Established about 50 years ago as Demag Ltda., SMS group Metalurgia do Brasil Ltda. is a 100-percent subsidiary of SMS group. It serves the South American market with all products contained in the SMS group portfolio.
Since its foundation, SMS group Metalurgia do Brasil Ltda. has managed to successfully complete numerous projects of SMS group in the steel and nonferrous metals sector, including metallurgical plants such as electric furnaces for steel and ferroalloys, converters, secondary metallurgy plants, continuous casters, hot and cold rolling mills as well as processing lines for long and flat products and also several projects in the field of forging technology and extrusion presses.
The result of this broad range of experience is a technically highly qualified staff able to quickly respond to local market requirements and to offer high quality at competitive prices. In Brazil, SMS group employs a total workforce of more than 150 persons distributed over three locations.
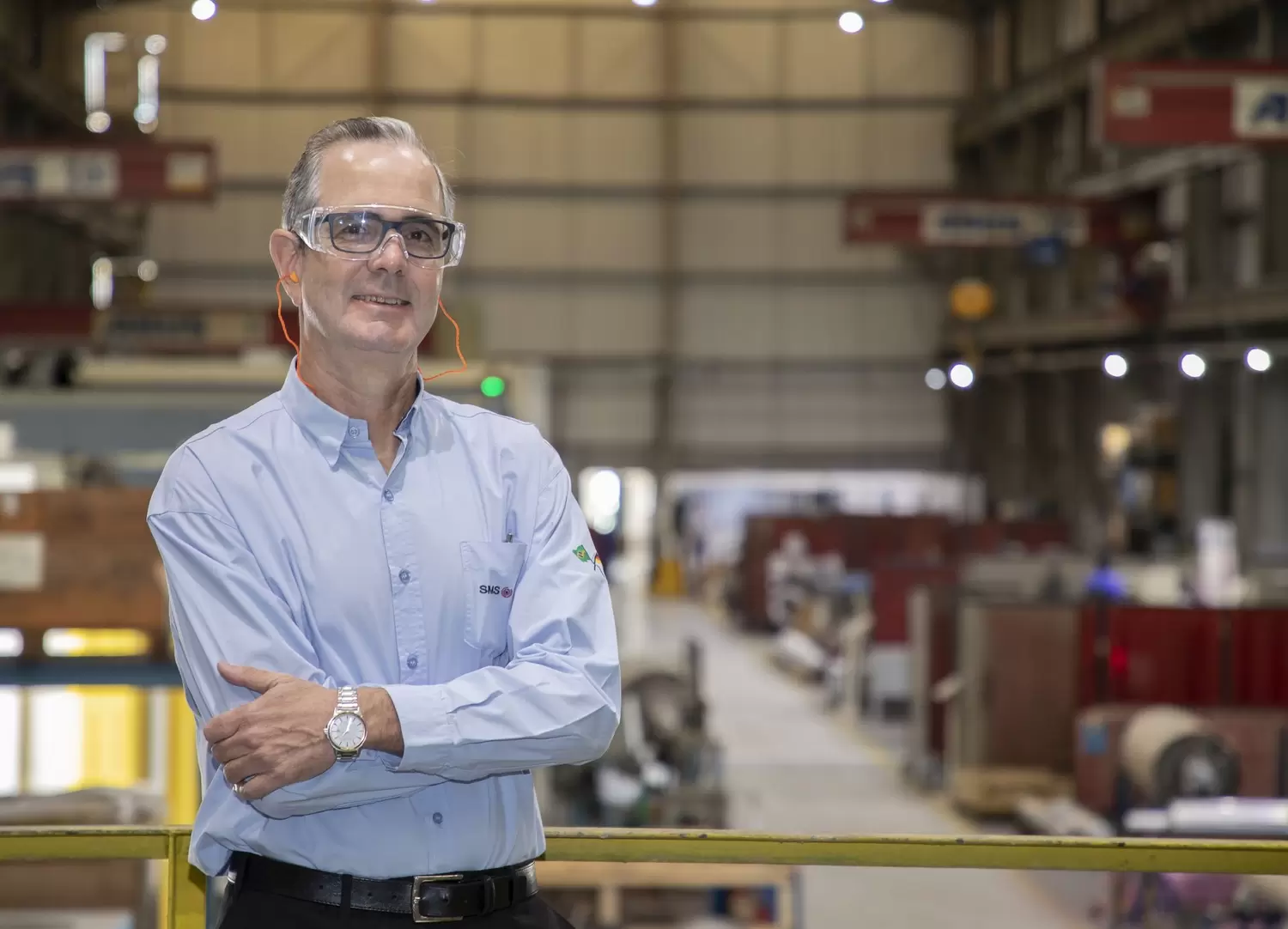
Vespasiano: Headquarter and central workshop
The headquarters of SMS group Metalurgia do Brasil Ltda., including main office and workshop, is located in the city of Vespasiano close to Belo Horizonte. Representing the majority of sales force, engineering team, workers and administration staff, about 130 persons are working at this site.
