Even the latest, self-optimizing plant has to be maintained and repaired by a maintenance team. By the use of modern methods and tools, the quality and efficiency can be increased sustainably by smart maintenance. Often the current situation is that different kinds of approaches, products and solutions are available. Each of these tools deliver information and reports - but they are not linked to each other and do not have unified interfaces. In contrast, SMS group offers an integrated concept, called Smart Maintenance Solutions.
Actual situation
The upcoming digitalization offers a lot of meaningful new opportunities and possibilities. But at the same time there are plenty of applications which can cause more disadvantages than positive optimization. In order to find the right way through the „jungle” of digitalization and not to get lost in this biggest challenge we all are facing now, clarification has to be provided regarding current questions.
What is the actual degree of digitalization and how should it be in the future? What kinds of resources have been used in the past and what will be available for realization – and how will the time frame look like? First, there is the need of an overview of current solutions.
Condition Monitoring
State-of-the-art condition monitoring systems are permanently monitoring the key components of a plant. That means continuous provision of real-time information about the status of the components including warnings in order to take action when needed.
Genius CM® (Condition Monitoring) is a modular online screening system for steel plants. It tracks and documents the current condition of both: critical components and parts subject to wear. This is how Genius CM® adds completely new dimensions that help to optimize quality and availability. The installed sensors at all key plant parts along the process chain constantly transmit measured data to Genius CM®, including torque, vibrations, temperatures, forces as well as oil flow, particles and viscosity.
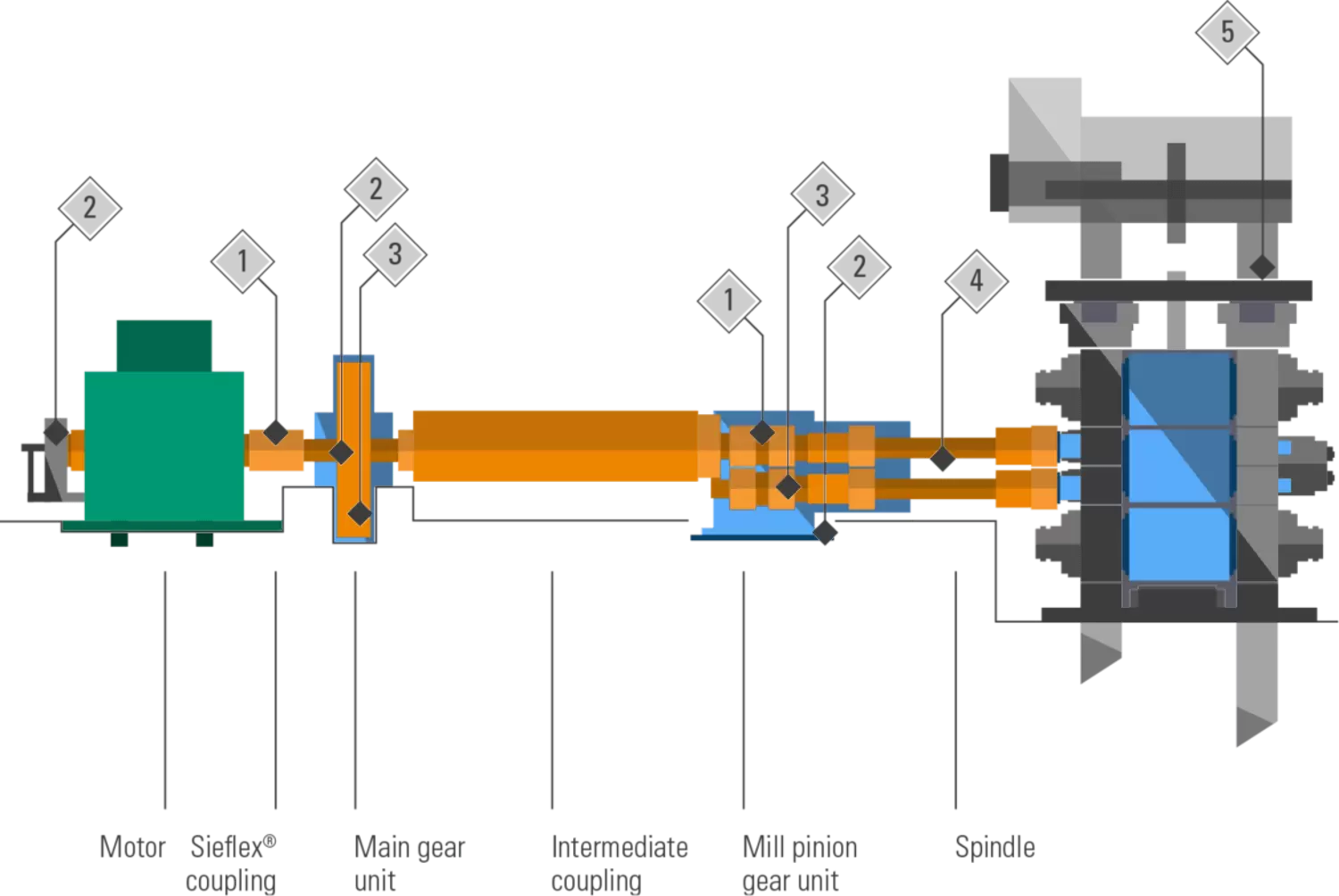
Unlike other analysis systems, Genius CM® compares the measured values with process data. Then it checks these findings against tolerances and triggers an alarm if boundary values are exceeded. This is how considerable damage can be avoided due to overstress and unforeseeable consequential damages before they happen. Unique to Genius CM® is its modular design so it can be suited to individual needs. The platform can be expanded and adjusted with individual modules at any time. In addition, Genius CM® includes the knowledge of the plant builder about design limits and specific tolerances of loads before damaging the equipment. As a result, everything from a single-component observation to a full-plant monitoring system is possible.
