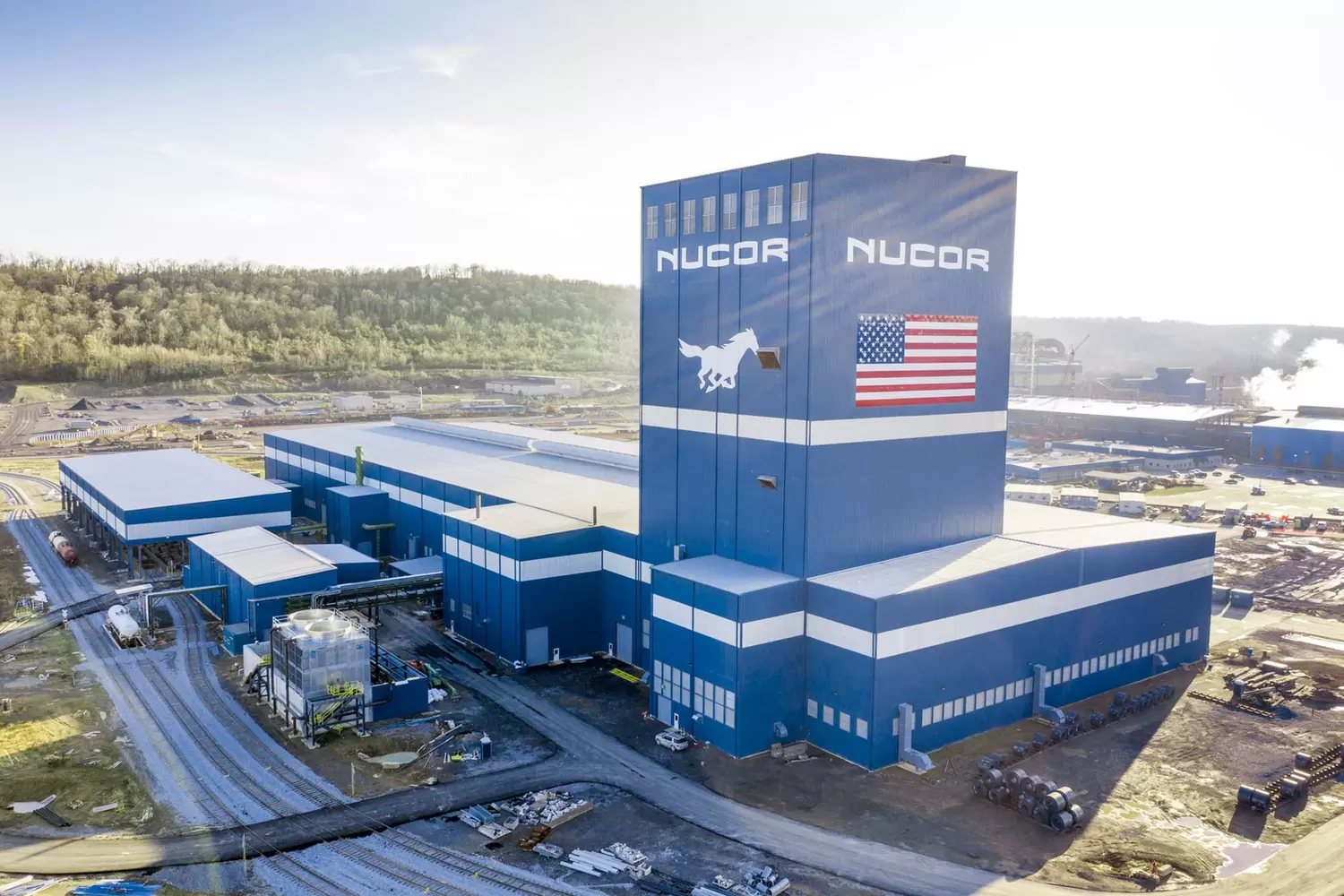
SMS group experts installed the automation system for the new line in the test center in Mönchengladbach, Germany and connected it with a virtual simulation of the plant and of the production process. All operation modes and processes were simulated in real-time and visualized by using X-Pact® Vision, with the original hardware and software on the customer’s systems. The real-time plant simulation reproduces a digital twin that features the same functions and technology as the plant for the Nucor Steel Gallatin. Within the scope of the Plug & Work test, this simulation was connected to the automation system of the plant to be tested and serves as substitute of the real plant.
Holistic integration testing with real customer data
That way, a high level of integration was achieved. Especially that concerned the Manufacturing Execution Suite 4.0: the loop from Nucors ERP to the virtual production and back was fully tested. To do so, the real Level 4 ERP-System of Nucor was incorporated. Past customer orders were utilized to configure and test the seamless transition of data from the new SMS group Level 3 production planning and process automation to existing Level 4 Systems of Nucor and back.
The aim of such intensive testing was not only to ensure smooth operation and a steep ramp-up. Nucor staff was closely involved in the process of configuring and testing all systems, which lead to a close relation between Nucors operators and the commissioning engineers of SMS group. Additionally, the operators got to know the new Manufacturing Execution Suite 4.0 by heart, even before the actual plant was fully commissioned and running.
With realistic coil data, the customers` Level 4 Systems were close incorporated into integration testing. In a first step the customer orders were fed into the Manufacturing Execution Suite 4.0. Here, the were transformed into production orders and production sequences were planned and scheduled. The PDIs and sequences were forwarded the X-Pact® process automation systems, where they were visualized with X-Pact® Vision HMIs and set-point for the basic automation were created.
The X-Pact® basic automation was then tested in the actual production simulation. In a digital twin the coil was virtually processed and all functionalities of the automation systems were tested. The simulation returned production data into the basic automation systems for further processing.
