Let’s start with the most important question: How much steel will the world need in 2050? Today, 8 billion people on Earth “consume” around 1.8 billion tons of steel annually. This translates into roughly 222 kg of steel per person each year. However, there are huge differences. The apparent steel use per capita ranges from 310 kg in Europe to around 30 kg in Africa.
The United Nations forecasts a global population of almost 10 billion in 2050. At today’s apparent steel use per capita, that will require an annual steel production of around 2.2 billion tons. However, many forecasts also anticipate a surge in steel demand per capita in populous regions such as India or Africa. This could drive steel production up to around 2.75 billion tons per year.
At the same time, the transformation of the energy grids to renewable energies will change the demand for steel. Presently, a mere 1% to 3% of steel is used for energy infrastructure. However, this figure is expected to rise significantly, exceeding 10%, especially for the construction of wind turbines or photovoltaic systems. The burgeoning electrification trend will also increase the demand for silicon steels.
So, how can we produce more steel and yet reduce CO2 emissions? One part of the equation is the existing plant infrastructure. Given their long investment cycles, plants and equipment will only be renewed step by step.
In 2022, 71% (1,347 million tons) of steel was produced using the traditional blast furnace and BOF (Basic Oxygen Furnace) route. This method produces an average of 1.9 tons direct CO2 emissions per ton of steel. Another 23% (or 412 million tons) of the total volume was produced via the scrap route with electric arc furnaces (and a CO2 intensity of 140 kg per ton of steel on average). The share of steel production via the direct reduced iron route was around 6% and emitted around 650 kg CO2 per ton of steel.
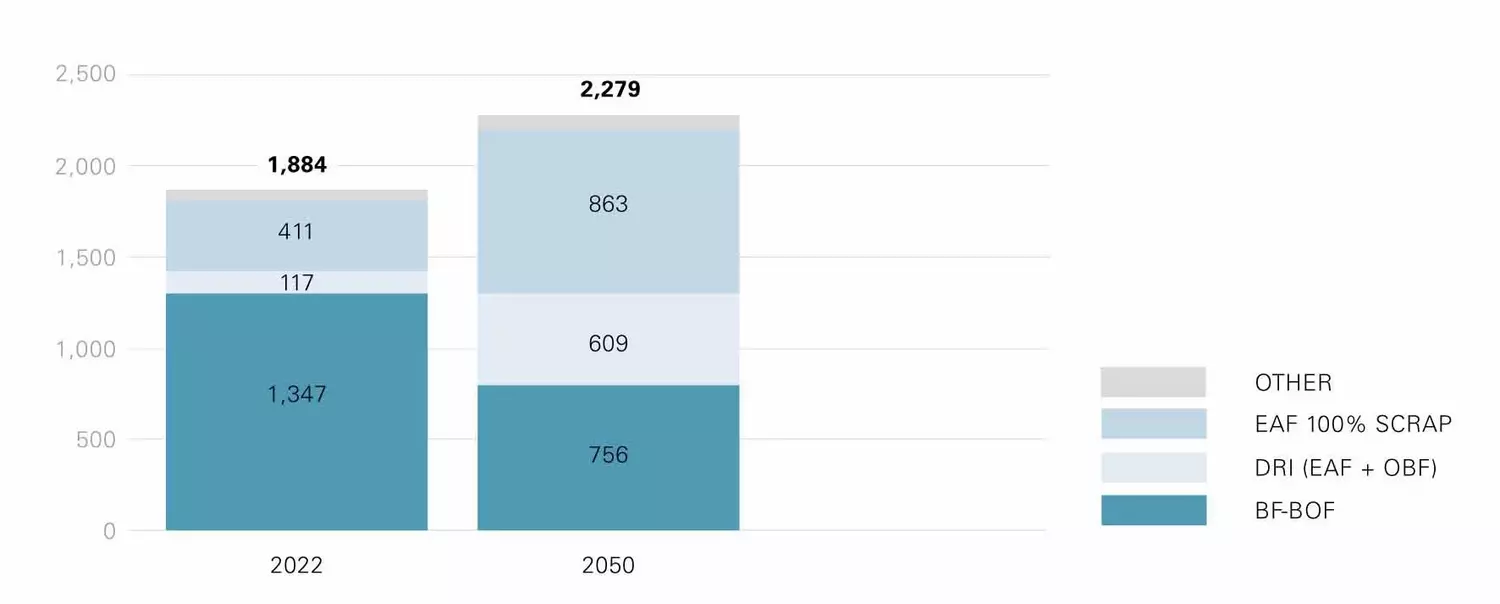
Scrap-based steelmaking: poised for significant growth
The electric steel route is the fastest way to produce near-zero emissions steel, as long as green electricity is used. But how much scrap will be available in the future? The World Steel Association expects end-of-life scrap to more than double from today’s 445 to around 900 million tons in 2050. Adding scrap from steel processing (prompt scrap) and internal scrap from steelmaking (home scrap), we can expect a total of up to 1.4 billion tons of scrap to be available each year.