Constantly, new in-depth analyses are developed, e.g. of connecting-rod bearings in hot strip sizing presses. Ultrasonic sensors measure acoustic emissions over a much larger frequency range than before. This opens up far-reaching investigation opportunities e.g. for slow-rotating shafts in transmissions and sizing presses. Now the information can be recorded meticulously about the status for reliable evaluations at all times.
IMMS®
Building on the classic RCM (reliability-centered maintenance) model, ME-RCM (Maintenance Engineering RCM) from SMS group is a method that reflects real-life conditions specifically in the metallurgical industries. Furthermore, in line with the best practice method, SMS group simplified the servicing routine according to European standards, introduced the IMMS® (Integrated Maintenance Management System) to make maintenance processes more transparent and efficient and was achieved in cooperation with steel producers. Individual parts can be serviced using suitable maintenance measures, resulting in the optimum strategy for the respective equipment. The focus is on prioritized measures with the right level of documentation for more efficient results than the conventional methods. The IMMS® combines computer-aided maintenance with valuable data and establishes both plant and customer–specific data to an all-round package.
Through mutual harmonization, all software functions work together perfectly. The maintenance management system is practice-oriented and is based on the principles of reliability-centered maintenance and an ideal mix of repair strategies supported by the rules of failure mode effects and critical analysis (FMECA).
Smart Parts
In modern manufacturing, high-quality materials, a well-thought-out design, the latest coating techniques and intelligent sensor technology are indispensable for maximum productivity and quality assurance.
System solutions that utilize new sensor technologies with “Industrie 4.0” in mind open up a wide range of possibilities also e.g. in the field of continuous casting. Intelligent mold plate management is an example that allows increased service lives and new, individually detailed logistics concepts to be established. Process integration and digitalization of the mold enable to introduce new business models, which are likewise digitalized.
