With more than 30 reference plants worldwide, CSP® (Compact Strip Production) is the leading thin-slab casting and rolling technology. With the typical configuration comprising a caster, tunnel furnace, finishing mill, cooling section and downcoiler, a CSP plant is able to produce 1.5 million t of hot strip per strand every year. It is characterized by comparatively low investment costs, a wide range of products, and high yield. Even ultra-thin final thicknesses of less than one millimeter can be produced on CSP® plants using the batch rolling or semi-endless rolling mode. With batch rolling, the slabs are cut into the corresponding coil size at the caster by the pendulum shear. In the case of semi-endless rolling, a so-called jumbo slab is cut by the pendulum shear and subsequently divided into several coils by the high-speed shear upstream of the coiler.
Rolling modes
While CSP® technology features the batch and semi-endless rolling modes, CSP® Nexus significantly expands the possibilities and offers real batch and endless rolling. The significant increase in the slab thickness up to 160 mm, in order to expand the product range in terms of grades and thicknesses, requires the use of a roughing mill. By decoupling the roughing and finishing processes, real batch rolling is possible, which is comparable with the rolling process in a conventional hot strip mill.
In the field of thin, high-strength and wide products (such as AHSS automotive steels), other casting-rolling concepts need energy-intensive endless rolling, where the caster is coupled to the roughing and finishing mill, in order to produce the desired final thicknesses. This is where CSP® Nexus offers the cutting-edge advantage of being able to produce a large share of the product portfolio by using the real batch rolling mode. The need for energy-intensive endless rolling technique can thus be limited to special applications such as ultra-thin strip (<1.0 mm).
What are the different rolling modes?
- Batch rolling: The pendulum shear downstream of the caster produces the desired coil size. The rolling mill is decoupled from the caster.
- Semi-endless rolling: The caster produces a jumbo slab. The high-speed shear upstream of the coilers cuts the strip to the desired coil size. The rolling mill is decoupled from the caster.
- Endless rolling: The high-speed shear upstream of the coilers produces the desired coil size. The caster, the roughing mill, and the finishing mill are force-coupled with each other.
- Real batch rolling: The pendulum shear downstream of the caster produces the desired coil size. The caster, the roughing mill, and the finishing mill are decoupled from one another.
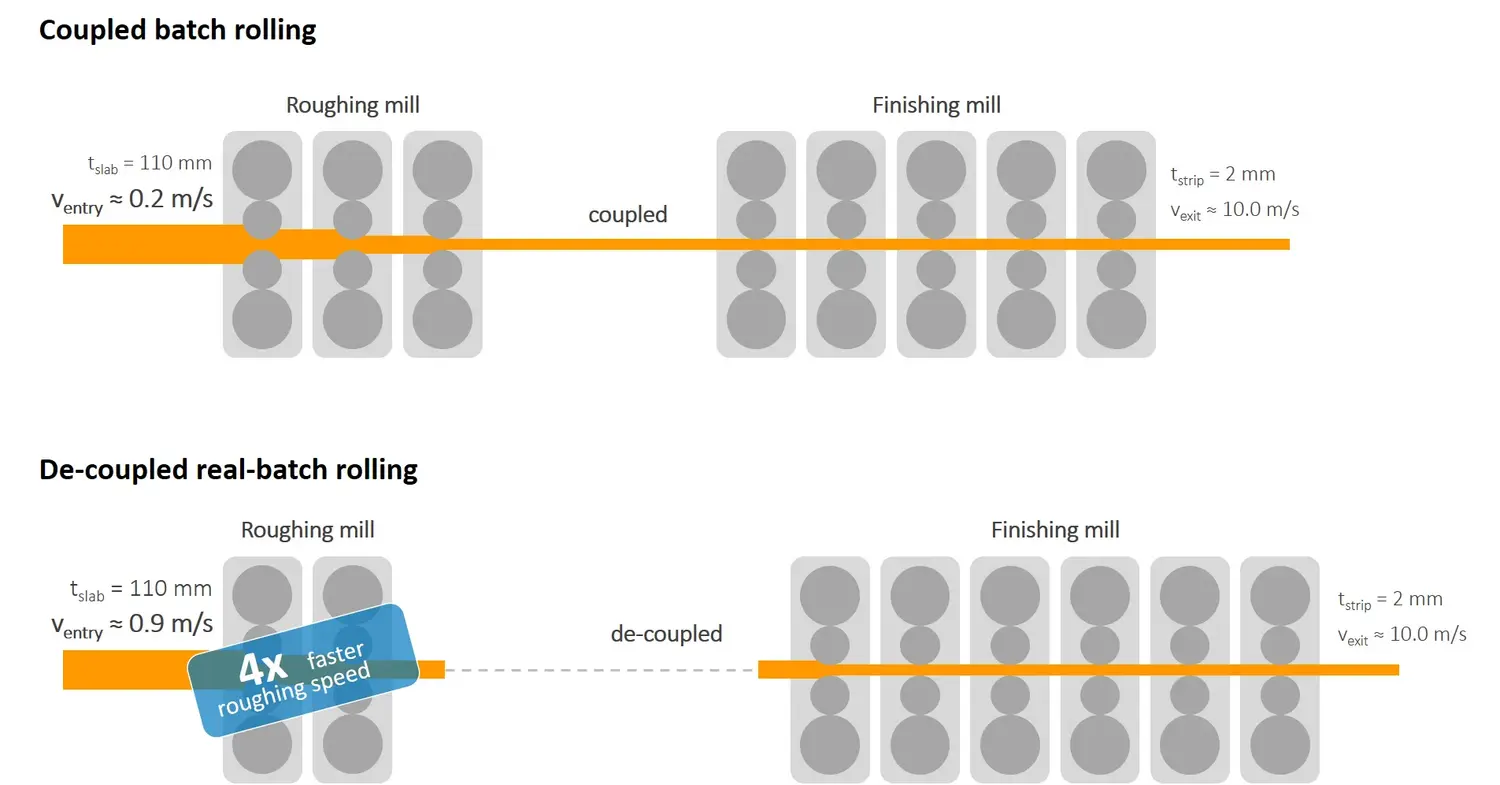
Real batch rolling with CSP® Nexus
In developing CSP® Nexus, SMS group has gone a crucial step further than conventional CSP® technology. With CSP Nexus, maximum sustainability meets maximum flexibility and productivity. CSP® Nexus includes possibilities that so far only a conventional hot strip mill could offer. The essential difference is that CSP® Nexus combines the decoupling of roughing and finishing phases with the benefit of customary temperature homogeneity and the efficiency of CSP® technology. The transfer bar area is equipped with a heated roller table to ensure temperature homogeneity. This decoupling has several advantages compared to the batch rolling of other casting-rolling concepts, where the roughing and finishing mills are directly interlinked and thus necessarily have to work in a force-coupled manner.
