The world’s first carbon-neutral steel plant
Carbon-neutral green steel, made with renewable hydrogen. A futuristic dream, set in a distant future? No – this is reality: a totally new, green steel facility to be built in northern Sweden making use of SMS group expertise and equipment. This hydrogen-based direct reduction plant will be fully integrated, transforming virgin raw materials into finished steel. Works will start in 2022 and the site is expected to be operational by 2025.
A landmark project for decarbonization
The Stegra project is an exciting step in the transition of the European steel sector towards carbon neutrality. Based near Boden, in northern Sweden, Stegra will be the world’s first renewable hydrogen-based integrated steel mill.
Stegra opens up the prospect of zero CO2 steel – a true revolution in a sector that currently emits two tons of the greenhouse gas or more per ton of steel produced. SMS group is proud to be a partner in the project.
SMS group will, together with Paul Wurth and its consortium partner Midrex, provide a MIDREX® direct reduction plant, the EAF based melt shop, a CSP® Nexus plant as well as an advanced cold rolling and processing complex for the production of a broad product mix including Advanced High Strength Steel and automotive steel grades.
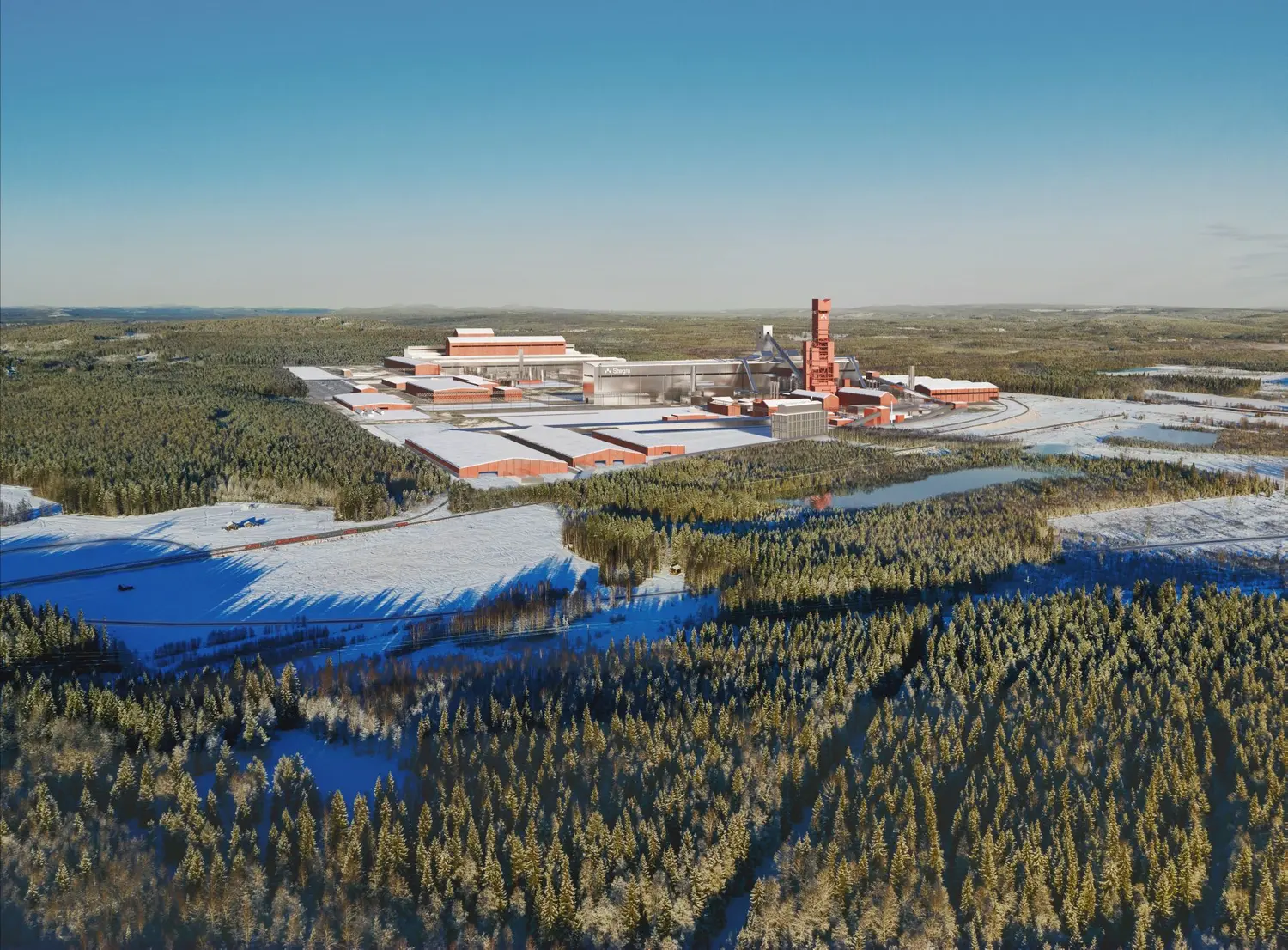
We are very proud to supply the technology for the world's first large scale all-green steel plant. Hydrogen based green steel is the future of primary steelmaking, and we are all working at full speed to deliver the key technologies to start a new era of steelmaking.
