Worldwide steel producers in 2021 worked to make their plants more competitive – from the steelmaking process right through to the final product. The demand and the potential for production growth is high, but to be able to make use of them, steel mills need to upgrade their equipment on a regular basis.
However, it is not only the competitiveness factor that speaks in favor of such modernization: The International Energy Agency (IEA) set a 28 percent emissions reduction target for the steel sector in 2050 (compared to 2011). At the same time, the production is projected to grow by more than 50 percent over the same period. Steel mills that want to thrive in such a challenging environment need technologies that will help them future-proof their business.
With the SMS offer of innovative and high-quality technology, tailored to customers' requirements and plants, and efficient concepts for minimum downtime and fast ramp-up, we have again successfully implemented modernization projects in the market in 2021. All over the world, customers appreciate our competence in this field and trust in our technologies, know-how and partnership.
Gerdau Ameristeel: Early adopter in need of new solutions
One of the manufacturers that relies on SMS group’s expertise is Gerdau Ameristeel Corp. in Petersburg, Virginia (USA). In 2019, Gerdau ordered new mill stands for its Petersburg heavy section plant and its medium section mill in Cartersville, Georgia.
Gerdau Petersburg invested in two additional continuous roughing mill stands with the proven and tested CCS® (Compact Cartridge Stands) stand design in order to improve their sheet pile production. The revamping work was carried out in several short shutdowns to minimize the impact on ongoing production – with a main shutdown lasting only two weeks. The Gerdau rolling mill in Petersburg is now successfully back in operation as scheduled.
Gerdau Cartersville was upgraded with the addition of three CS type stands in front of the continuous mill train. In addition, a new cold saw was added into the existing finishing end. The upgrade will allow the mill to increase productivity by optimizing the pass design and improving the section control. The heavy-duty CS compact stands are the ideal choice for demanding applications due to their superior rigidity and allowance for higher loads.
“Our goal is to further increase productivity and improve both performance and profile control", states Kevin Jilbert, Procurement Manager at Gerdau Ameristeel Corp. The new stands will also enable Gerdau to expand its product portfolio going forward. "This project is an important milestone in the long-standing and collaborative partnership with Gerdau", says Thomas Massmann, Executive Vice President Long Products at SMS group. Once the still ongoing project in Cartersville is finished as well, Gerdau will be able to fully leverage the synergy effects of its two plants.
Hyundai Steel: Strengthening competitiveness through upgrading
Another successful modernization project has recently taken place at Hyundai Steel’s Incheon plant in South Korea where a heavy beam mill has been put back into operation following an upgrade by SMS group. Together with the consortium partner Hyundai Rotem, a subsidiary of Hyundai Motor Group, SMS group equipped the rolling line for the production of larger beams with a web height of up to 1,100 millimeters and sheet piling with a system height of up to 800 millimeters. Thanks to this modernized beam mill, Hyundai Steel is able to meet the increased demand for sheet piling on the international market. During the course of the modernization, the rolling line downstream of the roughing stand was replaced by a new CCS® tandem group and an additional CCS® finishing stand.
With the new CCS® stands, Hyundai Steel benefits from reduced need for maintenance, shorter changing times, and higher rolling speeds with improved tolerances at the same time. Various new functions were also incorporated into the existing two-high roughing stand, which were put into service in the beginning of 2021. With a crude steel production output of 24 million tons per year, Hyundai Steel is one of the ten largest steel producers worldwide, mainly supplying the automotive, shipbuilding, and general construction industries. "The successful execution is mainly down to the excellent cooperation of all parties involved. Our success depended on us working together in close collaboration", says Tong-Il An, CEO, Hyundai Steel. "The high quality of the rolled products again confirms that our decision to choose SMS group for the beam mill upgrade was the right one."
Nucor-Yamato Steel Company (NYS): Ready to roll
Nucor-Yamato Steel Company (NYS), based in Blytheville, Arkansas (USA) represents another successful revamping project. Finalized in 2021, NYS has granted SMS group the Final Acceptance Certificate (FAC) for the successful modernization of the heavy beam mill No. 2, on which wide-flange beams and I-beams are produced. The goal of the modernization was to further strengthen NYS's leading market position in the structural steel sector by expanding the product range, increasing production, and processing new high-strength steel grades.
As a result, the upgrade mainly focused on replacing the existing conventional UR-E and UF stand arrangement with a compact three-stand tandem reversing CCS® mill 1500. The new stands are characterized by hydraulic adjustment under load and a fully automatic quick program change function, enabling higher rolling forces. With the CCS® mill stands, NYS can use both the existing as well as the new rolls and bearings with larger diameters, resulting in a significant reduction of roll costs.
Thanks to a detailed concept and comprehensive testing, the commissioning on-site could be finalized within a very short time: "With only 16 days, the main shutdown for the revamp, including the demolition of the old stands, was tightly scheduled, and it was strictly adhered to. The SMS group team was there to support us throughout the entire execution phase of the project," says Jim Shelton, Roll Mill Manager at Nucor-Yamato Steel. "We are confident that this revamp will give us a decisive advantage in the market.” At the same location, NYS also operates a medium section mill, which SMS group already modernized in 2014. The two rolling mills have an annual total capacity of 2.4 million tons of finished products. With the two mills now featuring cutting-edge technology, NYS is able to manufacture heavier products and expand its product portfolio.