To achieve the energy-efficient production of certain steel grades, the roughing speed is substantially increased, thus minimizing the time spent in the roughing mill. This means that temperature losses are also reduced to a minimum and energy is saved. In particular, the greatest energy savings can be achieved with products that in coupled batch/endless plants can only be produced in endless rolling mode. In endless rolling mode, there is basically no flexibility regarding optimum speed selection, so that the temperature losses are high and need to be compensated by an induction heating system. Accordingly, CSP® Nexus is using the option of endless rolling only where this is beneficial for the process.
Furthermore, the decoupling of roughing and finish-rolling enables the optimum roughing mill speed to be selected independently, so that the temperature of the transfer bar can be precisely set. This is particularly necessary for products that have to meet high demands in respect of thermomechanical rolling (e.g., API pipe grades).

Thin strip in combination with high final rolling temperatures
For certain products, a combination of thin final thicknesses, e.g., less than two millimeters, and high final rolling temperatures, e.g., above 880 °C, is required. Such products include, for example, ultra-low carbon steels, electrical steel, or high-strength low-alloy (HSLA) steels. Thanks to the possibility of considerably higher roughing speeds with a decoupled roughing mill, the temperature level in the area of the intermediate strip and in the first passes of the finishing mill can be increased substantially, resulting in:
- Far higher final rolling temperature with the same final strip thickness or
- Significantly thinner final strip thicknesses at the same final rolling temperature
The diagram below compares the final rolling speed and temperature for different concepts. It shows that with CSP® Nexus, high final rolling temperatures can be achieved even when rolling thin strip at moderate rolling speeds.
In plants with coupled roughing and finishing mills, the lower temperature level in the intermediate strip must be equalized with high power induction heating. This creates an additional area that, if coupled, must be passed through at low speed and with correspondingly high temperature losses. During batch rolling, plants with coupled roughing and finishing mills already reach their limits in terms of finishing rolling speed and temperature level at higher strip thicknesses. To avoid significant increase of chattering tendency and other quality issues, it is necessary to switch to the energy-intensive endless rolling process much earlier.
Accordingly, the CSP® Nexus predominantly employs endless rolling only where it makes sense from a process point of view. With the production of ultra-thin strip (<1.0 mm) in particular, the rolling process benefits from the increased stability of endless rolling, which in turn justifies the greater amount of energy required.
In real batch rolling, in contrast with endless rolling, it is also far easier to make greater thickness, width, and grade changes from one strip to the next. Roll changes can also be performed any time during a real batch rolling campaign, without having to interrupt the casting sequence. As a result, real batch rolling enables the design of a very flexible rolling campaign, while, at the same time, ensuring a high level of availability.
