By concentrating on characteristics such as high productivity, flexibility, product quality, availability, and safety, X-Pact® (PROCESS AUTOMATION CONTROL TECHNOLOGY) provides a solid foundation for both current and future requirements for the casting process.
Extensive diagnostic and assist features facilitate the interaction of the operating and maintenance personnel with the process and related equipment. As these focus on the actual process data and steps, non-productive times are noticeably shorter and there is less need for operator intervention.
With our integrated solution for process guidance, all quality-related data and parameter settings are provided centrally and several systems are combined in one user interface. This allows everyone involved in production (managers, metallurgists, maintenance personnel and operators) to improve the product and expand the product range.
Highlights
- Power supply and drive systems for greater sustainability
- Modular basic and process automation packages with process and production models
- Digital commissioning of automation systems during the X-Pact® Plug & Work integration test
- Innovative X-Pact® Vision HMI-concept for smart operation and visualization
- New standard for the future automatic control with X-Pact® Process Guidance
- Diagnostics for startup, devices, sequences, safety, and plan
- Quality monitoring and predictive system for condition analysis
- Fast start-up and commissioning
- Perfect infrastructure for remote support with X-Pact® Service
- Innovative measuring systems
OT products and solutions for slab casters
X-Pact® implements the vast technological experience of SMS group, developed over many years of supporting our customers. The challenging product diversity, high throughput, and required product quality are key parameters in the design of our X-Pact® technology packages.
X-Pact® Cast Optimizer
assigns order data to production data, optimizes width adjustments, cut lengths, and casting speeds, and tracks and documents the whole production process
HD moldTC (TC – Thermocouples)
transparently maps the casting conditions inside the mold and points out surface defects