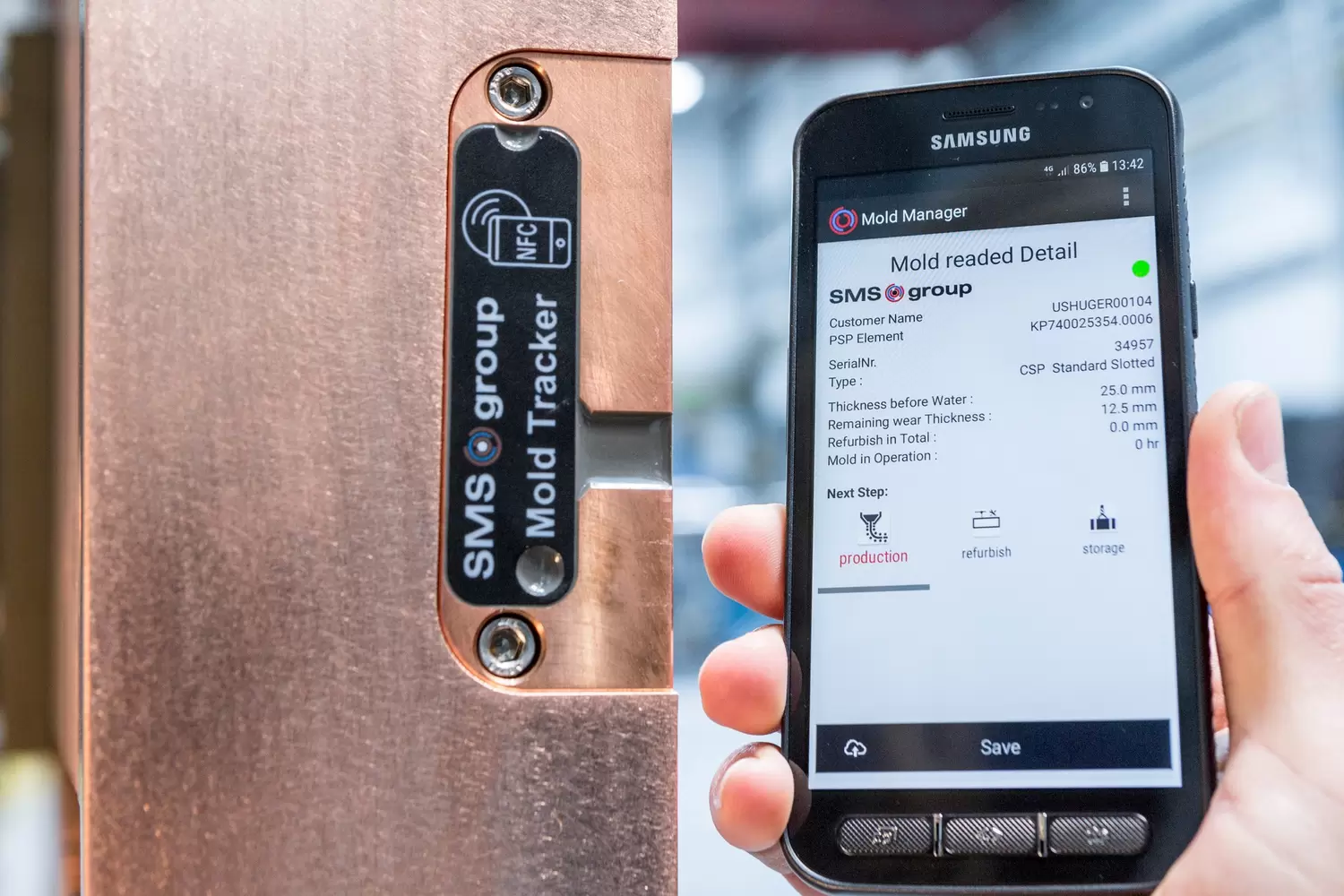
In the future, maintenance will no longer require large-scale and expensive storage facilities. Instead, stock-keeping will become faster and more transparent. Spare parts will be delivered in near-real time after the manufacturer has been informed online about the current degree of wear, likewise in near-real time. The operating hours and the wear on the individual plates are monitored in a continuous and fully automated manner and logged for subsequent evaluation.
This results in advantages and synergies for improved planning and logistics, greater flexibility and quality in production, as well as an immediate overview of the condition of the mold plate as a core component and the conditioning work performed thereon. The smart parts of SMS group are summarized under the name of 4io Parts.
eDoc
The digitalization of technical plant documentation offers new possibilities to increase efficiency and is an important step on the way to a 'learning steel plant'. The electronic catalog provided by SMS group is a technical plant documentation in a cloud solution. Digitalized documentations offer new ways to increase efficiency. For the US-steelmaker Big River Steel (BRS), thousands of documents were prepared in this structure and can now be used with a single tool. The database integrates a total of approx. 410,000 bills of material items, 30,000 drawings and 45,000 individual documents from the SMS group business units involved and from all sub-suppliers of single parts or assemblies which can now be called using a single tool after they have been consolidated and specially prepared in structure for this purpose. The new tool permits Big River Steel to identify and inquire parts quickly and easily. All data are continuously updated and, up to now, used by about 70 internal Big River Steel employees. Time-consuming searching for required information is a thing of the past. Further functions such as displaying identical parts throughout the entire plant, provide Big River Steel with the desired transparency and contribute to increasing efficiency and reducing the inventory.