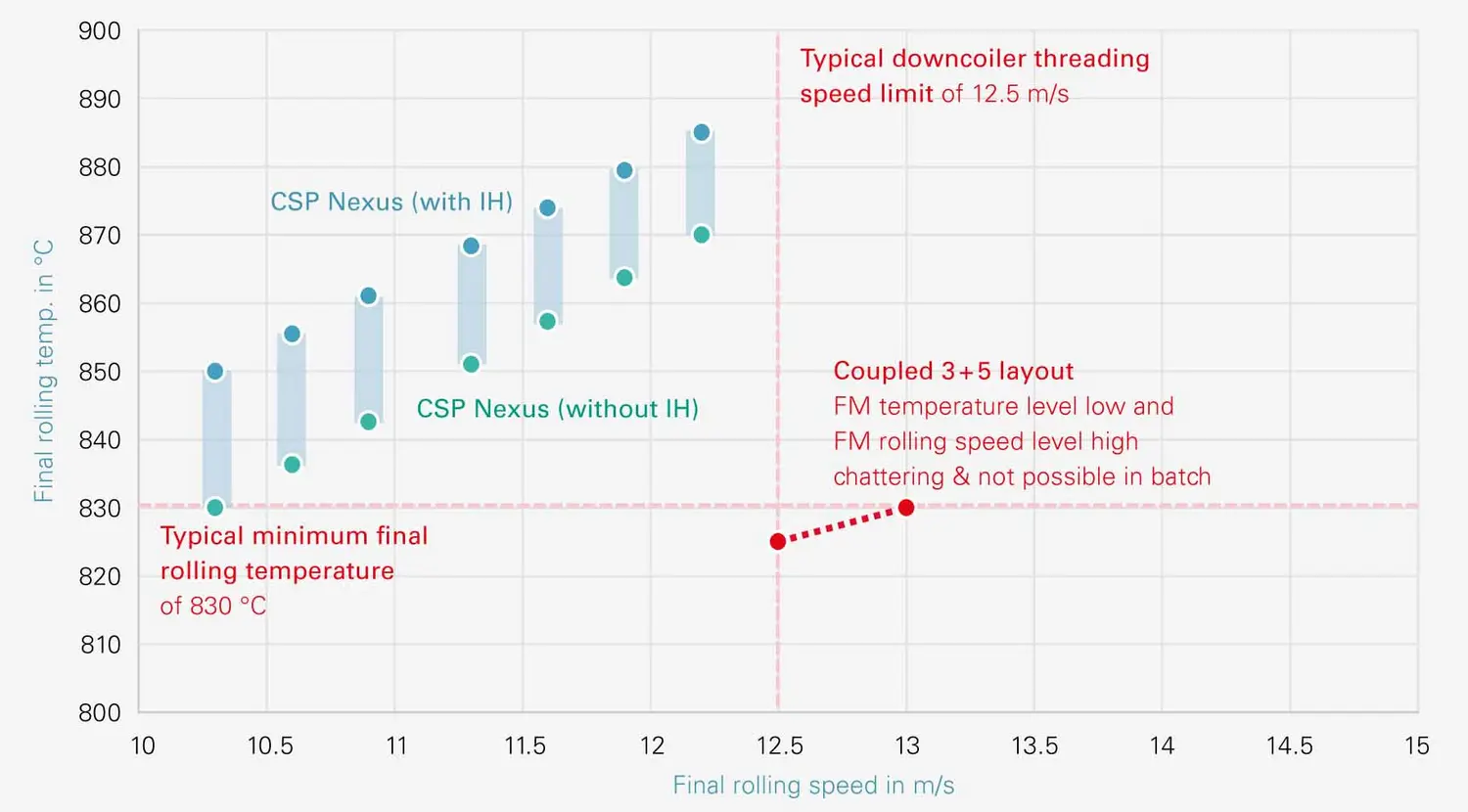
Highly efficient integrated process models
To increase the overall energy efficiency of the process, SMS incorporated the X-Pact® Integrated Process Model (IPM) in the level 2 automation system. The process model coordinates the results of the existing individual level 2 models such as X-Pact® Solid Control, X-Pact® Pass Schedule Calculation (PSC) or X-Pact® Cooling Section Control and considers the whole temperature evolution of all thin slabs from casting to coiling. It sets up the process prior to rolling in the most energy efficient way while maintaining the target dimensions and properties. Depending on the actual production scheme, the furnace temperatures can be set as low as possible to achieve the desired final mechanical properties and dimensions. Furthermore, the rolling load in the mill stands as well as the increased speed level in the cooling section, including an energy-optimized water pump setting, are taken into account.
