In future scenarios, batteries play a crucial role with regard to energy storage, the electrification of transport, and the operation of portable electronic devices. With expected annual growth rates of 15% and more, there is a growing need for efficient recycling solutions for end-of-life batteries. Battery recycling allows valuable raw materials, such as lithium, cobalt, and nickel, to be recovered from – and then used to produce – new battery cells.
A vast array of battery types
In recent decades, hundreds of different battery types have been launched on the market. The main types can be broadly categorized into the following groups:
- Lead-acid batteries are commonly used in automotive applications.
- Nickel-based batteries come in two main varieties: nickel-cadmium (NiCd), which are known for their durability and ability to perform well in extreme temperatures, and nickel-metal hydride (NiMH), which have a higher capacity and less environmental impact.
- Lithium-based batteries are used for various applications. Lithium-ion (Li-ion) batteries are prevalent in consumer electronics, electric vehicles, and renewable energy storage. Lithium iron phosphate (LiFePO4) batteries are noted for their safety and long life, while lithium polymer (LiPo) batteries offer high energy density and flexible form factors.
- Alkaline batteries are commonly found in household items, for example remote controls and flashlights, and are typically non-rechargeable.
- Flow batteries are suitable for large-scale energy storage systems, with types including vanadium redox flow and zinc-bromine flow.
Although each type of battery has its own specific applications, advantages, and limitations, they all have one thing in common. Batteries are highly complex products, which are characterized by a diverse and functional combination of metals and other materials that have to be “unmixed” during metallurgical processing in a cost-effective way. As a result, this calls for sophisticated recycling processes, starting with mechanical separation and followed by the most suitable, economically viable combination of pyro- and/or hydrometallurgical processes.
Pyrometallurgical solutions
SMS offers solutions for recycling all of the battery types described. Choosing the best recycling process for batteries and accumulators depends greatly on the amount and on the chemical and physical properties of the input material, as well as the location. The pyrometallurgical process route is best combined with hydrometallurgical steps, separating the individual metals from a multiple metals regulus to produce high-quality battery precursor material.
Pyrometallurgical technology such as the BlueSmelter, TBRC (top blown rotating converter), electric smelters, and the Kivcet furnace are typical melt production techniques. SMS group is also developing a solution that combines pyro- and hydrometallurgical steps for recycling complex metal-bearing materials, including lithium-ion batteries. The advantage of this new process route is that it offers more flexibility when processing rapidly changing battery chemistries.
Hydrometallurgical solutions from Primobius
To address the growing demand for recycling lithium-ion batteries, Primobius was founded – a joint venture between SMS group and Neometals Ltd., an Australian process technology developer. Primobius has developed a sustainable two-stage recycling process to recover cobalt, nickel, lithium, copper, iron, aluminum, and manganese and turn them into marketable products that can be reused in the battery supply chain, utilizing a combination of efficient mechanical and hydrometallurgical processes with recovery rates of up to 90%.
In the shredding and beneficiation stage (stage 1), spent batteries are shredded and the plastic and metal components are removed from the so-called “black mass.” The hydrometallurgical approach (stage 2) represents an extremely safe and efficient method of extracting materials from the black mass at ordinary temperatures with recirculating liquid solvents. In this process, Primobius complies with international battery regulations and places great importance on health and safety. Michel Siemon, CEO of Primobius: “Primobius stands for much more than just technology. We provide process know-how and an ecosystem of partners along the value chain and offer unique and flexible business models and opportunities for engagement with our partners.”
These advanced recycling solutions close the valuable materials loop and provide battery manufacturers in the automotive industry and other sectors with a way to decarbonize the supply chain and reduce dependence on critical and foreign-mined raw materials. Additionally, the consistent reduction and avoidance of CO2 emissions in all process stages have a positive impact on the carbon footprint of the lifecycle of the battery module as well as the electric vehicle in which it is used.
Mercedes-Benz relies on Primobius technology
The opening ceremony for the first Primobius battery recycling plant at Mercedes-Benz in Kuppenheim, Germany was held on October 21, 2024. German Chancellor Olaf Scholz opened the plant.