The workshop comprises an area of 2,000 square meters and specializes in the repair and upgrade of products, for example copper plates, including the UNIGUARD™ premium coating, rolls from processing lines such as zinc pot and furnace rolls, core components from rolling mills like mandrels and coilers, caster molds and segments as well as parts for submerged arc furnaces.
Besides the complete electroplating facilities needed to repair cooper plates of slab caster molds, the workshop is equipped with a thermal spray unit, an HVOF (High Velocity Oxygen Fuel) machine and a five-axis machining center supplied by reputed European companies.
In addition, the Vespasiano site has a dedicated workshop to manufacture welded parts like BOF hoods, ducts for cooling stacks, cooled panels for electric arc furnaces and submerged arc furnaces, electrode arms and columns, ladle furnace and EAF roofs as well as dedusting channel parts. Long-life performance of the cooled parts is ensured through special coatings applied by welding or spraying. This makes customers benefit from high quality combined with favourable prices.
The technology to manufacture laying head tubes for wire rod and bar mills has been provided by the SMS group headquarters in Germany.
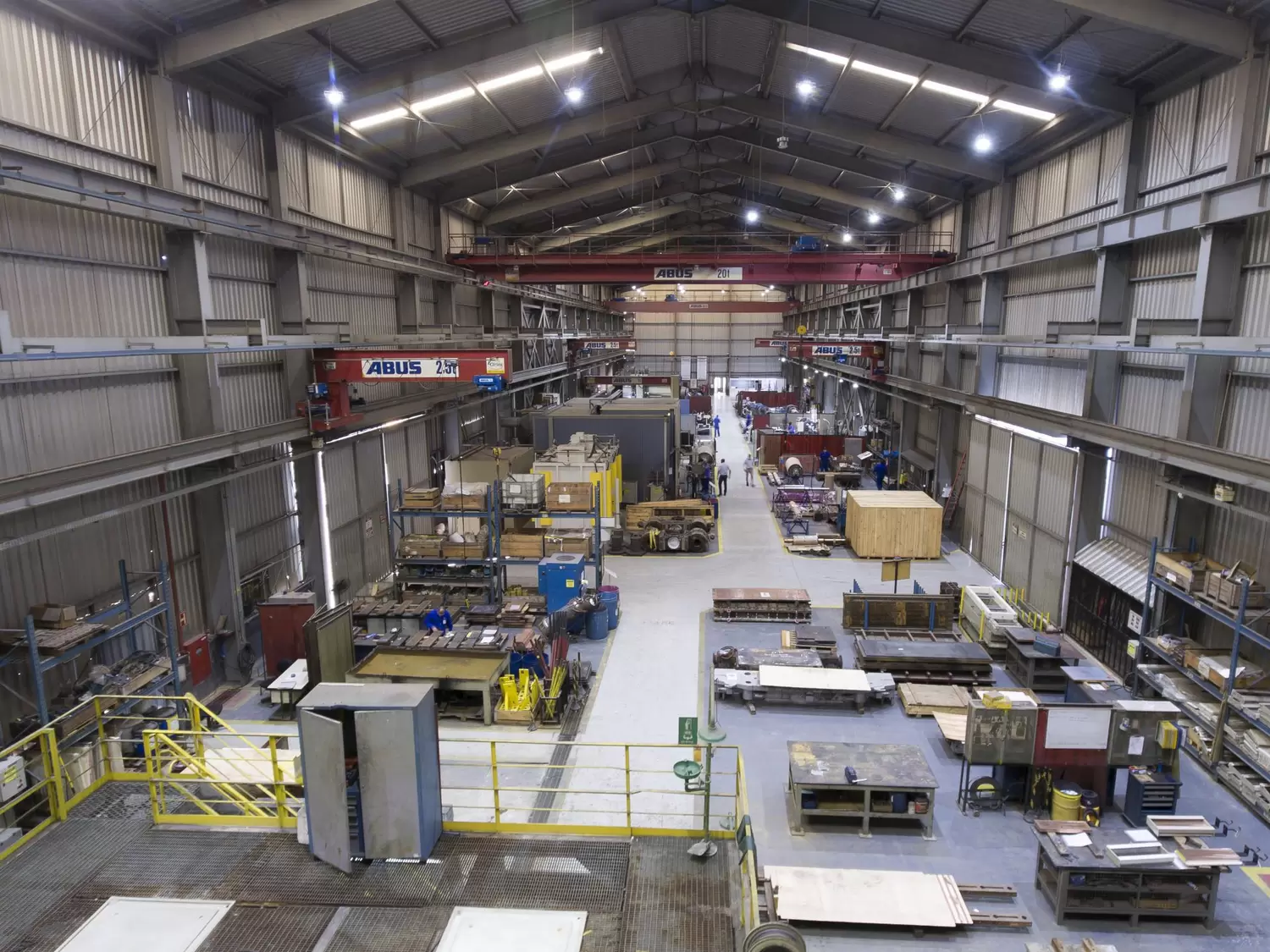
Workshops in Serra and Santana do Parnaiba
Employing a force of more than 30 experts, the Serra workshop is located in the city of Vitória and started its activities in 2010. Based on long-term contracts, it exclusively dedicates to the repair of segment rolls from continuous casting machines and can be considered an extension of the mold and segment workshops of the customers. Among others, the activities comprise caster rolls assembling and disassembling, spare parts management, roll cladding and the performance of tests.
