Expert Chock Maintenance and Repair
Using our skill, experience, technology and a disciplined process, SMS group Inc. skillfully repairs chocks used in metals production. As part of our repair process, we thoroughly clean and inspect incoming chocks and document inspection findings. Chocks are then carefully disassembled to ensure components aren’t damaged and parts are thoroughly cleaned. Using the latest in inspection technology, our skilled workforce inspect critical dimensions, develop a plan to repair the chock in the best, most costeffective way possible, and prepare a detailed report of the damage and recommended repairs for customer review and approval.
Our thorough repair process includes: premachining surfaces to ensure quality welds; expert welding; BoreGuard™ Arc Wire Spray Welding; stress relieving; and precise finish machining to ensure proper contact surfaces. To ensure top performance, bore diameters are verified and the width of shim liners is set. Final steps in the refurbishment process are inspection; deburring and sanding; cleaning and painting; careful reassembly, including bearing load zone rotation, and packing for shipping to ensure chocks arrive in perfect condition. Our rigorous repair process pays off. Chocks we have refurbished are returned in as-new or betterthan-new condition, regularly providing longer service runs with less downtime. Our innovative processes and manufacturing techniques reduce long-term maintenance costs. Our technical modifications improve reliability and performance.
New chocks have long service lives and reduced downtime
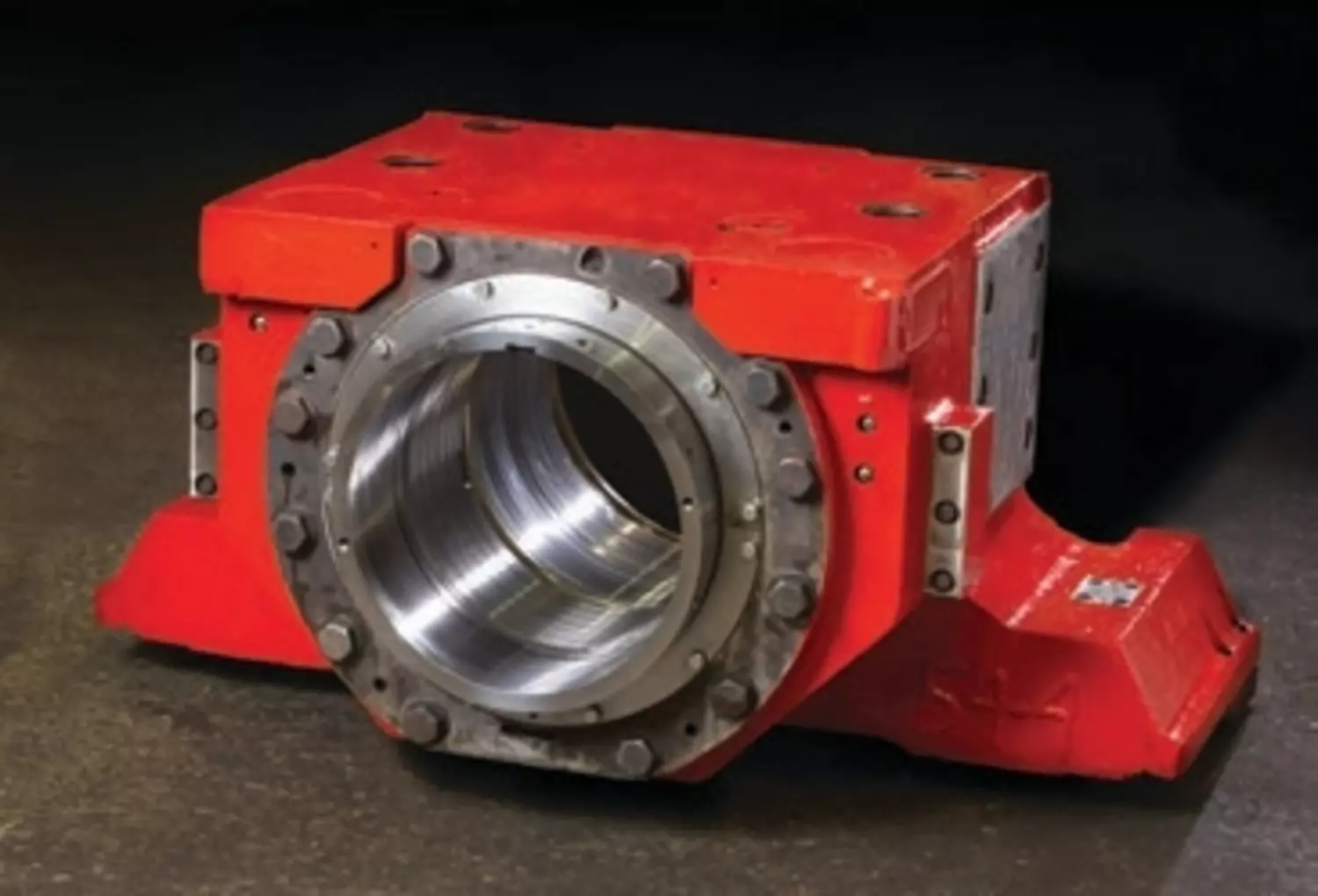
To ensure chocks reliability in the field, they are precisely machined
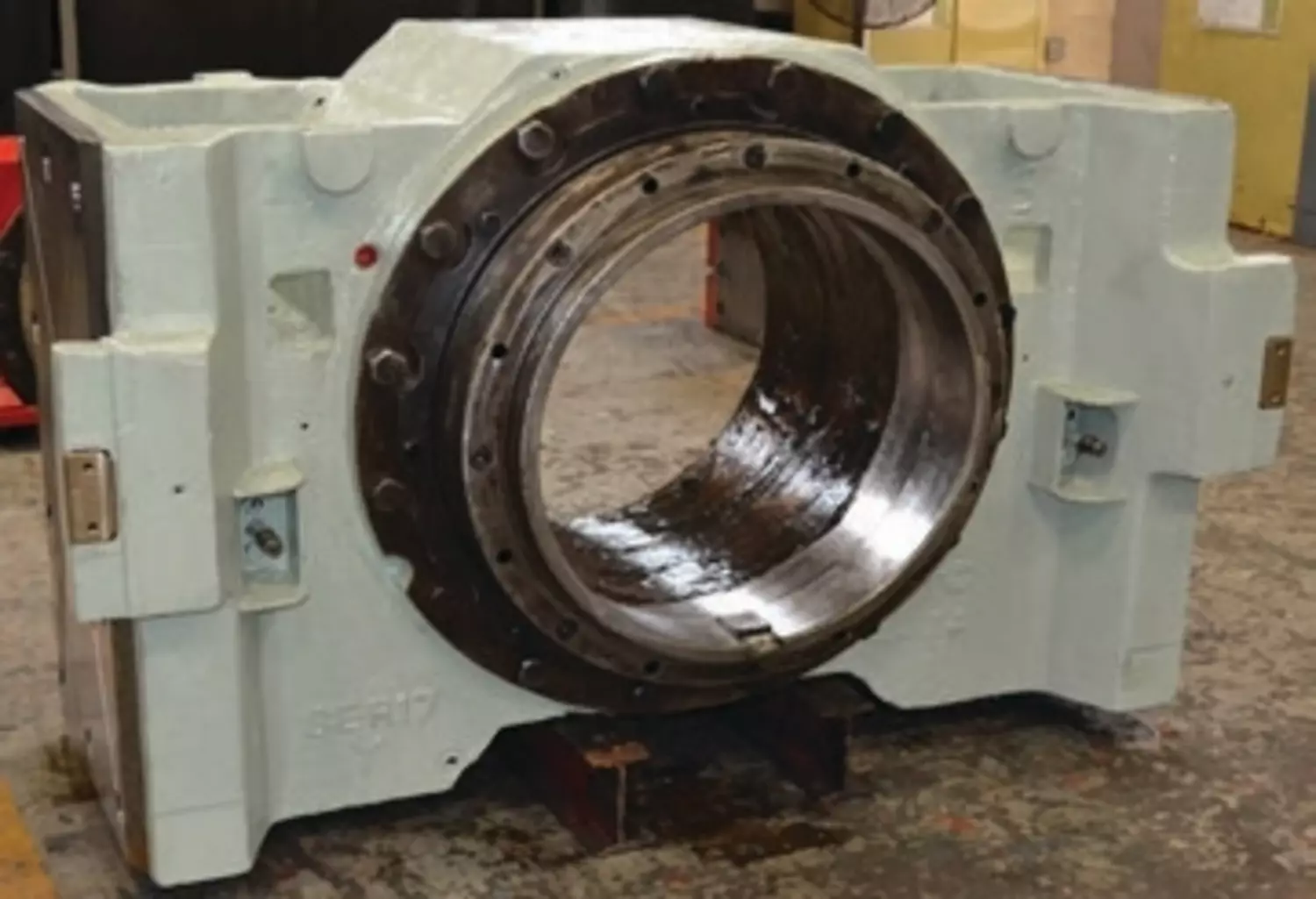
Chock Fleet Management
