The project
The CSP® plant of EZDK started production in 1999 and, before the upgrade, had an annual capacity of one million tons of flat steel. To ensure reliable availability of the plant, the Egyptian steel producer decided to completely replace the obsolete automation and drive systems. As the leading provider of technological systems for this modernization project, SMS group was also able to increase the share of ultra-thin hot strip, enhance the product range by new steel grades and simultaneously improve product quality.
Thanks to an efficient cooperation, the upgrade could be implemented within a shutdown of merely 20 days. Since then, EZDK’s production has been achieving record results.
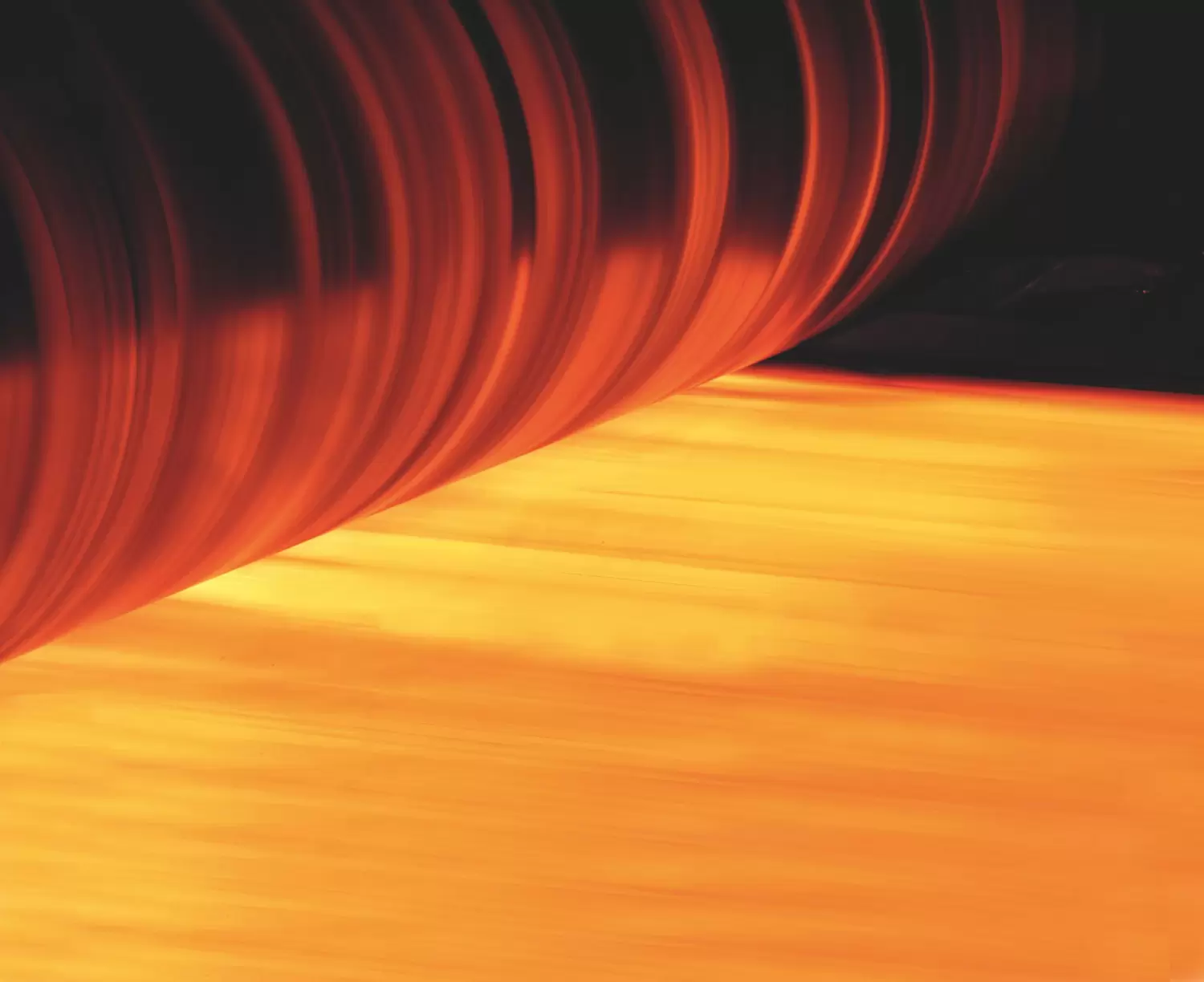
CSP® caster
The CSP® caster was designed to cast thin slabs up to maximum 70 millimeters thick, with their thickness being flexibly adjustable between 48 and 70 millimeters by means of LCR (Liquid Core Reduction). In the course of the modernization, SMS group also installed the mold monitoring system MMSplus supplying reliable information on the in-mold process sequence. The integrated system for early detection of breakouts reduces expensive production downtimes and repair costs to a minimum. The technological process model DSC® (Dynamic Solidification Control) is in use, too. Through optimized cooling strategies over the whole casting process, the DSC® stands for sustainable improvement in product quality and maximum furnace entry temperature of the thin slabs.