Our office with workshop located in Santana do Parnaiba city, close to São Paulo, concentrates on the scope of SMS Elotherm and specializes in the supply and repair of inductive furnaces and components for the automotive, forging and extrusion industries. The facility counts ten employees.
Our services: Diagnoses, modernizations and repairs
With a strong engineering team using the most modern software, tools and proven methods, SMS group Metalurgia do Brasil Ltda. can identify customers’ needs by a first diagnosis of the equipment condition. Whenever applicable, the specialists perform on-site 3D scans, thermographic measurements, NDT tests, metallographic analyses, dimensional tracking via laser and visual checks using augmented reality glasses for connection with the worldwide SMS experts to identify critical points. The on-site measurements are evaluated taking into account the experience gained from worldwide reference projects to propose the best technical solution. All of this is done by means of 3D modelling, finite element analyses (taking into consideration the 3D scans collected on site) and computational fluid dynamics simulation.
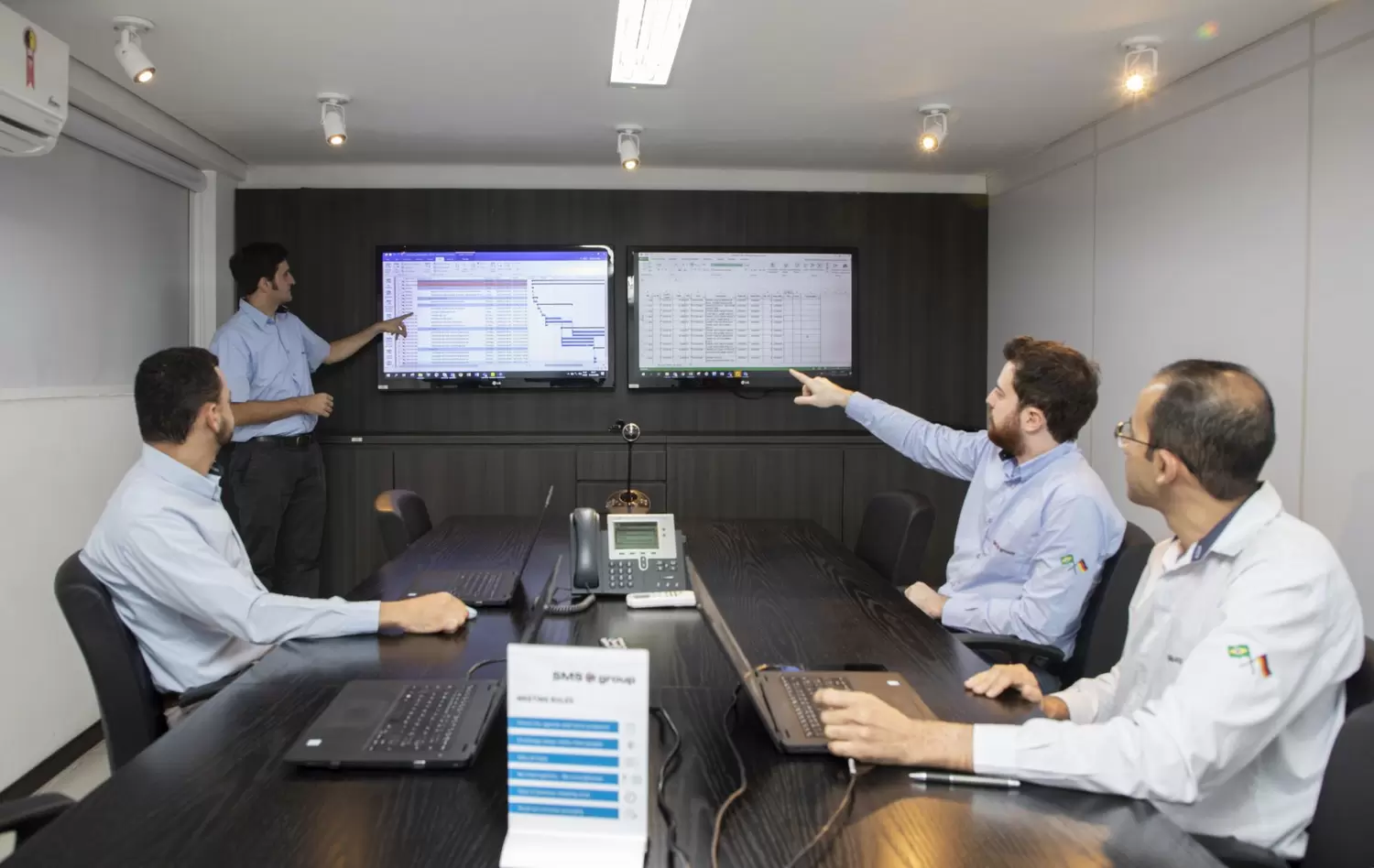
Some recent examples:
- Redesign and optimization, based on thermal analysis, of cooper plates and tundish of continuous casting machines, steel and pig iron ladles, etc. Such upgrades improve performance and equipment availability.
- Calculation of equipment residual life to avoid accidents and loss of production, giving the customer the opportunity of a more detailed maintenance planning.
- Capacity increase and campaign optimization of electric furnaces and ladles.
- Customized saving of staff in the operational area through modern technology.
- Equipment redesign aiming at better maintenance conditions, reliability and performance of roller tables, caster molds, rolling mill stands and mandrels, among others.