X-Pact® Solid Control
monitors and calculates the strand solidification and optimizes the cooling conditions under variable casting conditions
X-Pact® Level Control
ensures highly dynamic steel flow control for a stable mold level
X-Pact® Width Control
includes delta speed adjustment, which allows for larger width changes with shorter transition lengths and less stress on the strand shell
X-Pact® Oscillation Control
ensures always perfect surface quality
X-Pact® Gap Control
enables Liquid Core Reduction (LCR plus), with which the slab thickness can be variably adjusted to the optimum entry thickness in the mill
X-Pact® Tech Assist
manages all techno-metallurgical parameters in one centralized system and creates individual independence
X-Pact® Condition Advisor
guarantees the transparent plant
X-Pact® Slab Cooling
X-Pact® Strand Drives
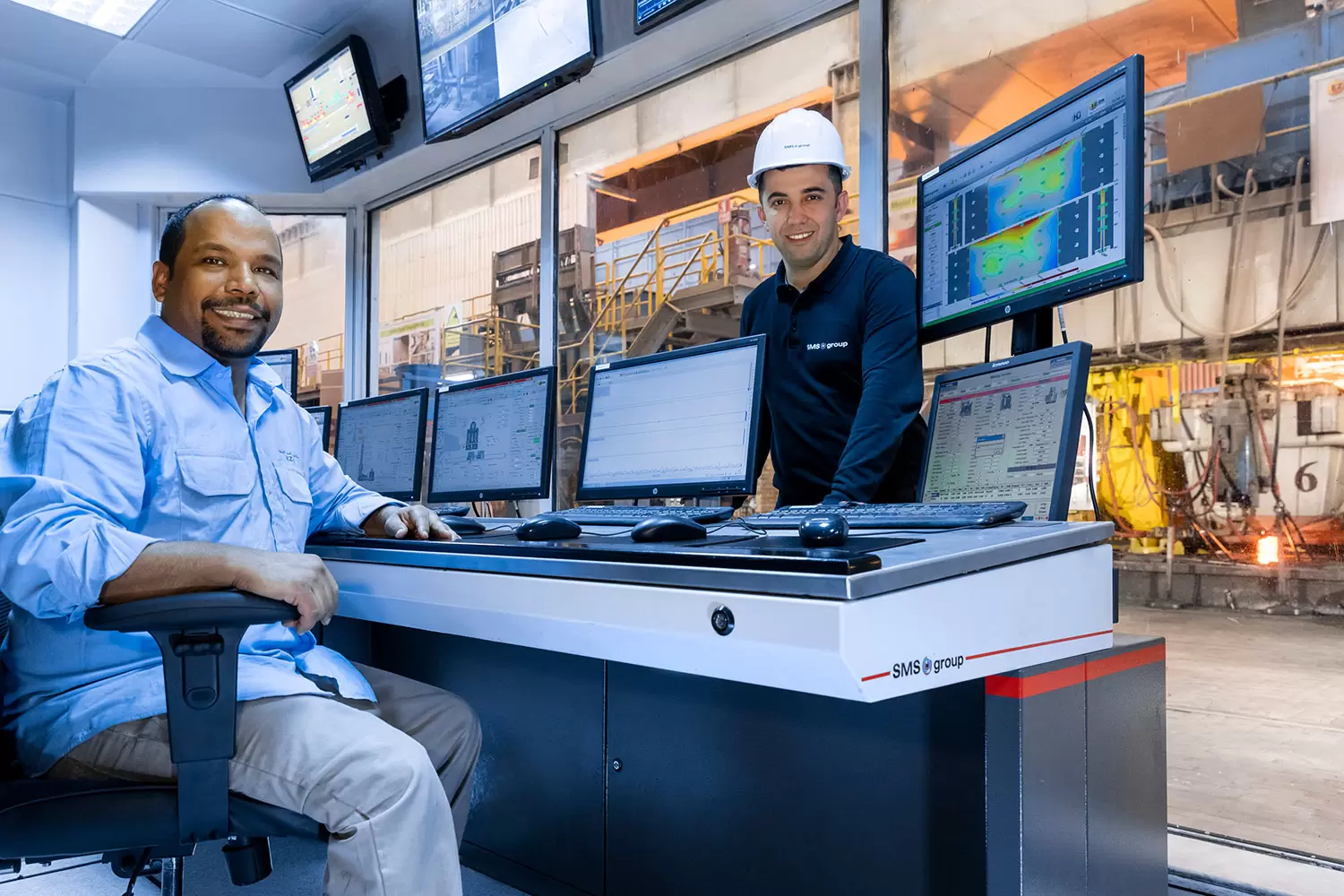
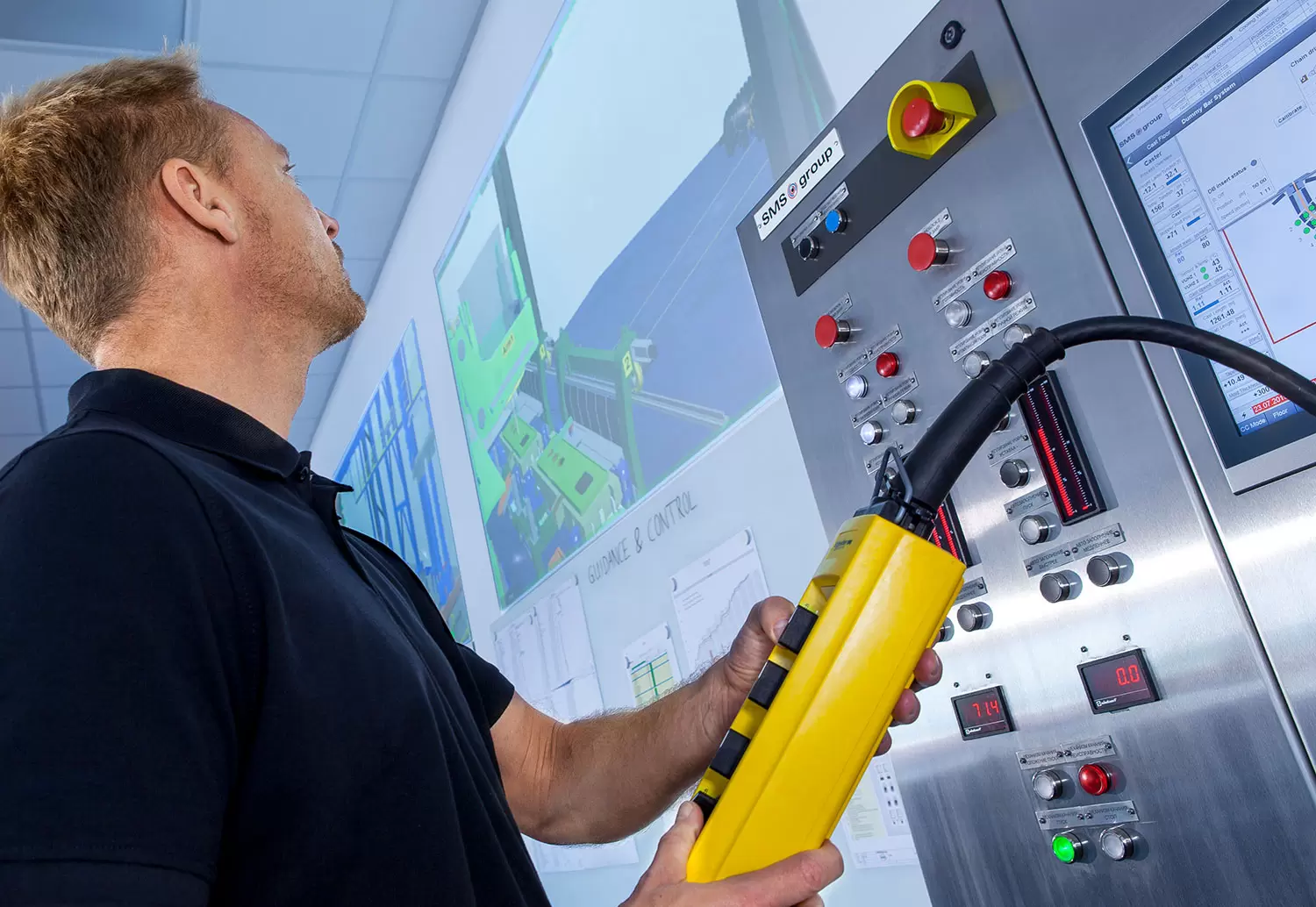
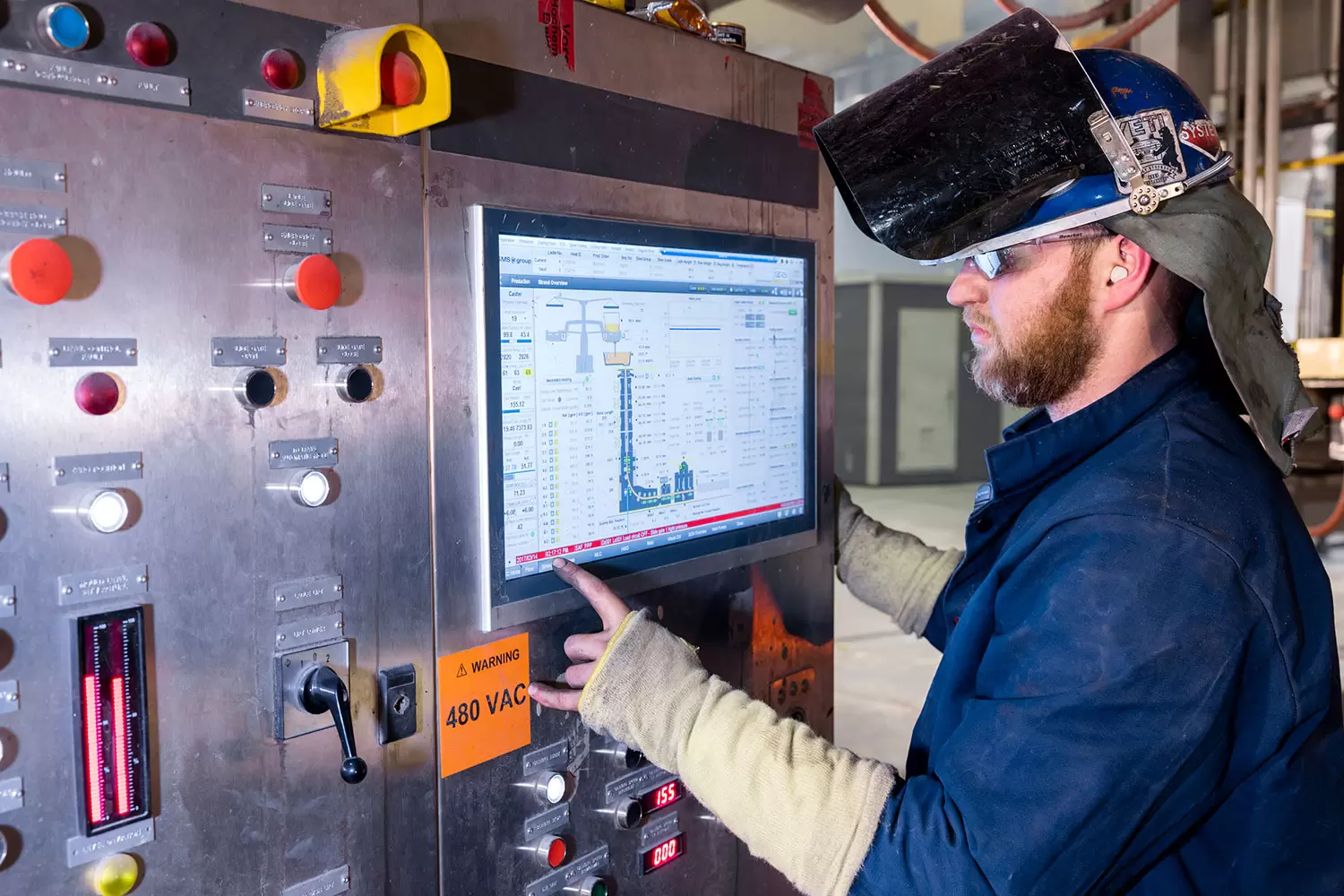
Use our contact form for questions, inquiries or personal contact.