- X-Pact® High Current switched-mode power supply units enable customized, module-based DC power supply for electrolytic processes in the steel industry
- The compact design makes the system perfectly suitable for new tinning lines and upgrades
- The solution saves more than 40 percent of energy and reduces the costs of installation, commissioning and maintenance
During the many years that electrolytic treatment plants such as tinning lines are in operation, market environments can change dramatically. Emission regulations may become stricter, and the costs of energy and raw materials may rise. Suppliers and operators of strip processing plants worldwide are faced with the challenge of reducing energy consumption and operating costs.
Most effective levers to achieve this are the reduction of CO2 emissions, higher availability of their plants and processes, and innovative developments that enhance strip processing performance. Switched-mode power supplies (SMPS) are today the standard in most direct-current applications (such as charging devices, power supply units for computers, LED drivers, etc). Since SMPS for high currents (of about 80,000 amperes) reached commercial maturity a few years ago, SMS group has successfully used them in its strip processing lines.
Benefits of switched-mode power supply units
Alongside the system-inherent advantages of a switched-mode power supply unit, such as modularity, space-saving design and high availability, X-Pact® High Current achieves dramatic energy and CO2 savings, thanks to which it is included in the portfolio of Ecoplants modules, SMS group’s holistic sustainability concept.
In everyday production, power rectifiers are often operated at partial load as they are designed for maximum requirements. The advantages of the SMS group’s switched-mode power supply units over conventional thyristor units in terms of energy savings become particularly evident during partial load operation. A replacement of older thyristor-based DC power supplies may achieve energy savings (costs and CO2 footprint) of more than 40 percent.
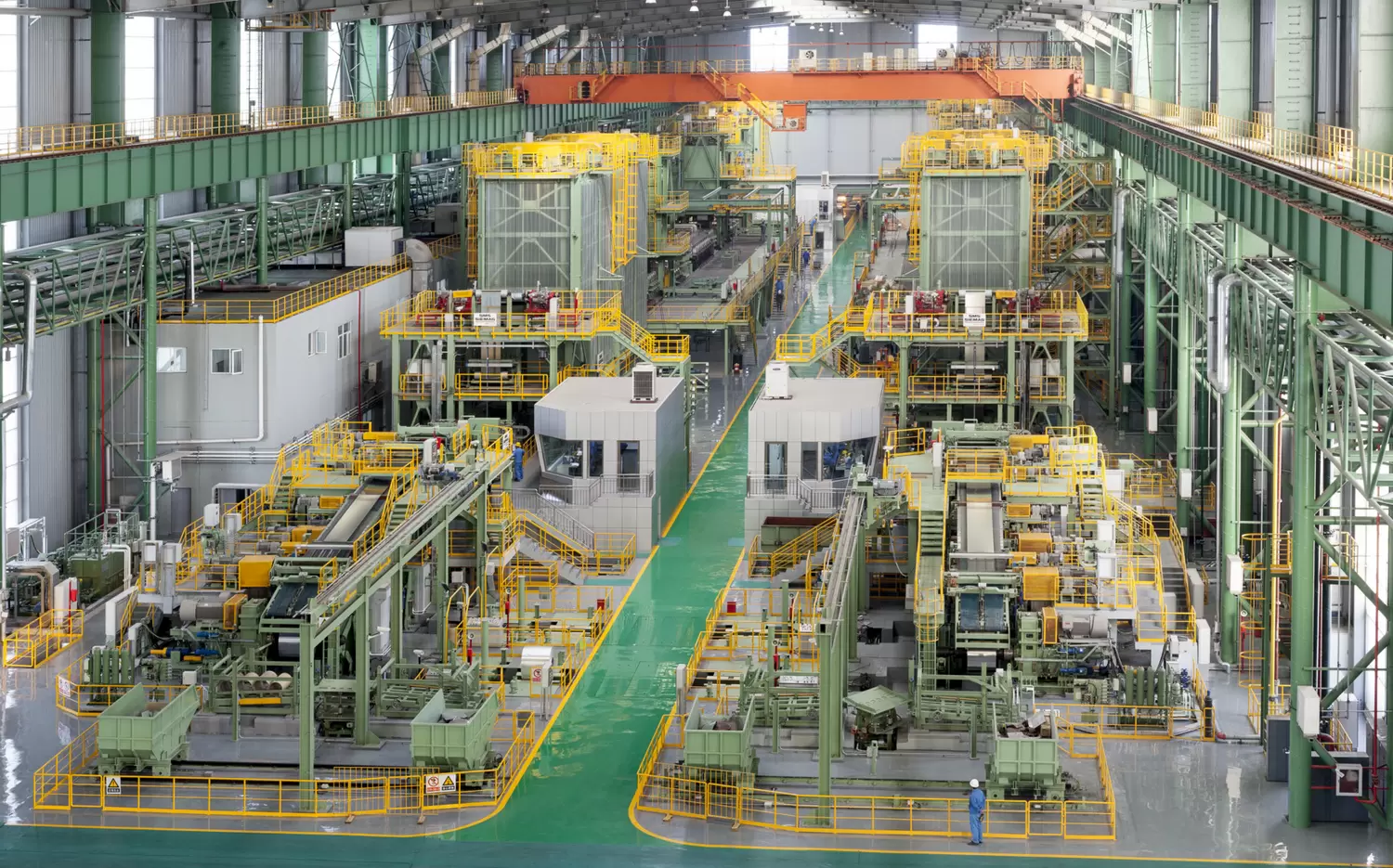
What is more, thanks to the modular design of the SMS group switched-mode power supply units, plant availability will be significantly improved. Should individual power modules fail, other modules can immediately take over the DC power supply of the process, avoiding any interruption of the production process.
A defective module can be exchanged during a line stoppage in a matter of minutes by just one person. Another benefit is that the costs of keeping spare parts in stock are significantly reduced, thanks to the very small number of different modules used.
Should it turn out during operation that the installed DC power supply capacity is not sufficient, further modules can be easily added to the installed units. Alongside the “regular” control options, such as high-performance current and voltage control (low residual ripple, high control accuracy, etc.), pulse mode or reverse pulse mode operation are possible alternatives.
SMS group’s comprehensive know-how and longstanding experience both in plant engineering for electrolytic strip processing and in power supply technology makes this integrated, high-performance solution for processing lines of this type so unique.