Field service
Safety, quality and meticulous planning are the issues the field service experts in Brazil pay particular attention to. The service portfolio of SMS group Metalurgia do Brasil Ltda. includes scheduled and non-schedule maintenance activities, assembly work, repairs and modernizations at the customer’s site within the complete portfolio of SMS group. Examples of recent services:
- Repair and refurbishment of converters: four references over the last two years, comprising the replacement of a complete vessel or its parts, such as trunnion rings and linear guides
- Slab caster alignment
- Boiler repair in a thermal power plant
- Torpedo car repair
- Rolling mill stands for flat and long products: alignment work, replacement of liners, upgrade and adjustment of drive systems
- Alignment of extrusion and closed-die forging presses.
Product highlights: Copper plates of caster molds
The Vespasiano facility is designed and fully equipped to offer to the local market, on an exclusive basis, the UNIGUARD™ technology of ceramic coating that makes the mold achieve excellent results.
The UNIGUARD™ coating method for copper plates is a breakthrough in mold coating because it unites a hardness of 1,100+ Vickers, which rivals hard chrome, and the ability to withstand the meniscus temperature of most continuous casting molds. As a result, the life of molds provided with UNIGUARD™ coatings is substantially increased, well beyond what was previously attainable. In addition, some steel producers may use the thermal properties of the UNIGUARD™ coating to alter the hot-face temperatures of near-scrap copper plates and, consequently, produce products with more consistent quality.
The traditional electroplating method for segment roll coatings with standard nickel and nickel alloy is also available.