Stegra: A project of superlatives
- The world’s first industrial-scale steel plant based on hydrogen and electricity from renewable sources
- Built in arctic conditions only a few kilometers south of the polar circle
- Size of site: 300 hectare
- Capacity of phase 1: 2.5 million t/year
- Start-up of first plant: 2025
- Order for SMS group: more than 1 billion euros
How does Stegra work?
Almost all technologies used along the entire process completely dispense with the use of natural gas or other fossil fuels. They will be replaced by hydrogen or electricity from renewable sources. As a result, Stegra will reduce CO2 emissions by up to 95 percent compared to traditional steelmaking.
The process equipment is not only designed for minimum CO2 emissions, but also to produce advanced automotive steel grades. Leading European car manufacturers signed agreements with Stegra about the supply of “green”, high-quality steel strip already.
1. All electricity requirements of Stegra will be covered by renewables
2. Giga-scale electrolyzers with a capacity of 800 MW produce green hydrogen
3. DRI made of 100 % hydrogen and high-grade iron ore
4. Energy recovery plants produce steam for electrolyzers and downstream processes
5. Steelmaking based on DRI, scrap, and green electricity
6. CSP® Nexus: Electrical and induction heating replace natural gas to produce carbon-neutral hot strip
7. Cold rolling and processing: Electrification of annealing and galvanizing furnaces to achieve a green final product
8. Result: High-quality flat steel with a 95 % smaller carbon footprint.
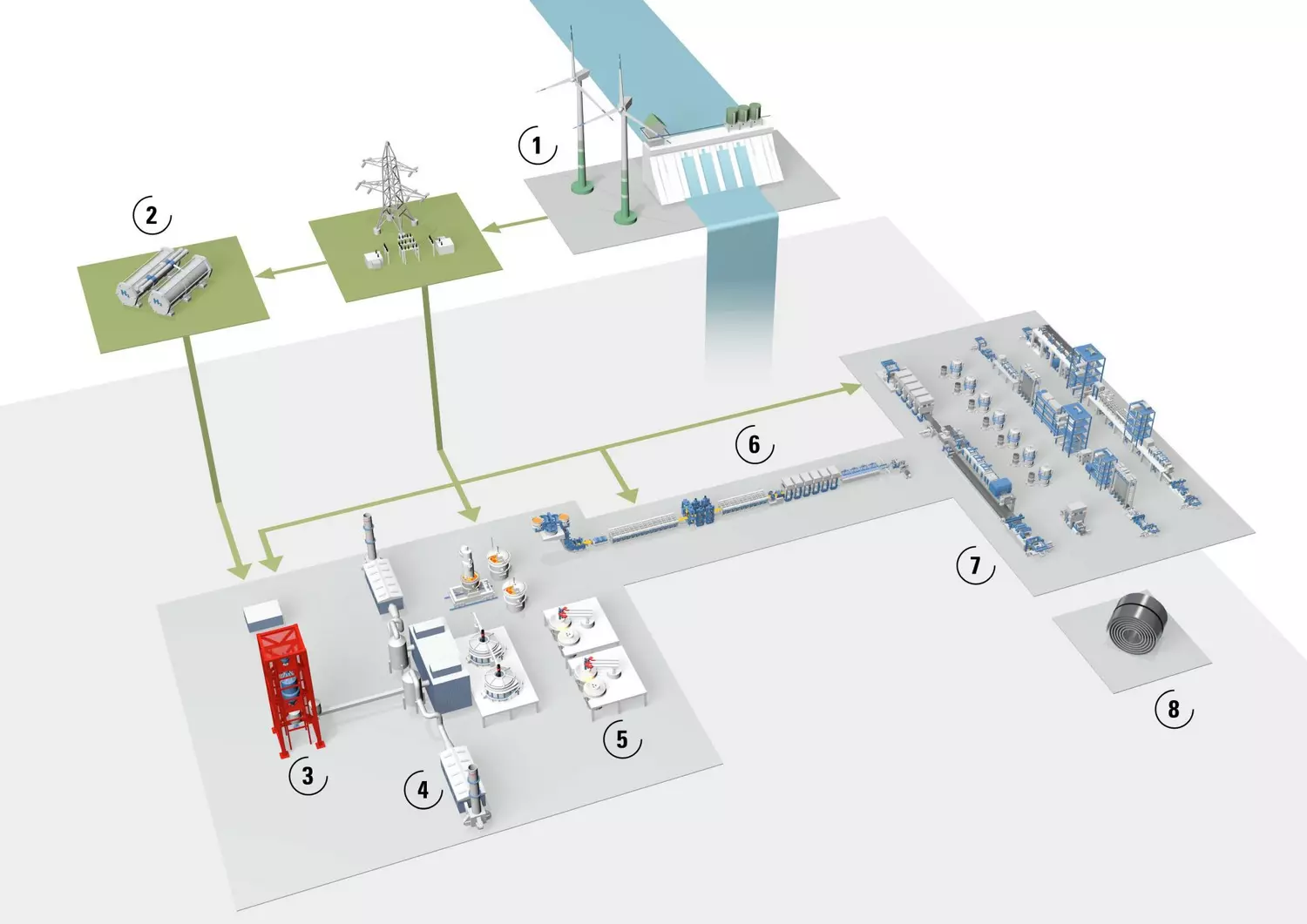
Our aim at Stegra is nothing less than to pioneer an industrial revolution in the steel industry. We have chosen SMS group for this project because we believe in their capabilities, which have been demonstrated in numerous industrial projects around the world.