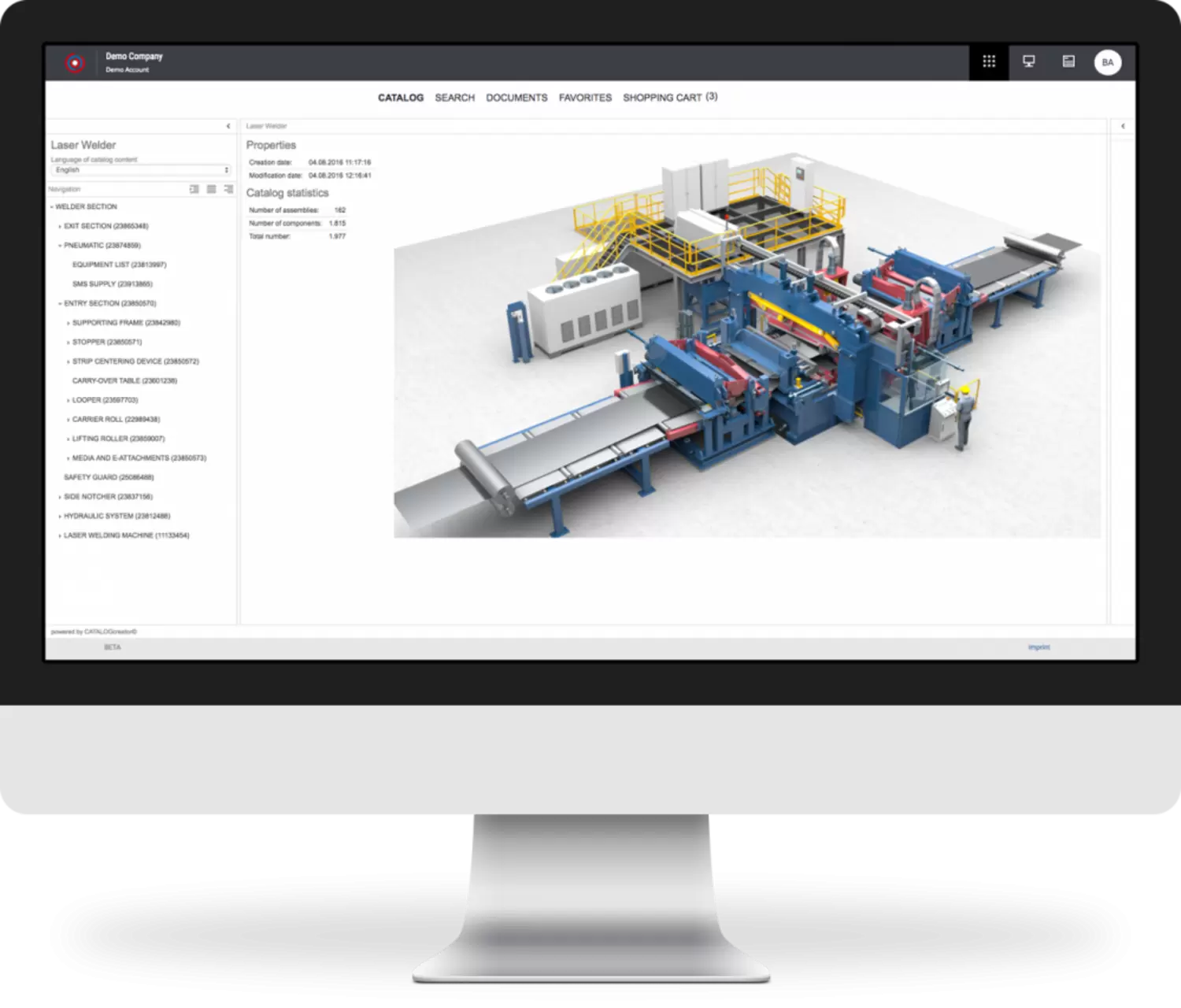
Randy Martin, Warehouse Material Coordinator at Big River Steel, is enthusiastic about the electronic parts catalog: “The catalog is very helpful, and we use it in the warehouse several times a day. But also maintenance people ask for our help in finding parts with the new system and see obvious benefits from the program. We can search for parts by title, material information, SMS group and Big River Steel material numbers, etc. The software is available around the clock seven days a week.”
In addition, the electronic parts catalog serves as the basis for further digital products. Being a virtual image of the plant, it allows digital services to be linked to purchasing actions. The required technical information is immediately available in all applications and can directly be transferred to the procurement process. If, for example, the condition monitoring system forecasts the failure of a component, it will be possible to simultaneously check information on identical parts, inventory and delivery times and to procure the wanted part. The eDoc of SMS group provides the foundation for Big River Steel for future challenges and satisfies all conditions to cope with the fourth industrial revolution – Industrie 4.0.
Big Picture
Smart Maintenance Solutions – this concept links production requirements to the machine status in order to identify, report, analyze and control the critical success factors.