SMS group Inc. offers turnkey chock fleet management solutions. These solutions take the burden of operating a maintenance program off of the metal producer. To start, we evaluate the total cost of the producer’s rolling mill operation. SMS group Inc. then further investigates the oil film bearing operations losses and water content, annual bearing consumption, delay rates caused by chock malfunction, and product quality defects. We can then determine if a significant cost reduction can be made from repairing chocks, mill stand components, and sealing modernizations. We assess the condition of the chock fleet by performing inspection on it and once the chock fleet condition has been sampled, a maintenance plan is implemented. With many cost saving repair methods, SMS group Inc. is able to develop a plan that will fit into the mill’s budget and create a ROI that can be calculated from this plan.
Chock Tracking
SMS group Inc. offers chock tracking services to maintain an accurate time line of when chocks need to be pulled from service for preventive maintenance. With this service, we can also categorize and track repairs/modernization performed, inspection history reports, track costs, and frequencies of maintenance to determine if the financial goal of reduction of operational costs has been achieved.
Inventory Management
In order to keep pace with the demands of rolling mills, SMS group Inc. offers spare part inventory management of all components needed to repair a chock in the shortest amount of time. This service also allows mills to manage their monthly budgets as spare parts and/or chock repairs are only paid for when needed. SMS group Inc. truly offers “just-in-time” delivery.
To learn more about how SMS group can keep your chocks performing reliably at peak efficiency, call us at +1-412-231- 1200.