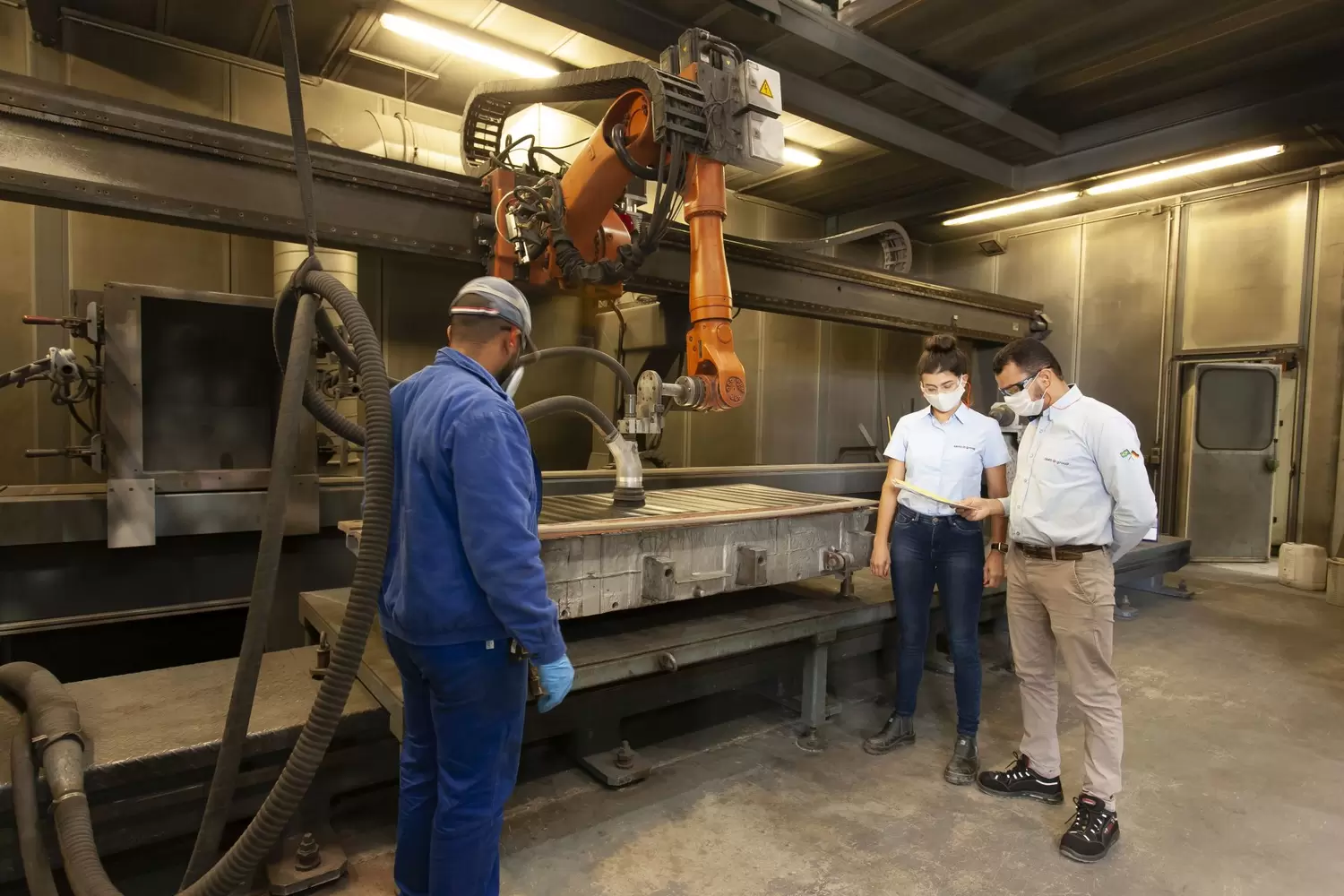
Product highlights: Repair of caster segment rolls
Repairing and manufacturing caster segment rolls is one of the key activities, regardless of OEM parts or other segment roll design. SMS group Metalurgia do Brasil Ltda. applies a weld overlay process that can be adapted to the caster segment roll condition as caused by wear and corrosion.
Long-bodied, short-bodied or shell-type rolls require different welding processes. Overlay materials, too, are manifold and address specific caster issues. The Vespasiano and Serra facilities are equipped for open-arc and submerged- arc wire welding and include all machines required for related services such as heat treatment, CNC turning, and milling.
The close and strong relation to other SMS group companies worldwide with years of experience in the repair of continuous caster segment rolls allowed the Brazilian colleagues to acquire the knowledge needed to offer reviews of the whole segment roll assembly. Based on the results thereof, the experts can suggest and carry out improvements to the housing design of bearings and to roll axles and couplings that will enable the customer’s segments to achieve record tonnages.
