A fine, gray powder with an unspectacular look, but with properties on which a completely new growth sector is going to evolve. This extremely homogeneous metal powder is the basis of additive manufacturing – the process of 3D printing of metal. It is made up of perfectly round minute spheres measuring only 15 to 45 micrometers (one thousandth of a millimeter). It is hard to imagine how these microscopic particles are produced in a 13 meters tall and highly complex plant involving an extremely sophisticated technique. SMS group has recently commissioned a pilot plant for the industrial-scale production of this type of powder.
A milestone for the future
The successful commissioning of the powder atomization plant marks a milestone for SMS group because only a high-quality powder can make a high-quality 3D printed component. The objective is to master – and allow the customers to master – the complete process chain of this innovative technology. This is why SMS deliberately chose to not build a small-scale but an industrial-scale pilot plant. Only this way the process can be tested under real conditions, i.e. at high temperatures and pressures and in long production cycles. SMS works with the cooperation partner Additive Industries, developer and provider of selective laser melting systems for 3D metal powder printing. The plan is to set up a demonstration plant for customers at the SMS group facilities in Mönchengladbach. That plant will comprise all process steps of additive manufacturing.
A sophisticated process based on SMS group know-how
The function of the new pilot plant built by SMS group is to atomize powder. Its main components are a vacuum induction furnace with a crucible and a tundish, atomization equipment arranged in the powder tower, vacuum pumps, cyclones, gas coolers, bag filters, air separators and screens for powder grading.
The plant melts the metals and the alloys inductively and under vacuum. The vacuum technology is key to achieving an ultra-clean product and reliably preventing the material from reacting with oxygen. If this is not guaranteed, oxides, oxide inclusions and other contaminations may result. Ultra-clean powder can only be produced under inert conditions. Especially in this area, SMS Mevac’s expertise and know-how in secondary metallurgy technology has contributed largely to the success of the process.
In the next step, the liquid metal is atomized in a jet nozzle of just a few millimeters by means of pure argon. This process produces spherical particles in the micrometer range. The particles cool down to microscopic spheres forming the metal powder. The fine metal powder undergoes further treatment and will be graded by grain sizes, resulting in fractions of high-purity product of perfect spherical shape, with defined grain sizes between 15 and 45 micrometers, an exact chemical analysis and free from inclusions and satellites (agglomerated material).
Our powder is of unparalleled quality because we have the know-how and expertise to master the complete production process.
Special materials for new performance properties
The new powder atomization plant makes metal powder from superalloys, Ni-based alloys, CoCr alloys, special steels, maraging steels and copper allows. Markus Hüllen: “The plant allows us to develop new alloys with new properties together with our customers and – this is unique - under real production conditions. At the same time we are establishing the basis for Industrie 4.0 in powder production as we are going to implement an automated, seamless quality control system covering the complete process chain of additive manufacturing. This type of consistent documentation and 100 percent traceability are an absolute must, for example, for components produced for the aerospace industry.“
Additively manufactured components are already used in a number of industries. These “enabler” industries include the aerospace industry, the automotive industry, medical engineering, prototype and tool making, and plant and mechanical engineering. Also SMS group uses additive manufacturing in the development of new or optimized components for its plants. A very impressive example are the spray heads used in drop forging plants for cooling and lubricating the dies. Compared to the previously used spray heads, the new ones made by additive manufacturing are much lighter, flow-optimized and individualized to perfectly meet the specific requirements of die at hand. The advantages: Forging press operators can increase the productivity of their operations and improve the quality of their products as a result of the dies being cooled faster and more efficiently.