However, not all of this will be available for the electric steel route. Much like today, a good third of this scrap will be used in primary steelmaking, i.e., the DRI-EAF route, and as cooling scrap in remaining BOF converters. Taking into account the typical yield losses of the EAF, we can project steel production quantities of between 850 and 900 million tons via direct scrap recycling. That would represent an increase from today’s 23% to more than 35% of total steel production. However, scrap availability on local markets will be impacted by trade restrictions. The rising concentration of tramp elements like copper, lead, and tin necessitates scrap processing of further dilution.
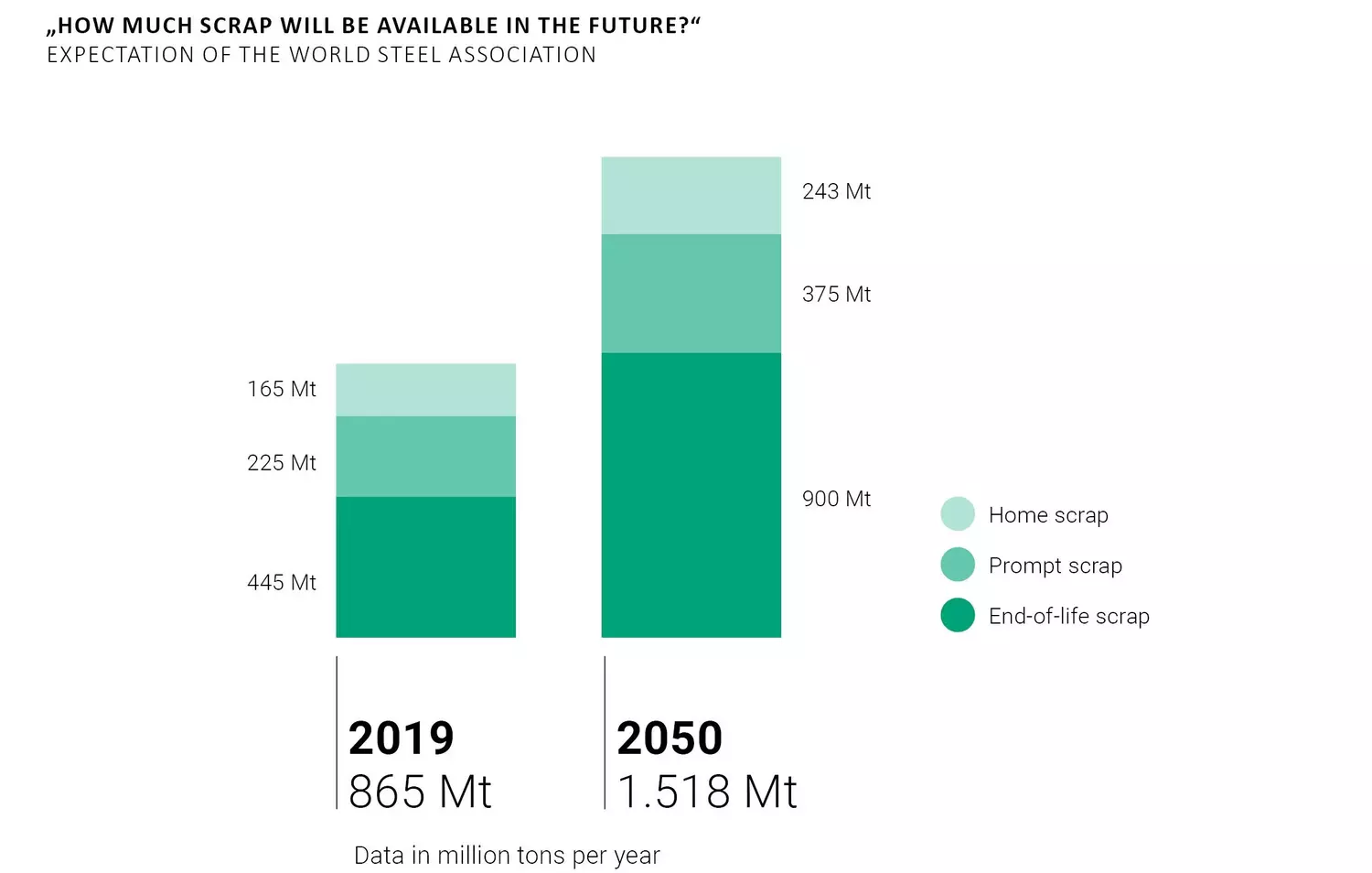
The availability of high-quality iron ore will be a limiting factor
While the EAF route may account for a third of the steel output by 2050, the remaining two-thirds will be based on virgin material. Even if scrap was abundantly available, for certain high-quality grades, there is no alternative to virgin material. That’s because the accumulation of tramp elements in scrap makes it impossible to produce all grades on the secondary route.
Most green steel projects today rely on direct reduction plants. H2 Green Steel is a pioneering example for many greenfield projects, relying entirely on green hydrogen and green electricity generated from hydropower and other renewable energies.
In a two-step process, direct reduction can also replace the traditional blast furnace in existing steelworks, as our flagship project at thyssenkrupp Steel Europe shows. Here, natural gas will be gradually replaced by hydrogen for reduction. The electric smelter (OBF, Open Bath Furnace) developed by us enables the production of hot metal, seamlessly integrating into the existing works infrastructure.
Several critical hurdles impede the exclusive adoption of direct reduction as the ultimate solution. The most important factor is that shaft-based direct reduction requires the use of high-quality (>67% Fe and <2% acidic gangue) iron ore pellets. Today, less than 40 million tons of this material is shipped to the global market.
To bolster the supply of these high-grade pellets, large sums have to be invested in the development of new, high-quality iron ore deposits, for example, in West or Central Africa. The beneficiation and enrichment of low-grade ores will also be increased despite the high cost and the resulting high quantities of tailings. In the upcoming decades, we’ll most probably also develop technologies tailored for the direct reduction of these lesser-grade ores. Yet, despite these developments, the availability of high-quality iron will remain a critical factor.
The battle for green hydrogen
The growth trajectory of the direct reduction route is not without its challenges. All scenarios anticipate that natural gas will be replaced by green hydrogen as a reducing agent for direct reduction, at least in the medium term. Steelmaking is the field in which the use of hydrogen is the most efficient because every ton of hydrogen saves around 28 tons of CO2. Nevertheless, the steel industry will face intense competition for the scarce resource hydrogen. Other sectors, including the chemical industry, also have their eyes set on hydrogen for decarbonization. Plus, its potential applications in transportation and heat generation may add to the demand.