Moreover, the integrated process model enables higher productivity. The casting thickness can be optimized to attain maximum productivity, while at the same time ensuring that the desired final thickness and width after rolling can be achieved. In addition to the extensive process controls and models, X-Pact® Centerline Control is an integrated strip flow control system that ensures the stability of the rolling process. A closed-loop control circuit detects strip centerline deviations and calculates proper tilting set-points for each mill stand. Various control strategies are used for the different rolling sequences (strip head end, main body, and strip tail end). SMS group’s integrated strip guide package comprises mechanical side guards, control strategies for adjusting the roll gap, and camera-based measuring systems for real-time control of the strip position.
Since real batch rolling was created on the basis of the conventional rolling process, the many years of experience gained in this field can be brought to bear. The high flexibility and quality of the X-Pact® Profile Contour and Flatness Control (PCFC) model, in particular, is a unique selling point. As plants that mainly operate in endless rolling mode have to focus on extending the rolling campaigns, their rolls are used with correspondingly wear-optimized roll barrel grinds, which means that continuously variable crown
(CVC®) technology cannot be applied. With the X-Pact® PCFC model in combination with customized CVC® grinds on the rolls in the finishing mill, the focus is on maximum quality and flexibility. Using special shifting strategies, such as “cyclic work roll shifting,” these advantages can also be combined with a wear-optimized operating mode.
The result is an extremely reliable product that ensures high plant availability on the one hand and hot rolled strip of extraordinary product quality and close tolerances on the other. Which is the reason why, over the last few years, SMS group has received a consistently growing number of inquiries and orders by customers who want to replace their work roll bending and shifting systems, delivered by other suppliers, with new short-stroke CVC® systems including the PCFC® model.
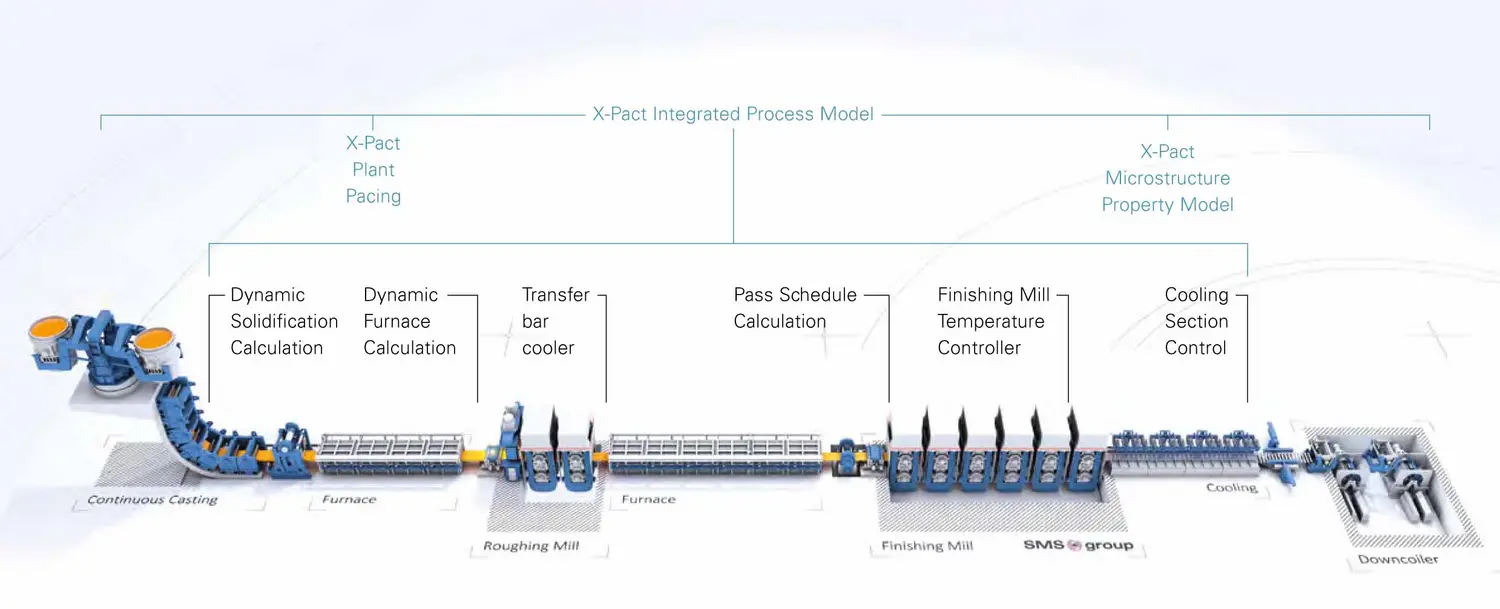