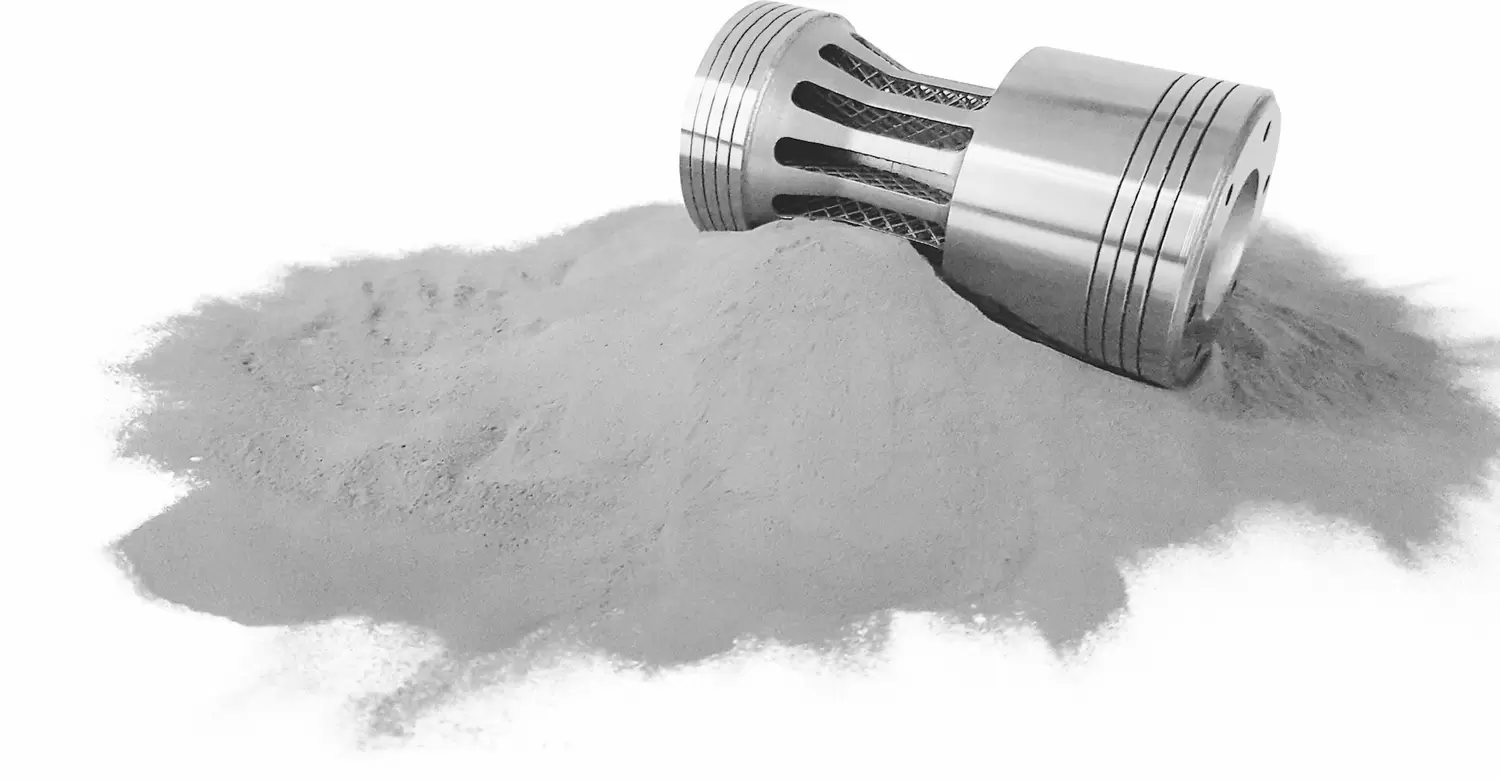
Additive manufacturing in series production
With the name Scale4Series, SMS group describes a holistic production concept for 3D printed components. SMS group has partnered with Additive Industries, manufacturers of 3D printers, to offer a turnkey concept that comprises the complete process chain from metal powder production and 3D printing all the way down to the finishing of the printed components. Besides these, additive manufacturing involves many other process steps, such as the grading, packaging, transport and storage of the metal powder.