Industrial-scale green hydrogen production through electrolysis calls for a significant ramp-up of wind and solar energy infrastructure. A complete conversion of the blast furnace capacity to green hydrogen-based direct reduction would require the additional production of around 4,600 terawatt hours of electrical energy – about 20% of today’s global electricity consumption. This figure alone illustrates the extent of the challenge ahead. In addition, geographical constraints make ubiquitous green hydrogen availability implausible, making ammonia a more feasible hydrogen carrier.
Given these complexities, forecasts expect direct reduction capacity to grow from today’s 117 million tons to almost 500 million tons by 2050. For that to happen, another bottleneck must be resolved: plant engineering. In recent years, an average of two new full-scale direct reduction plants have been built globally each year. To achieve an annual capacity boost of approximately 15 million tons, the construction of six to eight DRI plants per year would be required. Recognizing this, we are investing heavily in our engineering and order execution capabilities.
A plea for openness
To sum it up: Depending on the development of per capita steel use, experts assume a global annual crude steel production of between 2.32 and 2.75 billion tons. Under the lower scenario, around 20% (approx. 500 million tons) will come from direct reduction, while the electric steelmaking route will account for 35% to 40% (approx. 900 million tons). In addition, we’ll see the emergence of new processes, such as iron ore electrolysis, which are currently under development. Even under optimistic assumptions, no capacity of more than 50 to 100 million tons can be expected over these new routes by 2050.
Different regions and nations will pursue different paths towards decarbonization. Direct reduction technology will see the most significant growth in countries with access to high-quality iron ores and low-cost energy sources such as solar and hydroelectric power. The electric arc furnace route, on the other hand, is poised for substantial expansion in countries with rising scrap availability. In China, an influx of scrap resources is anticipated by the 2040s, as infrastructure established in the late 20th and early 21st century gets renewed.