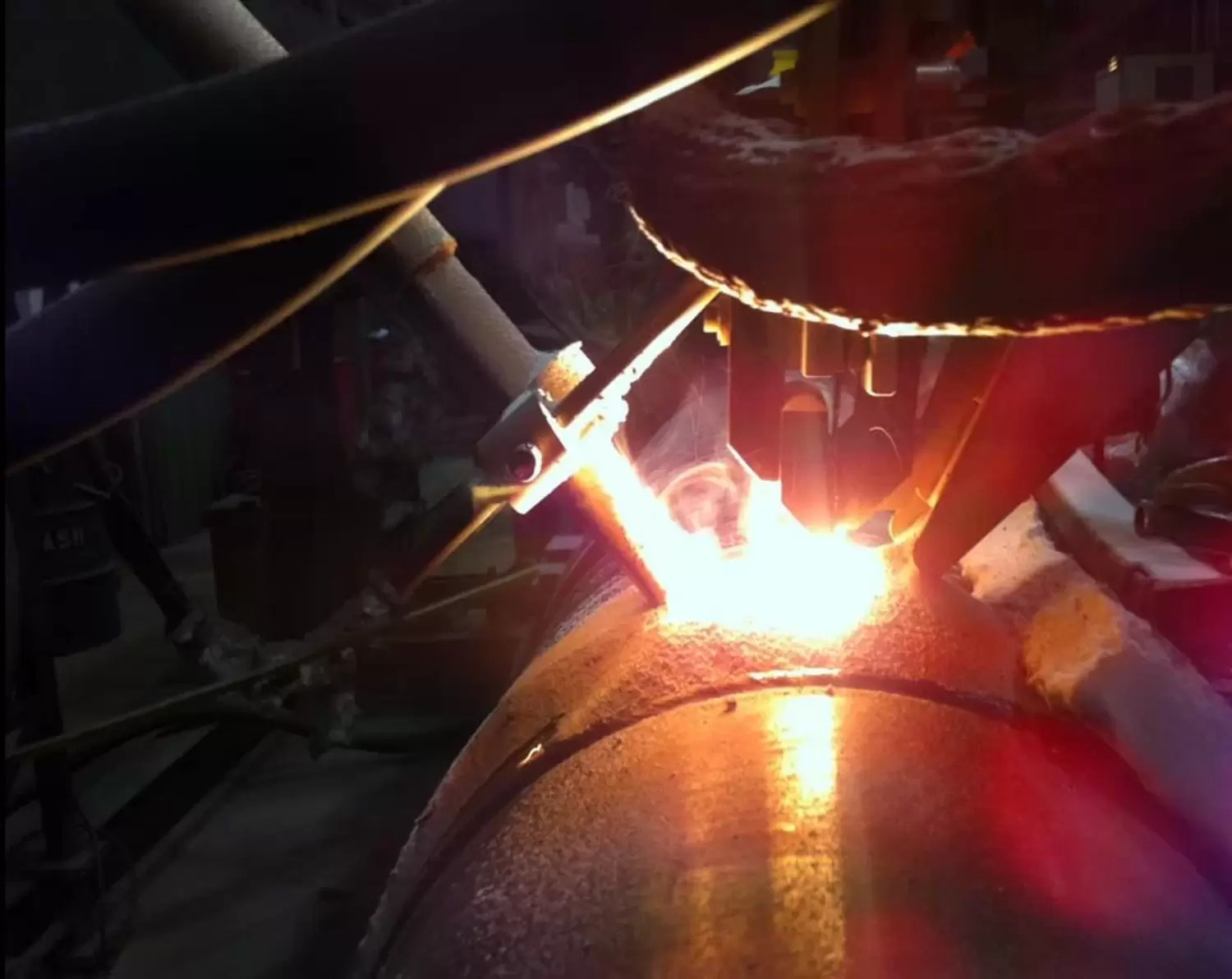
Product highlights: Repair of rolling mill rolls
The workshop of SMS group in Vespasiano is equipped with the most advanced technology to repair rolling mill rolls to the overlay cladding method, with the focus and expertise being targeted at most challenging rolls as are operating in hot rolling lines, for example descaler rolls, looper rolls, wrapper and pinch rolls.
Working closely with the South American customers to better understand their situation, their demands and challenges is an important factor. Paired with the work of the tribology and welding specialists, it is possible to create solutions for issues of welding wire and procedure that will help the customers achieve extraordinary results. In addition, continuous research opens up new opportunities to upgrade rolls and auxiliary equipment. This work is supported by the OEM know-how in hot strip lines and the CFD/FEM analysis performed by the engineering team.