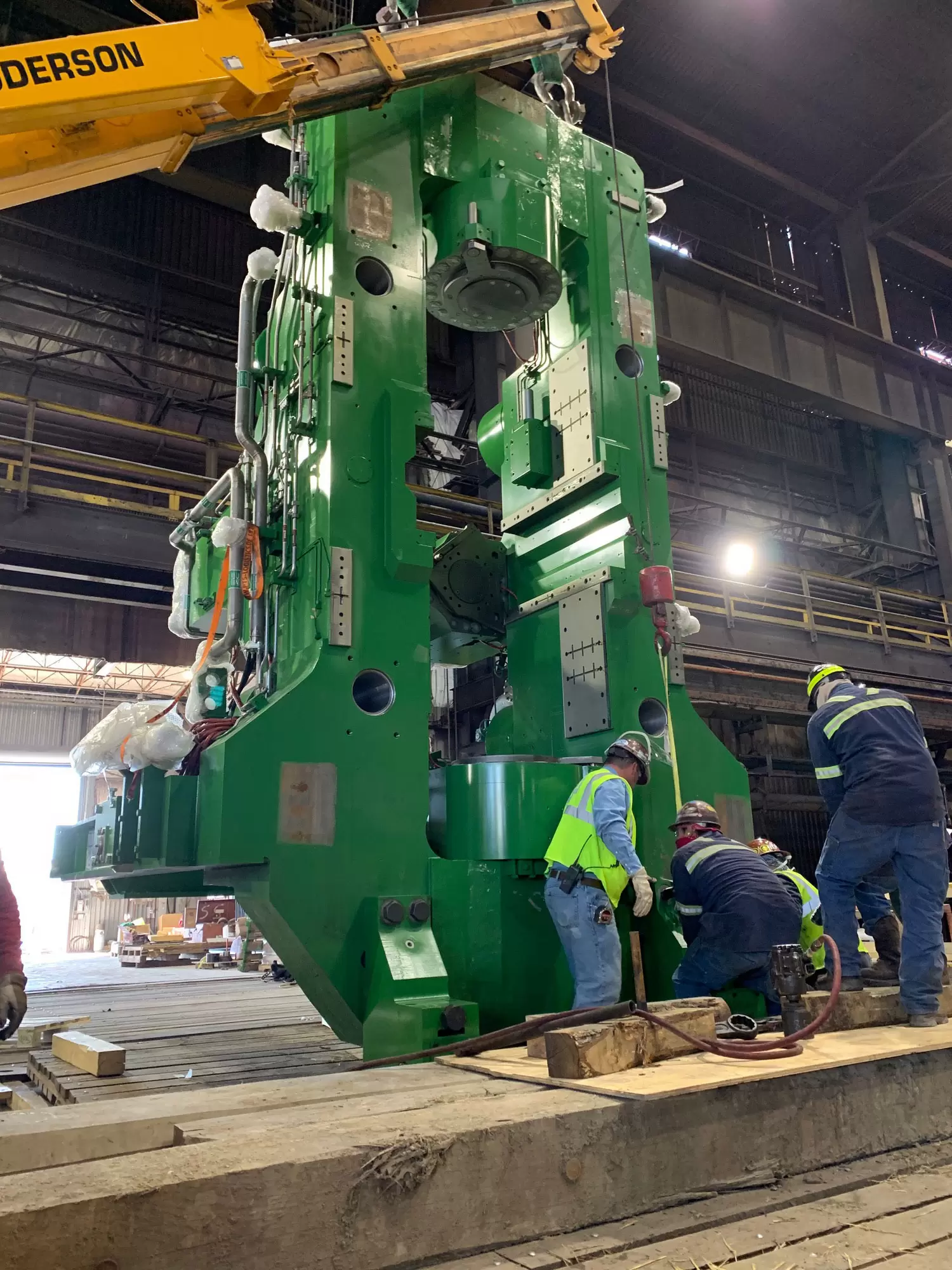
CELSA: More product variety thanks to upgrade
CELSA has successfully been cooperating with SMS group for many years. At its site in Castellbisbal in the province of Barcelona, the facilities include an EAF melt shop, a bar rolling mill, a wire rod mill and a medium-section mill. Annual production totals 2.4 million tons. Since 2000, CELSA Barcelona has been producing I and H beams on a medium-section mill supplied by SMS group. The mill was originally designed for an annual production of 500,000 tons. SMS group first expanded the initial range of products rollable on the mill during a revamp in 2007, and continuous plant optimization has raised the mill’s annual capacity to now 1 million tons. The upgrade covers the replacement of the existing cooling bed with one of higher capacity and the upgrade of the CRS® (Compact Roller Straightener), enabling it to process heavier products. The revamp also includes adjustments to and upgrades of the existing electrical and automation systems, all of which were also performed by SMS group. The revamp of the straightening machine took place during the 2020 summer break.
The new cooling bed comes with an aerosol cooling system that boosts cooling efficiency and, consequently, the mill’s productivity. Another special feature of the new cooling bed will be a turning device designed to turn I and H beams through 90 degrees into or out of an upright position, increasing the throughput rate. The modernization enables CELSA Barcelona to add HEA and HEB up to 600 to its portfolio and further enhance its production efficiency. Before the start of the revamp, SMS group conducted a comprehensive study to determine the investment, including the addition of a further strand to the continuous casting machine by SMS Concast in order to cast heavier beam blanks for future larger cross-sections. The new cooling bed is currently being installed during the winter shutdown of 2021.
In addition to these successful projects with long-standing partners, SMS group is currently planning further projects all around the world. “We have been providing cutting-edge technology for 150 years,” says Thomas Massmann, Executive Vice President Long Products at SMS group. “But even the best setup will eventually need an update. By building on existing facilities and infrastructure, we minimize production stops and help our clients to fully leverage their competitive advantage to be successful in a fierce market.”