However, all forecasts also show that the blast furnace route will continue to play a major role for the next three decades. Come 2050, almost 40% (approx. 850 million tons) of world crude steel will be produced using the conventional route. That it why the conversion of blast furnaces into low CO2 emission operation is the key challenge to decarbonize the steel industry.
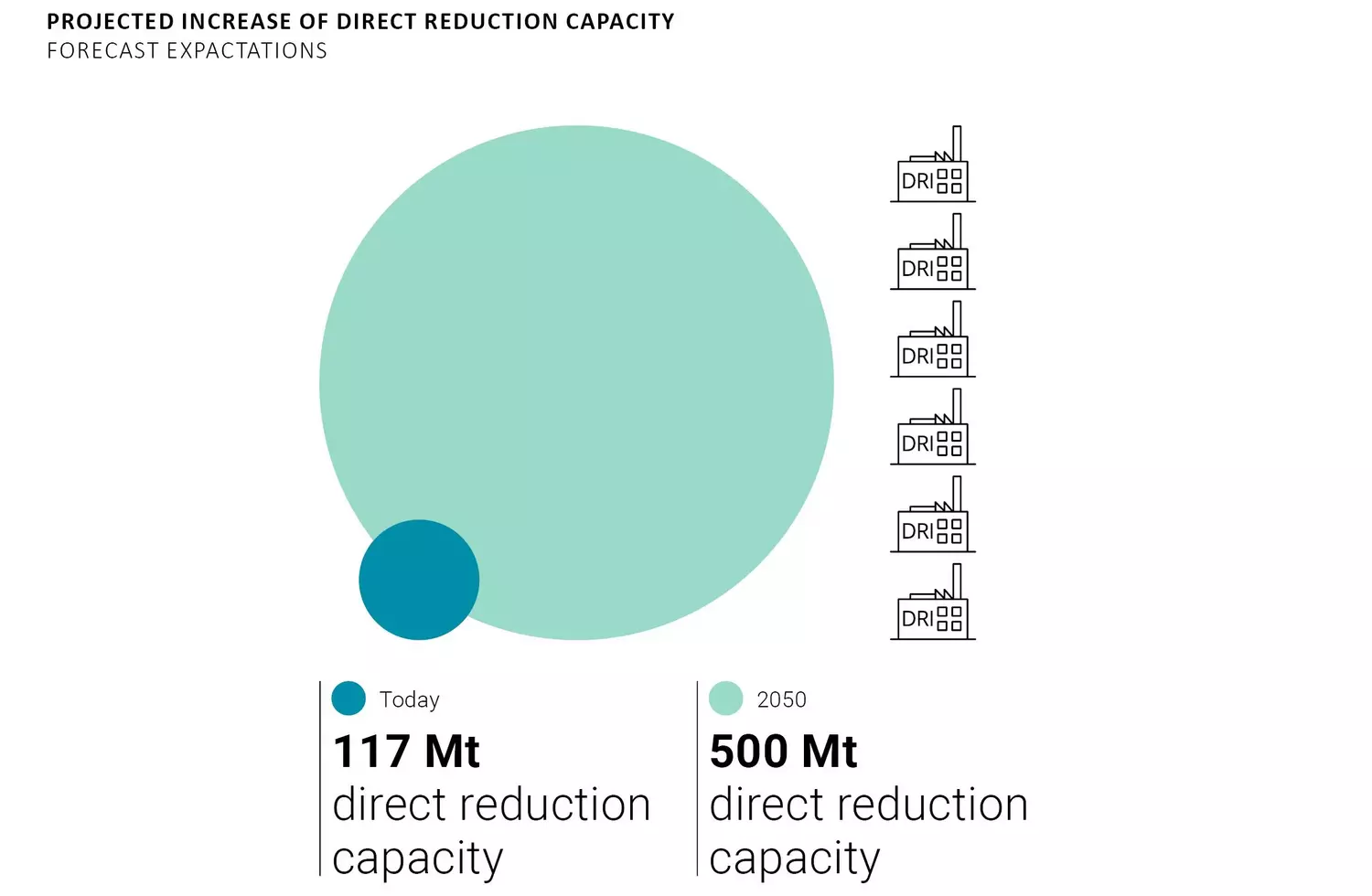
Decarbonizing the blast furnace
Two solutions that build on each other are available for this purpose: the Blue Blast Furnace and the EASyMelt. The Blue Blast Furnace would always be the ideal first step. Its advantage is its low investment costs and, therefore, its potential to swiftly slash CO2 emissions by around 15%. The defining feature of the Blue Blast Furnace is the generation of syngas and its injection through a new bustle pipe at the lower shaft area of the blast furnace. Comprised mainly of carbon monoxide and hydrogen, syngas acts as a reducing gas, substituting coke to facilitate the reduction of the iron burden in the shaft.
This gas can be produced via a variety of technologies. One is a new reforming process, the so-called dry reforming of coke oven and blast furnace gases in reformer stoves. During this process, methane, carbon dioxide, and water steam are reformed at a high temperature. Since the process mostly uses exhaust gases from the steel plant and can replace coal, it is called a circular carbon approach.
Based on, but going beyond, the emission reduction potential of the Blue Blast Furnace, SMS group is developing the Paul Wurth EASyMelt. This electrically assisted syngas smelter is an alternative to the direct reduction route and a complementary building block for filling the gap between iron ore availability and green steel demand. Building on the Blue Blast Furnace technology, EASyMelt can be realized in a step-wise approach of implementing several technological elements that work together towards near-zero emission ironmaking.
The process is flexible in its inputs, boosts resilience against supply shortages and market volatility, and can be adapted to various scenarios. Most importantly, however, traditional sinter feed may still be used in EASyMelt, avoiding fierce competition for the limited supply of (high-grade) pellets. This versatility, in conjunction with its energy flexibility, translates into highly competitive operational costs.