Primobius was responsible for the engineering, equipment supply, and installation of the complete two-stage integrated recycling plant, which will process 2,500 t of batteries annually. The facility will continue to receive technological and R&D support from Primobius.
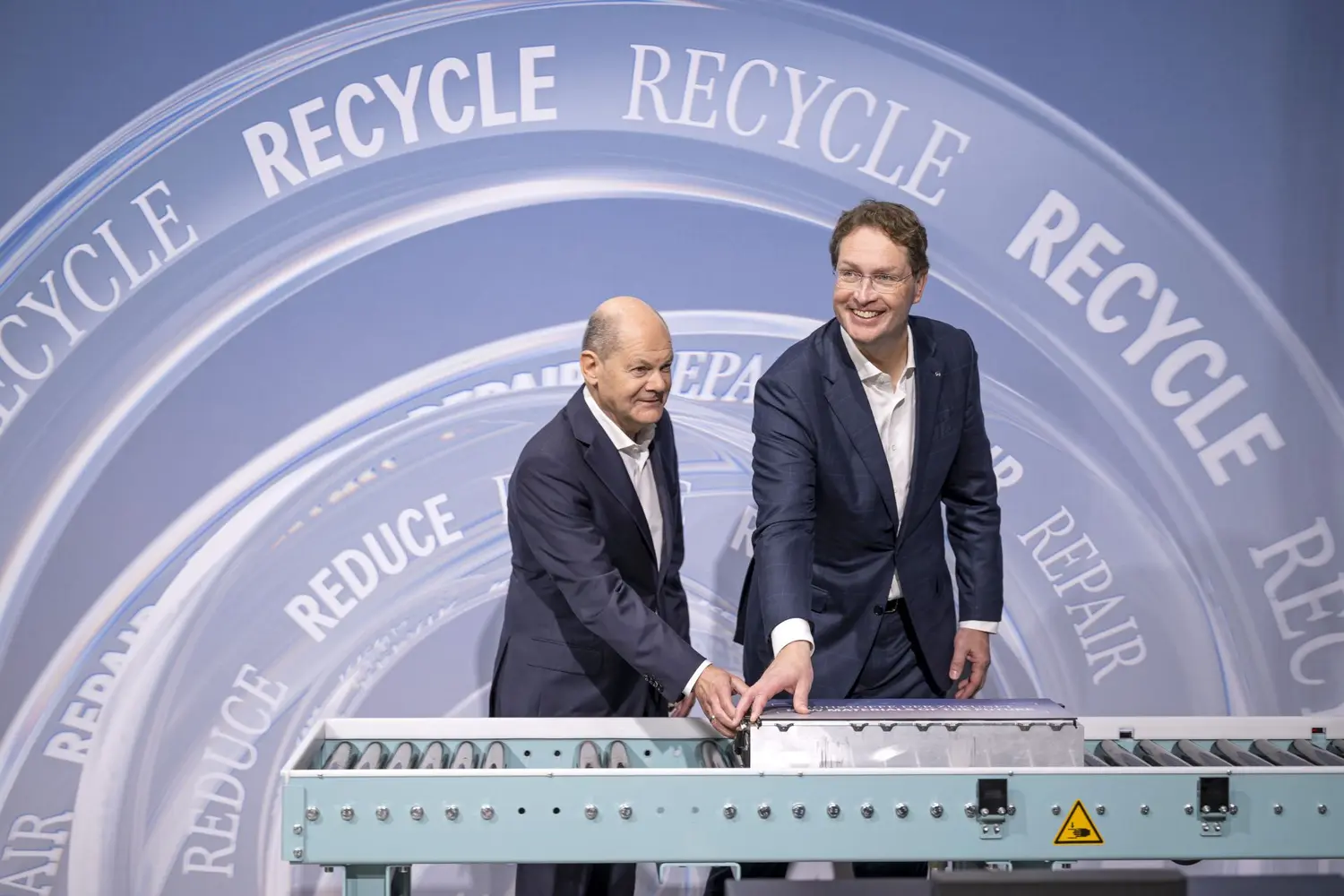