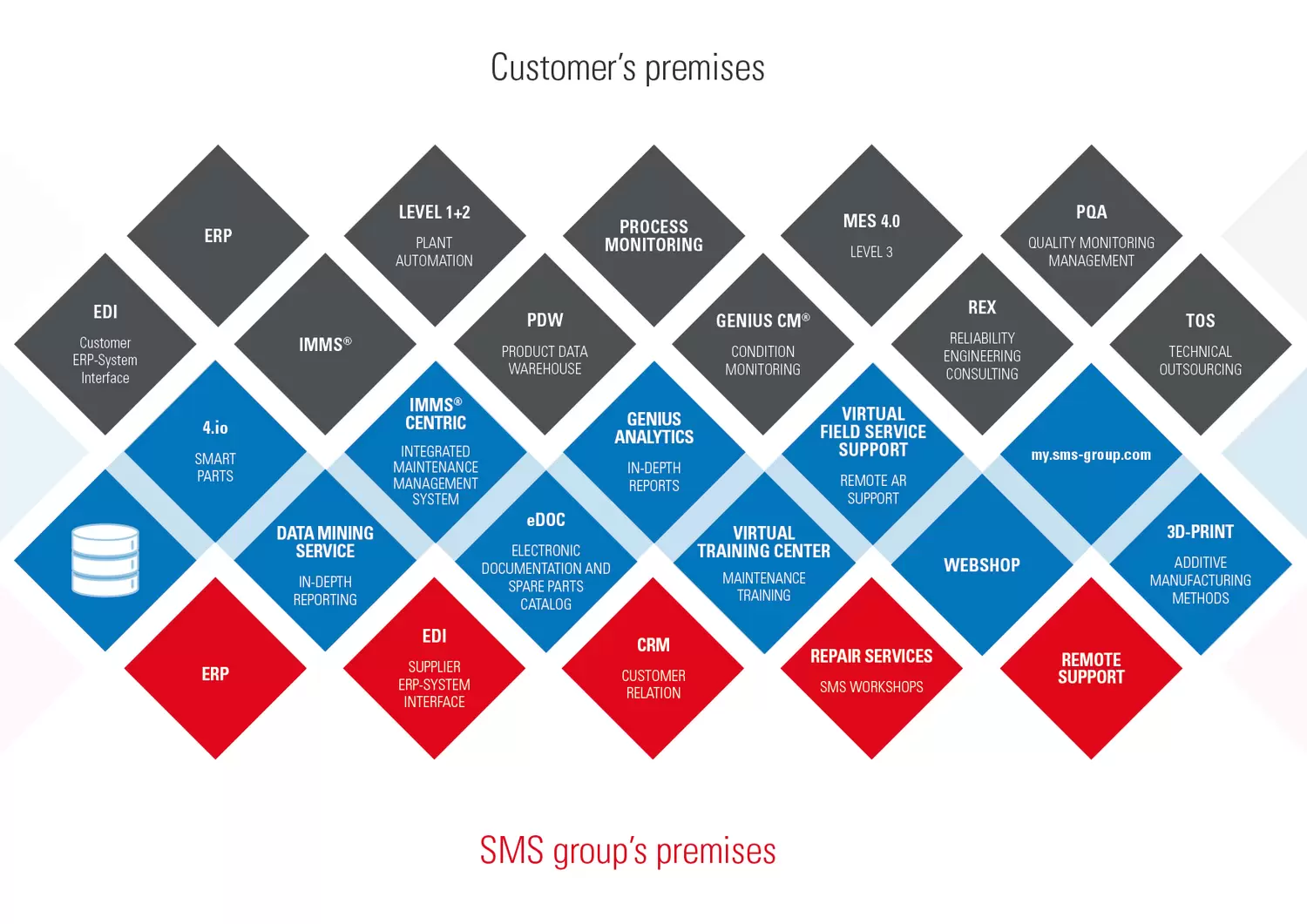
Between the premises of the customer and SMS group, there is a stream of systems, tools and products that will be merged in one big data warehouse. Step-by-step these solutions will create a landscape to a successful path towards Smart Maintenance Solutions by SMS group.
Despite all the euphoria, the first step will be trailblazing. By the use of a fact finding assessment the maintenance department will be evaluated, and not only regarding to the skills and the processes within the department, but also in the perspective of the possibility and chances for the complete plant. In its role as a leading partner in the metallurgical industry, SMS group will evaluate and discuss implemented tools as well as propose new developments in order to determine manageable steps to come as close as possible to the targeted vision.
Outlook
In future both sides – customers and SMS group – can be connected by an internet platform and all different kind of data will be sourced in just one database. By the use of new algorithm “Data Mining Service” in-depth reports will be the extract. Or in other words: the critical success factors of maintenance then can be identified, reported, analyzed and controlled.