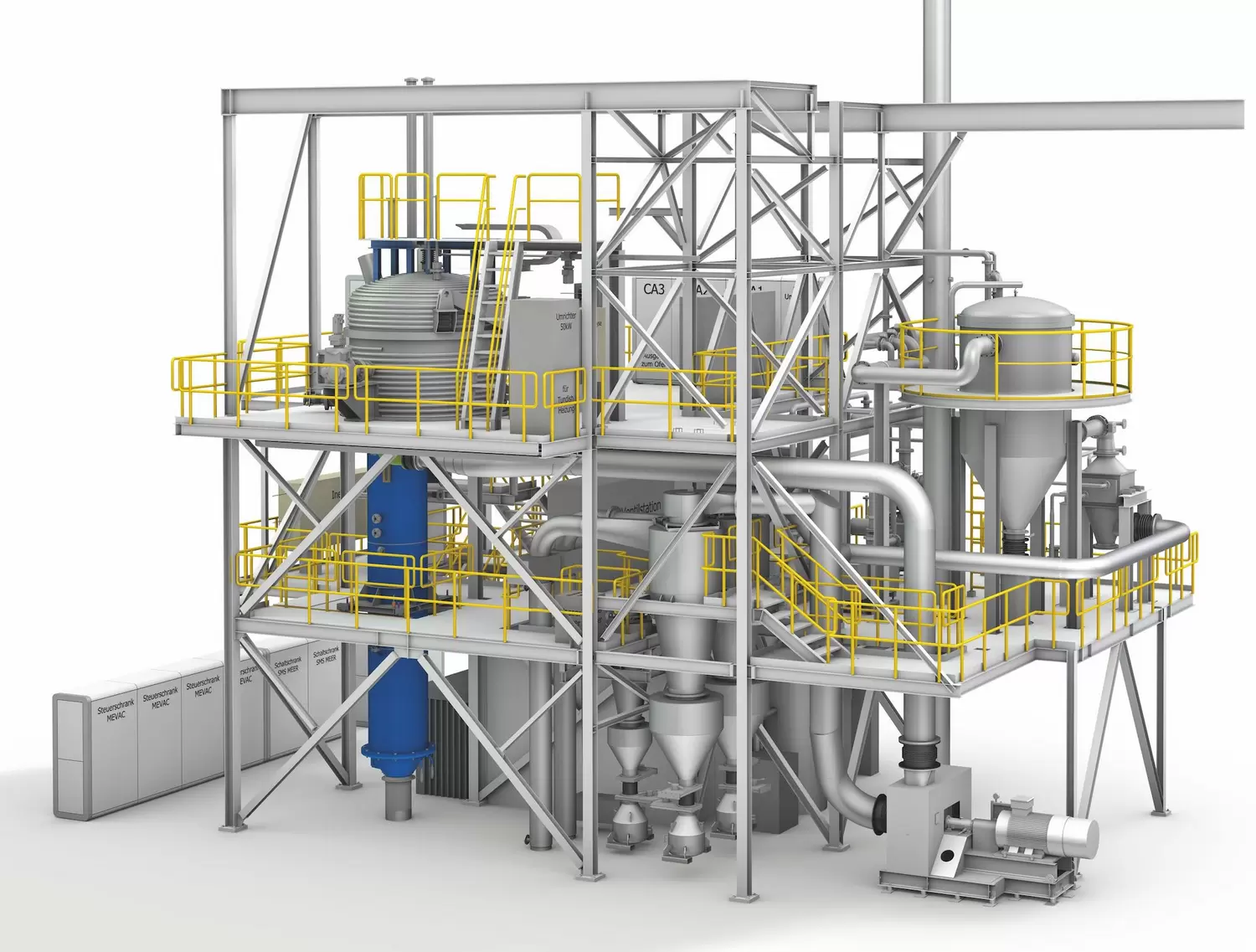
Scale4Series: The vision of additive series production. Under this concept, SMS group can offer their customers an integrated holistic solution with simplified interfaces and optimally harmonized components. This achieves an increase in productivity thanks to lower costs involved and a high, reproducible product quality.
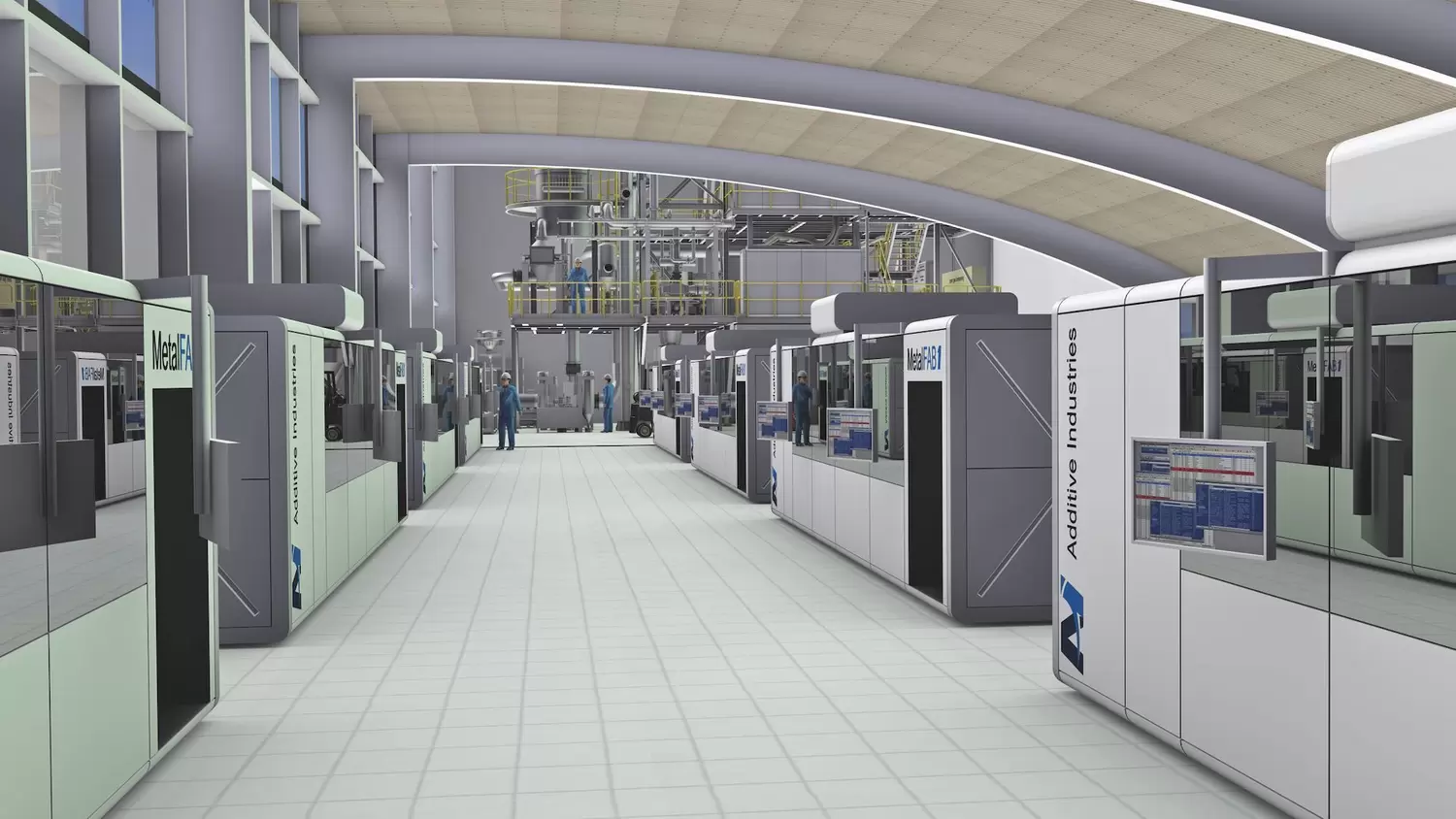
A market characterized by enormous dynamism and growth potential
Both the new powder atomization plant and components made by SMS group by AM techniques provide a very promising market potential. According to a study published by Roland Berger in 2017, between 2004 and 2016 the market for additive manufacturing grew from 0.8 billion to 5.5 billion euros. This corresponds to a CAGR (Compound Annual Growth Rate) of about 20 percent. However, this is only the beginning. Based on several institutes’ forecasts, which the study has evaluated, the market growth is predicted to experience a sharp rise reaching a global level of 24.1 to 28.3 billion euros by 2022.
Markus Hüllen: “As powder production and additive manufacturing are very young technologies, there are only very few established quality standards. SMS group has always set great store by complying with highest quality standards. Therefore we think beyond the stage of powder production. In order to be able to produce high-end, high-performance components from the powder, it is essential that the powder does not get in contact with oxygen in the downstream production processes. Therefore we have been developing solutions that ensure that the powder is safely protected by an inert gas atmosphere until it is processed in the 3D laser printer of our cooperation partner Additive Industries. This involves a great effort, but guarantees the high quality level as required, for example, for safety-critical components.“
According to Markus Hüllen und Norbert Gober, with the new powder atomization plant SMS group has accomplished a first great milestone. There are more to come. In Mönchengladbach a demonstration center is to be set up comprising the complete process chain, i. e. powder production, powder handling, 3D printing, heat treatment and machining, inspection, quality checks, logistics and, last but not least, a dedicated automation system.
A competent global partner for Additive Manufacturing
Nobert Gober: “As systems provider and “Leading Partner in the World of Metals”, our objective is to offer our customers complete additive manufacturing plants on a turnkey basis, by integrating the entire process chain from powder production down to the finished products while ensuring series production at a high, reproducible quality level. The pilot plant will allow us to optimize the processes so as to maximize productivity and minimize total costs. Our customers will receive modular, scalable solutions tailored to their individual requirements.“
With our world-spanning service and support network, we are always readily available for our customers to accompany them along their way into the world of additive manufacturing.