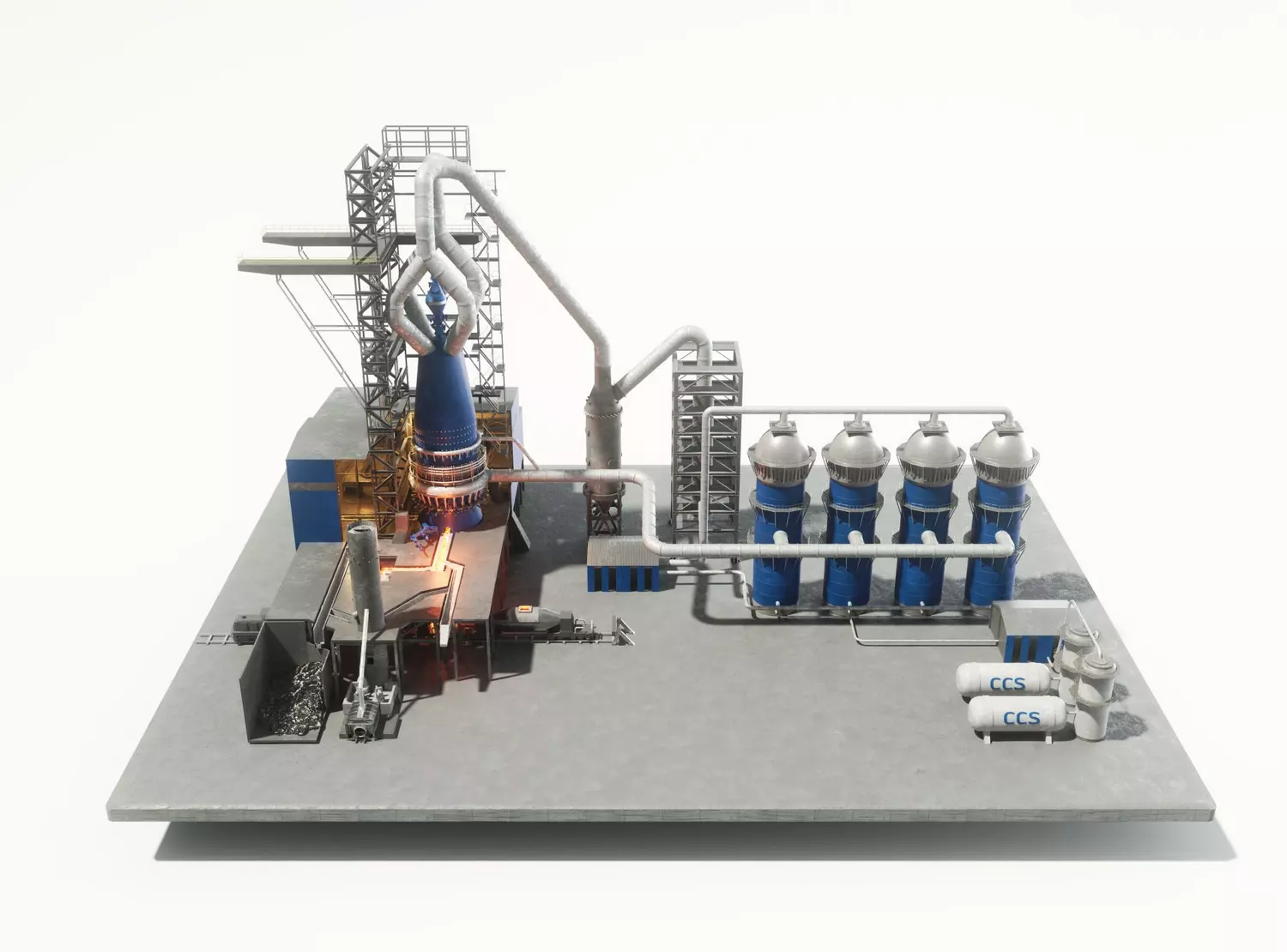