CSP® rolling mill
In the CSP® rolling mill, the upgrade included the optimization of gear units and the installation of new process models and control systems for thin-strip rolling. In addition, the MPM (Material Property Model) developed by SMS group supports quality assurance in terms of mechanical properties and reduces the need of taking samples.
Choosing SMS group as partner for the upgrade of our plant was the right decision. We are very satisfied with the production results achieved after only one year. Hence, the entire modernization project here at EZDK must be regarded a total success.
The MPM furthermore simplifies the development of new and the advancement of existing steel grades. As a full-range supplier, SMS group additionally renewed all auxiliary drives and the direct converters of the mill stand drives in the CSP® rolling mill.
Quality & productivity
To shorten the commissioning period, the automation system was tested by near-reality simulation, and the operating staff was trained at the virtual plant. Now, that the modernization has been completed, EZDK’s CSP® rolling mill can reliably produce strips of 1.0 millimeter thickness.
EZDK is part of ezzsteel, Egypt’s largest steel producer. The modernization of the CSP® plant helps EZDK raise its share of ultra-thin strip, expand its product range and improve product quality.
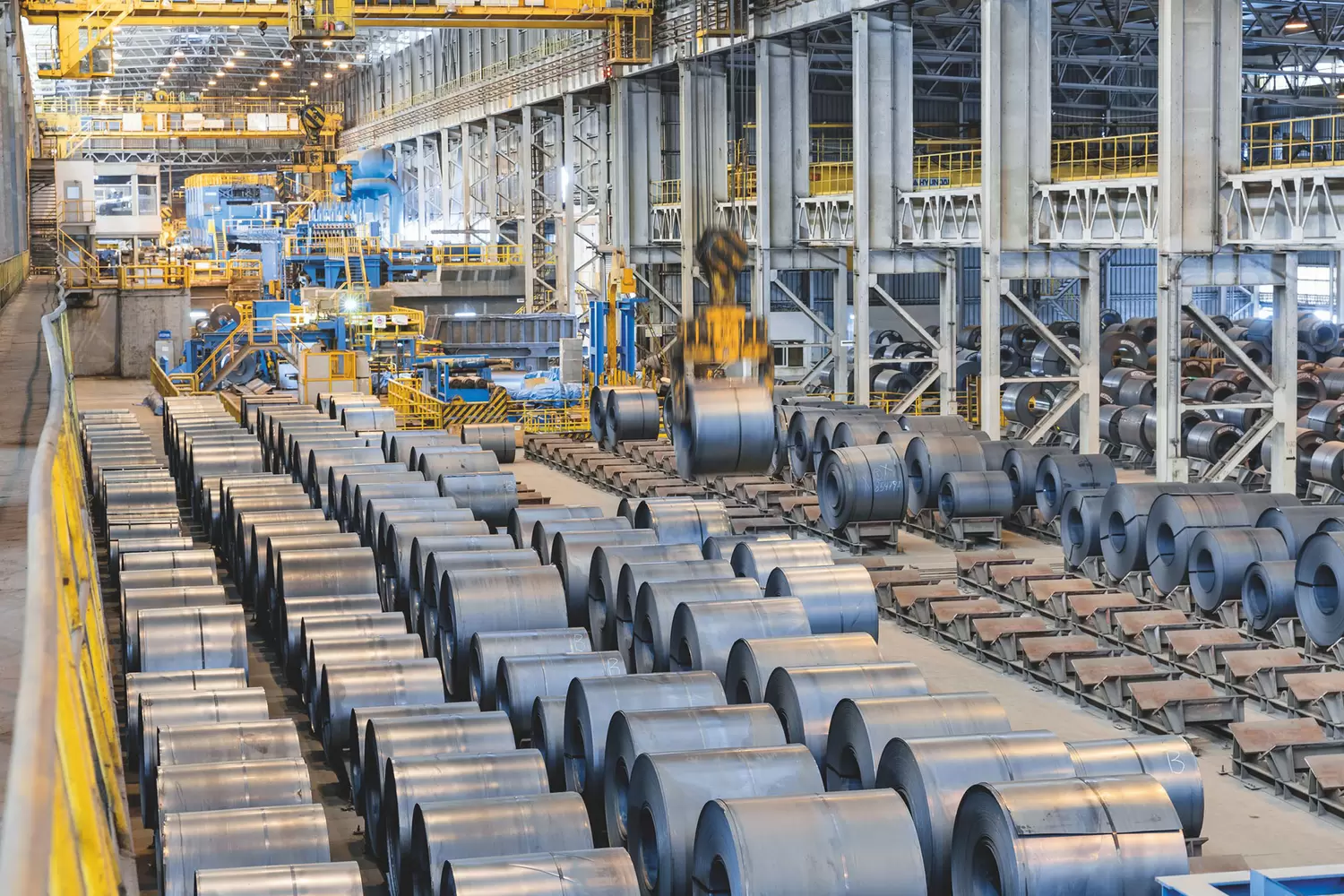
Super-reinforced cooling groups
In the laminar cooling section, SMS group replaced the first three units by super-reinforced cooling groups. The higher cooling rates generate a finer microstructure, which makes the hot strip stronger and tougher respectively allows the volume of expensive alloying elements to be reduced while leaving the chemical composition unchanged. Throughout the whole cooling section, SMS group installed the newly developed asymmetric edge masking system that permits the edge masks of all groups to be set individually and independently for drive side and operating side.