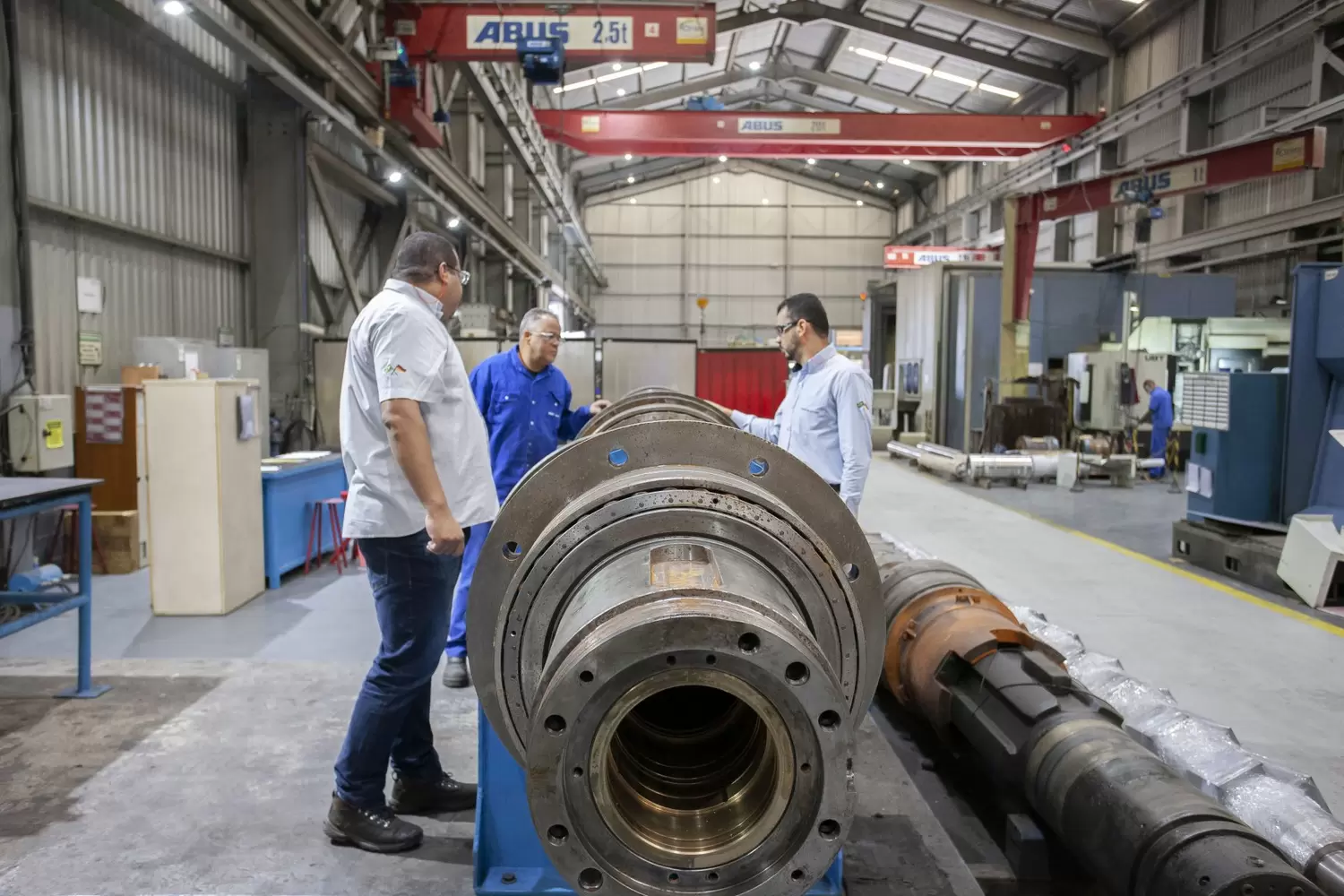
Product highlights: Repair of Continuous Galvanizing Line rolls
Rolls installed in continuous galvanizing lines (CGL) place particularly high demands. Their surface quality must always be perfect even in a very rough environment as a zinc bath with temperatures above 400 degrees Celsius or in a furnace with high tension, wear and temperatures of up to 1,000 degrees Celsius. To meet these challenges, SMS group Metalurgia do Brasil Ltda. relies on the OEM technology and know-how of DUMA-BANDZINK and Drever for the repair of CGL rolls. This applies to pot rolls and furnace rolls. Further support is provided by TOCALO Co., Ltd., Co., Ltd., the technological specialist for the development of powder and the coating process. Based on this strong partnership, CGL rolls can be repaired worldwide with best results. The process is standard in all SMS group workshops and is strictly controlled due to its technological complexity.