The X-Pact® process automation was utilized to process the simulated production data so that a smooth flow of data throughout the entire automation could be assured in both directions: upstream and downstream. As part of the process automation the production data were processed and archived and a full material tracking was assured.
The Level 3 Manufacturing Execution Suite 4.0 received the validated production results. Hence, full order tracking and quality tracking was established. The order result data were then fed back into Nucors ERP-Systems, so that a closed-loop testing approach was established.
Additionally the Business Intelligence Modules of the Manufacturing Execution Suite 4.0 were utilized to create reports on simulated production data.
X-Pact® Plug & Work integration test at a glance
The results of such comprehensive integration testing were striking. Based on the realistic real-time simulation the entire automation and digitalization landscape could be testes even before commissioning. During the training of the customer’s staff at the SMS group test field, the reality of working in a real plant is replicated. The customer’s personnel learn the plant functions and how to handle them under realistic operating conditions in a virtual production scenario. Additionally, Nucor operators were able to closely get involved in the process which lead to a high degree of motivation amongst staff, close collaboration between SMS group commissioning engineers and Nucor staff and a high training level long before production start.
With SMS groups X-Pact® Plug & Work integration tests, ramp-up curves can be shortened by up to 30%. At the same time high product quality and stable production can be assured right from production start.
At numerous locations worldwide, SMS group operates Plug & Work test centers and training facilities. At these specifically equipped test fields, original control desks, switch cabinets and automation systems are installed and con-figured according to the individual requirements of the customer. Then, all hardware components have to pass a function test to discover and remedy possible defects already in advance. The benefit for the customer is that he can rely on receiving faultless and thoroughly tested software. Many customer delegations visit the Mönchengladbach test center to experience live the virtual production by various plant types during digital commissioning and to gain an overview of the current innovative concepts.
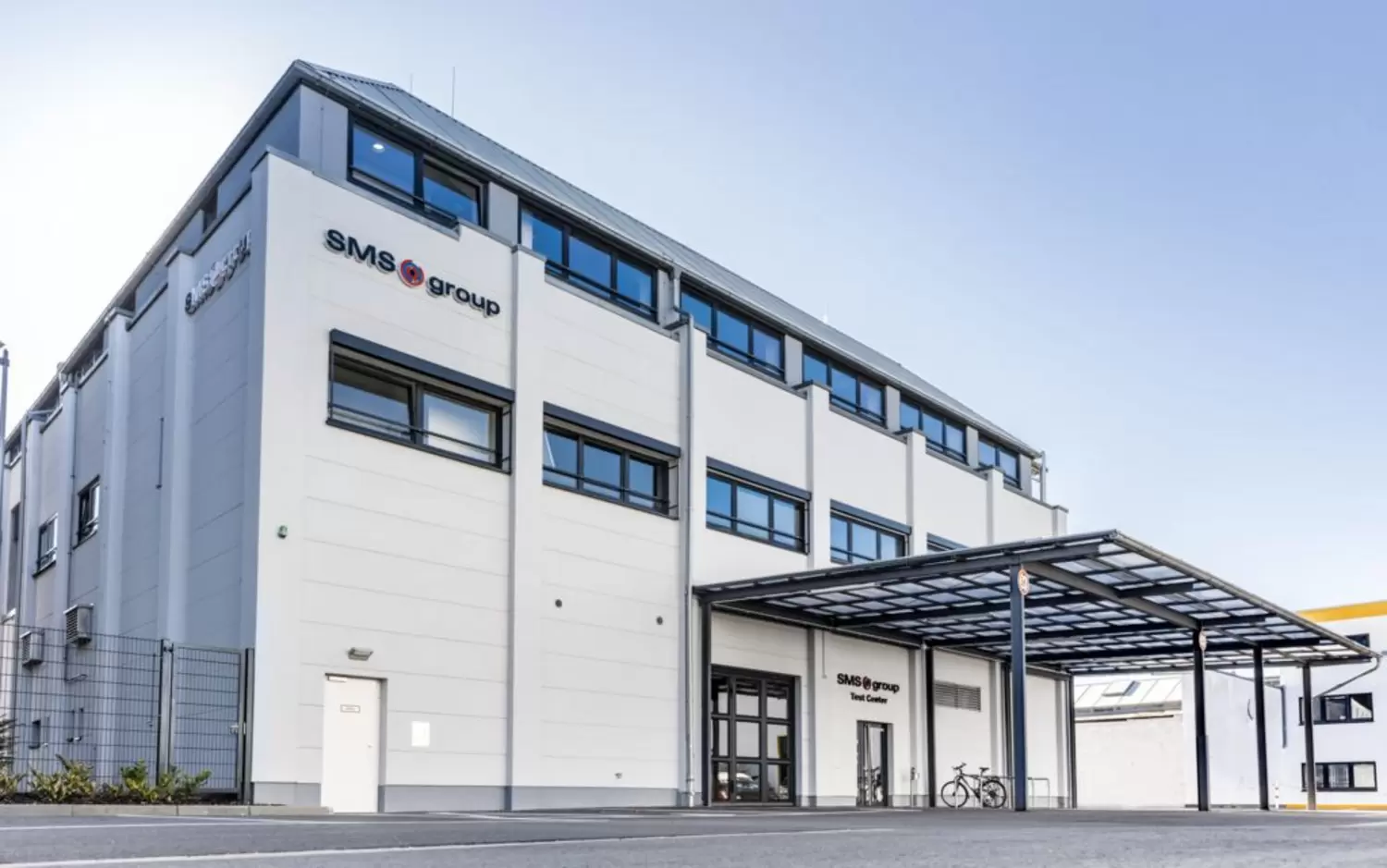