This enables the masking system to respond to strip center deviations, too. Edge masking serves to prevent excessive strip edge cooling and hence improves strip flatness. SMS group furthermore installed a surface inspection system featuring the latest optical techniques suited to assess and document the surface quality after the rolling process.
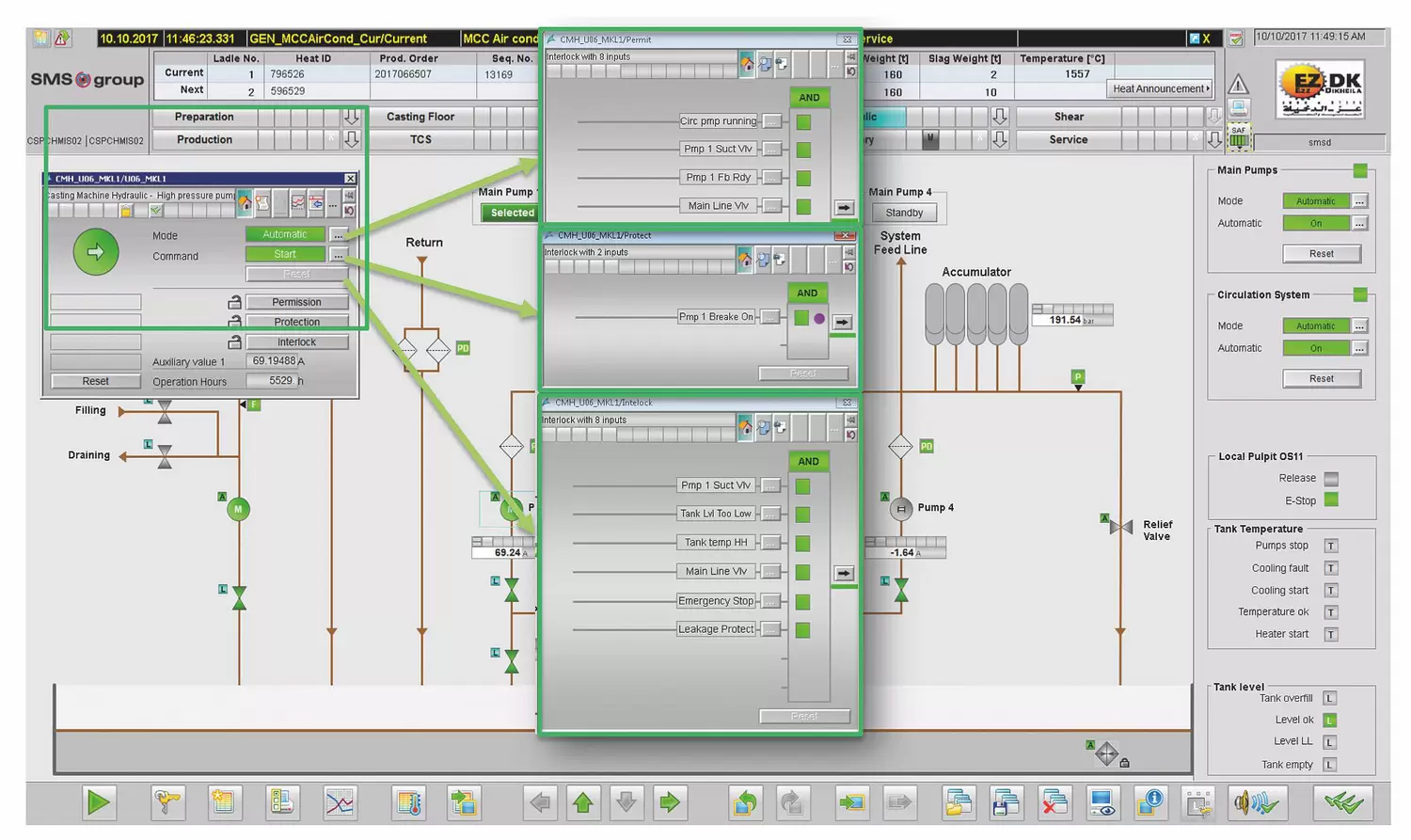