The first step of a CGL roll repair procedure is to carefully inspect the mechanical condition of the used roll. After that, the roll is machined, individually ground and prepared, in the case of sink rolls according to the special grooves, in the case of furnace rolls according to the accurate profile. In the next step, the HVOF (High Velocity Oxygen Fuel) machine applies the SMS group Cermet coating. With the objective of providing additional resistance to dross formation, the roll surface receives a further special sealing and heat treatment before it is delivered to the customer. All steps are closely monitored to ensure high roll performance.
Due to these developments on the Brazilian market it was possible to extend the lifetime of a zinc bath roll by 600 percent compared to conventional rolls. Achieving the highest performance level is a must that SMS group Metalurgia do Brasil Ltda. is always pursuing. The keys to meet this target are strong technological capacity and strict quality control of all steps taken in a CGL roll repair procedure.
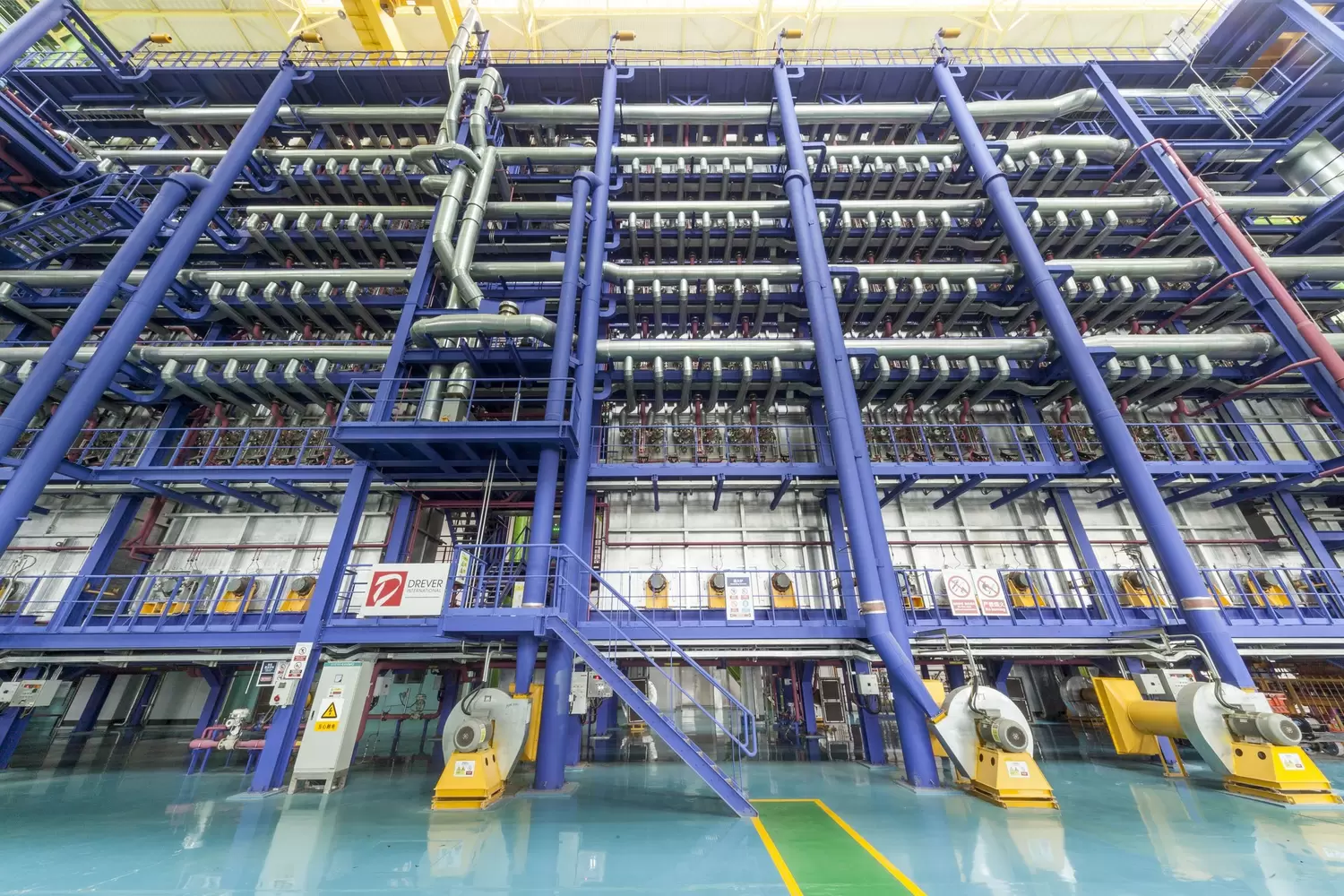